Металлосберегающие технологии кузнечно-штамповочного производства
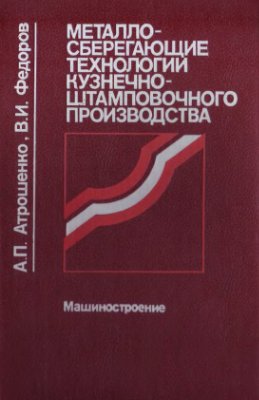
Атрошенко А.П., Федоров В.И.
Машиностроение, 1990 г.
ШТАМПОВКА НА ГИДРАВЛИЧЕСКИХ И ВИНТОВЫХ ПРЕССАХ
Интенсивное развитие авиационной и аэрокосмической техники, химического и энергетического машиностроения, автомобиле- и тракторостроения, тепловозо- и вагоностроения, электротехники и электроники и др. вызывает дальнейший рост производства крупногабаритных штампованных поковок.
Горячая штамповка крупногабаритных поковок, особенно из специальных малопластичных сталей и легких сплавов на мощных гидравлических прессах, более прогрессивна по сравнению с изготовлением таких поковок ковкой, поэтому в последние годы она получает широкое распространение, так как дает возможность организовать производство разнообразных крупногабаритных поковок, форма которых наиболее близка к форме конечной детали, и с относительно высокими технико-экономическими показателями. В этом случае не только достигается экономия за счет сокращения расхода металла и объема завершающей механической обработки, но и улучшается качество структуры благодаря направленному расположению волокон, повторяющему контур детали.
Отличительная черта этого производства — разнообразие форм и типоразмеров поковок при невысокой серийности. Внедрение крупногабаритных монолитных, штампованных деталей снижает трудоемкость их изготовления в 3 раза, позволяет уменьшить массу изделий и повысить их надежность.
Чтобы обеспечить машиностроительные заводы крупногабаритными прогрессивными штампованными поковками из высокопрочных сталей и сплавов, в нашей стране созданы и освоены вертикальные штамповочные гидравлические прессы с широким диапазоном усилий (вплоть до 750 МН), которые позволяют полностью обеспечить потребности машиностроительных заводов поковками с высоким уровнем механических свойств и высоким коэффициентом использования металла. Освоено производство штампованных поковок пустотелых валов из стали 13Х11Н2В2МФ-Ш (ЭИ961-Ш); организовано серийное производство поковок крупногабаритных дисков и валов из жаропрочных сталей и сплавов для газоперекачивающих установок; для отраслей тяжелого машиностроения и горнорудной промышленности изготовляются штампованные шестерни и колеса передаточных механизмов для тяжелых экскаваторов; освоено производство поковок уникального тяжелого коленчатого вала длиной до 4000 мм для магистральных тепловозов; внедрены технологии изотермической штамповки крупногабаритных поковок из титановых сплавов деталей типа лопаток, дисков и сложноконтурных оребренных деталей с площадью проекций в плане до 2000 см2. Изотермическая штамповка крупногабаритных поковок позволяет в 1,5—2 раза снизить расход титановых сплавов и на 15—30% уменьшить трудоемкость последующей механической обработки.
'Принципиально, новые технологические возможности открываются в кузнечно-штамповочном производстве в связи с созданием гидравлических прессов для много полостной штамповки точных поковок в закрытых штампах. Такое оборудование дает возможность изготовлять высокоточные поковки сложной конфигурации с несколькими внутренними полостями в штампах с разъемными матрицами. Коэффициент использования металла при штамповке поковок сложной конфигурации повышается в 2—3 раза.
Для точной горячей объемной штамповки поковок деталей ответственного назначения из труднодеформируемых, жаропрочных сталей и сплавов все более широко применяют винтовые прессы (фрикционные, электровинтовые, гидровинтовые), поскольку они имеют преимущества перед другими кузнечно-прессовыми машинами. Винтовые прессы обеспечивают высокую точность штампованных поковок благодаря работе до упора штампа в штамп, снижение трудоемкости в штамповочных и механических цехах, увеличение производительности труда и коэффициента использования металла. Винтовые прессы используют также для точной штамповки поковок с тонким полотном, особенно турбинных и компрессорных лопаток, из труднодеформируемых и жаропрочных сплавов и закрытой штамповки в цельных и разъемных матрицах. Благодаря своим достоинствам винтовые универсальные и специализированные прессы должны широко применяться в кузнечно-штамповочном производстве.
5.1. Штамповка крупногабаритных поковок
В связи с общей тенденцией увеличения единичной мощности машин и установок и повышения требований к их надежности й долговечности в машиностроении широко используют крупногабаритные детали, изготовляемые из горячештампованных поковок из алюминиевых, магниевых и титановых сплавов и других труднодеформируемых материалов, получаемые на мощных гидравлических прессах. Их применяют в самолетостроении (лонжероны, панели, рамы, кронштейны), в химической промышленности (днища, элементы обшивки емкостей), судостроении (лопасти гребных бинтов, каркасные детали), энергомашиностроении
(отводы трубопроводов, крышки реактора), тепловозостроении (коленчатые валы, колеса, диски), в вагоностроении (люки, рамы дверей), в автомобильной и тракторной промышленности.
Сборные конструкции, состоящие из большого количества мелких деталей, соединенных сваркой, клепкой или же с помощью болтов, заменяют монолитными деталями, полученными из цельно штампованных поковок, которые более прочны и надежны в эксплуатации. Примером изготовления таких деталей может служить цельноштампованная поковка балки (рис. 5.1, б) из алюминиевого сплава, заменяющая собой сборную конструкцию балки, которая состоит из отдельных деталей, соединенных заклепками (рис. 5.1, а).
Крупногабаритные детали,, изготовленные из цельноштампованных поковок, имеют более высокие прочность и долговечность, чем такие же детали, полученные фрезерованием из проката или кованых поковок, так как у штампованных поковок волокна соответствуют конфигурации детали, а у кованых поковок и катаных заготовок волокна располагаются в направлении протяжки или прокатки и при механической обработке перерезаются.
Применение штампованных поковок уменьшает трудоемкость изготовления благодаря сокращению сборочных работ и механической обработки вследствие меньших припусков по сравнению с заготовками, получаемыми другими способами обработки. При изготовлении лонжерона из цельноштампованной поковки трудоемкость механической обработки в сравнении со сборной конструкцией уменьшается на 40—50%. Коэффициент использования металла при изготовлении деталей из штампованных поковок составляет 20—90%, а при производстве из проката — 8—10%. В табл. 5.1 приведены сравнительные данные эффективности применения кованых и штампованных поковок при изготовлении из них различных крупногабаритных деталей [17].
На гидравлических прессах штампуют поковки различной конфигурации в открытых и закрытых штампах массой от нескольких сот килограммов до 8 т. Наиболее распространена штамповка в открытых штампах поковок из алюминиевых, магниевых и титановых сплавов, нередко очень больших размеров. Исходными заготовками для штамповки крупногабаритных поковок на гидравлических прессах служат заготовки полученные из слитков ковкой, прокаткой и прессованием.
Для штамповки таких поковок, как панели, применяют в основном плиты и полосы толщиной до 100 мм, которые получают на многоклетьевых станах непрерывной прокатки. Такие заготовки имеют мелкое зерно и волокнистую структуру, характеризующуюся ярко выраженной анизотропией механических свойств вдоль и поперек волокна. Для штамповки массивных поковок из алюминиевых и магниевых сплавов применяют прессованные заготовки, которые изготовляют на мощных горизонтальных прессах в виде полос длиной до 9 м с площадью поперечного сечения до 950 см2 (толщиной 50—100 мм, шириной 500—950 мм) и в виде прутков длиной до 13 м с площадью поперечного сечения до 2000 см2 (максимальный диаметр 500 мм). Наиболее крупные поковки из алюминиевых, магниевых и титановых сплавов штампуют из кованых заготовок, которые получают из слитков на молотах и гидравлических прессах протяжкой или осадкой с последующей протяжкой. В этом случае металл заготовок имеет наилучшие свойства.