Листопрокатное производство (справочник)
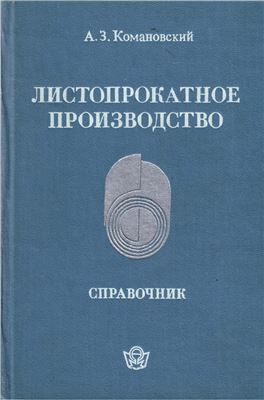
Комановский А.З.
Металлургия, 1979 г.
ТОЧНОСТЬ ПРОКАТКИ
Точность прокатки характеризуется продольной и поперечной разнотолщинностями полосы, а также выполнением допусков.
Продольная разнотолщинность вызывается колебаниями температуры по длине полосы при прокатке, рязнотолщинностью подката, изменением скорости прокатки и режима натяжения полосы между клетями непрерывной группы стана, биением опорных валков, вызванным их эксцентриситетом, химической и механической неоднородностью металла по длине полосы, тепловым расширением и износом валков. Продольная разнотолщинность не исправляется в процессе, холодной прокатки и неблагоприятно сказывается па качестве готового холоднокатаного листа.
Влияние изменения температуры при горячей прокатке па разнотолщинность полосы проявляется через изменение сопротивления металла деформации и усилия прокатки. Причем чем ниже температура, тем выше эти параметры и больше разнотолщинность полосы. Колебание температуры при горячей прокатке зависит от изменения температуры в нагревательной печи, определяемого изменением калорийности топлива, температуры дутья и давления в печи, от расстояния между печью и первой черновой клетью, от задержек слябов на рольганге и от времени нахождения слябов в печи, определяемого темпом прокатки.
Влияние разнотолщинности подката особенно ощущается на кромках полосы, что объясняется различной величиной боковых наплывов на слябах. Падение, температуры сляба в местах соприкосновения его е глиссажными трубами вызывает продольную разнотолщинность уже в первой клети черновой группы. В результате подкат, поступающий в непрерывную группу клетей, уже имеет колебания толщины полосы по длине.
Колебания толщины полосы при прокатке определяются изменением скорости деформации, причем с повышением скорости деформации сопротивление металла деформации возрастает.
На современных широкополосных станах горячей прокатки применяют одновременное, ускорение всех клетей непрерывной группы после, захвата переднего конца полосы моталкой или несколько ранее. В этом случае на изменение зазора между валками и, следовательно, на продольную разнотолщинность действуют следующие факторы: условия трения в очаге деформации, скорость деформации, изменение толщины масляной пленки в подшипниках жидкостного трения, изменение усилия прокатки и т. д.
Биение валков вызывает циклические изменения толщины полосы по длине. При этом с увеличением обжатия усилие прокатки возрастает, а зазор, вызванный пружиной клети, увеличивается тем больше, чем меньше жесткость клети. Фактическое изменение толщины полосы из-за биения валков составляет 0,05—0,06 мм (в отдельных случаях — 0,08- 0,10 мм) 1101].
На современных листовых станах с высокой жесткостью клетей при прокатке с ускорением биение валков является одной из основных причин колебания толщины полосы. Системы автоматического регулирования не успевают устранить разнотолщинность этого типа, поэтому необходима высокая точность подготовки и шлифовки валков, обеспечивающая отсутствие, биения.
С целью повышения производительности станов горячей и холодной прокатки в последние годы массу слябов повысили до 40 Мг (т). Крупные слитки, являющиеся исходными для получения слябов большой массы, отличаются значительной неоднородностью химического состава но сечению и высоте вследствие сегрегации элементов при затвердевании жидкой стали. Эта неоднородность сохраняется в слябах, особенно в головных, и распространяется на большую длину полосы. Для устранения химической неоднородности применяют химическое закупоривание стали.
Тепловое расширение и износ валков — медленно меняющиеся факторы, которые могут повлиять на продольную разнотолщинность в пределах партии металла, но не оказывают влияния на разнотолщинность по длине одной полосы.
Уменьшения продольной разнотолщинности достигают применением систем автоматического регулирования толщины полосы при прокатке с ускорением в чистовой группе и повышением жесткости клети. При прочих равных условиях наименьшая продольная разнотолщинность обеспечивается правильным распределением натяжений между клетями непрерывной группы.
Для устранения продольной разнотолщинности крайне важно повысить жесткость валков. Определяющим элементом в жесткости клети является валковая система, на долю которой приходится половина общей деформации. Из рис. 74 видно, что при увеличении диаметра бочки и шейки опорных валков, жесткость клети увеличивается. Оптимальным является положение, при котором диаметр шейки опорного валка составляет 0,8 диаметра его бочки. Увеличение диаметра рабочих валков также приводит к увеличению жесткости клети.
Поперечная разнотолщинность зависит от распределения вытяжки по ширине, которая в свою очередь обусловливается упругой деформацией валков
Поперечная разнотолщинность зависит от распределения вытяжки по ширине, которая в свою очередь обусловливается упругой деформацией валковой системы и характером распределения температуры по длине бочки валка.
При прокатке на непрерывных широкополосных станах па формирование поперечного профиля и формы полосы влияет профиль активных образующих рабочих валков, упругая деформация валков и другие факторы.
Размеры и форма прокапываемой полосы зависят в первую очередь от профиля валков. Если пренебречь упругими деформациями прокатываемой полосы и неравномерностью сжатия валков, можно утверждать, что профиль валка передается прокатываемой полосе.
В результате износа рабочих и опорных валков условия контакта между валками быстро изменяются, следовательно, меняются упругие деформации валков и влияние их на профиль полосы. Износ рабочих валков непосредственно скалывается на поперечном профиле полосы, износ рабочих и опорных валков в зоне межвалкового контакта влияет на профиль полосы через изменение деформации самих валков.
Уменьшить поперечную разнотолщинность можно повышением жесткости клетей и применением систем гидромеханического регулирования профиля полосы. Возможны дна способа повышения жесткости. Первый способ — увеличение диаметра опорных валков (до 1525 мм), сечений стоек станины, и применение подшипников жидкостного трения. При этом способе жесткость клети достигает 5—7 МН/мм (500—700 тс/мм).
Второй способ —создание четырехвалковых клетей новых конструкций и предварительное напряжение клетей. На некоторых станах находят применение бесстанинные клети, в которых подушки опорных валков стянуты регулирующими винтами, воспринимающими усилия прокатки. Этими же винтами устанавливают зазор между валками. Жесткость бесстанинной клети составляет около 6,4 Мн/мм (640 тс/мм), а масса оборудования примерно в два раза меньше, чем у обычной клети, предназначенной для прокатки листа того же сортамента. Недостаток такой клети — увеличение времени на перевалку по сравнению с обычными клетями.
Во ВНИИметмаше разработан способ напряжения обычной четырехвалковой клети путем установки между подушками опорных валков достаточно мощных гидроцилиндров. После задачи полосы в валки объем жидкости, находящейся в гидроцилиндрах, отключается от питающей системы, и клеть превращается в напряженную. Таким путем жесткость клети без увеличения ее массы можно повысить примерно на 30%.
Не менее эффективно предварительное напряжение клети с помощью установки клиновых устройств между подушками опорных валков, которые перемещаются гидроцилиндрами, вмонтированными в подушки опорных валков.
Существенного снижения поперечной разнотолщинности и получения высокой плоскостности листов достигают внедрением систем регулирования профиля валков методом противоизгиба. При этом между подушками рабочих и
При холодной прокатке, причины, вызывающие колебания толщины но длине, могут быть следующие: колебания толщины, связанные непосредственно с прокаткой (скорость, натяжение и т. д.); колебания толщины, вызываемые неточностью размеров исходного металла (колебания толщины, твердости, структуры по длине полосы подката и т. п.); колебания толщины, зависящие от состояния валков (профиль, температура, эксцентриситет, износ и т. п.).
На станах холодной прокатки ведут прокатку с переменной скоростью, что связано с необходимостью снижения скорости в начале и конце прокатки рулона и при прокатке сварных швов, причем при большой массе рулона снижение и повышение скорости происходит несколько раз па протяжении прокатки одного рулона. Такой режим прокатки связан с изменением толщины полосы, поскольку многочисленными исследованиями доказано, что при увеличении скорости прокатки толщина полосы уменьшается и наоборот. Это явление связано с коэффициентом трения при прокатке и толщиной масляной пленки в подшипниках жидкостного трения.
С повышением скорости прокатки коэффициент трения снижается, что влечет за собой уменьшение усилия прокатки, упругой деформации клети и зазора между валками и увеличение обжатия. Из рис. 76 видно, что натяжение полосы вначале растет, а во второй половине разгона стана резко падает.
Изменение толщины полосы происходит также вследствие уменьшения зазора между валками при всплывании шеек опорных валков в подшипниках жидкостного трения.
При прочих равных условиях наименьшую продольную разнотолщинность холоднокатаной полосы па участке заднего конца рулона и в районе сварного шва получают при увеличении скорости прокатки на этих участках, которое возможно при условии создания оптимального натяжения полосы перед валками с помощью мощных роликовых проводок.