Кокс
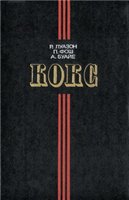
Р. Луазон, П. Фош, А. Буайе
Металлургия, 1975 г.
Метод, который позволяет объяснить, как добавка коксующегося угля способствует уменьшению трещиноватости кокса, производимого из угля с высоким выходом летучих веществ, может быть использован также для объяснения влияния добавок полукоксов. В исследованиях, результаты которых представлены на рис. 94, совмещали графически кривые усадки лотарингского жирного угля В и полукоксов псевдоожижения, полученных при различных температурах. Верхняя часть диаграммы представляет пунктирной линией кривую, относящуюся к жирному углю В, а сплошной линией — кривую, относящуюся к полукоксу. Нижняя часть диаграммы представляет кривую усадки шихты, состоящей из 80% угля и 20% полукокса, причем сплошной линией показана расчетная кривая, а пунктирной линией—экспериментальная. Довольно хорошее совмещение этих двух кривых показывает, что шихта ведет себя так, как этого можно было ожидать. Характер кривых показывает, что полукокс, полученный при температуре 600° С, должен быть менее эффективным, чем полукокс, полученный при 600° С. В самом деле, обе кривые почти одинаково немного уменьшают максимум усадки при температуре затвердевания, но полукокс, полученный при температуре 500° С, заполняя частично на подъёме впадину кривой усадки при 600° С, сильно уменьшает изменения усадки между 600 и 700° С. Напротив, полукокс, полученный при температуре 600° С, усиливает эти колебания. Таким образом объясняется влияние температуры процесса
2. ОБРАЗОВАНИЕ ПОЛУКОКСА
Твердый остаток, образующийся в промежутке времени, когда температура только приближается к 1000° С, за неимением более подходящего термина, мы называем полукоксом (иногда так называют кокс, получаемый при низких температурах).
Поскольку речь идет только о явлениях, происходящих ниже температуры затвердевания, здесь мы касаемся вопросов, связанных с образованием полукокса при температуре примерно 500° С.
В камеру коксовой печи уголь загружается с таким грануломе¬трическим составом, при котором примерно 80% шихты проходит через сито 2 мм.
В интересующей нас области температур, лежащей примерно между 300 и 500° С, скорость нагрева угольной загрузки составляет около 2—4е С/мин; как исключение, она повышается быстрее в не¬посредственной близости от простенка в самом начале коксования.
Соответствующий термический градиент dB/dx (x — расстояние от простенка) составляет около 100е С/см. Этот градиент меняется от 50° С/см, когда зона температур 300—500° С находится в центре камеры, и до 200° С/см и даже больше, когда эта зона находится у простенка. Плотность шихты, рассчитанная на сухой уголь, на¬ходится в пределах 0,7—1; это означает, что 50—70% от общего объема фактически заполнено углем.
Пластический слой или зона—экран
Определение и свойства
В соответствии с данными, изложенными ниже, можно ожидать, что уголь в пластическом состоянии будет находиться между изо¬термическими поверхностями соответствующими темпера¬турам начала плавления и затвердевания при данной скорости нагрева. Температура начала плавления угля при нагреве его в усло¬виях термического градиента несколько ниже, чем при равномерном нагреве. '
Толщина пластического слоя порядка 1 см увеличивается в направлении от простенка к середине печи. Этот пластический слой часто называют зоной—экраном, так как было установлено, что он создает большое сопротивление проходу газов. В случае применения угля высокой степени метаморфизма, хорошо плавящегося, тонкоизмельченного и хорошо уплотненного, потери давления осо¬бенно высоки. Газы гораздо быстрее проходят через пластический слой при большей крупности и небольшой плотности шихты. Пла¬стический слои играет основную роль в процессе вспучивания угля.
Пластический слой образует закрытую оболочку типа баллона. Поскольку газы, образующиеся внутри этой оболочки (например, пары при. 100° С), выходя из нее в некоторой степени теряют давле¬ние, можно было бы ожидать, что внутри пластического слоя господствует избыточное давление газа, который и приводит к возникновению наблюдаемого иногда давления распирания на стенки камеры. Однако дело обстоит не совсем так: эти давления создаются скорее от вспучивания самого пластического слоя, происходящего вследствие образования внутри него пузырьков газа, чем от увеличения давления внутри объема, который этот слой обволакивает. При этом предполагается, что пластический слой плохо замкнут или, по крайней мере, очень проницаем в верхней части загрузки и вдоль дверей печей, где термический градиент незначителен.
Пути движения летучих веществ
Большая часть летучих веществ, выделяющихся в процессе низкотемпературного пиролиза, за исключением паров свободной влаги, образуется в самых горячих областях пластического слоя.
Вследствие относительной непроницаемости экранной зоны по вертикали пиролизные газы следуют по двум путям в зависимости от того — выходят ли эти газы с горячей или с холодной стороны зоны-экрана.
Большая часть газов, а именно 75—90% общего количества летучих веществ, по мнению авторов, выходит с горячей стороны зоны и, пройдя через слой кокса, следует вдоль стенки камеры.
Остальная часть, состоящая главным образом из паров первичных смол, выходит с холодной стороны, проникает в верхнюю часть печи, проходя через уголь и не попадая в зону высоких температур.
Пары первичных смол содержат много компонентов, обладающих очень высокой точкой кипения; эти компоненты конденсируются вокруг более холодных зерен угля, которые им встречаются в не¬посредственной близости от пластического слоя. Вслед за тем температура зоны, в которой сконденсировались смолы, повышается вследствие передачи тепла от стенки камеры. Сконденсировавшаяся смола начинает частично испаряться, слегка удаляясь внутрь печи, и снова конденсируется вместе со вновь образовавшейся смолой. Следовательно, пластический слой в процессе своего движения «толкает» перед собой некоторое количество первичной смолы. Когда уголь доводится до температуры плавления, в нем содержатся тяжелые фракции еще не испарившейся смолы, и это изменяет его поведение по'сравнению с углем, не содержащим этих фракций и находящимся в условиях равномерного нагрева.
Считают, что в начале плавления уголь содержит от 1 до 5% этих тяжелых фракций; их определение и измерение довольно сложны и неточны; проведенные исследования 14] показали, что количество фракций увеличивается с увеличением выхода летучих веществ в загрузке и при удалении от простенка к внутренней части печи.
В условиях лаборатории можно легко проследить за тем, как присутствие некоторого количества тяжелых фракций смолы сильно увеличивает пластичность угля и значительно снижает, примерно на 10—20° С, температуру начала его плавления.
Способы определения толщины пластического слоя
Если в шихту, находящуюся в камере коксовой печи, поместить зонд для определения давления, то по измерениям давления можно будет судить о положении и движении пластического слоя. Гораздо более легким представляется изучение этого явления в лабораторных условиях.
Пластометрический аппарат Сапожникова. В некоторых странах Восточной Европы для изучения коксующих свойств углей используется метод Сапожникова.
Этот метод состоит в измерении толщины пластического слоя в условиях стандартизованного лабораторного опыта при нагреве пробы угля. Проба угля массой 100 г помещается в вертикальный цилиндр, нагреваемый снизу. Когда в его нижней части начинает образовываться кокс, в уголь вертикально вводят иглу. Момент, когда можно заметить, что сопротивление погружению иглы становится слабее, означает, что игла вошла в пластический слой. Продолжая углублять иглу, мы, наконец, наталкиваемся на слой затвердевшего полукокса.
Толщина пластического слоя измеряется величиной в миллиметрах участка иглы между этими двумя моментами при ее погружении.
Было предложено измерять одновременно с толщиной пластического слоя также температуру плавления и затвердевания, используя в качестве зонда термопару. Однако точность такого измерения на практике оказалась недостаточной, так как между спаем термопары и контактирующим с ним углем не достигается термического равновесия в результате попадания термопары в условия высокого термического градиента.
Рентгено-киносъемка пластического слоя. Пейтави и Лягуст [5] дали самые непосредственные и самые поразительные сведения о пластическом слое. Они помещали в пучок %-лучей, параллельных к изотермической поверхности, маленькую лабораторную печь с плоскостным нагревом, причем стенки этой печи были достаточно проницаемы для проникновения этих лучей. При этом было обнаружено, что при прохождении Х"Лучами пластической зоны наблю¬даются изменения в ее проницаемости для этих лучей, которые отражаются на флуоресцирующем экране и дают очень отчетливое изображение, поддающееся фотографированию и ускоренной съемке на кинопленку. При этом для коксующихся и сильно вспучивающихся углей D25 * наблюдаются четыре зоны, которые легко различаются на кинопленке:
1) зона, в которой уголь еще не подвергся термической деструкции;
2) самая непрозрачная зона, в которой находится уголь в начале плавления, еще до начала вспучивания, как в первой фазе усадки при дилатометрическом испытании (см. рис. 19). Здесь сосредоточивается смола, «толкаемая» пластическим слоем;
4. ЛИТЕЙНЫЙ КОКС
Может показаться, что производить опыты по определению стоимости использования литейных коксов значительно легче, чем доменного кокса, так как сравнительные опыты в вагранке можно сделать за несколько дней с пробами в несколько десятков тонн. На практике вагранки редко работают по несколько дней в достаточно стабильных условиях снабжения и производства, т. е. в постоянном термическом режиме; в аппаратах дающих плавку, по мере необходимости режим обычно меняется в течение суток. Топливо, следовательно, нужно оценивать с учетом частых изменений режима, сильно затрудняющих установление теплового, баланса. Кроме того, отбор проб газа для этих балансов совершенно невозможен из-за неоднородности их состава на колошнике.
Какие требования предъявляют к литейному коксу? Прежде всего, эти требования относятся к двум химическим свойствам: не давать серу в чугун и, смотря по обстоятельствам, науглероживать или, напротив, ненауглероживать чугун. Наконец, требуется, чтобы чугун вытекал из печи очень горячим. Только в некоторых случаях от вагранки требуют повышенную производительность.
Но в противоположность доменному процессу в литейном произ¬водстве расход кокса не имеет большого значения, так как топливо представляет лишь относительно малую часть стоимости шихты. Себестоимость ваграночного передела зависит преимущественно от брака литья, 'получающегося в результате недостаточной температуры чугуна.
Коксовая мелочь
Определение и возникновение
Кокс по определению представляет собой твердый остаток, получаемый при высокотемпературном нагревании угля без доступа воздуха. Нагревание доводят, по крайней мере, до температуры 800— 900° С так, что кокс практически не содержит больше летучих веществ.
Коксовая мелочь обычно является побочным продуктом, т. е. остатком, получающимся в результате грохочения кокса на сите с отверстиями около 10 мм. Недостаток коксовой мелочи вынуждает иногда измельчать мелкие классы кокса для ее получения. Можно также производить коксовую мелочь путем коксования в кипящем слое. Лишь в данном процессе имеется в виду коксование при частичном сжигании с воздухом. Для производства коксовой мелочи, температуру следует доводить, по крайней мере, до 800° С. Варианты зависят от того, каким образом уголь сушат, нагревают или иногда окисляют, возможно за счет рекуперации тепла реакций. Выбор варианта влияет на издержки производства кокса, но практически никак не влияет на его свойства.
Хотя все продукты полностью дегазируются, выход летучих не равен нулю (остается 1—3 или 4%). Речь не идет о настоящих летучих веществах, а о газе (воздух, пар и т. д.), адсорбированном во время тушения кокса на рампе.
Мы увидим, 'что коксовая мелочь, полученная из различных источников, является отощающей добавкой.
ВЛИЯНИЕ ТЕХНОЛОГИЧЕСКИХ ФАКТОРОВ НА КАЧЕСТВО КОКСА
Помимо выбора состава шихты, технологу коксового производства доступны еще некоторые способы воздействия на качество кокса. Однако возможности этих способов, как будет видно, ограничены в том смысле, что получаемые изменения незначительны и эффективность оперативной регулировки не всегда велика. Кроме того, задаваемый режим зависит от особенностей установки — ширина камеры определена конструкцией печей, возможности дробления ограничены существующей аппаратурой и т. д. Тем не менее, те изменения, которые может внести технолог в отдельные элементы регулировки, оказывают заметное влияние на качество кокса. Именно это и является предметом настоящей главы.
1. ПЛОТНОСТЬ ЗАГРУЗКИ И ВЛАЖНОСТЬ Общие положения
Хотя более правильно говорить об объемной массе, мы сохраним термин «Плотность загрузки», который по традиции используется коксохимиками.
Плотность загрузки определяется обычно путем деления загруженной массы угля на объем камеры коксования, ограниченный сверху уровнем планировки.
2) давление выше 200 гс/см2 является опасным, поэтому шихты, дающие при коксовании такие давления распираний, ни в коем случае нельзя использовать в промышленных коксовых печах;
3) определить опасное значение давления в интервале 100— 150 гс/см2 весьма трудно, но можно предположить, что большой опасности этот интервал давлений не представляет.
Необходимо подчеркнуть, что все опыты проводили с учетом промышленных условий коксования (это относится в основном к плотности загрузки и ее гранулометрическому составу). При этом необходимо учитывать коэффициент безопасности, поскольку условия эксплуатации могут нарушаться и изменяться. Например, на коксохимических предприятиях иногда применяют шихту самого крупного помола и самой низкой влажности. В этом случае, чтобы избежать неприятностей, можно увеличить плотность загрузки примерно на 10%, что позволит учесть неравномерность плотности шихты внутри печи.
8. ПУТИ УМЕНЬШЕНИЯ ДАВЛЕНИЯ РАСПИРАНИЯ
Способы снижения давления распирания можно разделить на две группы: воздействующие на характеристики шихты или на условия коксования.
Изменение характеристик шихты
Не все угли опасны с точки зрения возникновения давления распирания. Если какая-нибудь шихта оказывается опасной, то нужно попытаться ее изменить, если это позволяют условия углеснабжения завода и если это не приводит к недопустимому ухудшению качества кокса. В большинстве случаев к шихтам, дающим большое давление распирания, добавляют 20—35% угля с высоким выходом летучих, что позволяет снизить давления распирания до значений, не превышающих 100 гс/см2 без ухудшения качества кокса. Если для снижения давления распирания применяют инертные добавки, то необходимо помнить, что эффективность полукокса, коксовой мелочи и тощего угля тем выше, чем выше тонина помола. Однако в этом случае нужно опасаться ухудшения качества кокса, причем гораздо в большей степени, чем при добавках, состоящих из углей, богатых летучими.
Изменение условий коксования
На условия коксования могут влиять четыре фактора: плотность загрузки, гранулометрический состав углей, температура простенков и способ загрузки.
При классической загрузке шихты насыпным методом с незначительной влажностью (например, 4—5%) можно прибегать к ее увлажнению.до 8—10%, что уменьшает плотность загрузки на 5— 10%. Очевидно, что в подобных случаях следует даже пренебрегать