Химическая технология огнеупоров
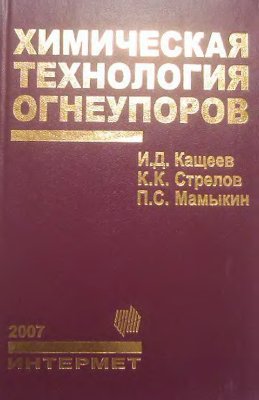
И. Д. Кащеев, К. К. Стрелов, П. С. Мамыкин
Интермет Инжиниринг, 2007 г.
ПРОИЗВОДСТВО ГРАФИТОШАМОТНЫХ ИЗДЕЛИЙ
Состав графитошамотных шихт для тиглей, пробок или стаканов неоднороден, с отклонениями в довольно широких пределах. Состав шихт для изготовления графитошамотных тиглей включает 22-25 % глины, 50-48 % графита, 25-30 % шамота, для изготовления пробок - соответствующие компоненты в количестве 30-35, 20-30 и 45-40 %. В качестве связки необходимо использовать тонкодисперсную высокопластичную глину с температурой спекания 1150-1250 °С. Такая глина в смеси с графитом позволяет получить высокопластичную массу, в которой графит наиболее защищен от окисления, а материалу обеспечивается хорошее спекание. Компоненты шихты дозируют по массе; порошки сначала смешивают всухую, затем увлажняют и перемешивают вторично. Последнюю стадию обработки увлажненной шихты обычно проводят на ленточном прессе, после которого куски массы поступают на 15-20 сут в камеры вылеживания для повышения пластичных свойств. После вылеживания массу еще 2-3 раза пропускают через ленточный пресс, форма мундштука которого обеспечивает получение заготовок необходимой конфигурации. Затем из заготовок путем допрессовки или формования в гипсовых формах изготовляют изделия.
Сушить графитошамотные изделия следует очень осторожно, так как чешуйчатый графит затрудняет перемещение влаги в изделиях. При чрезмерно интенсивной сушке на изделиях легко возникают вздутия и трещины. Особенно трудно сушить тигли, содержащие крупночешуйчатый графит. Поскольку графитошамотные изделия относятся к продукции, изготовляемой малым тоннажом, камерные сушила, в которых можно осуществлять любой режим сушки, следует считать предпочтительными. Для сушки тиглей рекомендуется следующий режим: вначале сушка 5-8 сут при 20-30 °С в невентилируемом помещении, а затем 8-10 сут при 30-40 °С - в вентилируемом. Крупногабаритные тигли сушат дополнительно 3-5 сут при 50 °С. Пробки сушат в течение 15-20 сут: 4-5 сут при 20-25 °С и 10-15 сут при 30-35 °С. Влажность изделий после сушки не должна превышать 3 %.
Обжигают графитошамотные изделия в коксовой засыпке в шамотных капселях при 1300-1350 °С. Обжиг в засыпке - трудоемкая операция, сопровождающаяся большим выделением угольной пыли, поэтому графитошамотные пробки целесообразно обжигать в восстановительной среде без коксовой засыпки в небольших периодических печах муфельного типа. В период охлаждения изделий до 500 °С в печь впрыскивается небольшое количество тонкораспыленного мазута, что предохраняет изделия от выгорания углерода в период охлаждения.
По комбинированному способу производства графитошамотных изделий, включающему сочетание пластического и полусухого способов, брикет для получения «ложного» зернового состава готовят пластическим способом, а изделия прессуют методом полусухого прессования. Графит и глина влажностью около 5 % в соотношениях, соответствующих составу шихты, смешиваются в шаровой мельнице периодического действия в течение 20-30 мин. Затем в смесь добавляют шамот и смешение продолжают еще 5 мин. При большом объеме производства совместный помол осуществляют в трубных мельницах. Такая обработка обусловлена стремлением уменьшить окисляемость графита путем диспергирования и покрытия его поверхности глиной.
Шихта после смешения в шаровой мельнице увлажняется до 20-30 % в двухвальном смесителе, в который подается около 2 % ЛСТ (от сухой массы), и поступает на ленточно-вакуумный пресс. Так получается брикет («валюшка»). Сухой брикет измельчают в зубчатых вальцах с расчетом получения предельного размера зерен 4 мм и менее 0,5 мм в количестве 30-35 %. Высушенный брикет дробят в смеси с влажным, благодаря чему регулируется влажность массы в пределах 6-7 %. Затем масса поступает на домол в гладкие вальцы и протирочное сито с отверстиями диаметром 5 мм. Так получается «ложный» зерновой состав. Крупные частицы размером более 4 мм, необходимые для пропрессовки изделий при полусухом прессовании, в действительности состоят из значительно более мелких частиц графита, шамота и глины.
Изделия прессуют на гидравлическом прессе усилием 630 т; лучшие результаты получают при гидростатическом прессовании. Сушат изделия весьма осторожно. Графитошамотные стаканы, например, сушат на стеллажах в помещении в течение 6-12 сут при температуре около 35 °С. При сушке в сушилках на полочных вагонетках соблюдают следующий режим. Температура сушки не должна превышать 20 °С при относительной влажности выше 65 %, продолжительность сушки 5-7 сут; остаточная влажность не более 2 %. Высушенные изделия сортируют поштучно. Изделия с трещинами, посечками, помятостями, расслоениями и другими дефектами отбраковываются. Обжиг изделий производят в коксовой засыпке. Применение глазурей позволяет улучшить санитарно-гигиенические условия и технико-экономические показатели производства графитошамотных огнеупоров. Глазурованные изделия можно обжигать в туннельных печах без коксовой засыпки. Свойства графитошамотных изделий: предел прочности при сжатии 35-50 МПа, огнеупорность 1900 °С, температура начала деформации под нагрузкой 0,2 МПа 1380-1490 °С, ТКЛР в интервале 0-1000 °С, 2,8-6-3,8-6 К-1 ,теплопроводность при 250 °С на горячей стороне 3,7-6,2 Вт/(мК).