Как повысить стойкость режущего инструмента
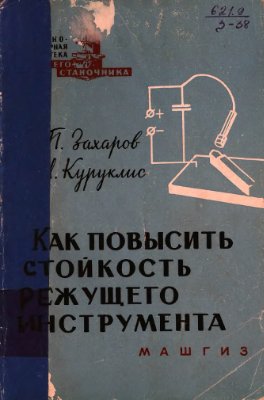
Захаров Б.П., Куруклис Г.Л.
Машгиз, 1962 г.
ШЛИФОВОЧНЫЕ ОЖОГИ
Чем объясняется такой странный характер износа? Почему вначале инструмент изнашивается быстро, а потом медленнее? Это объясняется тем, что на поверхности вновь изготовленного или заново переточенного инструмента всегда имеется тонкий испорченный, поврежденный/или, как принято его называть, дефектный, слой. Мы не говорим о том браке, который получается иногда при неумелой или небрежной работе термистов и заточников. Речь идет о таких повреждениях, которые получаются даже при самом тщательном выполнении всех технологических процессов. Возникновение этого дефектного слоя, как мы сейчас увидим, почти неизбежно. Однако толщина его очень сильно зависит от качества работы заточников. При неумелой и небрежной работе толщина дефектного слоя увеличивается.
Дефектный слой на поверхности режущего инструмента получается потому, что при заточке поверхность затачиваемого инструмента очень сильно нагревается. Температура в тонком слое на поверхности инструмента достигает нескольких сот градусов (800—1000°). Под влиянием, такого нагрева появляются так называемые шлифовочные ожоги, структура поверхностного слоя стального инструмента изменяется.
Кроме того, этот тонкий слой, почти мгновенно нагревшийся до очень высокой температуры, почти также быстро охлаждается со скоростью до 1000° -в секунду, так как остальная масса инструмента холодная. В результате этого происходит вторичная закалка, причем явно некачественная. Если инструмент изготовлен из углеродистой стали, то температура даже 800° для него излишне высока, и поверхностный слой окажется перегретым.
Если же инструмент изготовлен Ή3 быстрорежущей стали, то температура даже 1000° для нее совершенно недостаточна (для закалки быстрорежущей стали требуется температура 1250—1300°), и поверхностный слой окажется недогретым. А если быстрорежущую сталь не-догреть при закалке, то красностойкость ее сильно понизится.
Это еще не все. Некачественно закаленный поверхностный слой является еще и неотпущенным. А это также очень плохо: закаленная, но неотпущенная углеродистая сталь слишком хрупка, а закаленная, но неотпущенная быстрорежущая сталь имеет пониженную твердость, стало быть, ее износостойкость будет также пониженной.
Но и это еще не все. Под некачественно закаленным поверхностным слоем находится второй слой, который также нагревается при заточке, но до температуры 600—800°. При такой температуре происходит отпуск этого слоя. Твердость его снижается с 60—62 единиц по Роквеллу до 55—58 (быстрорежущая сталь) и до 30— 35 (углеродистая сталь).
Таким образом, получается, что от заточки на поверхности стального инструмента образуется тонкий некачественно закаленный и неотпущенный слой, который лежит на переотпущенном слое, потерявшем нормальную твердость.
На фиг. 2 схематически изображена структура поверхностного слоя инструмента, очень осторожно заточенного и не имеющего шлифовочных ожогов, и другого инструмента, заточенного в обычных условиях и имеющего дефектную структуру поверхностного слоя.
На фиг. 3 показано распределение твердости на различных расстояниях от поверхности заточенного инструмента.
Подтвердим сказанное одним очень интересным снимком. На фиг. 4 показана увеличенная фотография структуры поверхности быстрорежущей стали. Такая структура получилась в результате работы одного зерна заточного круга. Средняя узкая полоска, идущая посередине снимка,— это след (царапинка), который оставило зерно на поверхности стали. Посмотрите, как изменилась структура стали от работы одного единственного абразивного зерна: вдоль царапинки по обеим ее сторонам располагается светлый слой вторично закаленной стали, а дальше за ним идут темные слои переотпущенной стали. Когда производится настоящая заточка и работает не одно зерно, а множество зерен, то получается такая же картина, но только переотпущенные слои располагаются не рядом с вторично закаленными, а под ними.
Итак, дефектный поверхностный слой заточенного инструмента имеет плохую структуру и пониженную твердость. Но, может быть, это не так уж и страшно? Положим, что твердость снизилась на несколько единиц. Вероятно, на несколько процентов снизится и стойкость инструмента. Если бы это так и было, тогда, действительно, не стоило бы очень и огорчаться. На самом же деле все обстоит гораздо серьезнее. Рассмотрите внимательно фиг. 5, и вам станет ясно, почему так опасна пониженная твердость. Посмотрите, как круто взмывает кривая износа вверх по мере понижения твердости резца. Допустим, что вместо твердости 62—63 единиц по Роквеллу твердость резца получилась равной 58, т. е. уменьшилась на 4—5 единиц (всего на 7—8%). А сосчитайте на диаграмме по числу клеточек, на сколько увеличилась величина износа. Она увеличилась в три с лишним раза, то есть на 200%. Стойкость снизилась в три раза.
Очень интересна и фиг. 6. На ней изображена зависимость износа резца от скорости резания при точении.
Ничего нет удивительного в том, что кривые поднимаются вверх. Так оно и должно быть: чем больше скорость резания, тем значительнее величина износа. Это естественно, но не это мы хотим- подчеркнуть. На фиг. 6 изображены две кривые, постоянно расходящиеся по мере своего подъема. Одна из них относится к резцу, заточенному на круге, вращающемся со скоростью 33,3 м/сек, а другая — к резцу, заточенному на круге, вращающемся со скоростью, вдвое меньшей (16 м/сек). И χοτ резец, который был заточен при более высокой скорости заточного круга, быстрее изнашивается. В самом деле, сравним величины износа обоих резцов, например, при скорости точения 40 м/мин. Величина износа одного резца почти вдвое больше величины износа другого. Это легко сосчитать по клеточкам. Эту разницу в величинах износа нетрудно объяснить: у то-
го резца, который был заточен на круге, вращавшемся с большой скоростью, структурные изменения от нагрева получились более значительными, потому что и нагрев был значительнее, да и дефектная структура распространилась на большую глубину.
Мало того, что заточенный инструмент имеет в поверхностном слое дефектную структуру и по
ниженную твердость. В этом поверхностном велики и внутренние напряжения. В самом деле, поверхностные слои инструмента нагреваются при заточке до очень высокой температуры за короткое время. Нагревшись, они должны расширяться, но этого не может произойти, так как эти нагретые слои прочно скреплены с более глубокими холодными слоями. Наружные слои должны расшириться, но не могут, значит, они окажутся как бы.сжатыми, а внутренние слои — растянутыми; их растягивают нагретые наружные слои. При последующем, также очень быстром охлаждении возникнут новые напряжения, которые отчасти уменьшат прежние напряжения, возникшие при нагревании, а отчасти будут с ними суммироваться.
Инструментальщики знали, что эти напряжения значительны, но они не знали точного значения внутренних напряжений. Сравнительно недавно одному американскому ученому удалось, применив рентгеновский метод, определить численные значения этих внутренних напряжений. Результаты его определений представлены на фиг. 7. Обратите внимание, какой громадной величины достигают напряжения в самом поверхностном слое (90 кг/мм2).
Для того чтобы легче было представить эту величину, напомним, что предел прочности стали марки Ст. 3 составляет всего 40—50 кг/мм2.
Поверхностный слой заточенного инструмента с дефектной структурой, оказывается, не только имеет пониженную твердость, но к тому же еще и хрупок, так как весьма напряжен.
После всего сказанного легко понять, почему стальной инструмент изнашивается неравномерно. Вначале он изнашивается очень быстро, потому что в этот период происходит износ поверхностного дефектного слоя, имеющего низкую твердость и большие внутренние напряжения. Когда этот дефектный слой полностью износится, наступает второй период — период незначительного износа части инструмента с нормальной структурой. Когда же режущая кромка затупится, сила резания возрастает настолько, что увеличится трение и усилится нагрев, в результате чего возрастет износ.