Хромирование
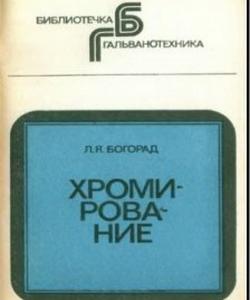
Богорад Л.Я.
Машиностроение, 1984 г.
I. ОСНОВЫ ПРОЦЕССА ХРОМИРОВАНИЯ
Общие сведения
Электролитическое хромирование существенно отличается от других гальванических процессов. Выделение хрома производится из растворов хромовых кислот а не из солей хрома. При этом в растворе обязательно должны присутствовать в небольшом количестве добавки активных анионов, без которых хром не выделяется из хромовой кислоты. Электролиты, основанные на солях хрома, широко изучаются, но до сих пор не получили промышленного применения.
Важной особенностью хромирования является более легкое выделение водорода на катоде, чем хрома; водород начинает выделяться при более положительном потенциале, чем хром, и выход по току при хромировании намного (в три — пять раз) меньше, чем при осаждении других металлов. На выход хрома по току существенно влияют плотность тока и температура электролита.
Показатели процесса и качества покрытия при хромировании и значительно большей степени зависят от режима электролиза (плотности тока и температуры электролита), чем при других гальванических процессах.
Рассеивающая и кроющая способности хромовых электролитов в отличие от других процессов низки, что заставляет применять при хромировании особые приемы для повышения равномерности покрытия. Низкая кроющая способность связана с сравнительно высокой минимальной плотностью тока, при которой начинается выделение хрома.
В хромировочных ваннах применяются только нерастворимые аноды, что требует периодического пополнения убыли хромовой кислоты путем ее непосредственного введения в электролит в необходимых количествах.
Растворы хромовой кислоты токсичны, они увлекаются выделяющимися при электролизе газами. Эго создает необходимость принятия мер предосторожности для оздоровления условий труда при работе на хромировочных ваннах.
2. Катодный процесс
Во время хромирования на катоде происходят следующие основные процессы:
осаждение хрома;
выделение водорода;
восстановление аниона хромовой кислоты, где хром шестивалентен, до соединений, в которых хром имеет меньшую валентность, в основном, трехвалентного хрома;
образование на поверхности катода тонкой пленки, состоящей из активного аниона и продуктов восстановления хромовой кислоты.
Большое влияние на эти процессы оказывает количество и род активных анионов, содержащихся в электролите.
Износостойкость хромовых покрытий в значительной степени зависит от их прирабатываемости. При недостаточно хороших условиях для приработки (местной шишковатости покрытия, неравномерном нагрузке на его поверхность и др.) возможны схватывания и задиры трущихся поверхностен. Для улучшения прирабатываемости кроме устранения указанных недостатков, рекомендуют сопряженную с хромом деталь оксидировать или фосфатировать. а деталь, покрытую пористым хромом, электролитически покрывать тонким слоем олова.
Высокая износостойкость хромовых покрытий полностью реализуется при трении по стали и чугуну. Имеются данные, что в паре с алюминиевыми сплавами и алюминиевыми бронзами при недостатке смазки хромовые покрытия изнашиваются значительно больше, чем по стали и чугуну.
11. Влияние хромирования на механические свойства основного металла
В зависимости от рода нагрузки, вызывающей разрушение металла, различают механические характеристики, определяемые при растяжении образца до его разрыва (пределы прочности и текучести, относительные удлинение и сужение поперечного сечения) и его выносливость (время до разрушения) при циклически меняющейся нагрузке (предел усталости). Возможны два вида нагрузок, от которых зависит время до разрушения: нагрузки, при которых циклические деформации металла не выходят за пределы упругой деформации, и нагрузки, при максимальных значениях которых возможна обычно небольшая пластическая деформация образца. В первом случае образец разрушается после воздействия миллионов циклов нагрузки (многоцикловая усталость), во втором случае разрушение происходит после нескольких тысяч циклов (малоцикловая усталость).
Особенно важными для надежности современных машин являются показатели прочности при циклически меняющейся нагрузке. Наиболее значительное влияние хромирование оказывает именно на эти показатели.
Хромирование может оказывать воздействие на механические свойства основного металла по следующим причинам:
хромовое покрытие отличается исключительно высокой прочностью сцепления с основным металлом, поэтому хромированную деталь необходимо рассматривать как систему, свойства поверхности которой определяются свойствами хромового покрытия;
в хромовых покрытиях имеются значительные напряжения растяжения, распространяющиеся по поверхности хромированной детали;
твердые хромовые покрытия не выдерживают пластической деформации основного металла, растрескиваются и эти трещины являются концентраторами напряжения для основного металла;
в процессе электроосаждения хрома выделяется относительно большое количество водорода, который, проникая в основной металл, вызывает его охрупчивание.
Прочность и пластичность хромированной стали. Предел прочности стали, определяемый при статическом растяжении, практически не изменяется после хромирования.
Хромирование цилиндров двигателей внутреннего сгорания. Увеличение износостойкости трущейся пары цилиндр — поршневые кольца осуществляется применением пористых хромовых покрытии. Как указывалось, пористый хром применяется для тяжелонагруженных деталей машин, работающих при высоких давлениях, повышенных температурах и недостаточно хорошей смазке. Гладкие хромовые покрытия в таких условиях, характерных для нормальной работы цилиндров и поршневых колец двигателей, недостаточно стойки. Практикой установлено, что зеркало цилиндра двигатели, покрытое гладким хромом, после 3—5 ч испытания на стенде оказывалось разрушенным.
Вследствие недостатка смазки происходит сильное местное разогревание и выкрашивание частичек хрома, влекущее за собой появление на зеркале цилиндра глубоких царапин. При пористом хромировании эти недостатки исключаются.
Увеличение срока службы цилиндра обычно достигается двумя путями. Первый состоит В' пористом хромировании внутренней поверхности цилиндра, работающего в паре с чугунными поршневыми кольцами. При этом многократное увеличение общего срока службы цилиндра возможно за счет проведения повторного хромирования цилиндра. Второй путь заключается в пористом хромировании поршневых колец, которые, работая в паре с нехромированным цилиндром, способствуют уменьшению его износа. Износостойкость детали, покрытой пористым хромом, возрастает в три — пять раз, срок службы сопряженно работающей детали увеличивается примерно в полтора — два раза. Выбор того или иного пути зависит от производственных возможностей.
В практике пористого хромирования шлифование хромируемой поверхности производится перед анодным травлением. После создания сетки каналов пористого хрома, при необходимости, производится приработка хромированной поверхности п масле (например, при беспритирочном пористом хромировании поршневых колец).
Применение для сглаживания пористого хрома хонингования или притирки абразивными порошками не допускается. При такой обработке сошлифовывается значительная часть пористого слоя покрытия, а частички абразива внедряются в каналы пористого хрома. В этом случае рекомендуется хромирование производить на реверсивном токе или после хромирования производить шлифование хрома до нанесения сетки пор.
При подготовке к хромированию имеющиеся на цилиндрах окна и смазочные отверстия необходимо заделать свинцом. Эту операцию следует выполнять так, чтобы свинец выступал над хромируемой поверхностью примерно на 0,5 мм. При этом выступающая часть свинца несколько экранирует края отверстия, и хром на них осаждается значительно меньшим слоем. Если заделку отверстия произвести заподлицо с поверхностью детали, то хром отложится на острых краях отверстия, и вследствие этого при работе цилиндра возможно его скалывание.
Повышение производительности ванн. Для этого необходимо рационально загрузить ванны деталями, полностью загрузить их током, сократить продолжительность хромирования за счет уменьшения расчетного слоя хрома, увеличения выхода по току, повышения равномерности покрытия. Для рациональной загрузки ванн деталями целесообразно распределить их по группам таким образом, чтобы в каждой группе были детали однотипные: по габаритным размерам, толщине слоя хрома, величине хромируемой поверхности и форме. Для каждого типа деталей разработать рациональные приспособления для завешивания в ванну.
Величина поверхности загруженных в ванну деталей определяется значением полной токовой нагрузки ванны, т. е. силой тока, при которой заданная температура электролита поддерживается за счет джоулевой теплоты, без подачи пара (для горячих электролитов).
Если по габаритным размерам детали загружают ванну полностью, а по величине поверхности загрузка недостаточна, то повышают плотность тока по возможности до достижения полной токовой нагрузки. Такое повышение плотности тока с сохранением требуемого качества покрытия достигается на основе изложенных ранее закономерностей, определяющих рабочий интервал. Хромирование при возможно более высоком выходе хрома по току связано с выбором состава электролита и режима осаждения. Выход по току наибольший (до 40 %) в тетрахроматных холодных электролитах, затем в сульфатно-кремнефторндных (17—19 %) и в сульфатных (13—15 %)
Выход по току возрастает с увеличением плотности тока, что особенно проявляется в малоконцентрированных сульфатных электролитах; в этом случае при «„ = 45 А/дм2 выход по току 15%, а при iK = 80 А/дм2 выход по току достигает 20 % (< = 55°С). Применение высоких плотностей тока в пределах сохранения требуемого качества покрытия возможно в проточном электролите с некоторым повышением выхода по току.
Выход хрома по току является важным показателем эффективности электролита, однако при технико-экономическом анализе для выбора электролита учитываются и другие его особенности: потери хромового ангидрида, зависящие от его концентрации в электролите, необходимость специальных установок для охлаждения электролита при низких температурах, химическая агрессивность электролита, сложность его состава и др.
При нанесении толстых покрытий значительное повышение производительности ванн может быть достигнуто за счет мероприятий, повышающих равномерность покрытия (см. гл. I). Скорость наращивания покрытия определяется на том участке поверхности, где толщина покрытия наименьшая. Поэтому, чем более равномерно покрытие, тем выше расчетная скорость наращивания при той же заданной средней плотности тока. Сокращение продолжительности хромирования, и довольно значительное, дает также применение размерного хромирования, при котором покрытие наносится без припуска на шлифование. Толщина этого припуска примерно 0,1—0,15 мм и его наращивание требует продолжительности хромирования при плотности тока 60 А/дм2 1.5—2,0 ч.