Металловедение. Сталь. Том 2.2
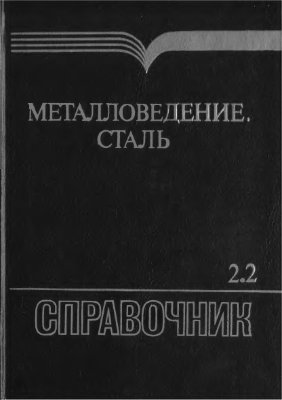
Енихе В., Даль В., Клернер Г.-Ф. и др.
Металлургия, 1995 г.
Влияние химического состава и структуры на коррозионную стойкость
ХРОМ КАК ОСНОВНОЙ ЛЕГИРУЮЩИЙ ЭЛЕМЕНТ
Коррозионная стойкость нержавеющих сталей, определяется содержанием хрома. При содержании > 12 % Сr на чистой металлической поверхности на воздухе и в оксилительных водных электролитах возникает характерное для хромистых сплавов пассивное состояние. Это химическое состояние поверхности, наблюдаемое также на благородных металлах, связано с образованием на ней субмикроскопического оксидного слоя, состоящего на нержавеющих сталях из оксида хрома, который и обеспечивает им химическую стойкость. Образование и стабильность этого защитного слоя предполагают присутствие значительного количества кислорода. Стационарный электрохимический потенциал железа по отношению к нормальному водородному электроду при содержании ~12 % Сr скачком возрастает до достаточно высокого значения в положительной области (рис. Г13.12) [20]. При более высоком содержании хрома коррозионный унос металла в агрессивных средах снижается до незначительной величины.
Исследованиями причин интеркристаллитной коррозии нержавеющих сталей установлено, что коррозионная стойкость пропорциональна содержанию хрома, растворенного в твердом растворе (не связанного с углеродом или с азотом). Когда хром связан только с углеродом в карбид Сr23С6, свободный хром рассчитывается по данным [21] следующим образом: % Сrсв = % Сrобщ— 14,54% С. Для мартенситных сталей, для которых основными свойствами являются твердость и прочность (определяемые содержанием углерода), содержание свободного хрома в твердом растворе как раз соответствует нижнему пределу области коррозионной устойчивости. Поэтому для сталей, содержащих 13 % Сr, достаточная коррозионная стойкость обеспечивается только в атмосферных условиях или в средах средней агрессивности. Другим условием коррозионной стойкости является хорошее качество поверхности, получаемое путем шлифовки и полировки. После закалки и низкого отпуска содержание хрома в твердом растворе наиболее высокое, соответственно, и коррозионная стойкость сталей самая высокая (рис. Г13.13) [22, 23]. При температуре отпуска от 400 до 600 °С выделяется богатый хромом карбид и соответственно снижается коррозионная стойкость, поэтому отпуск в этой области температур нежелателен. При обычно применяемых температурах отпуска от 650 до 780 °С выделяется мелкодисперсный карбид Сr23С6, который практически не ухудшает коррозионную стойкость.
Для ферритных и аустенитных сталей, для которых не требуется легирование углеродом для получения необходимой прочности, следует отметить, что с учетом взаимосвязи коррозионной стойкости и содержания хрома в твердом растворе, содержание углерода должно быть как можно меньше, поскольку тогда температурная область зернограничного выделения смещается к более низкой температуре и к большей длительности инкубационного периода (см. рис. Г13.4). Аустенитные стали, содержащие <0,03 % С, достаточно устойчивы к интеркристаллитной коррозии, так что допускаются сварка (даже на толстых деталях), горячая правка, а также отжиг для снятия напряжений при ограниченной длительности выдержки.
В аустенитных Cr—Niсталях азот даже при содержании~0,5 % не оказывает неблагоприятного влияния на зернограничный распад твердого раствора. В аустенитных сталях с молибденом азот даже повышает сопротивление к питтинговой коррозии и входит в величину характеризующей его «эффективной суммы» [24] с множителем 30
Напротив, для обеспечения устойчивости к интеркристаллитной коррозии ферритных сталей без добавки стабилизирующих элементов (поскольку растворимость углерода и азота в феррите очень мала) необходимо, чтобы суммарное содержание углерода и азота было <0,01 %. В условиях промышленного производства это может быть обеспечено только выплавкой в вакууме.
ВЛИЯНИЕ ДРУГИХ ЛЕГИРУЮЩИХ ЭЛЕМЕНТОВ НА КОРРОЗИОННУЮ СТОЙКОСТЬ
Никель является наиболее важным после хрома легирующим элементом нержавеющих сталей. При содержании 12—30 % Сr никель весьма эффективно улучшает устойчивость сталей в кислотах, при этом плотность тока пассивации заметно снижается. При содержании >20 % Niон препятствует растворению металла даже в активном состоянии, в случае недостаточного окислительного действия агрессивной среды, т. е. в восстановительных условиях, когда не происходит образования пассивного защитного слоя.
В мартенситных хромистых сталях высокое содержание никеля улучшает коррозионную стойкость за счет того, что даже при пониженном содержании углерода становится возможным образование мартенситной структуры, благодаря чему содержание хрома в твердом растворе после закалки соответствует химическому составу стали.
На сопротивление стали коррозионному растрескиванию (КР), индуцированному ионами хлора, никель оказывает неоднозначное влияние. Если чисто хромистые стали еще устойчивы к этому особому виду коррозии, то достаточно уже малых добавок никеля, чтобы значительно снизить напряжение коррозионного растрескивания [26]. Однако феррито-аустенитные стали, содержащие 6—8 % Ni, вновь проявляют хорошую стойкость к коррозионному растрескиванию в нейтральных или слабокислых средах. С увеличением доли аустенитной фазы стойкость к КР вновь снижается; только при чисто аустенитной структуре при увеличении содержания никеля выше 10 % наблюдается улучшение [27]. Низкая чувствительность легированных никелем сталей к КР в сернокислых растворах известна. На стойкость сталей к питтинговой коррозии никель оказывает положительное действие только в сочетании с молибденом.