Металлокорд для автошин
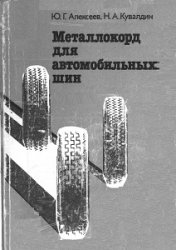
Алексеев Ю.Г. Кувалдин Н.А.
Металлургия, 1992 г.
ТЕХНОЛОГИЯ И ОБОРУДОВАНИЕ ДЛЯ ПРОИЗВОДСТВА МЕТАЛЛОКОРДА
ТЕХНОЛОГИЧЕСКАЯ СХЕМА ИЗГОТОВЛЕНИЯ МЕТАЛЛОКОРДА
К основным технологическим операциям производства металлокорда относятся следующие стадии: подготовка поверхности исходной катанки к волочению (удаление прокатной окалины механическим способом или химическим травлением и нанесение подсмазочного покрытия), волочение, патентиро-вание и подготовка поверхности проволочной заготовки промежуточных диаметров к дальнейшему волочению (при необходимости патентирование может выполняться также и на исходной катанке), патентирование и нанесение латунного покрытия, мокрое волочение заготовки с латунным покрытием на проволоку готового размера, свивка прядей и металлокорда, контроль свойств и упаковка готовой продукции.
Исходным сырьем для металлокорда является сорбитизированная катанка диаметром 5,5 или 6,5 мм в бунтах массой до 2000 кг, материалом которой служит сталь, содержащая 0,70—0,74 % С и характеризующаяся высокой чистотой по вредным и остаточным элементам, а также неметаллическим включениям. Применяемая катанка должна обеспечивать минимальную обрывность наитончайшей проволоки диаметром 0,15—0,38 мм при волочении и скручивании в процессе свивки.
Первой операцией переработки катанки диаметром 6,5 мм в готовую проволоку диаметром 0,15—0,265 мм является окалиноломание и волочение катанки на проволоку диаметром 6,1мм в один переход со скоростью 170м/мин. Затем эту проволоку патентируют на непрерывных многониточных термотравильных агрегатах, нагревая ее в печи до 970 С и охлаждая в ванне с расплавом селитры при 470 С. После выхода из ванны с селитровым расплавом нити проволоки травят, промывают водой, обрабатывают раствором буры в соответствующих ваннах, сушат и наматывают на катушки. Далее следует второе волочение проволоки с диаметра 6,1 мм до 4,0—3,0 мм. Эту проволоку на аналогичных термотравильных агрегатах подвергают следующему патентированию, а затем волочению до диаметра 2,0—1,15 мм. Третьему патентированию подвергается проволока диаметром 1,8—2,0 мм, которую протягивают до диаметра 0,65—0,85 мм. По мере уменьшения диаметра проволоки скорости волочения и патентирования увеличивают. Проволоку диаметром 0,65—1,28 мм подвергают патентированию и латунированию в одном технологическом потоке на многониточных травильно-гальванических агрегатах. При этом на проволоке формируется слой латунного покрытия /-фазового состава толщиной 1,4-2,2 мкм с содержанием 64-72% Си. На бортовой латунированной проволоке толщина покрытия должна быть не ниже 0,6 мкм. Обработка проволоки для металлокорда и бортовой латунированной проволоки осуществляется при скорости соответственно 28-38 и 70м/мин.
Далее следует заключительное волочение латунированной проволоки диаметром 0,65-1,28 мм до проволоки конечного диаметра 0,15—0,265 мм в 18—20 переходов с суммарным обжатием 93—97% со скоростью 600—720м/мин. После волочения толщина латунного покрытия на готовой проволоке составляет 0,20—0,40 мкм. Транспортировка проволоки между операциями осуществляется на катушках емкостью 1000, 250 и 10 кг для проволоки диаметром 0,65-6,1; 0,65-1,28 и 0,15-0,30 мм для обычной, латунированной готовой проволоки соответственно.
Следующим процессом является свивка нескольких проволок диаметром 0,15—0,265 мм в пряди и металлокорд на пря-девыощих, канатовьюших и оплеточных машинах при скорости вращения ротора 6000-10000 мин-1. Готовый металлокорд наматывают на катушки вместимостью 15 кг и после испытания физико-механических свойств упаковывают в плотную тару с силикагелем, например, в металлические бочки.
Катанку диаметром 5,5 мм перерабатывают в готовую проволоку диаметром 0,15—0,265 мм по более простой и более перспективной схеме. На первой операции осуществляют подготовку поверхности катанки к волочению в ваннах садочного типа или на высокоскоростных однониточных установках. Затем следует первое волочение на заготовку диаметром 3,15—2,40 мм. Эту проволоку подвергают патентированию и подготовке поверхности к волочению на многониточных термотравильных агрегатах. Потом следует второе волочение на проволоку диаметром 0,85—1,50 мм. Дальнейшая переработка проволоки совпадает со схемой переработки катанки диаметром 6,5 мм.
ТРЕБОВАНИЯ К КАТАНКИ ДЛЯ МЕТАЛЛОКОРДА
На эффективность производства и свойства металлокорда заметное влияние оказывают не только условия всех видов обработки проволочной заготовки, применяемые процессы окончательного волочения проволоки и свивки, а также свойства стали и катанки из нее.
Качеству катанки уделяется большое внимание всеми ведущими зарубежными фирмами. Фирма "Pirelli" предъявляет к катанке для металлокорда следующие требования [5], %: С 0,69-0,74; Μn 0,50-0,70; Si < 0,30; S и Ρ 0,015; Ni, Си и Сr 0.05; А1 и N5 0,005; 2см3/Ю0г Hj. Глубина поверхпостных дефектов и толщина обезуглероженного слоя не должна превышать соответственно 0,15 мм и 1 %. Временное сопротивление должно составлять 980-1176 Н/мм2, относительное удлинение и сужение соответственно не менее 11 и 35%, размер деформируемых включений не более 30 мкм, недеформируемых не более 15 мкм.
Сталь фирмы Thyssen" марки Stahlkord содержит, %: С 0,67-0,73; Μn 0,57-0,65; Si 0,17-0,25; Ρ 0,003-0,016; S 0,005-0,02; Ν 0,001-0,005; Сu 0,01-0,04; Сr 0,015-0,05; Ni 0,01—0,04. Катанка диаметром 5,5 мм из этой стали имеет среднее временное сопротивление 1062 Н/мм2, относительное удлинение образца длиной 100 мм - 11%, относительное сужение 50%. Микроструктура катанки состоит на 65% из сорбита, на 35% из перлита и менее чем на 1% из феррита. Включения сульфидов и недеформирующиеся оксиды, имеющие размер более 15 мкм, не обнаруживаются. Сталь практически свободна от оксидов алюминия. Балл недеформирующихся оксидов и ликвации равен соответственно 0,45 и 0,25.
Особое внимание зарубежными фирмами уделяется снижению ликвации (сегрегации) в процессе производства катанки из стали. Источниками недеформирующихся неметаллических включений и ликвации являются продукты раскисления стали и шлак. Размеры осевой ликвации в стали обычно больше, чем размеры недеформирующихся включений, поэтому сегрегации уменьшают пластичность проволоки значительно сильнее. Другим фактором, снижающим пластичность, является формирование частиц заэвтектоидного цементита по границам зерен. Этот отрицательный эффект проявляется особенно сильно, когда размер частиц больше ширины пластин основной структуры.
Технология производства стали марки Stahlkord для металлокорда включает получение чугуна высокой чистоты по сере и фосфору, переплавку его вместе с оборотным ломом в сталь в конверторе комбинированного дутья типа ТВМ, двухступенчатую обработку в вакуумной установке и установке для аргонного раскисления, непрерывную разливку на блюмы размерами 260x300 мм на шестиручьевой установке непрерывной разливки стали с электромагнитным перемешиванием. Затем заготовка прокатывается на профиль квадратного сечения 105x105 мм, после чего деформируется в четырехниточном мелкосортном стане в 23 прохода в катанку диаметром 5,5 мм с последующим охлаждением способом Stelmor. Непрерывная разливка стали с электромагнитным перемешиванием позволяет уменьшить сегрегации и особенно осевую ликвацию. С той же целью температуру перегрева расплава в промежуточном ковше и скорость разливки стремятся максимально уменьшить.
Предсказание поведения катанки во время волочения и свивки является сегодня трудной задачей из-за отсутствия надежных методов определения геометрии (объема, периметра, формы), а также химического состава неметаллических включении.
Фирмой "Pirelli" приемка поступающей катанки заключается в переработке небольшого количества катанки из каждой плавки с оценкой частоты происшедших обрывов и определением их причин. Если частота обрывов ниже установленной нормы, принимается решение о запуске катанки в производство.
Деформируемость оксида алюминия и алюминатов практически равна нулю, следовательно, они являются наиболее вредными и их следует избегать, если необходимо, чтобы проволока легко поддавалась волочению и скручиванию. Как правило, при приемочных испытаниях из-за большого количества обрывов бракуются те плавки катанки, которые содержат неметаллические включения, состоящие из алюмосиликатов с содержанием оксида алюминия от 30-40% (анортит) до 80-90% (корунд), которые классифицируются как смешанные, твердые недеформирующиеся включения.
Катанка с хорошим поведением при волочении имеет неметаллические включения, представленные силикатами или алюмосиликатами с содержанием около 10% оксида алюминия и размером менее 4,5 мкм. Таким образом, чем меньше количество и размер включений, содержащих оксид алюминия, а также процентное содержание алюминия в смешанных включениях, тем лучше поведение катанки при волочении.
Наличие включений, превышающих по размеру 20—30 мкм, явление чрезвычайно редкое, и поэтому вероятность их обнаружения на металлографических образцах катанки очень незначительная. Чаще они обнаруживаются на поверхности излома тонких проволок. Однако преобладание в катанке неметаллических включений в виде алюмосиликатов можно считать признаком возможного обнаружения крупных включений с высоким процентным содержанием оксида алюминия или даже чистого оксида алюминия.