Лабораторный практикум по металлографии и физическим свойствам металлов и сплавов
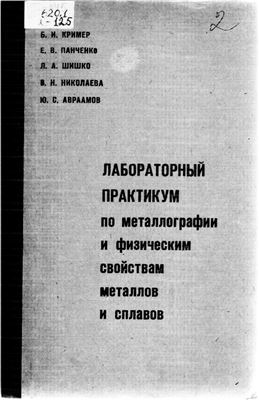
Кример Б.И., Панченко Е.В., Шишко Л.А. и др.
Металлургия, 1966 г.
Приготовление микрошлифа для изучения микроструктуры при помощи светового микроскопа
Цель работы
Освоить методику изготовления образцов различных металлов и сплавов для микроскопического исследования при помощи светового микроскопа.
Для выполнения работы необходимы: образцы углеродистой и нержавеющей сталей или меди, латуни, набор шлифовальной шкурки, полировальный станок, полировальную жидкость, установку для электролитической полировки и травления, металлографический микроскоп, установку для запрессовки и приспособления для других видов монтировки образцов.
Форма и размеры микрошлифов
Наиболее удобны простые формы образцов: цилиндр, куб, параллелепипед. Образцы изготавливают со скошенными углами на поверхности микрошлифа, чтобы при полировке не рвать сукно (фетр).
Наиболее удобны образцы диаметром 10—20 или стороной квадрата 10—20 мм при высоте 10—15 мм.
Иногда размеры образцов (микрошлифов) определяются формой и размерами изделия (проволока, тонкий лист и т. д.).
Отбор образца для микрошлифа
Образец берут из той части изделия или заготовки, которая представляет в данном исследовании наибольший интерес. Например, если нужно установить причину разрушения, образец берут в непосредственной близости к месту разрушения. От листового материала отбирают два образца; один вдоль, второй— поперек деформации. Для изучения микроструктуры изделий после химико-термической обработки образец отбирают таким образом, чтобы его поперечное сечение включало поверхностный слой.
Образцы вырезают ножовкой или на токарном, фрезерном, строгальном станках. От металлов и сплавов, обладающих высокой твердостью и плохой обрабатываемостью (закаленные стали, белые чугуны, стали аустеиитного класса и др.), образцы вырезают па тех же станках с применением режущего инструмента, наготовленного из твёрдых или сверхтвердых сплавов или при помощи тонкого наждачного круга, а также электроискровой резки. От хрупких металлов и сплавов образцы отбирают путем излома.
При механической резке должны быть приняты меры, предохраняющие образцы от разогрева, если это связано с изменением структуры.
Изготовление мнкрошлифа сводится к последовательному выполнению следующих операций: 1) выравнивание поверхности среза или излома грубой шлифовкой; 2) тонкая шлифовка; 3) полировка.
Грубая шлифовка. Грубую шлифовку проводят на абразивных кругах. Мягкие или очень хрупкие металлы и сплавы шлифуют напильником или грубой наждачной бумагой. При шлифовке на абразивных кругах следует применять во избежание нагрева интенсивное охлаждение. Шлифовку заканчивают после полного выравнивания всей поверхности среза (шлифа).
Тонкая шлифовка. Образец после грубой шлифовки очищают от частиц металла и абразива и подвергают шлифовке на шлифовальной бумаге различной зернистости на специальных шлифовальных станках или вручную. В табл. 4 приведена классификации абразивных порошков, основанная на разделении абразивов по величине зерна, и изготовленных из них шлифовальных бумаг.
Таблица 4
№ зернистости шлифовального порошка | Размер зерна мкм | № зернистости ннкропорошка | Размер абразивного зерна, мкм |
100 | 150—125 | Μ 28 | 28—20 |
120 | 125—105 | Μ 20 | 20—14 |
150 | 105-75 | Μ 14 | 14—10 |
180 | 85-63 | Μ 10 | 10—7 |
220 | 75—53 | Μ 7 | 7—5 |
280 | 53—28 | Μ 5 | 5-3,5 |
320 | 42—20 |
|
|
Шлифовку проводят на 4—5 номерах шлифовальной бумаги, которые выбирают в зависимости от наименования металла или состава сплава.
При шлифовке вручную шлифовальную бумагу помещают на стекло для создания ровной и твердой подкладки и образец перемещают на этой бумаге, слегка его прижимая. Шлифуют до тех пор, пока не исчезнут следы предыдущей обработки. Каждый раз при переходе на более тонкую шлифовальную бумагу образец очищают от наждачной пыли, поворачивают под углом 90° и шлифуют до тех пор, пока не исчезнут следы предыдущей обработки (риски от предыдущей наждачной бумаги). После тонкой шлифовки образец промывают струей воды для удаления частиц металла и абразива и подвергают полировке.
Механическая полировка. Полировку производят на специальном полировальном станке, диск которого обтянут фетром, сукном или бархатом . Диск станка смачивают полировальной жидкостью, состоящей из воды, в которой во взвешенном состоянии находятся частицы полировального порошка (твердые частицы): окиси алюминия, или окиси хрома, или окиси железа, или других соединений.
Образец не следует сильно прижимать к диску. Полировка продолжается 5—10 мин, иногда и несколько больше и определяется состоянием поверхности до полировки, свойствами металла или сплава, полирующей жидкостью и др.
Полировку заканчивают после того, как микрошлиф приобретает зеркальную поверхность. Правильным критерием высокого качества поверхности микрошлифа является отсутствие на ней дефектов в виде рисок.
После полировки микрошлиф промывают водой, высушивают теплым воздухом или фильтровальной бумагой и рассматривают под микроскопом при увеличении в 100—125 раз.
При полировании сплавов с относительно большой разницей в твердости фаз или структурных составляющих последние хорошо выявляются после полирования и не требуют дополнительного травления. Этот способ применим для белого чугуна, заэвтектондных сталей и др. и основан на том, что мягкие составляющие сплава истираются при шлифовке и полировке быстрее, чем твердые. Этот способ полировки называется полировка в рельеф.
Абразивная (механическая) полировка, описанная выше, в ряде случаев не дает удовлетворительных результатов (очень мягкие металлы и сплавы, аустенитные стали и некоторые другие сплавы). Абразивная полировка также неприменима, когда по роду исследования нельзя допускать упрочнения (наклепа) поверхностных слоев металла. В указанных случаях абразивную полировку заменяют электролитической.
Электролитическая полировка совершается в результате электрохимического растворения металла на полируемой поверхности
Химическая полировка. Некоторые металлы и полупроводники высокой чистоты и высокой хрупкости, такие как кремний и германий, подвергают химической полировке.
Предварительно поверхность микрошлифа подвергают шлифовке мелким порошком карбида бора на стеклянных пластинах или на чугунном круге, установленном на валу полировального станка. Отшлифованный образец кремния помещают полностью в смесь, состоящую из 1 ч. HF и 2 ч. HNO3 (60%). Продолжительность полировки 2—3 мин. При полировке образец все время перемешают в смеси. Смесь должна находиться в чашечке из фторопласта, щипцы, в которых держат образец, должны иметь фторопластовые наконечники.
После полировки образец необходимо как можно быстрее перенести в воду во избежание окисления на воздухе.
Полировальную смесь нагревают до появления белого дыма, и в этот момент погружают образец. Продолжительность полировки 10—15 сек (отсчет времени от момента появления бурых паров).
Посуда и щипцы должны быть такими же, как и при химической полировке кремния. Полировальная смесь должна быть свежая, но выстоявшая в течение 0,5 ч с момента смешения.
После полировки образец немедленно промывают в холодной воде.
В одной порции раствора можно полировать не более двух образцов.
Монтировка мелких образцов для изготовления микрошлифов
Мелкие образцы неудобной формы (от тонких листов, проволоки, кромки режущего инструмента и т. п.) должны быть заключены в специальные приспособления.
Для лучшего сохранения краев образцов при шлифовке рекомендуется применять прокладки между образцами и стенками зажима.
Для изготовления шлифа из образцов тонкого листового материала можно их склеить клеем БФ-2.
Очень распространен способ заливки мелких образцов. На гладкую металлическую поверхность устанавливают отрезок трубки диаметром 10—20 мм и высотой 10—20 мм. Внутри ее размещают образцы и свободное пространство заполняют жидким легкоплавким сплавом или серой. После охлаждения эта оправка вместе с образцами шлифуется и полируется для изготовления микрошлифа.
В табл. 6 приведены химический состав и температура плавления некоторых легкоплавких сплавов.
Таблица 6
Химический состав, Η (по массе.)
Рb | Sn | Вi | Cd | Температура плавления °С |
25,0 | 12,5 | 12,5 | 50,0 | 60,5 |
26,5 | 13,5 | 50,0 | 10,0 | 70,0 |
40,0 | — | 52,0 | S.0 | 91,5 |
— | 26,0 | 53,0 | 21,0 | 103,0 |
44,0 | — | 56,0 | — | 125,0 |
Введением в эти легкоплавкие сплавы некоторого количества ртути можно еще больше снизить температуру плавления.
Применяют запрессовку образцов в пластмассы (полистирол, бакелит и др.).
Запрессовку полистиролом производят следующим образом:
Образец вынимают из пресс-формы, шлифуют и полируют.
Недостаток запрессовки состоит в том, что в нагретых до 120—130°С образцах в некоторых случаях заметно изменяется микроструктура. Сказанное относится и к заливке образцов легкоплавкими сплавами с относительно высокой температурой плавления.