Металловедение для сварщиков
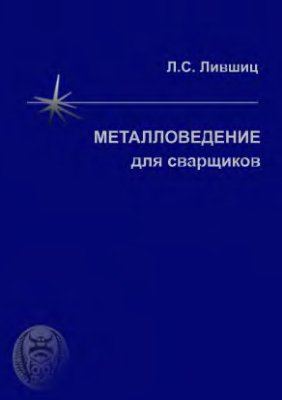
Лившиц Л.С.
Машиностроение, 1979 г.
ХЛАДОСТОЙКИЕ, ЖАРОПРОЧНЫЕ, КИСЛОСТОЙКИЕ И ВЫСОКОПРОЧНЫЕ СТАЛИ.
На высоколегированных сталях с аустенитной основой может быть достигнуто сочетание особых свойств: жаропрочности, кислотостойкости, хладостойкости и высокой прочности, значительно превышающих по своим показателям аналогичные характеристики низко- и среднелегированных сталей и высоколегированных хромистых. Такая особенность свойств связана прежде всего с особенностями аустенитной основы, а также со свойствами низкоуглеродистого «никелевого» мартенсита. Особенности аустенитной основы сталей связаны с двумя определяющими обстоятельствами: кристаллическим строением с системой расположения атомов в решетке граиецентрированного куба и высокой степенью легирования — сумма легирующих элементов не ниже 25—30%. Наличие ГЦК-решетки обеспечивает высокую пластичность и вязкость материала. Высокая степень легирования, всегда значительно превышающая критическую величину отношения МеС, обеспечивает упрочнение твердого раствора основы и низкий коэффициент диффузии в ней углерода и легирующих элементов.
У металлов и сплавов с ГЦК-решеткой по сравнению с металлами, имеющими ОЦК-решетку, вязкость значительно выше. Имеются различные предположения о причинах этого явления. Наиболее вероятным в последнее время считают то, что металлы с ГЦК-решеткой значительно меньше, чем металлы с ОЦК-решеткой чувствительны к влиянию примесей, особенно примесей, дающих растворы внедрения, на блокировку дислокаций. Даже незначительные количества примесей — углерода, азота, кислорода и др., всегда имеющиеся в технических и промышленных металлах, находясь в ОЦК-решетке, существенно деформируют ее и тем самым создают энергетические препятствия перемещению дислокаций. При этом сильно понижается способность материала к деформированию. Такое влияние примесных атомов на деформируемость особенно заметно на ОЦК-металлах при пониженных температурах. Наряду с этим те же примеси в ГЦК-металлах не вызывают столь больших искажений, и деформируемость этих материалов сохраняется при охлаждении высокой.
Хладостойкие стали. Указанная особенность сплавов с ГЦК-решеткой служит основой получения высокой хладостойкости аустенитных сталей. Таким образом, главным условием получения высокой хладостойкости аустенитных сталей является сохранение стабильно аустенитного состояния при низких температурах и при деформации. В аустенитных хромо-никелевых сталях температура мартенситного превращения лежит ниже —100° С и зависит от состава стали. В связи с этим в хладостойких аустенитных сталях содержание аустенитообразу-ющих и ферритообразу-ющих элементов должно быть таким, чтобы температура начала мартеи-ситиого превращения всегда была заметно ниже рабочей температуры металла. Вводимые иногда в хладостойкие стали для повышения прочности карбидообразу-ющие элементы (молибден, титан и др.) не должны обеднять твердый раствор углеродом настолько, чтобы сталь перешла в нестабильно аустенитное состояние при низкой рабочей температуре.
Карбидные выделения и примесные атомы могут понизить хладостойкость и в том числе, если они сосредоточатся на границах зерен. В этом случае большое количество атомов примесей на границах зерен может даже в аустенитной стали с ГЦК-решеткой привести к значительным искажениям и понизить деформируемость и вязкость пограничных участков.
В связи с таким возможным отрицательным влиянием карбидных выделений и неравномерного распределения по зерну примесных атомов наилучшей термообработкой рассматриваемых хладостойких сталей может быть закалка на гомогенный аустенит. Если имеется в виду повышение прочности за счет создания дисперсной карбидной фазы, применяют строго регламентированное старение — отпуск. Эта обработка и легирование стали не должны вызвать неблагоприятной сегрегации по границам зерен примесей и не должны стимулировать активного карбидообразования. Нагрев ЗТВ при сварке способен вызвать понижение их хладостойкости.
Превращение аустенита в мартенсит может иметь место при пластической деформации, особенно, если деформация эта происходит при пониженных температурах. Такой распад аустенита под влиянием деформации при низкой температуре может иметь место там, где одно охлаждение не вызвало бы превращения γ —» α. Поэтому хладостойкие стали должны иметь запас аустенитности при данной низкой рабочей температуре, рассчитанной на дополнительное влияние деформации. Влияние термообработки, температуры и деформации на образование мартенсита в стали 12Х18Н10Т иллюстрируется на рис. 99.
Характерным примером влияния деформации на мартенситное превращение аустенита и снижение хладостойкости могут быть аустенитные марганцовистые стали типа Г13 К. В. Попов и В. Г. Савицкий показали, что меньшая хладостойкость марганцовистого аустенита, чем хромоиикелевого, связана с высокой его склонностью к мартеиситному превращению при деформации, сопровождающей разрушение.
Важное значение для хладостойкости аустенитных хромо-никелевых сталей имеет мелкозернистость. Стали с мелким зерном более хладостойки, чем с крупным. Значение, по-видимому, имеет как увеличение протяженности границ зерен, так и рассредоточение примесных атомов (табл. 35).
Жаропрочные стали. Высокая вязкость основы высоколегированных хромоникелевых сталей с ГЦК-решеткой использована и в жаропрочных сталях этого типа. Благодаря высокой вязкости основы представилась возможность значительного упрочнения ее дисперсными или упругосвязанными с матрицей выделениями карбидов или интерметаллидов. При этом высокая степень легирования основы и низкий коэффициент диффузии в ней углерода и легирующих элементов при нагреве до сравнительно высоких температур делают дисперсное состояние упрочняющей фазы устойчивым при нагреве, что обеспечивает сохранение прочности и сопротивления деформированию при высоких температурах С повышением температуры уменьшение скорости диффузии за счет легирования уменьшается и резко начинает снижаться жаропрочность. Так, С. 3. Бокштейн отмечает, что легирование никеля 20% Сr снижает коэффициент диффузии хрома при 700° С в 20 раз, а при 1000° С — всего в 2 раза. В связи с этим с повышением температуры нагрева упрочненных дисперсными выделениями жаропрочных сталей должна происходить их ускоренная коагуляция, с чем необходимо считаться при оценке изменения жаропрочности ЗТВ при сварке.
Значение аустенитной основы в жаропрочных сталях связано не только с ее более высокой вязкостью по сравнению с ферритной, а и с тем, что при одинаковом легировании процессы диффузии в аустените идут намного медленнее, чем в феррите. Об этом можно судить по тому, что даже в чистом железе при температуре 910° С (полиморфное превращение) скорость самодиффузии для α-железа в 350 раз выше, чем для у-железа (С. 3. Бокштейн). Таким образом, наличие феррита в аустенитных сталях оказывается неблагоприятным фактором. Феррит и с точки зрения технологичности стали при операциях обработки давлением также неблагоприятен, так как затрудняет деформируемость и способствует получению анизотропии свойств прокатанного металла.
В аустенитных сталях холодная деформация определяет возможность протекания γ—»α -превращения в недостаточно стабильной основе. Кроме того, аустенит под влиянием холодной деформации упрочняется значительно сильнее, чем феррит. В жаропрочных аустенитных сталях деформация как холодная, так и при повышенных температурах стимулирует выделение упрочняющей дисперсной фазы.
Таким образом, аустенитиые жаропрочные стали могут быть трех типов. 1) стали, в которых используется только повышенная жаропрочность высоколегированного аустенита, 2) стали с дополнительным карбидным упрочнением аустенитной основы и 3) стали с интерметаллидным упрочнением (или карбидно-интерметаллидным) аустенитной основы.
Стали типа 1 — это обычно низкоуглеродистые высоколегированные хромом и никелем; стали типа 2 имеют повышенное содержание углерода и стали типа 3 легированы специальными карбидо- и интермсталлидо-образующими элементами, молибденом, вольфрамом, ниобием, таганом и др
Высокие жаропрочные свойства на аустенитных сталях достигаются после специальной термообработки. Для сталей типа 1 — это закалка на аустенит, для сталей типов 2 и 3 — это закалка и старение — отпуск Закалка при этом должна обеспечить растворение углерода и легирующих элементов, а старение — выделение их в дисперсной или упругосвязанной с матрицей формой карбидов или интерметаллидов Сохранение этого состояния упрочняющей фазы при последующих после старения технологических операциях изготовления изделия, и в том числе при сварке, является условием сохранения жаропрочности Само собой разумеется, что эксплуатационный нагрев также не должен привести к изменению состояния упрочняющей фазы Поэтому старение после закалки обычно осуществляют при температуре, близкой к температуре эксплуатации изделия (табл 36)
Кислостойкие стали. Высокое содержание хрома и никеля в аустенитных сталях делает их стойкими против химической и электрохимической коррозии Сопротивление коррозии этих сталей зависит от их фазовой и структурной однородности, а также однородности по химическому составу, поскольку все эти факторы определяют прежде всего электрохимическую однородность и наличие повсеместно необходимой концентрации легирующих элементов для обеспечения определенного электрохимического потенциала В связи с этим наличие в сталях карбидов хрома или других легирующих элементов неблагоприятно для их коррозионной устойчивости Это определяет использование закалки сталей на гомогенный аустенит как оптимальной термообработки для повышения коррозионной стойкости
Все коррозионно-стойкие аустенитные хромоникелевые стали являются одновременно и жаропрочными и иногда применяются для работы в химически активных средах при повышенных температурах Нагрев таких сталей способствует стабилизации их фазового состояния и при наличии в сталях углерода и хрома — выделению из твердого раствора карбидов хрома (стали 08Х18Н10, Х23Н12 и др ). Выделение этих карбидов происходит в энергетически наиболее благоприятных участках — по границам зерен Образование карбидных выделений по границам зерен приводит к тому, что на границах вследствие появления второй фазы увеличивается склонность к электрохимической коррозии Кроме того, при образовании карбида на его создание с приграничных участков зерна уходит хром, приграничная область объединяется хромом, и коррозионная стойкость в ней снижается Процесс карбидообразования на границах зерен повышает в этих зернах уровень микронапряжений
И, наконец, карбидные выделения на граничных участках приводят к повышению в них хрупкости. Эти процессы образования карбидных выделений по границам зерен могут происходить при длительных эксплуатационных нагревах при повышенных температурах В тех случаях, когда сталь работает только как жаропрочный материал без коррозионно-активной среды, в ней со временем снижается пластичность и вязкость Там же, где имеется химически активная среда, в стали развивается склонность к межкристаллитному коррозионному разрушению (межкристаллитная коррозия — МКК).
Предрасположенность к МКК аустенитных сталей развивается при нагреве в интервале температур 500—700° С. При достаточно длительном нагреве на более высокие температуры — выше 800° С на склонности к МКК начинает сказываться другой процесс — диффузионное перемещение атомов хрома из глубинных участков к обедненным хромом приграничным областям Обогащение приграничных участков зерен хромом повышает стойкость стали против МКК Поэтому 2—3-часовой нагрев стали при температуре ~850—900° С, при котором одновременно происходят два процесса — выделение карбидов по границам зерен и восстановление концентрации хрома в приграничных зонах, используют как термообработку, создающую устойчивость аустенитной стали против
МКК При этом, однако, происходит некоторое снижение вязкости металла
Разработан ряд способов повышения стойкости стали προτιπ. МКК, например ограничение содержания в стали углерода и сведение тем самым к минимуму процесса карбидообразования Это привело к созданию промышленных сталей с очень низким содержанием углерода — 00Х18Н10 (С <: 0,04%), 000Х17Н13М2 (С < 0,03%) и др. Однако столь низкоуглеродистые стали очень дороги Другое направление повышения стойкости аустенитных сталей против МКК — введение в них элементов стабилизаторов, элементов, дающих стойкие карбиды — титана, ниобия (сталь 12Х18Н10Т, 08Х18Н12Б и др ).
Количество этих элементов должно соответствовать содержанию углерода в стали с тем, чтобы они связали в стойкие карбиды весь имеющийся углерод (Ti/C или Nb/C равное или несколько выше критического отношения). В этом случае практически исключается образование карбидов хрома по границам зерен и обеднение хромом пограничных участков, так как весь углерод оказывается связанным элементами, имеющими с ним значительно более высокое химическое сродство, чем хром. Карбиды титана и ниобия выделяются из стали, как правило, при охлаждении в области высоких температур и располагаются обычно не по границам зерен, а в самом зерне Это служит залогом того, что карбидообразование не сказывается на склонности к МКК.
В некоторые хромоникелевые аустеиитные стали для повышения стойкости против общей коррозии в ряде активных сред вводят молибден, а иногда и медь (стали 10Х17Н13М2Т, 0Х23Н28МЗДЗТ и др ).