Конструкция и расчет машин и агрегатов металлургических заводов
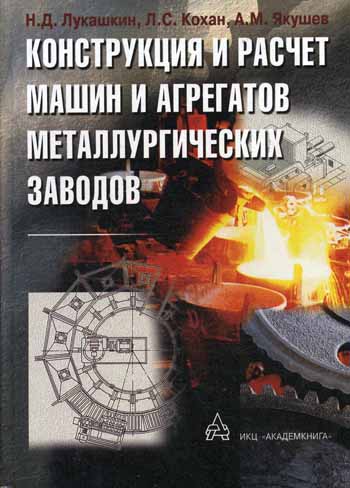
Лукашкин Н.Д., Кохан Л.С., Якушев А.М.
Академкнига, 2003 г.
2.5. Конструкция и расчет топливных печей цветной металлургии с жидкой ванной и их механизмов
В цветной металлургии широко используют топливные печи с жидкой ванной, в которых протекают разнообразные процессы: расплавление металла, расплавление рудной шихты с получением штейна, восстановление составляющих шихты с расплавлением продуктов плавки, расплавление чернового металла с его последующим рафинированием или заливка в отапливаемую печь жидкого металла с его последующим рафинированием и др.
2.5.1. Конструкции плавильных печей и их механизмов
Конструкции шахтных печей
Шахтные печи применяют на медеплавильных заводах для плавки кусковых сульфидных руд; на никелевых заводах — для плавки агломерата, брикетов и кусковых окисленных никелевых руд, а также кусковых сульфидных медно-никелевых руд; на свинцовых заводах — для плавки агломерата и переплава бедного штейна и шликеров; на оловянных заводах — для плавки шлаков и других оборотных материалов.
В шахтную печь загружают крупнокусковые материалы. Куски агломерата должны иметь размеры 50-150, кокса — 50-100, других видов шихты — 15-100 мм. Жесткие требования к крупности материала обусловлены особенностями шахтной плавки.
Наличие в шихте между крупными кусками мелких кусков или пыли затрудняет прохождение газов снизу через шихту (ее газопроницаемость), что существенно снижает производительность печей.
В качестве топлива и восстановителя в шахтных печах используют кокс, загружаемый в строгой последовательности с порциями шихты. Расход кокса зависит от состава шихты. Для его снижения и интенсификации процесса плавки необходим подогрев дутья и обогащение его кислородом до 28-30%.
Шахтные печи имеют в основном одинаковое устройство и принцип действия, и отличаются друг от друга лишь конструктивным исполнением отдельных узлов, что объясняется спецификой технологических процессов. Современные печи имеют прямоугольное сечение, но применяют и круглые печи, диаметр которых составляет 1,5-1,6 м. Размер длинной стороны сечения прямоугольных печей зависит от заданной производительности. В печах для плавки свинца этот размер составляет не более 10 м, а для печей на медно-никелевых заводах достигает 26,5 м, что позволяет переплавлять до 2500т шихты в сутки.
На рис. 2.81 показана принципиальная схема шахтной печи. Основными ее элементами являются: горн 1, фурмы 2, шахта 4, колошник 7 и газоход 8. Шихту загружают через окна .9, расположенные с двух сторон на колошнике по длинным боковым сторонам печи. В некоторых печах, имеющих открытый колошник шихту загружают сверху; в печах с закрытым колошником шихту загружают сверху через двухконусные аппараты, препятствующие поступлению атмосферного воздуха в печь).
Для защиты стенок 5 от повреждения шихтой загрузочные окна оборудованы отбойными плитами 6. Снизу в разогретую шихту вдувают через фурмы 2 воздух, обогащенный кислородом. Воздух к фурмам подается от коллектора 3. В результате сгорания топлива и серы, содержащейся в шихте, в нижней зоне шахты создается температура 1450-1500° С. Здесь шихтовые материалы расплавляются и жидкая фаза (продукты плавки) стекает вниз в горн. Горячие газы поднимаются вверх и подогревают опускающуюся навстречу им шихту. Температура уходящих в газоход 8 газов составляет 150-300° С.
В печах для выплавки медного штейна расплав (штейн и шлак) из печи выпускают непрерывно по водоохлаждаемому желобу, и они поступают в наружный горн для разделения. Штейн, как более тяжелый, оседает и периодически сливается через шпуровые отверстия, а шлак всплывает наверх и непрерывно сливается в ковш. Шпуровые отверстия забивают глиняными пробками с помощью пневматических пушек.
В печах для плавки никелевой шихты продукты плавки также перетекают из внутреннего горна в отстойный (наружный) горн, где штейн отделяется от шлака. Шлак выпускают из отстойника непрерывно через летку, а штейн — периодически через шпуровое отверстие. Выпуск продуктов плавки из печей для плавки свинца описан ниже.
Конструкции отражательных печей
Отражательные печи применяют для переплава рудного сырья, а также для рафинировочных процессов. Термин «отражательные» они получили потому, что при горении топлива свод нагревается до высокой температуры и переизлучает (отражает) тепло, полученное им от газов, что способствует плавлению шихты. В качестве плавильных агрегатов отражательные печи широко используют при производстве меди, в качестве рафинировочных агрегатов их применяют при огневом рафинировании меди, никеля и свинца.
Отражательная плавильная печь состоит из фундамента, подины, стен, свода, Металлического каркаса, устройств для загрузки шихты и выпуска продуктов плавки, топливосжигающих устройств и газохода (рис. 2.83). Ванны современных крупных печей имеют ширину 7-11,5 м, длину 30-40 м и глубину 0,8-1,2 м. Высота пространства над ванной достигает 2,85 м. Общая масса печи может превышать 3000 т, а масса расплава при глубине ванны 1 м составляет 1000-1200 т.
Печи устанавливают на железобетонном фундаменте, в котором предусмотрены вентиляционные каналы для охлаждения пода.
На фундаменте размещена лещадь (под печи). Под современных печей выкладывают из кирпичей в форме обратной арки, ранее для этого использовали динасовый кирпич, а на новых печах хромомагнезитовый. Толщина пода составляет 0,6-1,5 м.
Стены выкладывают из хромомагнезитового или магнезитового кирпича; толщина стен у лещади равна 0,75-1,0 м, а вверху 0,5-0,6 м.
Стойкость стен повышают закладкой в футеровку водоохлаждаемых кессонов. Печи снаружи укрепляют металлическим каркасом. Вертикальные стойки-колонны каркаса сваривают из швеллеров или двутавров и связывают их горизонтальными ригелями. Противоположные стойки соединяют стяжками с пружинами, которые компенсируют термическое расширение футеровки.
Свод малых печей (шириной 6-7 м) делают арочным из динасового кирпича. У больших печей своды хромомагнезитовые. Они могут быть арочными распорно-подвесными или подвесными; последние делают плоскими либо трапециевидными. На рис. 2.83 показана печь с арочным распорно-подвесным сводом.
Подвесной свод состоит из отдельных блоков, которые подвешивают на стальных подвесках к ригелям, расположенным над сводом поперек печи. Распорно-подвесной свод также собран из отдельных блоков, подвешенных на арочные опоры. Он выложен в виде арки и поэтому частично опирается на подпятовые балки, уложенные вдоль боковых стен и приваренные к каркасу.
В качестве топлива применяют каменноугольную пыль, мазут, природный газ или смесь газа с мазутом. Для сжигания топлива служат горелки, установленные в передней торцевой стене печи. Температура газов в головной части печи 1500-1600°С, а в конце печи 1250-1300° С
Продукты плавки (штейн и шлак) скапливаются в ванне по всей ее площади. Штейн (соединения меди с серой, железом, цинком, никелем) и шлак выпускают из печи с двух уровней: первый — со дна ванны, второй — с верхней ее отметки. Шлаковые окна, размещаются в задней торцевой стенке или в боковой стенке вблизи газохода на высоте 800-1200 мм от лещади. Штейн выпускают через сифонные устройства или через шпуры периодического действия, расположенные в одной из боковых стен печи.
Шпуровые отверстия кессонированы медными литыми плитами с залитыми в них трубами для охладителя. Для вскрытия и забивки отверстий применяют специальные машины (пневматические пушки и прожиговые устройства).