Конструкционные стали. Справочник
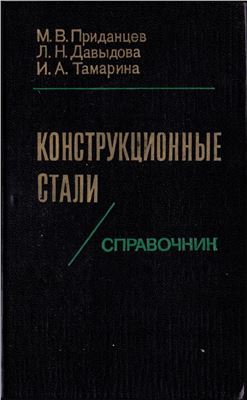
Приданцев М.В., Давыдова Л.Н., Тамарина И.А.
Металлургия , 1980 г.
НЕКОТОРЫЕ ОБЩИЕ ДАННЫЕ О СТАЛЯХ
Учет некоторых общих сведений о специфических свойствах рассматриваемых сталей необходим для того, чтобы наиболее правильно использовать их при производстве стали на металлургических предприятиях, при предъявлении требований во время заказа потребителями и использовании проката на машиностроительных заводах.
Помимо конкретных свойств, приведенных ниже по каждой марке стали, необходимо объяснить сущность некоторых пунктов примечаний, указанных в ГОСТ 4543—71. В примечании 2 (с. 2) записано: «По требованию потребителя сталь, обработанная в ковше синтетическими шлаками, поставляется с определением и гарантией обрабатываемости».
При обработке жидкой стали в ковше синтетическим шлаком резко снижается содержание серы и количество неметаллических включений в готовой стали, что благоприятно сказывается на значении ударной вязкости, выносливости и других свойствах, но при этом ухудшается ее обрабатываемость на металлорежущих станках. По этой причине и записан этот пункт в стандарте, поскольку нижний предел по содержанию серы в сталях не ограничивается.
При выборе и заказе стали потребители должны исходить из того, что им требуется: более высокое качество стали по комплексу механических свойств или при требованиях стандарта по механическим свойствам —лучшая обрабатываемость на металлорежущих станках.
В примечании 4 (ГОСТ 4543—71) к таблице химсостава сталей (с. 10) записано: «для сталей 20ХГР, 20ХНР, 20ХГНР, 27ХГР и 18Х2Н4МА допускается технологическая добавка титана по расчету (без учета угара) до 0,06%».
Причины и смысл этого замечания для сталей, содержащих бор, и хромоникельмолибденовой стали различные и сводятся к следующему.
Стали, содержащие бор
Основной особенностью конструкционной стали с микродобавкой бора является повышенная прокаливаемость ее по сравнению с аналогичной сталью без бора.
Бор относится к элементам внедрения и имеет очень малую растворимость в твердом растворе, не более 0,003% (по массе). Поэтому фактическое содержание бора в конструкционной легированной стали обычно не превышает 0,002—0,003%, так как при более высоком его содержании образуется боридная эвтектика, приводящая к снижению горячей пластичности и вязкости стали при нормальной и пониженных температурах. Увеличение прокаливаемосги стали достигается только находящимся в твердом растворе бором, а избыток его выше предела растворимости в виде боридов эвтектики прокаливаемости не увеличивает.
В зависимости от метода раскисления и порядка введения бора при выплавке стали влияние бора на прокаливаемость может быть либо эффективным, либо неэффективным,
Бор обладает сродством к азоту и образует нитриды в жидкой фазе; в этом случае он не входит в твердый раствор и не увеличивает прокаливаемости стали при закалке. Неэффективное влияние бора на прокаливаемость стали наблюдается в том случае, когда микролегирование бором осуществляется присадкой ферробора в хорошо раскисленйую алюминием сталь. При этом растворенный в жидком металле азот образует с бором нитриды. Свободный же металлический алюминий может образовывать нитриды только в твердом растворе при температурах ниже 1200—1250° С.
Для обеспечения эффективного влияния бора на прокаливаемость стали необходимо перед присадкой ферробора в раскисленную алюминием сталь добавить титан, который обладает большим сродством к азоту, чем бор, и также образует нитриды в жидкой фазе.
Обычно при выплавке стали с микродобавкой бора вводят указанной последовательности титана в 4—5 раз больше (в виде ферротитана), чем содержание азота в стали, учитывая отношение атомных весов титана и азота, а также степень усвоения титана.
При введении в сталь бора не в виде ферробора, а в виде комплексного ферросплава, содержащего, кроме бора, титан или цирконий, последний присаживается также после раскисления стали алюминием. Указанные особенности выплавки учитываются при производстве борсодержащих конструкционных легированных сталей.
Микродобавка титана для связывания азота до окончания кристаллизации стали не только обеспечивает эффективное влияние микродобавки бора на прокаливаемость стали, но и препятствует образованию таких дефектов, как сколы в изломе крупного сорта и камневидного излома при последующих переделах — ковке, штамповке и термической обработке.
Хромоникельмолибденовая сталь 18Х2Н4МА
Добавка указанного количества титана в стали 18Х2Н4МА, Ι8Χ2Η4ΒΑ и в другие аналогичные стали при их выплавке, как правило, совершенно необходима и предназначена для устранения межкристаллитных трещин в слитке, выявляемых на макротемплетах, и блестящих ровных участков поверхностей дендритов, выявляемых в изломе литого металла.
Указанный дефект, давно обнаруженный в слитках такой стали, связанный с повышенным содержанием азота, вызывал при горячей механической обработке слитков грубые рванины, был устранен присадкой титана в хорошо раскисленный алюминием жидкий металл. В том случае, когда титан связывал основное количество азота в нитриды титана до затвердевания слитка, образования указанного дефекта не наблюдалось.
Этот дефект можно наблюдать не только в слитках сталей 18Х2Н4МА и 18Х2Н4ВА, но и в ряде других аналогичных сталей при выплавке в дуговых электропечах (когда имеет место более высокое поглощение азота жидким металлом) в случае, если азот не связывать титаном.
Межкристаллитные трещины и грубые рванины при горячей обработке слитков давлением наблюдаются главным образом при нагреве перед обработкой холодных слитков. При горячем посаде отлитых слитков, как правило, они деформируются без образования трещин. Указанный дефект наблюдается в хорошо раскисленных алюминием сталях, но отсутствует при присадке в раскисленный жидкий металл титана.
Это указывает на то, что повышенное содержание азота является первопричиной образования дефекта в конце кристаллизации слитка, поскольку избыточный алюминий образует нитриды в твердой фазе, которые, выделяясь при температурах ниже 1200—1250° С, способствуют дальнейшему развитию трещин по границам дендритов уже при сравнительно низких температурах в результате напряжений (термических, при фазовых превращениях). Титан образует нитриды в жидкой стали и полностью или в большей части связывает азот, устраняя таким образом первопричину образования данного дефекта, приводящего к браку металла на металлургических предприятиях.
Межкристаллитные трещины и рванины наблюдаются и в стальном литье из хромоникельмолибденовых сталей. Добавка титана и в этом случае устраняет эти дефекты. Добавка титана для связывания азота в хромоникельмолибденовые стали, кроме того, делает их нечувствительными к образованию трудноисправимого камневидного излома, причиной которого являются нитриды алюминия, а также устраняет такой дефект, как сколы.
Камневидный излом в сталях без добавки титана может быть исправлен только высокотемпературным нагревом для растворения дисперсных нитридов алюминия, выделившихся по границам крупного зерна аустенита при горячей обработке (ковке, штамповке), и последующим быстрым охлаждением для предотвращения обратного выделения нитридов алюминия из аустенита. Температура нагрева для растворения нитридов алюминия должна быть не ниже 1250° С. После такой обработки последующей нормализацией и затем обычной закалкой исправляют перегрев. Такая сложная обработка для устранения камневидного излома менее целесообразна с точки зрения производительности, чем применение стали с технологической добавкой титана.
Предупреждение образования флокенов
Все приведенные в справочнике конструкционные легированные стали имеют меньшую или большую флокеночувствительность после, горячей обработки давлением. В литом состоянии все стали обычно не имеют флокенов, поскольку в этом случае имеется достаточно большое количество усадочных пор — резервуаров, в которые может выделяться водород з молекулярном состоянии при превращении аустенита и не создавать таких больших давлений в них, которые могли бы способствовать образованию флокенов при определенных температуре и времени.
Деформированный металл имеет большую плотность, и поэтому в нем развиваются при определенных условиях флокены, причем флокены развиваются при температурах ниже 100—150° С не сразу, а по истечении определенного времени в зависимости от химического состава стали и образующейся структуры при превращении аустенита, т. е. существует так называемый инкубационный период для их образования. Дальнейшее их развитие, т. е. увеличение размеров флокенов, происходит во времени.
Из приведенных в справочнике сталей наименее чувствительными к образованию флокенов, если не принимать меры, исключающие их образование, являются менее легированные стали, содержащие небольшое количество углерода и имеющие меньшую устойчивость аустенита при охлаждении в области перлитного превращения (например, 15Н2М, 20Н2М, 20ХН, 12ХН2 и др.).
Наибольшей флокеночувствительностью обладают более легированные стали, с более высоким содержанием углерода, у которых при охлаждении после горячей обработки на воздухе образуется мартенситная или бейнито-мартенситная структура (например, 40Х2Н2МА, 18Х2Н4М(В)А, 25Х2Н4М(В)А, 38ХНЗМФА, 45ХН2МФА и др.).
Флокеночувствительность всех сталей зависит от сечения заготовок, готовых поковок и метода выплавки стали (т. е. от содержания в ней водорода). У блюмов более крупных сечений, заготовок, готовых поковок, полученных при первом переделе слитков сталей, флокеночувствительность больше. Флокеночувствительность сталей, выплавленных в кислых печах (мартеновской, электродуговой), электрошлаковых (двойной переплав), и тем более вакуумированной стали значительно меньше. Ν
С учетом вышеприведенных положений о флокеночувствительности сталей в справочнике для каждой стали указаны в общих чертах необходимые условия охлаждения или термическая обработка после горячей обработки давлением с целью предупреждения образования флокенов.
Конкретные режимы медленного охлаждения разных сталей в зависимости от устойчивости аустенита (от термокинетических диаграмм превращения его) могут быть различными как по скорости охлаждения, так и по конечной температуре охлаждения. Для сталей с меньшей устойчивостью аустенита, когда при определенной скорости охлаждения имеет место полное феррито-перлитное превращение, конечная температура замедленного охлаждения может быть более высокой, чем у сталей с устойчивым аустенитом, для которых удаление водорода до неопасной концентрации в стали проходит при более низких температурах из твердого раствора α в течение определенного времени.
Для крупных блюмов, заготовок и поковок сталей с устойчивым аустенитом обычного медленного охлаждения оказывается недостаточно, и в этом случае применяют специальную противофлокенную термическую обработку. После горячей обработки давлением блюмы, заготовки можно охлаждать на воздухе в штабелях до температуры 200—150° С и затем подвергать их не позже чем через четыре часа высокому отпуску для удаления водорода и предупреждения образования флокенов. Аналогично можно охлаждать и крупные поковки на воздухе или загружать их в холодную печь для накопления и охлаждения до этой температуры и затем проводить однократный или двукратный высокий отпуск. В случае двукратного отпуска охлаждение поковок в печи после первого отпуска нужно проводить до температуры 100—150° С для более полного распада аустенита, что позволит при отпуске наиболее полно удалить водород и предупредить образование флокенов.
Необходимость охлаждения до указанных температур объясняется тем, что благодаря дендритной ликвации всех легирующих элементов и углерода в межосных участках дендритов содержится их большее количество, чем в осях, и выше среднего содержания в плавке по химическому анализу. Поэтому нельзя ориентироваться для сталей с устойчивым аустенитом на точку М, поскольку это начало мартенситного превращения, которое продолжается при понижении температуры стали (как это показано на некоторых диаграммах превращения аустенита), а следует ориентироваться на температуру превращения аустенита в межосных пространствах бывших дендритов (которые в результате пластической деформации.
Подверглись изменению в предельном случае образуют первичное волокно из бывших осей и межосных пространств дендритов).
При охлаждении до значительно более высоких температур как при одинарном, так и/при двукратном высоком отпуске оставшийся аустенит может сохраниться при температуре высокого отпуска, что затруднит более полное удаление водорода из стали.
Обратимая отпускная хрупкость стали
Стали, за исключением содержащих молибден, имеют различную чувствительность к развитию хрупкости при медленном охлаждении не только после высокого отпуска, но и при медленном охлаждении после умягчающей термообработки (высокого отпуска или отжига), а также при отпуске закаленной стали в температурном интервале -развития обратимой отпускной хрупкости, особенно в случае достаточно длительной выдержки при таком отпуске.
Молибден задерживает развитие обратимой отпускной хрупкости, но полностью ее не устраняет. Он значительно повышает температурный интервал развития хрупкости, и при длительном высоком отпуске наблюдается некоторое развитие отпускной хрупкости у сталей с молибденом, особенно при его высоком содержании.
Чувствительность к отпускной хрупкости конструкционных легированных сталей, содержащих никель, хром, марганец, увеличивают такие элементы, как фосфор, мышьяк, сурьма, олово.
В большинстве случаев приведенные в ГОСТ 4543—71 после закалки сталей режимы отпуска и охлаждения после отпуска исключают развитие обратимой отпускной хрупкости. Что касается развития хрупкости сталей при медленном охлаждении после умягчающей термической обработки (состояние поставки проката потребителям), то это следует рассматривать как Положительный факт, так как обрабатываемость стали в охрупченном состоянии на металлорежущих станках улучшается, а при последующей термической обработке деталей из такого проката охрупченное состояние устраняется.