Литье слитков меди и медных сплавов
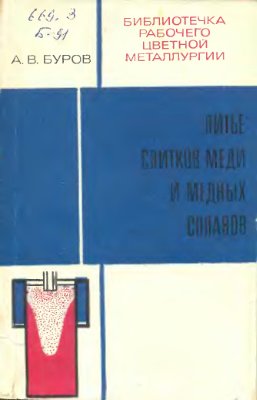
Буров А.В.
Металлургия, 1972 г.
Получение бескислородной меди
Из слитков бескислородной меди изготавливают трубы, прутки, ленты и полосы, поставляемые предприятиям радиотехнической и электронной промышленности. Значительное количество бескислородной меди используют также для получения проводников тока, различных профилей и шин, широко применяемых в электротехнической промышленности. Бескислородная медь, используемая для изготовления деталей радиотехнических и электронных приборов, должна отвечать следующим основным требованиям:
1) обладать высокой электропроводностью и химической чистотой;
3) содержать не более 0,001% кислорода и менее
1,5 мл/100 г металла других газов.
Таблица. СОСТАВ ЗАЩИТНОЙ АТМОСФЕРЫ ПРИ ПЛАВЛЕНИИ БЕСКИСЛОРОДНОЙ МЕДИ, %
Компоненты газа | При использовании технического азота | При использовании воздуха |
Азот | 98,5—99,5 | 65,0—75,0 |
Углекислый газ | 0,01—0,1 | 2,0—4,0 |
Окись углерода | 0,01—1,2 | 25,0—30,0 |
Кислород | 0,01—0,1 | 0,01—0,3 |
Водород | 0,01—1,0 | 0,01—2,0 |
Древесный уголь, применяемый при производстве бескислородной меди, прокаливают в вакууме в течение 3,5—4,0 ч при температуре 900—1000° С и загружают в печь горячим, непосредственно после прокалки. Толщина слоя угля в печи или миксере должна составлять не менее 250—300 мм.