Металлография коррозионностойких сталей и сплавов
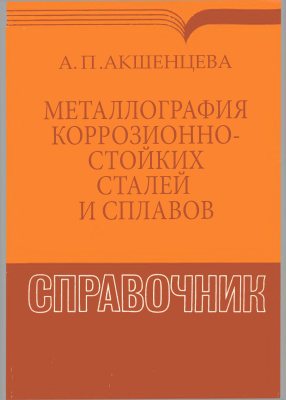
Акшенцева А.П.
Металлургия, 1991 г.
2. СКЛОННОСТЬ СТАЛИ К MKK И К СТРУКТУРНО-ИЗБИРАТЕЛЬНОЙ КОРРОЗИИ СВАРНЫХ СОЕДИНЕНИЙ
Испытания на склонность стали к межкристаллитной коррозии в кипящем сернокислом растворе медного купороса длительностью 120 ч были выполнены на всей серии образцов, подвергну-
тых кратковременному нагреву в течение 2,5 мин и нормализации от 800, 900, 1000, 1100, 1300 °С. Как показали последующие микроисследования, все образцы подвергались межкристаллитному разрушению, свидетельствующему о склонности закаленной стали 14Х17Н2 к MKK (рис. 25, а).
Коррозионные испытания образцов, подвергнутых повторному нагреву - отпуску при 300- 650 *С, 30 мин, показали, что в кипящем сернокислом растворе медного купороса в стали обнаруживается структурно-избирательная коррозия с выщелачиванием структуры отпущенного мартенсита, ферритные зерна заметной коррозии не подвергаются (рис. 25, б). После отпуска при 600 °C, 30 мин сталь 14Х17Н2 приобретает наибольшее снижение коррозионной стойкости, о чем можно судить по толстому слою меди 0,20 мм, осевшему на поверхности образца и глубине слоя коррозионного разрушения 750 мм.
На образцах стали 14Х17Н2, отпущенных при 680-700 0C в течение 0,5-1 ч, межкристаллитная и структурно-избирательная коррозия отсутствовала. Повышенная коррозионная стойкость в этом узком температурном интервале 680-700 °C, очевидно, объясняется тем, что высокий отпуск способствует наиболее полному распаду мартенсита с образованием сорбитной структуры и выравниванию концентрации хрома на границах двух фаз у- 6, около выделившихся карбидов, за счет более высокой скорости диффузии хрома.
Отпуск при 680- 700 °C в течение I ч рекомендуется применять и для сварных соединений стали 14Х17Н2 для улучшения коррозионной стойкости и получения максимальной пластичности. Повторный нагрев стали при 750, 800, 850, 900 °C в течение 30 мин вновь вызывает MKK по границам раздела двух фаз δ-у (феррита и аустенита).
Как показали коррозионные испытания сварных соединений в кипящем сернокислом растворе медного купороса, зона термического влияния сварных соединений подвергается коррозионному разрушению. Для сварки стали 14Х17Н2 применяли электроды марки ЦЛ-11/св. 08X19НI ОБ. Сварные соединения из стали 14Х17Н2, сваренные аустенитным электродом за один проход без подварки корня шва, обнаруживают в зоне термического влияния МКК. Сварка стали с подваркой корня шва вызывает у сварных соединений структурно-избирательную коррозию со стороны основного шва и MKK вблизи границы сплавления подварочного шва с основным металлом. Коррозионная стойкость сварных соединений из стали 14Х17Н2 может быть улучшена путем отпуска при 680- 700 °С, 1ч. Сварной шов, выполненный электродом ЦЛ-11/св. 08X19НI ОБ после отпуска 700 "С, 1ч, склонности к MKK не обнаруживает [33, 36].
Сталь 14Х17Н2 была использована для изготовления фланца ротора центрифуги НОГШ-350. Фланец изготавливали из поковки диаметром 230 мм, высотой 90 мм, которая после ковки дополнительной термической обработке не подвергалась. При исследовании причин разрушения фланца ротора, изготовленного из поковки стали 14Х17Н2, было установлено, что ударная вязкость очень низкая и составляла 0,04МДж/м2, твердость 311HB. Микроструктура стали фланца состояла из мартенсита и небольшого количества феррита, расположенного неравномерно по сечению поковки. Микротвердость мартенсита 4805 МПа, а микротвердость ферритных участков в структуре поковки 2098 МПа. Наиболее отчетливо структура стали 14Х17Н2 была выявлена электролитическим травлением в 10 %-ном хромовом ангидриде (рис. 26, о). Данный реактив выявляет границы бывших аустенитных зерен, а также отчетливо выявляет карбиды, выделившиеся на границе раздела двух фаз аустенита и феррита (рис. 26, б). Таким образом, замедленная скорость охлаждения поковки из стали 14Х17Н2 вызвала выделение карбидов на границах ферритных зерен и протекание мартен- ситного превращения, что привело к охрупчиванию стали и разрушению ротора центрифуги НОГШ-350 при работе. Детали центрифуг, изготавливаемые из стали 14Х17Н2, следует подвергать следующей термической обработке: нормализации от 950-980 °C и отпуску при 680- 700 0C, I ч с охлаждением на воздухе для повышения механических свойств и устранения склонности стали к МКК.
Сталь применяется для лопаток газовых турбин, крепежа и других ответственных изделий при рабочих температурах до 450 °C, когда стали с 13 % Cr не обеспечивают тоебуемой коррозионной стойкости [35].
I. СТРУКТУРА, ФАЗОВЫЙ СОСТАВ, УДАРНАЯ ВЯЗКОСТЬ СТАЛИ 1QX28AH ПОСЛЕ НОРМАЛИЗАЦИИ С ВЫСОКИХ
ТЕМПЕРАТУР
Микроструктуру стали исследовали на ударных образцах, пред варительно подвергнутых электронагреву по термическим циклам, имитирующим сварочный нагрев. Температуры нагрева были выбраны в диапазоне 20-1250 °С с интервалом через 50 °С, время выдержки 1-5 мин, охлаждение в воде. При выявлении структуры стали 10Х28АН в состоянии поставки были встречены трудности. Границы зерен феррита были выявлены только после электролитического травления шлифа в концентрированной азотной кислоте при плотности тока 0,2 А/см2 в течение 30 с.
На рис. 27, а представлена структура стали 10X28АН в исходном состоянии. Она состоит из зерен феррита и мелких частиц вториЧ' ной фазы - аустенита, округлой формы. Карбиды на граница*
ферритных зерен отсутствовали. Исходная структура сохранялась без изменения при кратковременном нагреве до 900 eC. Начиная с температуры нагрева 950 °C в стали происходил рост зерен феррита и выделение аустенитной фазы Hа границах зерен, а также внутри зерна; а у-превращение тем полнее, чем выше температура нагрева. При достаточно быстром охлаждении, как, например, при сварке обратного превращения у-а практически не происходит.
На рис. 27, б приведена структура стали 10Х28АН после кратковременного нагрева до 1150 °C с охлаждением в воде. Здесь отчетливо видна двухфазная структура, состоящая из ферритной основы и зерен аустенита, выделившихся на границах зерен феррита. С повышением температуры нагрева до 1200-1250 “С происходит увеличение количества аустенита и рост ферритных зерен (рис. 28, а, б). Аустенитная фаза выделяется по границам ферритнык зерен, причем аустенитные зерна имеют вид пластин г прямоугольными гранями под углом 60е; пластины растут от границ внутрь ферритных зерен (рис. 28, б). Внутри ферритных зерен выделились дисперсные карбиды. Обычное металлографическое травление не всегда достаточно четко дифференцирует выделяющиеся фазы. Примененный в исследовании магнитно-металлографический метод, разработанный Н.И.Ереминым [43,44], оказался весьма надежным средством дифференциации фаз. В качестве примера на рис. 29 приведены магнитные микрофотографии структуры стали 10X28АН, нагретой до 1200 °C. Частицы магнитного коллоида осели только на ферритной составляющей структуры. Аустенитная фаза имеет белый цвет.
На рис. 30, о, б приведены электронные микрофотографии структуры стали 10Х28АН, полученные с помощью лаковых реплик, оттененных хромом, после различной термообработки. Аустенитная фаза представляется более рельефной, выпуклой частицей.
В результате кратковременного высокотемпературного, в том числе и сварочного нагрева, происходит изменение структурного состояния стали, что влияет на ее механические свойства и коррозионную стойкость. Ударная вязкость стали в зависимости от максимальных температур предшествующего испытанию нагрева меняется более резко. Под воздействием сварочного нагрева происходит изменение свойств стали в двух зонах. Первый спад ударной вязкости для основного металла, обнаруживаемый у зоны совместной кристаллизации, связан с явлением так называемой высокотемпературной хрупкости и некоторого роста зерна стали. Второй спад ударной вязкости наблюдался на расстоянии около 10 мм от оси шва, обусловлен, по всей вероятности, отпускной
хрупкостью легированного феррита (так называемая 475-град хруп, кость феррита) [27]. Отпускная хрупкость проявлялась после натре, ва в температурном интервале 350-550 °С. Последующей термической обработкой при 950 *С ударная вязкость может быть вновь повышена до исходных величин.
Сварку стали 10Х28АН проводили электродуговым способом с применением ферритно-аустенитных электродов с азотом или аустенитно-ферритных. В работах [25,27] Ю.И.Казенновым разработаны электроды марки 39А (со стержнем из стали 10X28АН и покрытием, содержащим порошковый никель) и новая электродная проволока Х26Н4А. При применении проволоки Х26Н4А электроды могут изготавливаться с любым простым покрытием, например ЭНТУ-3, Ф-1 и др. Наименее склонными к кристаллизационным (горячим) трещинам оказываются сварные швы, содержащие около 0,2- 0,25 % N, 3-4% Ni и 25- 27% Cr. Наплавленный металл с указанной системой легирования обладает механическими свойствами, мало отличающимися от свойств основного металла. Шов имеет ферритно-аустенитную структуру (рис. 31). Механические свойства сварных соединений на стали 10Х28АН, выполненных электродом 39А следующие: σΒ = 618 МПа, ая = 0,68МДж/м2 при надрезе по шву, ан = 0,31 МДж/м2 при надрезе по основному металлу, угол загиба 180°. В НИИхиммаше также разработаны электроды марки ЗБ, обеспечивающие получение сварных швов состава Х23Н1Б, а также электроды марки КБ-3. Эти электроды, давая аустенитно-ферритную структуру металла шва, обусловливают более низкий порог хладноломкости, чем у основного металла.
2. СКЛОННОСТЬ СВАРНЫХ СОЕДИНЕНИЙ СТАЛИ IOXMAH К НОЖЕВОЙ КОРРОЗИИ
Для определения области применения стали 10Χ28ΑΉ в химическом аппаратостроении под руководством И.Г.Воликовой были проведены исследования их коррозионной стойкости в типовых коррозионно-активных средах, так как эти стали могут быть склонны к MKK [25,27]. Было проверено, можно ли применять для них существующие ускоренные методы испытаний; в стандартном сернокислом растворе медного купороса; в 10 %-ном растворе NaNO3 с добавкой 2 % HF и 65 %-ном растворе HNO3 при кипении с цикличным методом исследования. Оказалось, что для стали 10Х28АН могут быть применены без изменений все три метода, но рекомендуется проводить испытание в стандартном сернокислом растворе медного купороса, в котором происходит минимальная общая коррозия. Основной металл стали 10Х28АН в состоянии поставки
оказался не склонным к MKK после испытания во всех трех указанных растворах.
Испытания сварных соединений в таких агрессивных кипящих средах, как 59 %-ная HNO3, 97 %-ная CH3COOH, 55 %-ная H3PO4 и др., показали значительное коррозионное поражение основного металла в зоне термического влияния. Наряду с развитием MKK в этих участках протекала и структурно-межкристаллитная коррозия. Под структурно-межкристаллитной коррозией понимается коррозионное разрушение металла, происходящее по границам зерен, с одновременным избирательным растворением второй фазы. Воз- никновение склонности к структурно-мехкристаллитной коррозии, как показали металлографические исследования, связано со структурными изменениями металла в результате высокотемпературного сварочного нагрева.
Увеличение продолжительности выдержки металла в интервале температур 900-1000 eC свыше 20 мин способствует уменьшению, а затем и ликвидации межкристаллитной коррозии. При этом вследствие превращения а- у и протекающих диффузионных процессов происходит выравнивание концентрации твердого раствора по зерну и коагуляция карбидной фазы. Путем термической обработки сварных соединений возможно повысить их коррозионную стойкость.
Отжиг при 930-950 0C с выдержкой (для толщин З мм) при этой температуре 30- 40 мин и охлаждение на воздухе сварных соединений из стали 10Х28АН обеспечивает устойчивость против межкристаллитной коррозии во всех типовых средах (HNO3, H3PO4, уксусной CH3COOH) и механические свойства сварных соединений оказываются равноценными свойствам основного металла в состоянии поставки.
Следует отметить, что термическая обработка применима только для сварных соединений из стали 10Х28АН, швы которых имеют ферритно-аустенитную структуру (см. рис. 31). Для сварных соединений с аустенито-ферритными швами такая термическая обработка не рекомендуется из-за образования в них о-фазы, вызывающей снижение пластических свойств металла шва. Ударная вязкость металла шва снижается до 0,2 МДж/м2.
3. СТРУКТУРА СВАРНОГО СОЕДИНЕНИЯ СТАЛИ МАРКИ 10Х28Н4
Исследование структуры стали 10Х28Н4 проведено на горячекатаном листе толщиной 3 мм (плавка N0 11) после отжига при 900 °С, 30 мин с охлаждением ка воздухе. Химический состав стали 10Х28Н4
(плавка №11) следующий, %: 0,11 С; 0,50 Si; 0,82 Mn; 28 Cr; 4,0 Ni, Сталь сваривали электродами, дающими ферритно-аустенитную структуру, с системой легирования Cr-Ni-Nb-Al-Ti. Сварочные технологические свойства стали 10Х28Н4 без азота мало отличаются от таких же показателей для стали марки 10Х28АН.
На рис. 32, о представлена структура шва сварного соединения стали 10Х28Н4 - она состоит из ферритной основы, в которой выделились частицы аустенита в виде продолговатых ромбов. В зоне совместной кристаллизации аустенитная фаза выделяется по границам столбчатых кристаллов в виде узких длинных пластин (рис. 32, б). На рис. 32, а также представлена структура зоны термического влияния. Здесь виден рост ферритных зерен до № 3-4 и выделение вторичной фазы по границам зерен феррита. Просмотр структуры при больших увеличениях (х.1000 и х.2000) показал, что на границах зерен феррита в зоне перегрева сварного соединения из стали 10Х28Н4 выделились неравновесные сложные хромистые карбиды в виде листовидных розеточных пластинок (рис. 32, б, г). Наиболее отчетливо строение карбидов просматривается под электронным микроскопом (рис. 32, в). При высокотемпературном сварочном нагреве в пришовной зоне на границах зерен феррита первоначально выделилась аустенитная фаза, в которой растворимость углерода гораздо больше, чем в феррите. При последующем охлаждении происходит распад аустенита на феррита карбидную смесь.
Отмеченные изменения структурного состояния основного металла· стали 10Х28Н4 в зоне перегрева приводят, как следствие, к низкой его стойкости против МКК, которая весьма четко проявляется при испытании в стандартных растворах. Таким образом, установлено, что сварные соединения стали 10Х28Н4 нельзя использовать как коррозионностойкий материал в химическом машина строении.
Глава VH
ХРОМОНИКЕЛЕВЫЕ КОРРОЗИОННОСГОЙКИЕ СТАЛИ АУСТЕНИТНОГО КЛАССА
Наибольшее применение в промышленности среди коррозионностойких сталей получили хромоникелевые стали с титаном марок 12Х18Н9Т, 08Х18Н10Т; 12Х18Н10Т и 08Х18Н12Т, различающиеся между собой содержанием углерода, никеля и отношением титана к углероду (Ti/C). Титан относится к сильным ферритообразующиь· элементам, и, чтобы не допустить появления двухфазности (V + о)· необходимо иметь в стали несколько повышенное содержаний
никеля (порядка 10 %). Когда это не учитывается, в стали 12Х18Н9Т появляется ферритная фаза, которая в прокатанном металле располагается в виде вытянутых вдоль прокатки волокон.