Кульков С.Н., Гнюсов С.Ф. Карбидостали на основе карбидов титана и вольфрама
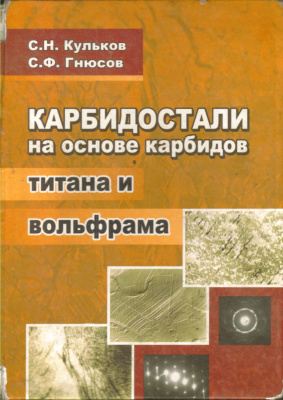
Кульков С.Н., Гнюсов С.Ф. Карбидостали на основе карбидов титана и вольфрама
Томск, 2006 г.
ФАЗОВЫЙ СОСТАВ И СТРУКТУРА КАРБИДОСТАЛЕЙ, ФОРМИРУЮЩАЯСЯ ПРИ ИХ ПОЛУЧЕНИИ И ТЕРМИЧЕСКОЙ ОБРАБОТКЕ
1.1. Методы получения карбидосталей
Карбидосталями называют MaTqjnanbi, состоящие из сталей и карбидов с массовой долей от 20 до 70%. В качестве карбидов чаще всего применяют карбид титана и вольфрама. По свойствам и назначению они занимают промежуточное положение между быстрорежущими сталями и твердыми сплавами. Карбидостали сочетают свойства обеих составляющих: тугоплавкой твердой основы и стальной матрицы. Тугоплавкая составляющая обеспечивает сплаву твердость, прочность и износостойкость, а сталь - вязкость и пластичность.
В качестве цементирующей связки используют стали различных классов: аустенитные, нержавеющие, мартенситные, стали карбидного класса, быстрорежущие стали и т.д. - в зависимости от требуемых свойств получаемого материала.
Карбидостали получают обычными методами порошковой металлургии [I - 4]: прессованием смеси порошков исходных материалов в брикеты и последующим спеканием полученных прессовок, пропиткой пористого спеченного карбидного каркаса стальным расплавом, горячим прессованием смеси исходных порошков и горячей экструзией спеченных композиционных материалов.
Первые два способа нашли наибольшее распространение, поскольку они относятся к широко применяемым методам порошковой металлургии [I, 2]. Технология получения карбидосталей этими способами включает в себя те же операции, что и изготовление твердых сплавов [5 - 8]: размол и смешивание исходных компонентов; замешивание их с клеящим веществом; формование прессовок с применением различных методов, обусловленных геометрическими размерами будущих деталей;
предварительное спекание с целью удаления из заготовок каучука (парафина) и придания заготовкам необходимой прочности; окончательное спекание. На заключительном этапе получения осуществляется контроль качества спеченных сплавов.
Смешивание обычно совмещается с размолом смесей. Продолжительность смешивания в мельнице, футерованной твердосплавными пластинами, с применением твердосплавных шаров составляет от 2 до 4 суток [3, 9]. При этом выяснено, что пористость сплавов после спекания закономерно уменьшается с увеличением длительности помола. Размолом карбидов в шаровых мельницах добиваются необходимой дисперсности карбидной и металлической компонентов, распределения их по размерам, минимального загрязнения смеси примесями, минимального окисления кислородом воздуха и компонентами среды размола. Для реализации этих условий в каждом конкретном случае экспериментально подбирают размольную жидкость, длительность размола, соотношение размольных тел и размалываемой смеси. В качестве размольной жидкости используют безводный этиловый спирт, бензин, ацетон, циклогексан [10]. Из экспериментальных данных известно, что отношение «шары : смесь» составляет 5 :2 иногда 5 : I [11]
Использование атгрипторов в качестве размольных агрегатов позволяет снизить продолжительность смешивания с 48 до 3 - 4 часов и измельчить порошки до ультродисперсного состояния за счет соударения мелких шариков между собой и стенками рабочей камеры при вертикальном вращении мешалки [12]. Частота вращения мешалки не превышает 500 об/мин, что обеспечивает незначительный износ стенок рабочей камеры и шариков. Сушку измельченной смеси проводят на воздухе при температуре 320 340 К.
Режимы прессования полученной смеси порошков подбирают экспериментально. Они определяются скоростью нагружения, конечным давлением, временем выдержки и скоростью снятия нагрузки. Свойства прессовок зависят от рода пластификатора, вводимого в шихту. Пластификаторами обычно служат раствор синтетического каучука в бензине, парафин, полиэтилен, глицерин. Количество пластификатора, вводимого в шихту, обычно определяется сложностью формы детали и составляет I - 2 вес.% [2,3, 6].
Самой важной стадией изготовления изделий из карбидосталей является спекание, так как эксплуатационные свойства карбидостали в основном определяются пористостью, зернистостью карбидной фазы,
равномерностью распределения металлических компонентов в спеченных заготовках.
В зависимости от требуемого качества и вида карбидосталей спекание проводят в вакууме, водороде, аргоне или гелии при температуре 1620 -5-1750 К с выдержкой при заданной температуре 0,5 * 2,5 часа.
Большинство работ по изучению процессов спекания системы металл - карбид металла в присутствии жидкой фазы связывают обычно с представлениями о смачиваемости карбидов металлами, выбранными в качестве цементирующих связок [13, 14]. Такой подход к изучению спекания объясняется тем, что выбранные компоненты должны обладать способностью к физико-химическому взаимодействию, обеспечивающему получение сплавов с заданными свойствами. При детальном исследовании смачиваемости карбидов металлов IV, V, VII групп различными переходными и непереходными металлами было установлено, что ни один переходный металл и тем более непереходный не образуют с карбидом титана краевого угла смачивания, равного нулю ни в атмосфере водорода и аргона, ни в вакууме [15, 16]. Наименьшие краевые углы смачивания карбид титана образует с расплавами кобальта, марганца и никеля, для которых он составляет б, 15 и 25° соответственно. При контактировании карбида титана с расплавленным железом краевой угол смачивания составляет 125°. Анализ результатов исследования [8] смачивания карбида титана сталями и сплавами на основе железа показал, что он хорошо смачивается всеми исследуемыми сталями в температурном интервале жидкофазного спекания карбидосталей (табл. 1.1). Установлено, что повышение содержания углерода и серы в стальной матрице улучшает смачиваемость, и особенно для стали Xl2М.
Таблица I . I
Смачиваемость карбида титана сталями при различных емпературах [8]
Марка стали | Температура, К | Θ,град | Марка стали | Температура, К | ©,град |
Х12М | 1670 | 45 | Х18Н15 | 1770 | 35 |
| 1720 | 30 | - | 1870 | 7 |
| 1770 | 7 | - | - | - |
Х4Н2М | 1670 | 60 | Р18 | 1670 | 50 |
| 1770 | 35 | - | 1690 | 20 |
| 1870 | 0 | - | 1700 | 0 |
Х13М2 | 1720 | 40 | Р9К5 | 1670 | 42 |
| 1770 | 25 | - | 1710 | 26 |
| 1870 | 20 | - | 1720 | 0 |
Спекание - термически активируемый, самопроизвольный или инициируемый внешним воздействием переход системы контактирующих частиц твердых тел или пористой среды в термодинамически равновесное состояние путем уменьшения площади свободной поверхности [17]. Термодинамическим условием жидкофазного, так же как и твердофазного, спекания многокомпонентных систем является стремление системы к равновесию. Однако, в отличие от твердофазного, при жидкофазном спекании благодаря большей подвижности атомов нагляднее проявляется действие основных движущих сил объемного уплотнения — сил капиллярного стягивания, активнее протекают процессы перекристаллизации элементов структуры и уплотнения. Благодаря увеличению скорости переноса компонентов в расплаве интенсивнее протекают процессы гетеродиффузии, растворения и осаждения, что приводит к ускорению сплавообразования, объемного уплотнения перекристаллизацией через жидкую фазу, а также к более заметному проявлению тормозящих усадку эффектов диффузионного роста [8,18].
В настоящее время общепринятой является точка зрения, что усадка при жидкофазном спекании обусловлена тремя основными процессами [3, 19,20].
1. Процесс перегруппировки. Наличие жидкости не только обуславливает возникновение капиллярного давления, способствуя перемещению частиц, но и значительно облегчает это перемещение, так как жидкость, затекая в пространство между частицами, выполняет роль смазки, резко уменьшая трение и заклинивание частиц. Величина объемной усадки, осуществляемой перегруппировкой частиц, увеличивается с увеличением количества жидкой фазы и уменьшением размера частиц тугоплавкой фазы, поскольку при этом уменьшается вероятность заклинивания частиц при их взаимоперемещении. Авторы работы [18] считают, что полное уплотнение в результате только одного процесса перегруппировки может быть получено при содержании жидкой фазы порядка 50 об.%.
2. Растворение - осаждение. Сжимающие усилия на контактах частиц приводят к большей растворимости вещества твердой фазы на этих участках и переносу материала от места контакта на свободную поверхность, вследствие чего частицы сближаются и образец уплотняется. В жидкости в первую очередь растворяются наиболее мелкие зерна вследствие их повышенной поверхностной энергии, и образующийся раствор оказывается пересыщенным по отношению к крупным зернам с
меньшей поверхностной энергией, на которых происходит приводящая к росту этих зерен кристаллизация из жидкости [21 - 23]. Рост зерен продолжается до тех пор, пока не исчезнут мелкие зерна и структура сплава не станет относительно однородной.
3. Образование жесткого скелета. Рост крупных зерен за счет мелких в ходе растворения-осаждения может приводить к срастанию частиц с образованием жесткого скелета, тормозящего усадку и препятствующего быстрому зарастанию пор. Аналогичная ситуация возникает при недостаточной смачиваемости частиц твердой фазы жидкостью, последняя не проникает на стыки между частицами, реализуется «сухой» контакт. Таким образом, оба предыдущих механизма либо отсутствуют вовсе, либо сильно заторможены - усадка мала или вовсе отсутствует. Образование жесткого скелета обычно происходит в тех случаях, когда материал твердых частиц хорошо спекается твердофазно при температуре ниже температуры плавления легкоплавкого компонента, тогда между частицами возникает схватывание. На этой стадии спекания уплотнение идет очень медленно: твердые частицы срастаются, жидкость уже не может затекать в межчастичные промежутки, и усадка связана только с процессами, имеющими место при твердофазном спекании.
В зависимости от природы спекаемых компонентов, количества образующейся жидкости, размера твердых частиц и начальной пористости порошковой формовки какая-либо из стадий жидкофазного спекания становится преобладающей. Сами стадии в процессе спекания непрерывно переходят одна в другую [19,24].
При жидкофазном спекании с взаимодействующими компонентами эффективное уплотнение достигается при меньших количествах жидкой фазы благодаря дополнительной усадке по механизму химической перегруппировки, которая обеспечивает возможность объемного дополнительного уплотнения с помощью диспергирования крупных тугоплавких частиц при зернограничном проникновении расплава, аккомодации их формы, коалесценции тугоплавких частиц по механизму растворение-осаждение.
Форма зерен изменяется в зависимости от количества жидкой фазы при спекании. Это объясняется тем, что при малом содержании жидкой фазы растворение и осаждение зерен карбида будет локализовано в малых областях между зернами. При этом будет быстро достигать насыщение жидкости атомами, входящими в состав карбидов, т.е. зерна в значительной степени будут сохранять свою первоначальную форму.
При достаточном количестве жидкой фазы карбидные зерна свободно перемещаются в жидкости, частично растворяются, и растворенное вещество затем осаждается на гранях больших зерен с малой поверхностной энергией, что обуславливает изменение их формы [5,25,26].
Таким образом, в процессе жидкофазного спекания происходит уплотнение карбидостали, изменение формы и размера карбидных зерен, а перераспределение и массоперенос карбидной фазы осуществляется по следующим механизмам: миграция расплава и перегруппировка карбидных зерен, диффузионный рост карбидных зерен вследствие их растворения и последующего осаждения, коалесценции частиц карбидов, «плавающих» в жидкости.
В результате взаимодействия компонентов смеси, а также системы со средой спекания может происходить изменение класса сталей, используемых в качестве связки. В работе [8,27] после спекания карбидостали карбид титана - сталь Р18 в вакууме проводили анализ стальной связки и карбида титана. Данные исследования показали, что с увеличением содержания карбида титана исчезал основной карбид быстрорежущих сталей MjC3 изменялась легированность твердого раствора на основе α-Fe вследствие растворения вольфрама, хрома и ванадия в карбиде титана, увеличивалось растворение титана в α-Fe. С увеличением содержания стальной связки уменьшался параметр решетки карбида титана, что свидетельствует об изменении его состава [8]. Химическим анализом подтверждено, что на растворимость в стальной высоколегированной связке оказывает существенное влияние содержание в карбиде титана связанного углерода. Чем ниже его содержание в карбиде, тем он менее устойчив, тем выше его растворимость в стальной связке. Растворимость титана в стальной связке способствует обезуглероживанию металлической фазы в процессе спекания и стабилизации а-феррита [8]. Сталь переходит из мартенситного в ферритный класс.
Карбидостали, полуденные методом пропитки карбидного каркаса стальным расплавом, как правило, обладают более высокой плотностью и ударной вязкостью, чем полученные обычным методом прессования и спекания [5, 28 - 30]. Это достигается за счет получения структуры с изолированными мелкими включениями карбидной фазы в стальной матрице. Кроме того, дополнительным технологическим преимуществом процесса получения карбидосталей методом пропитки является использование небольших давлений для уплотнения порошков, что дает возможность изготовления изделий сложной формы.