Износостойкие белые чугуны: свойства, структура, технология, эксплуатация
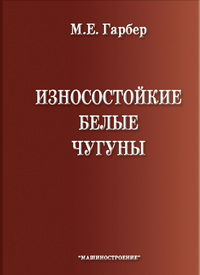
Гарбер М.Е.
Машиностроение, 2010 г.
ИЗНОСОСТОЙКОСТЬ
СТРУКТУРА и износостойкость В НЕЙТРАЛЬНЫХ АБРАЗИВНЫХ СРЕДАХ
Изучение износостойких белых чугунов проводилось на стенде, где образцы изнашиваются, вращаясь по кругу в резервуаре, заполненном смесью песка и воды. Присутствие воды в абразивной массе вызывает коррозионное воздействие на образцы. Однако высокая абразивность остроугольных зерен песка и сравнительно слабое коррозионное воздействие водопроводной воды позволили изучать износостойкость сплавов в нейтральной абразивной среде.
В белых чугунах, специально предназначенных для изготовления износостойких отливок, содержится 2,5—3,6 % углерода. Во избежание графитообразования содержание кремния не должно превышать 1,0 %, для большего подавления образования в структуре графита вводят карбидообразуюшие легирующие элементы (чаше всего — хром).
Структура белых перлитных чугунов состоит из карбидов и перлита. При введении в состав белых чугунов определенных легирующих элементов (Ni, Mo, Мп) перлитное превращение аустенита подавляется. После охлаждения аустенит в этих легированных чугунах частично превращается в мартенсит, а частично сохраняется в структуре. Такие структуры образуют основу мартенситных чугунов [27, 28, 87, 88].
Влияние легирующих элементов на свойства белых чугунов весьма велико. Легирующие элементы в значительной мере определяют тип карбидов и металлическую основу белых чугунов.
Свойства сплавов Fe—Сr—С обусловливаются двумя важными особенностями хрома как легирующего элемента — ограничением у-области и образованием карбидов.
Высокое сродство хрома к углероду обусловливает образование в структуре хромистых сталей не только карбидов цементитного типа, но и более устойчивых специальных карбидов хрома. При относительно малых содержаниях хрома в сталях образуется карбид железа — цементит (Fe3C), в котором может быть растворено до 18—20 % Сr. В высокохромистых сплавах образуются специальные карбиды хрома (Сr, Fe)7C3 и (Сr, Fe)4C. Тригональный карбид хрома (Сr, Fe)7C3 растворяет от 30 до 50 %, а кубический карбид (Сr, Fe)4C — до 35 % Fe.
Из диаграммы системы Fe—Сr—С видно, что чем больше в сплаве углерода, тем при более высоких концентрациях хрома образуются карбиды (Cr, Fe)7C3 и (Cr, Fe)4C. Чтобы исключить образование карбида цементитного типа (Fe, Сr)3С при содержании менее 1 % С достаточно 5—6 % Сr, а при 2 % С нужно не менее 17—18 % Сr.
Влияние хрома на превращения в сплавах Fe—Сr—С видно из псевдобинарных диаграмм состояния Fe—С при 5, 13, 25 % Сr.
В связи с уменьшением растворимости углерода в аустените под влиянием легирования хромом линия предельной растворимости карбидов в аустените, а вместе с ней эвтектоидная точка сдвигаются влево, в сторону меньших концентраций углерода, у-область в сталях под влиянием хрома сужается, но поскольку углерод, образуя карбиды, выводит хром из твердого раствора, для полного исключения аустенита в структуре сплава Fe—Сr—С требуется тем больше хрома, чем больше углерода в сплаве. Так, полное исчезновение у-области в стали с 1 % С происходит при содержании хрома, превышающем 30 %, тогда как в безуглеродистых сплавах Fe—Сг достаточно 12 % Сr, чтобы получить чисто ферритную структуру. С увеличением содержания хрома эвтектическая точка сдвигается влево.
В табл. 2.1 приводится состав ряда белых износостойких чугунов разных марок, применяемых в России и за рубежом, и некоторых сталей и чугунов, износостойкость которых изучалась.
Эти чугуны могут быть разделены на несколько групп:
а)чугуны с карбидами Л/3С подразделяются на перлитные и мартенситные;
б) чугуны с карбидами Л/7С3, М4С и типа VC — на ферритные, аустенитные, мартенситные.
Перлитные чугуны с карбидами М3С. Наличие в структуре чугунов карбидов делает их более износостойкими, чем конструкционные стали. Сравнительно мягкая перлитная металлическая основа и цементит делают эти сплавы наименее износостойкими из всех белых чугунов.
Мартенситные чугуны с карбидами М3С. К материалам с более высокими характеристиками износостойкости, чем у белого перлитного чугуна, относится нихард (3—5 % Ni, 1,5—2,5 % Сr), в 1,5—2,5 раза более износостойкий, чем белый перлитный чугун.
В литом состоянии нихард имеет мартенситную матрицу с участками остаточного аустенита или бейнита и сложные доэвтектические и эвтектические карбиды железа и хрома. Мартенситная структура матрицы литого нихарда обусловлена наличием никеля и хрома. Однако низкая температура конца мартенситного превращения приводит к тому, что в микроструктуре металлической основы наряду с мартенситом имеется остаточный аустенит.
В табл. 2.2 приведены составы наиболее распространенных чугунов "нихарда". Состав сплава выбирается в зависимости от назначения детали и условий ее работы. Так, для работы в условиях интенсивного абразивного износа, где ударные нагрузки невелики, применяется высокоуглеродистый чугун нихард-1.
Чугун с низким содержанием углерода нихард-2 характеризуется меньшей износостойкостью, но более прочен, чем высокоуглеродистый нихард-1 [43].
Для получения мартенситной структуры в деталях с массивными сечениями необходимо повысить содержание никеля, при этом возрастает опасность появления в структуре графита. Поэтому для отливок применяют одну из разновидностей нихарда — сплав 3-2-1 [85], отличающийся более низким содержанием никеля (1,5—3,25 %) и наличием 0.4-1.1 % Мо. Этот сплав по сравнению с другими распространенными никельхромовыми белыми чугунами обладает более высокой износостойкостью, лучшими механическими и эксплуатационными свойствами. Молибден так же, как и никель, подавляет образование перлита при охлаждении в форме, но в отличие от никеля не является графитизатором. Уменьшение содержания никеля снижает склонность к образованию графита в толстостенных деталях и, кроме того, повышает износостойкость остаточного аустенита, который при износе превращается в более твердый и, следовательно, более износостойкий мартенсит.
Был создан сплав, в котором в целях экономии никеля часть его заменена медью. Комбинация из 1,5 % Сu, 3,5 % Ni и 2 % Сr обеспечивает свойства, близкие свойствам стандартных составов нихарда: 4 % Ni и 2 % Сr [126]. Однако в [43] указывается, что применение нихарда с медью вызывает осложнение в производстве, так как возможно появление неоднородности в структуре, а также опасности увеличения содержания меди в возврате.
Для нихарда рекомендуется сравнительно низкое содержание кремния (0,3—0,5 %), что вызвано влиянием на устойчивость аустенита — кремний сдвигает С-образные кривые влево в области перлитного превращения [43]. В тонкостенных отливках желательно повышать содержание кремния до 0,75 %, если при этом не образуется свободный графит. Содержание марганца стремятся поддерживать на относительно низком уровне (0,3—0,7 %), так как марганец вызывает образование очень устойчивого аустенита, который трудно превращается в мартенсит и бейнит при термической обработке и в процессе изнашивания, что снижает стойкость деталей.
Количество серы и фосфора в чугунах должно быть минимальным. При содержании фосфора более 0,25 % повышается хрупкость. Сера также способствует понижению прочности отливок. Никель — основной элемент в нихарде. Он определяет твердость и прочность матрицы. Недостаточное содержание никеля приводит к образованию низкотемпературных продуктов распада аустенита—троостита или даже перлита, что резко снижает износостойкость сплава. Чрезмерное содержание никеля способствует появлению остаточного аустенита, также понижающего износостойкость.
Хром в нихарде выполняет три функции. Во-первых, стабилизирует карбид и подавляет графитизацию. Никель является графитизатором в нихарде, поэтому необходимо соблюдать соотношение никельхром. Во-вторых, хром способствует повышению твердости карбидов и, в-третьих, способствует стабилизации аустенита [47].
Белые чугуны с карбидами М7С3 и М4С. Увеличение в белых чугунах содержания хрома выше 10 % приводит к образованию в их структуре первичного карбида три тонального типа, имеющего формулу (Сr, Fe)7C3.
При кристаллизации аустенитной хромистокарбидной эвтектики карбиды типа M7С3 в отличие от ледебурита с карбидами типа Л/3С не образуют непрерывную фазу, а располагаются в виде изолированных тригональных карбидов в аустенитной основе.
Карбиды типа М7С3 более тверды и дисперсны, чем карбиды M3С, что обеспечивает чугунам с карбидами первого типа более высокие износостойкость и прочность. Микротвердость карбидов (Сг, Fe)7C3 составляет 1200—1500 Нц, что значительно превышает микротвердость кварца (-1000 Нц), тогда как твердость карбидов цементного типа Fe3C или (Fe, Сr)3С близка к микротвердости кварца и составляет 800—1100 Нц. Отсюда становится объяснимой высокая износостойкость высокохромистых чугунов в условиях эксплуатации.
Как правило, применяют доэвтектические и эвтектические чугуны, так как в заэвтектических чугунах при кристаллизации образуются крупные иглообразные карбиды, снижающие износостойкость и, особенно, прочность отливок. Поэтому необходимо так подбирать химический состав сплава, чтобы он не был заэвтектическим. При содержании в чугунах 12—18 % Сr сплавы, содержащие более 3,6 % С, становятся заэвтектическими .
При содержании хрома в пределах 25—30 % и около 2,7 % С подавление перлитного превращения обеспечивается без добавки других легирующих элементов только в тонкостенных отливках.
При содержании в чугуне около 34 % Сг и 1,5—2,2 % С металлическая основа состоит из феррита, что приводит к сравнительно низкой износостойкости этого сплава в абразивных средах. Этот сплав обладает хорошей коррозионной стойкостью в окислительных средах (азотная, крепкая серная, уксусная, фосфорная, органические кислоты) и в щелочах, растворах солей, морской воде, обычной атмосфере и в сернистых газах. Высокохромистый чугун не стоек в соляной кислоте и в разбавленной серной. Этот чугун обладает хорошей жаростойкостью при r < 1200 °С [42].
Ванадиевые чугуны с карбидами типа VC. В этих чугунах форма сечения карбидов близка к шаровидной. В зависимости от содержания марганца и других элементов, а также от термической обработки структура их металлической основы может быть аустенитной, ферритной или мартенситной. Эти чугуны обладают сравнительно хорошей износостойкостью, однако при аустенитной или ферритной матрице главным их преимуществом является относительно высокая для износостойких чугунов пластичность. Детали из чугуна с аустенитной структурой подвергаются нагреву до 1100 °С и охлаждению на воздухе.
Сравнительное исследование износостойкости белых чугунов. Данные различных авторов об износостойкости белых чугунов разных марок противоречивы. Например, в работах [85, 86] указывается, что износостойкость чугуна "клаймэкс аллой-42" в два-три раза выше, чем чугуна нихард. Из этих же работ можно сделать вывод, что износостойкость чугуна с 27 % Сr выше, чем износостойкость ни-харда. В РТМ 28—61 приводятся данные лабораторных испытаний на износ, показывающие, что износостойкость нихарда в 3,7 раза выше, чем стойкость высокохромистых чугунов ИЧХ28Н2 и ИЧХ15М2 (состав последнего аналогичен чугуну "клаймэкс аллой-42").
Если данные РТМ 28—61 (по-видимому, изданные в 1961 г.) о высокой износостойкости чугуна "нихард" можно объяснить недостаточным опытом исследования нихарда в СССР, то странным выглядит утверждение изданной в 2005 г. работы Е.И. Маруковича и М.И. Карпенко [78] о том, что в особо жестких условиях наибольшей износостойкостью, в том числе и против эрозии, отличаются мартенситные чугуны типа нихард (Заметим, в [78] приводится много рисунков из работ М.Е. Гарбера, Е.В. Рожковой и др. без ссылки на авторов).