Литейные сплавы и технология их плавки в машиностроении
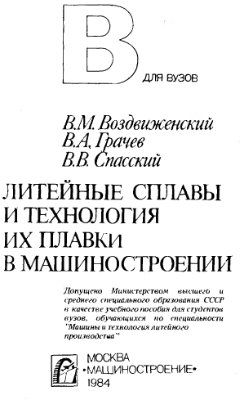
Воздвиженский В.М.
Машиностроение, 1984 г.
ОБРАЗОВАНИЕ НАПРЯЖЕНИЙ И ТРЕЩИН. ТРЕЩИНОУСТОЙЧИВОСТЬ СПЛАВОВ
ВИДЫ НАПРЯЖЕНИЙ.
В процессе формирования отливки и охлаждения до температуры окружающей среды в ней возникает сложное напряженное состояние. По физической природе и размерам области уравновешивания различают напряжения I рода—зональные напряжения, возникающие в макрообъемах, с градиентом по всей отливке или отдельным крупным частям ее; напряжения II рода—в микрообъемах, в пределах микрозерна или группы зерен; напряжения III рода—в субмикроскопических областях, в пределах кристаллической решетки.
При изучении сплавов необходимо рассматривать напряженное состояние и механизм релаксации напряжений раздельно в микрообъемах (на уровне отдельных структурных составляющих) и макрообъемах (т. е. в отливке в целом или в отдельных крупных частях ее). Микропластические сдвиги, исчерпание запаса пластичности и местные разрушения — образование микротрещин — могут происходить без заметных внешних изменений в геометрии отливки. Макроизменения будут наблюдаться только после сильной пластической деформации в большинстве зерен или при образовании крупных трещин за счет роста и слияния мелких.
По источнику происхождения напряжения подразделяют на усадочные — возникающие в результате сопротивления усадке металла со стороны формы и стержней; термические — возникающие за счет градиента температур по сечению отливки и неравномерного или неодновременного сжатия (расширения) отдельных частей отливки, слоев и структурных зон; фазовые — возникающие в результате различия удельных объемов фаз при фазовых превращениях. Независимо от источника происхождения все эти напряжения алгебраически складываются, и их результирующее воздействие зависит от соотношения суммарного напряжения и механических свойств сплава.
Усадочные напряжениявсегда растягивающие. Их величина зависит от сопротивления формы и стержней. По размерам области уравновешивания— это в основном напряжения Iрода. При высоких температурах происходит релаксация усадочных напряжений вследствие пластической деформации. С переходом сплава в упругоесостояние напряжения накапливаются и достигают максимума к моменту выбивки отливки из формы; после выбивки напряжения частично снимаются.
Термические напряжениязависят не только от условий формирования отливки, но и от теплофизических свойств сплава. Например, уменьшение теплопроводности сплава увеличивает градиент температур по сечению отливки и, следовательно, уровень напряжений I рода. Очевидно также влияние температурного коэффициента линейного расширения а на уровень напряжений I рода. В результате различия а структурных составляющих могут возникать также термические напряжения II рода. Анализ процесса возникновения термических напряжений [8] показывает, что остаточные напряжения не зависят от размеров отливки и пропорциональны различию сечений элементов отливки. При этомв толстых сечениях развиваются растягивающие напряжения, втонких — сжимающие.
Фазовые напряженияв наибольшей степени зависят от свойств сплава (точнее, от свойств фаз и структурных составляющих). Возникновение и уровень напряжений определяются: 1) различием удельных объемов фаз; 2) упругими и пластическими свойствами матрицы сплава (т. е. основной структурной составляющей); 3) последовательностью протекания фазового превращения в объеме отливки (из-за наличия градиента температур фазовые превращения протекают, как правило, не одновременно). Из сказанного очевидно, что по размерам области уравновешивания это напряжения I и II рода.
Большое значение имеет температура, при которой происходит фазовое превращение, так как с повышением температуры свойства матрицы и избыточных фаз сильно изменяются: снижается прочность и повышается пластичность. Поэтому при высокотемпературных превращениях, даже в случае большого различия удельных объемов фаз, происходит релаксация напряжений в результате микропластических сдвигов и не возникает больших остаточных напряжений. Превращения при температурах в зоне упругости сплава и пониженной пластичности вызывают большие временные напряжения, релаксация которых может осуществляться только путем микроразрушений — образования микротрещин. Кроме того, сохраняются высокие остаточные напряжения. Наиболее опасны с этой точки зрения фазовые превращения в высоколегированных сталях с мартенситной матрицей, в отбеленных чугунах следебуритной матрицей и в жаропрочных сплавах, содержащих большое количество интерметаллидов.
Склонность сплавов к образованию напряжений оценивается различными технологическими пробами, которые представляют собой небольшие отливки, включающие участки с различным (усадочная решетка) или переменным сечением. По окончании охлаждения отливку разрезают, и существующие в ней напряжения вызывают деформации отдельных ее частей. Деформации измеряют специальными датчиками или непосредственным промером по базовым отметкам. По степени деформации рассчитывают значение напряжений. Размеры и конфигурация проб ГОСТом не регламентируются.
СНЯТИЕ НАПРЯЖЕНИЙ.
Для снятия напряжений обычно используют термическую обработку различных видов. При отжиге Iрода температура нагрева не связана с температурой фазовых превращений. Отжиг стальных и чугунных отливок обычно производится при температуре 450—650 °С в течение 2—10 ч. Отливки из алюминиевых сплавов отжигают при 250—350 °С. С повышением температуры нагрева скорость релаксации напряжений резко возрастает, и, следовательно, сокращается необходимая длительность отжига. Отжиг IIрода связан с фазовой перекристаллизацией сплава, поэтому он наиболее полно снимает напряжения в отливках и одновременно исправляет крупнозернистую структуру в сталях и некоторых сплавах.
Крупногабаритные чугунные отливки (базовые детали станков и т. п.) для частичного снятия остаточных напряжений и предотвращения коробления иногда подвергаются длительному вылеживанию в течение нескольких месяцев при температуре окружающей среды. Этот процесс обычно называют естественным старением, что не соответствует терминологии, принятой в металловедении.
ОБРАЗОВАНИЕ ТРЕЩИН В СПЛАВАХ.
В зависимости от температурных условий образования трещины подразделяют на горячие и холодные. Горячие трещины обычно имеют усадочное происхождение и возникают в интервале температур затвердевания сплава. Они проходят по границам макрозерна и имеют неровную окисленную поверхность, на которой иногда видны дендриты. В крупных дендритах горячие трещины могут образовываться по периферии дендритных ячеек. Холодные трещины возникают вследствие высоких внутренних напряжений в отливке. Они обычно имеют гладкую светлую или зернистую поверхность с цветами побежалости.
Зарождение и развитие трещин в отливках определяются четырьмя группами факторов:
1)податливостью формы, а также ее теплофизическими свойствами и конструкцией;
2) конструкцией отливки (наличием тепловых узлов и сочетанием различных сечений, способом подвода металла и т. д.);
3)условиями формирования отливки, определяющими последовательность затвердевания ее частей, а также возможность получения определенной макро- и микроструктуры сплава;
4)усадочными, механическими и теплофизическими свойствами сплава, а также характером его кристаллизации. Технологические условия литья влияют путем изменения кинетики формирования отливки.
В настоящее время проблема трещинообразования в отливках приобретает особое значение, так как широко используются неподатливые формы (кокили, пресс-формы для литья под давлением, керамические формы), а также высоколегированные специальные сплавы, содержащие большое количество хрупких интерметаллидных фаз и имеющие повышенную склонность к трещинообразованию.
Наиболее характерны для отливок горячие трещины, кинетика образования которых изучалась А. А. Бочваром, Н. Т. Гудцовым и их учениками. Было установлено, что горячие трещины начинают зарождаться с момента перехода сплава в твердожидкое состояние при температуре ниже температуры образования твердого скелета и начала свободной линейной усадки, т. е. в эффективном интервале затвердевания. Горячие трещины образуются вследствие торможения свободной усадки со стороны формы или стержней и локализации возникающей при этом деформации растяжения. В то же время при температурах, близких температуре солидуса, сплавы обладают низким комплексом механических свойств: малой прочностью (~ 1 —2 МПа) и пониженной пластичностью. Явление резкого падения пластичности вблизи tsполучило название высокотемпературной хрупкости, или горячеломкости а опасный интервал температур между tCKи tsбыл назван Н. Н. Прохоровым температурным интервалом хрупкости (ТИХ). В этом же интервале температур наблюдается наибольшая усадочная деформация. Такое неблагоприятное сочетание факторов приводит к повышенной вероятности образования трещин в зоне горячеломкости.
Зарождение и развитие трещин связаны с наличием некоторого количества жидкой фазы — «жидких прослоек» — по границам дендритов (порядка 5—15 %). По данным И. И. Новикова [21 ],
разрывы по стыкам дендритов образуются в том случае, когда усадочная деформация превосходит некоторую критическую величину, допустимую для интервала хрупкости. Если количество жидкой фазы более 20—25 %, то возможно «залечивание» возникших разрывов поступающим расплавом. Этим объясняется снижение горячеломкости при температуре, близкой к tCKили концентрации компонентов более Сск. Таким образом, можно говорить о некотором критическом количестве жидкой фазы, наиболее опасном с точки зрения образования горячих трещин.
Склонность сплавов к образованию трещин связана с шириной температурного интервала кристаллизации.
Развитие горячих трещин зависит также от макро-и микроструктуры сплавов. Наибольшей трещиноустойчивостью обладает равномерная мелкозернистая макро-и микроструктура, значительно меньшей — крупнозернистая равноосная структура. Столбчатая структура образует «поверхности слабины» в местах стыка двух фронтов кристаллизации. Включения окисных плен и неметаллических частиц также снижают трещиноустойчивость.
Фазовые превращения в сплавах действуют различным образом на трещиноустойчивость. Образование фаз с большим удельным объемом в твердожидком состоянии или при высокой температуре снижает усадочную деформацию и вследствие этого — склонность к образованию горячих трещин (выделение графита в серых чугунах резко повышает их трещиноустойчивость). В других случаях фазовая перекристаллизация увеличивает усадочную деформацию, и трещиноустойчивость падает. (Так влияет превращение б → у в низкоуглеродистых сталях).
По данным А. М. Королькова [15], в тройных и многокомпонентных сплавах причины и механизм возникновения горячих трещин такие же, как в двойных сплавах.
Необходимо отметить, что известные показатели горячеломкости обоих типов (т. е. использующие оценку запаса пластичности или предельную упругую деформацию) удовлетворительно коррелируются с экспериментальными данными, но не могут дать надежную априорную оценку свойств сплава. В связи с этим склонность сплавов к образованию трещин обычно оценивается по специальным технологическим пробам. Наибольшее распространение получили два метода: 1) определение «критического сечения» (или длины) образцов из сплавов различного химического состава, при котором в условиях полностью затрудненной усадки горячие трещины еще не появляются; 2) определение «критического состава»,
Борьба с горячими трещинами большей частью осуществляется технологическим путем (увеличением податливости формы, изменением конструкции отливки и т. д.), так как марка сплава обусловлена техническими условиями и не может произвольно заменяться. Однако нельзя недооценивать роли структуры и свойств сплава. Незначительные изменения химического состава (в пределах допуска), снижение содержания вредных примесей, введение небольших технологических добавок, модифицирование — все это может значительно увеличить трещиноустойчивость сплава и резко снизить брак по горячим трещинам без изменения технологии изготовления формы и конструкции отливки или тепловых условий ее формирования.