Химико-термическая обработка стали
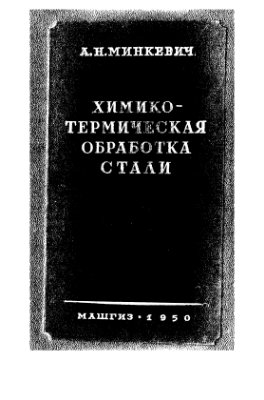
Минкевич А.Н.
Машгиз, 1950 г.
СТАЛЬ, ПРИМЕНЯЕМАЯ ДЛЯ ЦЕМЕНТАЦИИ
Цементованные детали после соответствующей термической обработки должны иметь твердый поверхностный слой высокой прочности, устойчивый против износа и продавливания, и одновременно достаточно прочную и вязкую сердцевину. В связи с последним требованием для цементации применяют низкоуглеродистую сталь с содержанием углерода в пределах 0,08 —0,25%. Для деталей, большого сечения или при необходимости иметь повышенную прочность сердцевины применяют сталь с содержанием углерода 0,20—0,30%.
В последние годы наметилась тенденция к увеличению содержания углерода в цементуемой стали, применяемой для многих ответственных деталей и, в частности, для высоконагруженных шестерен, поэтому большинство сталей новых составов содержит углерод по верхнему из указанных выше пределов.
Л. С. Мороз и С. С. Шураков [6] на основании проведенных механических испытаний и опыта промышленности считают, что содержание углерода в высоколегированной цементуемой стали ряда марок должно быть повышено с 0,10—0,18 до 0,18—0,24°,Повышение содержания углерода позволяет снизить глубину цементованного слоя, не опасаясь его продавливания при больших нагрузках, предотвращает преждевременное разрушение цементованного слон из-за пластической деформации слоев металла, лежащих непосредственно под ним, оказывает положительное влияние на обрабатываемость стали резанием и сближает критические точки цементованного слоя и сердцевины, что позволяет производить закалку сердцевины без перегрева цементованного слоя.
Исследования большого количества шестерен танков, изготовленных во время Великой Отечественной войны в Чехословакии, США, Англии и Германии, также показывают [6], что содержание углерода в стали большинства шестерен колеблется от 0,18 до 0,25%, а в отдельных случаях доходит до 0,30%, т. е. находится на верхнем пределе и даже несколько выше, чем это допускалось ранее для цементуемой стали.
Для цементации широко применяется низкоуглеродистая качественная сталь марок 08, 10, 15 и 20. Для деталей, изготовляемых на станках-автоматах (болты, гайки, винты), применяется автоматная сталь марок Авт. 12, Авт. 15, Авт. 15Г и Авт. 20, дающая чистую поверхности резании. Для неответственных деталей применяется низкоуглеродистая сталь обыкновенного качества — Ст. 1, Ст. 2, Ст. 3.
Для ответственных цементуемых деталей, сердцевина которых должна обладать высокими механическими свойствами, а цементованный слой —повышенными износоустойчивостью и прочностью, применяется легированная сталь. Ее применение вызывается также повышенной прокаливаемостью и возможностью уменьшить деформации деталей при закалке. Последнее достигается закалкой стали в масле вместо закалки в воде и применением во многих случаях одинарной (или непосредственной) закалки вместо двойной, поскольку легированная сталь большинства марок имеет более мелкое зерно.
При выборе стали для тех или иных целен следует учитывать работу деталей в области упругих деформаций, поэтому при оценке стали различных марок для таких деталей необходимо ориентироваться не на величину предела прочности, а на величину предела упругости и предела текучести.
Второй характеристикой свойств цементуемой стали является пластичность сердцевины, которая характеризуется главным образом величиной ударной вязкости. Несмотря на общепринятое этого требования, в ряде работ [6] было доказано отсутствие во многих случаях прямой связи между ударной вязкостью, а также? прочностью при статическом изгибе цементованных образцов и этими же характеристиками для сердцевины этой стали. Это объясняется тем. что исходные трещины при статическом и динамическом изгибе ((испытании на удар) цементованных образцов возникают на поверх л гости цементованного слоя и, играя роль острых надрезов и источников напряжений, затем быстро распространяются в глубь стали. Таким образом, прочность цементованного слоя, так же как и свойства сердцевины, должна учитываться при выборе стали для изделий ответственного назначения.
Л. С. Мороз и С. С. Шураков (на основании широко поставленных экспериментов пришли к выводу, что к легированной цементуемой стали помимо требований к чистоте стали, отсутствия полосчатости, анормальности в цементованном слое и технологических требований (хорошая обрабатываемость резанием, минимальная деформация л т. д.) должны предъявляться также следующие требования:
1. Состав стали не должен способствовать чрезмерной концентрации углерода в цементованном слое, так как образование большого количества карбидов снижает прочность цементованного слоя.
2. В цементованном слое ire должно быть большого количества остаточного аустенита, также снижающего прочность слоя.
3. Цементованный слой должен обладать максимально возможным пределом прочности при изгибе.
4. Первостепенной характеристикой сердцевины цементуемой стали должен являться высокий предел текучести. Это объясняется тем, что при определенных свойствах сердцевины и отношениях глубины цементованного слоя к толщине детали под цементованным слоем при приложении изгибающих нагрузок может развиваться пластическая деформация, вызывающая перенапряжение цементованного слоя и его разрушение. Следовательно, более высокий предел текучести сердцевины предотвратит перенапряжение цементованного слоя.
Указанные авторы, а также В. Т. Чириков предлагают ввести новую важную характеристику цементованной стали — прочность. Цементованного слоя на изгиб с определением усилия в момент образования первой трещины.
Из изложенного следует, что неверно было бы судить по величине Ударной вязкости сердцевины стали о прочности цементованной детали в работе при приложении динамических и статических нагрузок. Важнейшее влияние на прочность цементованной детали оказывают свойства цементованного слоя и предел текучести сердцевины.
В табл. 9 приведен химический состав, а в табл. 10 — механические свойства применяемой цементуемой легированной стали.
Хромистая сталь является наиболее широко применяемой в различных отраслях промышленности легированной цементуемой сталью. Преимуществом хромистой стали марок 15Х u 20Х по сравнению с углеродистой является возможность закалки ее в масле, что гарантирует меньшее коробление в процессе закалки и получение меньших напряжений в закаленных деталях.
Сталь 20X3 имеет по сравнению со сталью марок 15Х и 20Х ряд недостатков . После цементации в активном карбюризаторе и последующей закалки поверхностная зона цементованного слоя этой стали обладает повышенной хрупкостью вследствие большого количества карбидных выделений. В цементованном слое этой стали закалкой фиксируется значительное количество остаточного аустенита. Сталь 20X3 склонна к перегреву и короблению при закалке. Большими недостатками этой стали являются также трудность ее выплавки (плавка ведется при высокой температуре, что приводит к быстрому прогоранию сводов мартеновских печей) и склонность к образованию волосовин и трещин при прокатке.
Сталь 20X3 имеет высокие механические свойства, ее цементованный слой отличается прочностью и износоустойчивостью, и детали из этой стали обладают высокой эксплуатационной стойкостью (19]. Эта сталь является заменителем стали марок 12Х2Н4А, 12ХНЗ, 18ХГМ и др.
Поверхностная твердость стали 20X3 после цементации и закалки находится в тех же пределах, что у стали марок 15Х и 20Х {Hrg=58-62). Хромистая сталь после цементации и закалки обладает несколько повышенной чувствительностью к образованию шлифовочных трещин. Повышение температуры отпуска со 150—170° до 200—220° уменьшает возможность появления шлифовочных трещин, однако сопровождается некоторым понижением твердости.
Из стали марок 15Х и 20Х изготовляются детали, работающие на износ при малых и средних нагрузках, из стали 20X3 —детали, работающие при больших нагрузках. Например, в автомобильной промышленности из стали марок 15Х и 20Х изготовляются распределительные валы, кулаки тормоза, толкатели клапана и т. д., из стали 20X3 изготовляются шестерни полуоси, шестерни ведомые, крестовины и сателлиты дифференциала и т. д. В станкостроении из стали марок 15Х и 20Х изготовляются различные шестерни, валики и другие детали.
Исследования [83—84] по цементации нержавеющей высокохромистой стали типа Ж1 (0,15% С; 12,5—14,5% Сr) были проведены с целью выявления возможности изготовления из нее измерительного инструмента и деталей приборов и машин, работающих на истирание. Скорость цементации такой стали заметно меньше, чем нелегированной стали. После закалки цементованной стали этого состава с 850—920° удается получить поверхностную твердость Hrc —=65 -66. При закалке с 1050° в поверхностном слое получается структура почти чистого аустенита, и при последующем отпуске наблюдается явление вторичной твердости благодаря выпадению мелкодисперсных карбидов хрома и превращению остаточного аустенита в мартенсит.
Цементация стали, содержащей одновременно большое количество хрома и никеля, не привела к положительным результатам, так как эта сталь науглероживается весьма медленно. По данным Н. Т. Гудцова и Л. Д. Масштаковой у стали с 8% хрома и 1896 никеля, цементованной в естественном газе при 930° в продолжение 100 час, глубина цементованного слоя достигает всего лишь 0,35—0,45 мм.
Никелевая сталь, обладающая повышенной вязкостью, нашла в промышленности ограниченное применение только для самых ответственных деталей: в двигателестроении, дизелестроении и автостроении для распределительных валов, кулачковых шайб, наиболее ответственных шестерен и других деталей. В последнее время вместо никелевой стали находят все более широкое применение хромоникелевые стали с пониженным содержанием никеля, а также другие стали, которые по механическим свойствам почти не уступают никелевой стали.
Марганцовистые цементуемые стали, обладающие по сравнению с углеродистой сталью несколько повышенной прочностью, нашли ограниченное распространение и применяются преимущественно для малоответственных деталей вследствие чувствительности к перегреву цементованного слоя. В качестве цементуемых применяются стали марок 15Г и Авт 15Г. В последней наличие марганца предотвращает красноломкость стали при горячей механической обработке.
Добавка вцементуемую сталь какого-либо одного легирующего элемента не всегда в достаточной степени улучшает механические и технологические свойства стали или улучшает одни свойства, но ухудшает другие (например, при повышении предела прочности и предела текучести понижается вязкость), поэтому в сталь, применяемую для ответственных деталей, добавляют одновременно два или три легирующих элемента. Таким путем удается достигнуть необходимого сочетания высоких свойств сердцевины и поверхностного цементованного слоя стали и улучшить некоторые ее технологические свойства.
Совместное легирование стали хромом и никелем весьма эффективно, как для получения глубокой прокаливаемости, так и для получения после термообработки высокой прочности, вязкости и износоустойчивости. При высоком содержании в стали хрома и никеля обрабатываемость стали резанием ухудшается. При продолжительной Цементации в поверхностном слое хромоникелевой стали с повышеннымсодержанием хрома наблюдается как и в хромистой стали образование крупных скоплений карбидов (реже в виде сетки и чаще в виде глобулей).