Карбиды и сплавы на их основе. Сборник статей.
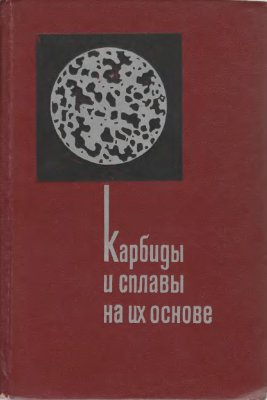
Наукова думка, 1976 г.
ПРИМЕНЕНИЕ ТУГОПЛАВКИХ КАРБИДОВ ДЛЯ ИЗГОТОВЛЕНИЯ ДЕТАЛЕЙ ИСПАРИТЕЛЬНЫХ ЭЛЕМЕНТОВ
Ρ.Е. МУРАШКО, В. Н.СУМАРОКОВ, Л. И. СТРУК, С. А. ШВАБ
Одним из прогрессивных технологических процессов, получающих все большее развитие в последние годы, является процесс вакуумной металлизации, используемый для получения материалов с особыми свойствами, которые применяют в различных областях техники.
Основным узлом установок вакуумной металлизации является испаритель металлов. В промышленных установках непрерывного и полунепрерывного действия обычно применяют электроннолучевые испарители, основными элементами которых являются источник электронов — электронная пушка и тигельное устройство (испарительный элемент), содержащее испаряемый металл [1].
Условия работы тигля включают разогрев его с испаряемым металлом до высокой температуры (температуры интенсивного испарения металла), длительный контакт с перегретым металлом и его парами в вакууме, частые смены температур при включении и выключении установки. В случае испарения химически активного металла, такого, как алюминий, испарение которого происходит при большом перегреве (температура интенсивного испарения алюминия равна 1400—1600° С), разработка тигля представляет большие трудности и является одной из основных задач при создании промышленных агрегатов вакуумного алюминирования, так как сроком службы тигля определяется ресурс непрерывной работы установки вакуумной металлизации.
Основными требованиями, предъявляемыми к испарительному элементу, являются высокая термостойкость; способность обеспечивать высокие и стабильные скорости испарения на протяжении всего срока службы; длительный срок службы, измеряемый, как минимум, несколькими часами; небольшие тепловые потери при работе. Поэтому к материалу испарительного элемента предъявляются такие основные требования: высокая химическая устойчивость к перегретому алюминию и его парам; высокие плотность и механическая прочность; низкая упругость пара при температурах испарения алюминия; простота обработки.
В практике испарения алюминия для изготовления испарительных элементов применяются графит, окисная огнеупорная керамика и тугоплавкие бескислородные соединения, причем, как показывает опыт, для получения чистых алюминиевых покрытий требуется применять тугоплавкие соединения, такие как бориды Ti, Zr, карбиды Ίi, Та, Zr, Si, нитриды Si, В, А1 [2,3].
В частности, для повышения стойкости графитовых тиглей в расплаве алюминия применяется создание на их рабочей поверхности защитных слоев карбидов, препятствующих взаимодействию алюминия с графитом. Такие слои из карбидов Ti, Zr, Та, Si, Wполучают либо предварительной специальной обработкой поверхности тигля, либо добавлением этих металлов в расплав алюминия в начальной стадии работы [4—6].
Хотя наличие таких карбидных слоев на поверхности тигля и играет положительную роль, препятствуя образованию в расплаве большого количества карбида алюминия, сильно снижающего скорость испарения, оно не приводит к заметному повышению срока службы графитового тигля, разрушающегося в результате образования трещин в защитном слое из-за неодинаковости физических свойств материалов защитного слоя. Применение для изготовления тиглей графитовых материалов, содержащих в своем составе карбид циркония, также не дало нужных результатов. Недостаток тиглей из этих материалов — образование в расплаве большого количества карбида алюминия в результате взаимодействия расплава со свободным углеродом. Так, для тиглей с размерами в плане 110 *70 мм и высотой 50 мм при мощности нагрева до 7—8 квт через 1 ч работы в режиме испарения скорость испарения снижалась почти до нуля. Конденсат при испарении из такого тигля содержит значительное количество углерода.
Наилучшие результаты дает применение тугоплавких соединений — боридов, карбидов, нитридов, имеющих повышенную стойкость к перегретому алюминию. Однако ни один из этих материалов не отвечает полностью требованиям, предъявляемым к материалу тигля для испарения алюминия. Наиболее подходящее сочетание свойств, а именно сочетание высокой стойкости к алюминию с термомеханической прочностью и высокой плотностью можно получить, создавая многокомпонентные материалы .