Магниевые сплавы с иттрием
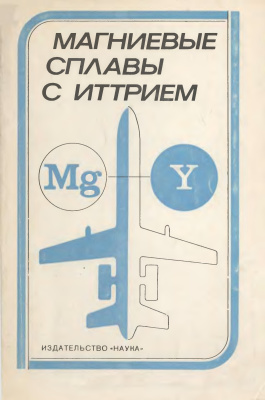
Дриц М.Е., Рохлин Л.Л., Падежнова Е.М., Гурьев И.И., Миклина Н.В., Добаткина Т.В., Орешкина А.А.
Наука, 1979 г.
ТЕХНОЛОГИЯ ПЛАВКИ. ЛИТЬЯ И ОБРАБОТКИ ДАВЛЕНИЕМ ДЕФОРМИРУЕМЫХ МАГНИЕВЫХ СПЛАВОВ С ИТТРИЕМ
Технология плавки и литья слитков
Высокая концентрация дорогостоящего иттрия в большинстве деформируемых магниево-иттриевых сплавов определяет особенности технологии производства из них слитков, а именно плавку в условиях контролируемой атмосферы защищающей расплав от окисления.
Для этой цели используют плавильно-литейный агрегат для бесфлюсовой плавки, состоящий из индукционной тигельной печи, гидравлической литейной машины и устройств для переливания расплава [109—112]. Проведение плавки без флюса обеспечивает малые потери иттрия во время плавки. В этом агрегате печь одновременно служит и миксером. Агрегат питается от сети переменного тока промышленной частоты напряжением 380 В. Печь состоит из стального каркаса, магнитопроводов, индуктора, тепловой изоляции и тигля. Тигель печи сварен из листовой стали, внутренняя часть печи выложена шамотным кирпичом. Дно тигля имеет сферическую форму.
Схема плавнльно-литейного агрегата представлена на рис. 80.
В качестве защитной атмосферы при выплавке слитков на этом агрегате используют либо аргон, либо сернистый ангидрид, С целью очистки расплава от окисных плен, образующихся в результате реакции взаимодействия его с кислородом, содержащимся в защитной атмосфере и натекающим в тигель извне, а также от поверхностной плены окислов, внесенных в расплав шихтой, применяют отстаивание расплава при высокой температуре с последующей его фильтрацией через металлическую сетку при транспортировке из печи в кристаллизатор литейной машины.
При приготовлении сплавов в качестве шихты используют первичные металлы, лигатуры магний — иттрий, магний — марганец, магний — цирконий и т. д., а также отходы соответствующих магниево-иттриевых сплавов.
Технологический процесс приготовления сплавов предусматривает следующий порядок операций. В тигель загружают максимально возможное количество шихты. По окончании загрузки шихты загрузочные люки закрывают. В тигель подают защитную атмосферу, включают печь.
Подгрузку чушкового магния, лигатур магний — марганец, магний — иттрий, магний — цирконий и других шихтовых материалов осуществляют по мере оплавления и опускания шихты. После расплавления всей шихты производится съем окисных плен с поверхности расплава. После присадки легирующих элементов расплав перемешивают в течение не менее 15 минут и затем при температуре 760—780° С отбирают пробы на экспресс- анализ. По результатам экспресс-анализа производится подшихтовка и расшихтовка до среднего химического состава.
Расплав перегревают на 50° С выше температуры литья, чтобы обеспечить возможность осаждения окисных плен и шлака при последующем охлаждении при выключенной печи. Печь выключают. Расплав выстаивают при выключенной печи в течение 30—40 минут с охлаждением металла до температуры литья. Затем производят затравку металла через инжектор, включают электромагнитный насос, начинают литье. Во время литья подачу газа в тигель не прекращают. В кристаллизатор и коробку подают сернистый ангидрит.
Литье слитков из магниевых сплавов производится на машинах полунепрерывного литья с гидравлическим приводом как наиболее обеспечивающим выполнение заданных технологических режимов отливки.
Наиболее распространенным типом кристаллизатора при литье магниевых сплавов является корпусной кристаллизатор, состоящий из корпуса и гильзы. Гильза изготавливается с внутренним конусом в 1,5—2,0 градуса из материалов с высокой теплопроводностью. Ниже приводятся основные размеры кристаллизаторов, применяемых при отливке слитков, угол подачи воды на слиток, а также режимы литья круглых и плоских слитков магниево-иттриевых сплавов.
Отлитые слитки проходят контроль на чистоту металла с помощью изломов темплетов, взятых от донной, литниковой и средней частей.
Технология прокатки листов и плит
Производство листков и плит магниево-иттриевых сплавов осуществляется карточным методом. Технологический процесс аналогичен процессу производства этих полуфабрикатов из серийных магниевых сплавов:
а) подготовка слитков;
б) горячая прокатка слитков;
в) теплая прокатка листов;
г) термическая обработка;
д) правка и резка;
е) зачистка поверхности листов и плит;
ж) химическая обработка поверхности листов и плит.
Плоские слитки, отлитые полунепрерывным методом с охлаждением водой, подвергаются фрезерованию со съемом 12— 20 мм по большим плоскостям и малым граням для удаления ликвационных скоплений, неслитин и других поверхностных дефектов.
Таблица 44
Режимы гомогенизации сплавов
Сплав | Температура нагрева, | Время выдержки, ч |
ИМВ6 | 540 | 12 |
ИМВ8 | 510 | 12 |
ИМВ5 | 510 | 12 |
ИМВ7 | 510 | 12 |
ВМД10 | 450 (I) + 480(11) | I—6+II—10 |
Примечание. I — первая ступень нагрева; II — вторая ступень нагрева.
Таблица 45
Режимы горячен прокатки слитков из сплава ИМВ6
Сплав | Вид изделия | Температура прокатки, °С | Обжатие за | Температура, | |
начала | конца | проход, % | валков, °С | ||
ИМВ6 | Лист Плита | 480—500 480—500 | 320—370 350-380 | 10—33 10-24 | 90 90 |
Гомогенизацию большинства магниевых сплавов проводят с целью получения однородной структуры слитка и повышения пластичности сплавов. Режимы гомогенизации сплавов приведены в табл. 44.
Перед началом горячей прокатки слитки нагревают до соответствующих температур в электрических печах конвейерного типа с циркуляцией воздуха. Время нагрева слитков составляет от 4 до 10 ч в зависимости от массы заготовки.
Нагретые заготовки прокатывают на плиты или листы (подкат) за 11—21 проход в зависимости от конечной толщины.
Валки прокатных станов перед началом горячей или теплой прокатки подогревают специальными нагревательными устройствами.
Для горячей прокатки магниево-иттриевых сплавов применяют реверсивный трехвалковый прокатный стан. Для уменьшения налипания металла и окислов на валки используют смазку, наносимую на поверхность валков из пульверизатора или (при горячей прокатке) применяют водомасляную эмульсию, которая смывает с поверхности валков налипшие окислы.
В настоящее время катаные полуфабрикаты изготавливают из сплава ИМВ6 по режимам, приведенным в габл. 45.
После прокатки обрезают передний и задний концы, а также кромки прокатанных листов и плит. Далее плиты подвергают правке на. гидравлическом прессе, а листы режут на карточки для последующей прокатки. Плиты затем подвергаются контрольным испытаниям и поступают на отделку.
Теплая прокатка ведется на двухвалковом стане. Перед теплой прокаткой заготовки из сплава ИМВ6 подвергают химической обработке для очистки поверхности от окислов.
Режимы теплой прокатки листов из сплава ИМВ6: температура начала прокатки 390—490° С, температура конца прокатки 90—110° С, обжатие за проход 2—10%, обжатие за нагрев 20%.
С целью получения листовых полуфабрикатов требуемой геометрии и заданного качества поверхности применяют отделочные операции, включающие резку, правку под грузом, механическую зачистку поверхности листов, а затем оксидирование.
Технология производства прессованных полуфабрикатов
Технология изготовления прессованных изделий сводится к следующему, гомогенизированные заготовки после обточки подвергаются нагреву перед прессованием. Для изделий малого сечения применяют предварительно деформированные заготовки, что способствует уменьшению расхода энергии при прессовании по сравнению со слитком, а также повышает суммарную степень деформации.
Нагрев слитков (заготовки) перед прессованием осуществляют в индукционных печах промышленной частоты или в электрических методических печах сопротивления с воздушной циркуляцией. Приняты следующие режимы прессования магниево- иттриевых сплавов: температура контейнера 400—420° С; температура заготовок 460—490° С, скорость истечения при прессовании литой заготовки 0,5—2,0 м/мин, скорость истечения при прессовании прессованной заготовки 1,0—3,0 м/мин.
По окончании прессования осуществляют правку на растяжных машинах с остаточной деформацией не более 3% при температуре 200—250° С. Растяжка производится сразу же вслед за прессованием. Далее прессованные изделия из магниево-ит- триевых сплавов подвергают травлению и оксидированию.
Технология производства штамповок из магниево-иттриевых сплавов
Штамповки из магниево-иттриевых сплавов изготавливают на гидравлических прессах в закрытых штампах. Исходной заготовкой служат прессованные прутки различных диаметров. Принятые в настоящее время температурные интервалы штамповки учитывают следующие положения: при горячей обработке давлением наблюдается большая зависимость пластичности сплавов от температуры. Высокая температура окончания деформирования позволяет использовать наибольший запас пластичности сплавов, но при этом образуется более крупнозернистая структура, что в свою очередь, вызывает снижение уровня механических свойств и уменьшение анизотропии материала.
Нагрев заготовок перед штамповкой производится в воздушных электрических печах с нихромовыми нагревателями или в индукционных печах промышленной частоты.
Нагрев заготовок для штамповки сплава ИМВ6 проводится обычно при температурах порядка 450° С. В случае сплава ВЛ1Д10 используется нагрев при более низких температурах — порядка 370° С. Скорость деформирования при штамповке обычно составляет 1,0—1,5 м/мин. При низких температурах штамповки металл при деформировании может несколько нагреваться (на 20° С). Однако разогрев при деформировании может быть незначительным, и температура металла после штамповки может оказаться даже более низкой, чем до штамповки.