Литые прокатные валки
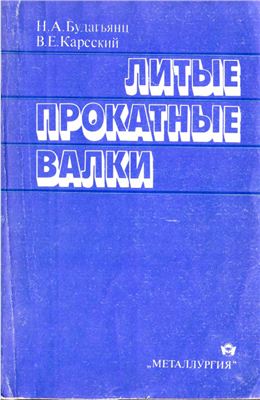
Будагьянц Н.А., Карсский В.Е.
Металлургия, 1983 г.
Глава I. ВИДЫ ВАЛКОВ И ИХ ХАРАКТЕРИСТИКИ
В СССР применяются свыше 50 типов чугунных и стальных литых валков для прокатки металла. Каждый из них имеет свои особенности, а требования к ним обусловливаются техническими условиями. Все валки должны обладать высокими эксплуатационными качествами, которые определяются в основном их твердостью, прочностью и термостойкостью. Эти качества определяют высокую износостойкость валков и способность их противостоять резким изменениям температуры в процессе прокатки. Кроме того, валки должны обеспечивать высокое качество поверхности проката и требуемый захват металла.
Чугунные валки всех видов отливают в комбинированную форму, состоящую из чугунного или стального кокиля, в котором происходит ускоренная кристаллизация рабочего слоя бочки валка, и опок с отформованными в них шейками, трефами и прибыльной частью. Отливают валки вертикально, с тангенциальной установкой питателя в нижней части формы. Такой способ подвода питателя обеспечивает вращение металла, необходимое для получения чистой поверхности валка. В процессе вращения все более легкие частицы (шлак, неметаллические включения) и газы перемещаются к центру валка и затем выносятся в прибыль. Сифонная установка питателя при всех своих преимуществах имеет и крупный недостаток, заключающийся в том, что после заливки наиболее горячая часть валка находится внизу, что нарушает направленное затвердевание металла — снизу вверх. Поэтому при отливке многих стальных валков, затвердевающих в небольшом интервале температур кристаллизации, металл заливают через прибыльную часть формы валка (рис. 1).
ИЗМЕРЕНИЕ ТВЕРДОСТИ ПРОКАТНЫХ ВАЛКОВ
В эксплуатации прокатные валки должны обладать определенным комплексом физико-механических свойств. Но специфика вальцелитейного производства не позволяет произвести контрольные испытания всех отлитых валков. Вырезать образцы для испытаний из готовых валков невозможно, а образцы отлитые для контроля из валкового расплава, вследствие разницы в массе отливок и условиях кристаллизации по своим физико-механическим свойствам не идентичны готовым валкам.
Одной из главных характеристик валков является твердость рабочего слоя, регламентируемая техническими условиями на поставку валков.
Твердость определяют на поверхности бочки и в глубине рабочего слоя. Для испытания твердости и проверки микроструктуры на глубину рабочего слоя бочку отливают на 50—70 мм длиннее заданного размера. Из этого припуска при обработке валков на станке отрезают кольца, от которых отбирают темплеты для лабораторных испытаний. Испытуемая поверхность образца не должна иметь рисок. В случае необходимости ее шлифуют.
Структура литых прокатных валков относительно крупнозернистая и состоит из неоднородных по твердости составляющих. Поэтому наиболее точные усредненные показатели могут быть получены при измерении твердости на твердомерах Бринелля, позволяющих охватывать площадку в несколько квадратных миллиметров. Но твердомер Бринелля с шариком диаметром 10 мм, изготовленным из закаленной стали, непригоден для испытания валков твердостью > НВ 450 вследствие возможной опасности деформации или поломки шарика. Кроме того, на темплетах отбеленных валков с высоким содержанием углерода и большим количеством» хрупкой карбидной составляющей в микроструктуре отбеленного слоя при вдавливании шарика часто образуются трещинки по радиусам лунки, искажая результаты замеров. Поэтому на твердомере Бринелля при нагрузке 3000 кг испытывают образцы, отобранные от валков твердостью рабочего слоя <НВ 400-450, а также от шеек всех валков.
Структура рабочего слоя валков с высокой твердостью более мелкозерниста, и поэтому для испытания твердости таких валков применяют твердомер Роквелла, работающий по принципу вдавливания наконечника с алмазным конусом в испытуемый образец при нагрузке 150 кг. Шкала твердомера Роквелла показывает твердость в условных единицах.
КЛАССИФИКАЦИЯ ЛИТЫХ ВАЛКОВ
В зависимости от применяемого материала валки делят на чугунные и стальные. Такое деление несколько условно, так как существуют виды валков, которые по структуре и свойствам можно отнести как к стальным, так и к чугунным. Это валки из железоуглеродистых сплавов с содержанием 1,8-2,6 % С.
При содержании углерода до 2 % их обычно относят к стальным валкам, а при содержании углерода в пределах 2,0—2,6 % — к низкоуглеродистым чугунам. За рубежом их называют полустальными или валками со стальной основой.
В зависимости от назначения валки изготовляют двух типов: листопрокатные (Л) для прокатки листов любой толщины как из черных, так и цветных металлов и сортопрокатные (С) для прокатки всех видов сортового металла, включая рельсы и широкополочные балки. К этой же группе относятся валки для прокатки труб (Т) . Деление валков на типы также условно, так как валки типа Л в некоторых случаях можно использовать в сортопрокатных станах и наоборот.
По форме графитовых включений чугунные прокатные валки делят на палки с пластинчатым графитом (П) и валки с шаровидным графитом (Ш). В последнем случае графитовые включения могут иметь форму правильных и неправильных глобулей. Микроструктура рабочего слоя прокатных валков может быть перлито-карбидной, перлито-карбидо-графитной и перлито-графитной. В легированных валках могут содержаться и другие продукты превращения аустенита - верхний и нижний бейнит, мартенсит.
Для более полной характеристики валков в конце буквенного обозначения типа валков цифрами указывают нижний предел твердости рабочего слоя валка в единицах Шора. Такое обозначение широко принято и за рубежом, но некоторые зарубежные фирмы ставят среднее значение твердости, характерное для данного типа валков.
В зависимости от выполняемой функции валки делятся на рабочие и опорные.
Литые стальные валки, применяемые в различных станах, включают валки из доэвлектоидных сталей (0,4-0,8 % С), эвтектоидных (0,75— 0,9 %) и заэвтектоидных (1,2—2,0 %) как нелегированные, так и легированные. Особенно широкое применение нашли валки из заэвтектоидной стали, легированной хромом, никелем и молибденом — 150ХНМ и 180ХНМ. Необходимые свойства валкам придаются в зависимости от их назначения соответствующей термической обработкой. За рубежом такие валки часто используют не только в сортопрокатных, но и в листовых станах.
ХИМИЧЕСКИЙ СОСТАВ И СТРУКТУРА ВАЛКОВ
Требования к валкам очень разнообразны и нередко противоречивы. Так, высокую твердость рабочего слоя трудно получить в сочетании с высокой термостойкостью и прочностью и часто вязкостью металла сердцевины, шеек и трефов валка. Поэтому перед вальцелитейщиками ставится сложная задача: в различных зонах одной и той же отливки получить металл с различными физико-механическими свойствами. А так как свойства любой стальной или чугунной отливки определяются сочетанием микроструктурных составляющих железоуглеродистых сплавов, образующихся при затвердевании и охлаждении отливок, то основным критерием, определяющим физико-химические свойства валка, является его структура.
Сравнительная твердость НВ отдельных структурных составляющих железоуглеродистых сплавов приведена ниже:
Цементит Fe3C...........................800-1000
Феррит. Технически чистое железо................80—100
Графит. Форма пластинчатая ипи шаровидная.........3—5
Аустенит. Твердый раствор углерода в γ-железе.......180—200
Мартенсит. Игольчатая структуре, высокодисперсная
форма превращения кристаллов аустенита..........600—800
Бейнит, Дисперсная форма распада кристаллов аустенита 450—600
Перлит тонкопластинчатый, слабо дифференцированный
Механическая смесь цементита и феррита...........300—450
Перлит пластинчатый, отчетливо дифференцированный. Конечный продукт распада аустенита. Механическая смесь пластинок цементита и феррита.................200—300
В чугунных литых валках встречаются все структуры железоуглеродистых сплавов. Одними из основных факторов, определяющих заданную структуру валка, являются химический состав металла и скорость охлаждения. В чугунных и стальных валках, кроме железа и обычно сопутствующих элементов (углерода, кремния, марганца, фосфора и серы) могут содержаться хром, церий, никель, кальций, молибден, медь, магний и алюминий.
В ограниченных количествах для легирования валков применяют бор, титан, ванадий, ниобий. Для корректировок жидкого металла при отливке отбеленных валков широко применяют теллур. Кроме того, в любом валковом расплаве содержатся газы: кислород (почти весь в виде оксидов), водород и азот.
Перечисленные элементы оказывают на расплав карбидообразующее или графитизирующее действие.
Углерод
Углерод в железоуглеродистых расплавах при ускоренном охлаждении образует карбиды железа (цементит) и выделяется в виде свободного углерода (графита) при замедленном охлаждении. Присутствие в расплаве таких элементов, как хром, марганец, сера, молибден, также ведет к образованию карбидов железа, а никель, алюминий и особенно кремний — к образованию графита.
Способность углерода в железоуглеродистых сплавах в зависимости от условий охлаждения образовывать карбиды железа или выделяться в виде графита широко используют при производстве валков, особенно чугунных. Применяя разную скорость охлаждения различных частей валка (бочки, шеек), получают различные структуры, обеспечивающие необходимые для эксплуатации свойства — прочность, износостойкость, способность противостоять резким изменениям температуры и др.
Содержанием углерода при производстве валков с отбеленным слоем из нелегированного белого чугуна определяется твердость рабочего слоя, которая тем выше, чем больше в нем белой (карбидной) составляющей (рис. 13). Повышение твердости отбеленного слоя связано линейной завиcимостью с содержанием углерода: Hш = 16,67 % С + 13, где Hш — твердость по Шору. Эта зависимость характерна для содержания углерода