Металлография
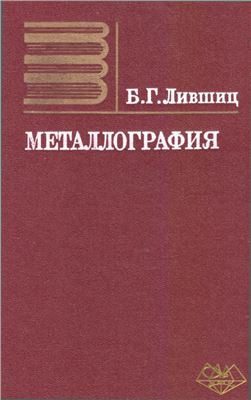
Лившиц Б.Г
Металлургия, 1990 г.
СТРУКТУРА СТАЛИ ПОСЛЕ ХИМИКО-ТЕРМИЧЕСКОЙ ОБРАБОТКИ И ОКИСЛЕНИЯ
Химико-термической называется такая обработка, при которой заданным образом изменяется состав поверхности изделия. Поверхностный слой измененного состава называют диффузионным. При химико-термической обработке металлическое изделие помещают в среду, содержащую тот компонент, который должен продиффундировать в поверхностный слой изделия. Таким образом, в одном изделии (в середине и на поверхности) удается получать различные свойства.
Химико-термическую обработку применяют для повышения твердости на поверхности, для защиты изделия от коррозии, от окалинообразования при высокой температуре и других целей. Ею пользуются при изготовлении не только стальных изделий, но также и изделий из меди, титана, молибдена и других металлов и сплавов.
Рассмотрим изотермическую при температуре Τ диффузию компонента В в металл А через его поверхность в условиях, при которых достигается насыщение твердого раствора α на основе А. Как следует из теории диффузии, при достижении такого насыщения продолжение диффузии В приводит к появлению на поверхности той фазы, которая следует за α-фазой на диаграмме равновесия при продвижении от А к β по оси концентраций. Обозначим эту фазу буквой β. При этом α-фаза проникает в глубь металла. Двухфазная область α + β получиться не может.
При дальнейшей диффузии может получиться на поверхности следующая (по оси концентраций диаграммы равновесия) фаза γ и т. д. Итак, на поверхности образуются чередующиеся фазы γ, β, α. Если при комнатной температуре наблюдается гетерогенная структура, то это однозначно свидетельствует о том, что какая-либо из высокотемпературных фаз распалась при охлаждении с температуры Т.
Распространенными химико-термическими обработками низкоуглеродистой стали являются цементация и азотирование. При цементации стальное изделие насыщается с поверхности углеродом, при азотировании — азотом. Цементацию проводят путем нагрева изделий при высокой температуре (выше Aci) в твердой, жидкой или газообразной среде. На рис. 246 показана микроструктура цементованной стали, содержащей 0,1 % С. Как видно из рисунка, сталь в своей основной массе состоит из феррита с небольшим количеством (около 10%) перлита (середина). По мере продвижении к краю количество перлита в микроструктуре увеличивается до 100 % и затем наряду с ним появляется сетка вторичного цементита (край). Сталь постепенно из доэвтектоидной становится эвтектоидной и заэвтектондной, так как содержание углерода в ней увеличивается. При температуре, например, 1000 °С (рис. 247) во время цементации сталь находилась в аустенитном состоянии, и науглероживание протекало путем диффузии углерода в аустените в пределах концентраций, определяемых на рис. 247 линией ab. После цементации медленное охлаждение привело к распаду аустеннта и получилась микроструктура, приведенная на рис. 246.
Часто в производственных условиях при прокатке, ковке, термической обработке и других технологических процессах под влиянием кислорода воздуха сталь, нагретая до высокой температуры, обезуглероживается с поверхности. На поверхности изделия может образоваться слой железа, почти не содержащий углерода, который выгорает и удаляется в виде CO2 .
Обеднение углеродом поверхности вызывает его диффузию изнутри и дальнейшее удаление с поверхности в окислительной атмосфере. На рис. 247 такой процесс можно представить перемещением содержания углерода от точки b к точке а (при 1000 °С). Диффузия углерода, согласно этой схеме, идет в аустените, который в результате приобретает переменный состав в диффузионном слое. После медленного охлаждения стали, например с 1,35% С (точка b) до комнатной температуры, аустенит испытывает фазовые превращения. На поверхности изделия образуется феррит, далее вглубь послойно — феррит + перлит, перлит и перлит + вторичный цементит.
СТРУКТУРА ЛИТОЙ И ДЕФОРМИРОВАННОЙ СТАЛИ
Подавляющее количество стали отливают в виде слитков, затем их прокатывают или (реже) проковывают при высокой температуре. Получение хорошей структуры стали в результате соответствующих технологических операций очень важно, так как все дефекты стали, появившиеся на металлургическом заводе, переносятся на готовые изделия в машиностроении, приборостроении и т. д. Стальной слиток, затвердевший в изложнице, в верхней части имеет усадочную раковину. Причиной образования усадочной раковины является сжатие стали в жидком состоянии и при затвердевании. Усадочная раковина внутри слитка заполнена газами, выделяющимися из стали при ее охлаждении. Необходимо, чтобы усадочная раковина была сосредоточена в верхней части слитка; для этого различными способами в процессе затвердевания в этой части слитка поддерживают высокую температуру (выше температуры плавления). Иногда получается не сплошная усадочная раковина, а перегороженная так называемыми «мостами», как показано на рис. 138. Если сталь недостаточно раскислена, то при ее затвердевании выделяется много газов, особенно СО, которые не могут пробить себе дорогу через затвердевшую поверхность слитка и остаются в нем в виде газовых пузырей (рис. 248). Раковины и пузыри можно обнаружить невооруженным глазом, если разрезать слиток вдоль или поперек. Описанные дефекты слитка составляют практически важную особенность его макроструктуры. Указанное относится и к макроструктуре отливок готовых изделий, не подвергшихся обработке давлением.
Кроме того практически очень важно в макроструктуре стального слитка его дендритное строение. В общем виде оно описано на с. 45. В сечении слитка стали ясно видны три зоны кристаллизации:
1) зона мелких дендритов;
2) зона вытянутых от поверхности к середине слитка дендритов, ориентированных своей большой осью вдоль направления тсплоотвода, т. е. зона столбчатой кристаллизации
3) зона крупных равноосных дендритов в средней части слитка, не имеющих преимущественной ориентировки.
Дендритное строение слитка выявляют на шлифованной поверхности разреза с помощью травления соответствующим реактивом. При этом получается рельеф, который обязан споим возникновением дендритной ликвации. В пределах дендрита распределение химических элементов неоднородно. Оси дендритов, затвердевающие в первую очередь, содержат гораздо меньше примесей, загрязняющих сталь (серы, фосфора), и обычных спутников технического железа, таких как кремний, марганец и др., чем межосные пространства, в которые эти примеси оттесняются при образовании дендрита.
ной стали содержат повышенное количество углерода. При затвердевании углерод, как и другие примеси, скапливается в межосных пространствах, но затем, как показал Стед (1915 г.), углерод под влиянием фосфора вытесняется к осям дендритов. Все названные элементы при высокой температуре находятся в растворе (в у-железе), за исключением серы, которая присутствует в виде сульфидов (Mn, Fe)S. Вследствие обогащения межосных пространств серой и фосфором они сильнее вытравливаются на шлифе под действием реактива, чем осп, и таким образом получается рельеф, воспроизводящий дендритное строение.