Использование железа прямого восстановления при выплавке стали
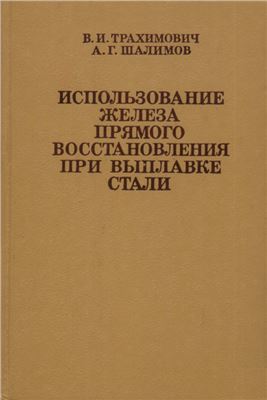
Трахимович В.И., Шалимов А.Г.
Металлургия, 1982 г.
ИНДУКЦИОННАЯ ПЛАВКА
В последнее время за рубежом вновь возрос интерес к индукционным печам как к возможным агрегатам получения слитков, особенно с использованием в качестве шихты металлизованных окатышей.
Применение печей этого типа в сталеплавильных цехах ограничивается во всем мире целями получения сплавов или лигатур, в связи с чем емкость их, как правило, не превышает 5 т.
В литейных цехах, напротив, работают крупные печи. Самая крупная установка в мире включает в себя 4 печи емкостью по 60 т и мощностью по 20 кВт с общей производительностью 160 т/ч. Используемый лом подогревается до 600 °С.
По целому ряду важнейших параметров печи этого типа предпочтительнее дуговых электропечей. В связи с этим возникают вопросы относительно возможных граничных условий применения их в сталеплавильном производстве. Имеющаяся практика свидетельствует о том, что допустимое напряжение может составлять 3000 В и сила тока 70 000 А. Таким образом, кажущаяся мощность может быть в перспективе повышена до 210 МВА. Индуцированная действительная мощность, зависящая от толщины стен тигля, относится к кажущейся мощности как 1:5-1:7.
Движение металла в индукционной печи, являющееся в целом весьма положительным с металлургических позиций фактором, при чрезмерной удельной мощности может быть, однако, сопряжено с выбросами металла. По этому показателю удельная мощность крупных печей ограничивается пока что величиной 330 кВт/т металла.
На мощность индукционных печей может существенно повлиять толщина футеровки тигля. Футеровка должна быть достаточно надежной и долговечной. Однако по мере увеличения ее толщины снижается полезная мощность печи, к примеру, для печи емкостью 100 т при кажущейся мощности 210 МВ-А она снижается до 38 МВт при толщине стен 15 см и до 28 МВт при толщине стен 40 см. Выбор материала стен также на сегодня является большой проблемой. Кислая футеровка выдерживает большое число плавок, что позволяет иметь расход огнеупоров 0,7 кг/т стали при температуре выпуска стали 1550 С. Однако такая футеровка годится далеко не для всех случаев и, как правило, не приемлема для выплавки стали из обычного лома из-за невозможности удалить из металла серу и фосфор в этом случае. К тому же углерод и марганец металла будут вступать во взаимодействие с кремнеземом футеровки, что может привести к последствиям, влияние которых необходимо ограничивать.
Удаление таких примесей, как кремний, сера, марганец, из металла можно в известной мере обеспечить вдуванием соответствующих порошкообразных материалов без чрезмерного износа футеровки. Можно также обеспечить и кипение металла с известным понижением мощности в этот период во избежание выбросов.
С позиций усвоения легирующих, расплавления легковесной шихты, удаления газов из металла и снижения его газонасыщенности индукционные печи обладают несомненными преимуществами перед дуговыми. Наряду с этим индукционные печи по принципу работы являются по существу агрегатами непрерывного действия и поэтому могут быть более пригодными для передела металлизованной шихты. Важно и то, что работа индукционных печей не сопровождается такими значительными колебаниями электрических параметров, как работа дуговых печей.
Капитальные и эксплуатационные затраты на производство стали в индукционных и дуговых печах близки между собой. Но при организации непрерывного процесса плавки можно ожидать снижения затрат в случае использования индукционных печей вследствие упрощения конструкции зданий и газоочистки, устранения затрат на борьбу с шумом, меньших затрат на обслуживающий персонал и огнеупоры, более гибкого регулирования температуры и химического состава стали.
Использование индукционных печей для переплава металлизованных окатышей имеет ряд дополнительных преимуществ.
Вследствие интенсивного движения металла в индукционной печи металлизованные окатыши могут быстро увлекаться в глубь ванны, что предохранит их от окисления в процессе плавления. К тому же само плавление происходит без перегрева окатышей, что обеспечивает минимальный угар железа и выделение пыли из печи.
При заданной подводимой мощности к печи температура металла легко регулируется скоростью подачи окатышей.
Могут быть сокращены капитальные затраты, поскольку установка может иметь два тигля, один из которых находится в ремонте, другой в работе. В этом случае достигается высокая степень использования установленной мощности.
Малое время- соприкосновения окатышей с атмосферой, а также отсутствие зон высоких температур»как это имеет место под электрическими дугами в дуговой печи, позволят получать очень низкие содержания азота в металле — на уровне их содержаний в металле, выплавленном в кислородных конверторах.
Что касается металлургических процессов в индукционной печи при переплаве металлизованных окатышей, то они по существу сводятся к двум процессам: удалению фосфора и удалению углерода с одновременным довосстановлением содержащихся в окатышах окислов железа. Содержание серы в окатышах при газовом восстановлении может быть получено на низком уровне.
На ряде индукционных установок в ФРГ емкостью от нескольких десятков килограммов до двух тонн были проведены достаточно разносторонние эксперименты по переплаву металлизованных окатышей, которые позволили выявить многие особенности этого процесса, его преимущества и недостатки, а также в известной мере определить перспективы на будущее.
Скорость нагрева губчатого железа в индукционной тигельной печи джоулевым теплом зависит как от параметров самого губчатого железа, так и печи. При проведении сравнительных экспериментов в двух печах мощностью 54 и 30 кВт с частотой тока соответственно 250 и 2000 Ги при массе плавки от 4 до 22 кг, с использованием губчатого железа пяти сортов с колебаниями размеров кусков от 2-16 до 6-40 мм, насыпной ачотности от 1,01 до 2,52 г/см3 и степени металлизации от 83,9 до 99,2 были установлены следующие основные закономерности [227]. Величина индуктируемой в садке мощности и скорость нагрева губчатого железа возрастали с увеличением частоты тока и мощности печи, а также величины кусков губчатого железа, степени его металлизации и насыпной плотности. Однако при наличии выявленной технической возможности расплавления губчатого железа в индукционной печи в отсутствие какого-то количества предварительно расплавленного металла, так называемого "болота", была установлена нецелесообразность такого процесса. Губчатое железо начинало плавиться на дне тигля, а находившийся выше слой губчатого железа вниз не сходил и спекался настолько прочно, что дальнейшая загрузка губчатого железа оказывалась невозможной. Попытки расплавить этот слой могут привести к перегреву уже расплавленною металла и прогару тигля. Чтобы получить необходимую для плавления высокую индуктируемую мощность, необходимы высокочастотные установки, которые значительно более дороги и к тому же металл в них очень слабо перемешивается. Наконец, необходимый нагрев губчатого железа достигался при очень высоком расходе электроэнергии, т.е. при значительно более низком к.п.д. печи, чем при плавлении скрапа.
Дальнейшие опыты с высокочастотной печью (2000 Гц) емкостью 120 кг подтвердили неперспективность использования печей такого типа для плавления губчатого железа. Даже при загрузке губчатого железа на чистую поверхность предварительно расплавленного металла окатыши быстро расплавлялись только в начальный период их загрузки, не увлекаясь при этом в глубь ванны. В дальнейшем начинал образовываться шлак, поверхность которого вследствие излучения и охлаждающего эффекта губчатого железа покрывалась коркой, что препятствовало поступлению свежих порций губчатого железа в металлическую ванну.
Гораздо более обнадеживающими были эксперименты, проведенные в низкочастотной печи (150 Гц) емкостью 1,5 т, в ходе которых переплавлялось губчатое железо со степенью металлизации от 87,6 до 97,0 с крупностью кусков 6-40 мм. Каждую плавку начинали при наличии в печи около 1 т расплавленного металла и дополнительно загружали около 300 кг губчатого железа, после расплавления выпускали около 250 кг металла и скачивали шлак. При этом расход электроэнергии в случае выплавки стали с 0,5 % С составил в среднем 2617 МДж/т и в случае выплавки стали с 1,8 % 2318 МДж/т. На каждый 1 % снижения степени металлизации расход электроэнергии увеличивался на 36 МДж на 1 т выплавленною металла. Длительность плавления каждой порции губчатого железа составляла 16 мин, при этом температура ванны вследствие недостаточности подводимой мощности снижалась на 90 °С. Таким образом, производительность плавления определялась не скоростью плавления, а подводимой мощностью. Поскольку пустая порода губчатого железа имела кислый характер (2,5 % Si02; 0,1 % СаО и 0,2 7с А1203), то износ основной футеровки тигля был довольно значительным, увеличивался сверху вниз и достигал 15 % от начальной толщины, составляющей 13 см. Доля восстановленных окислов железа за время плавки составляла около 65 %. В тех случаях, когда шлак не раскислялся кремнием и марганцем, он был пористым и быстро охлаждался с поверхности, что вынуждало прекращать загрузку губчатого железа для скачивания шлака, если степень металлизации губчатого железа не превышала 90 %.
На специально построенной на заводе в Оберхаузене индукционной печи промышленной частоты емкостью 2 т и установленной мощностью 750 кВт [154] было проведено изучение взаимодействия шлака и огнеупорной футеровки тигля, а также реакций на границах раздела фаз губчатое железо - расплав и расплав - шлак. Толщина кладки стен составляла в начале кампании 100 мм и допускалось ее снижение до 40 мм. Использовалось губчатое железо, полученное на установке Пурофер с различным содержанием углерода и пустой породы, а также степени восстановления (табл. 27).
При переплаве железа марки Л с низким содержанием фосфора и кислой пустой породой можно было работать на кислых шлаках и кварцевой футеровке тигля. При этом насыщенный шлак содержал около 82 % SiO2; 10 % FeO и 8 % Al2O3. Износа нижней части тигля не наблюдали, но верхняя его часть изнашивалась довольно быстро, ко не за счет химического взаимодействия со шлаком, а в результате попадания на стенки окисленных капель металла и образования при этом легкоплавких силикатов. Устранено это явление может быть путем изготовления этой части: тигля из глинозема.
При переплаве губчатого железа марки В основность шлака составляла около 1,5 и количество его не превышало 100 кг/т. Такой шлак разъедал футеровку из плавленого или обожженного магнезита тигель из материала, содержащего 80 % MgO и 20 % Сr2O3, стоял в течение трех недель при трехсменной работе.
При изучении металлургических процессов при переплаве губчатого железа было отмечено два важных обстоятельства.
1. При выбранных электрических параметрах печи металл в ней интенсивно перемешивался и губчатое железо быстро увлекалось в глубь ванны. Благодаря этому, а также наличию кислорода и углерода в самом губчатом железе реакция обезуглероживания получала большое развитие и протекала с высокими скоростями, несмотря на неблагоприятное соотношение поверхности ванны к ее объему в индукционной печи по сравнению с дуговой печью. В экспериментах скорость обезуглероживания достигала 1 кг/(м2-мин) и предположительно может быть повышена. Благодаря этому скорость расплавления губчатого железа в индукционной печи емкостью 100 т может достигать 50 т/ч.
2. Температура шлака в индукционной печи не может превышать температуру металла и поскольку к тому же фосфор в губчатом железе находится в пустой породе, то существенно облегчаются возможности получения низкого содержания фосфора в металле. Для стали, выплавленной из губчатого железа марки В, типичным был следующий химический состав, %: С -0,1; Мn -0,04; Р -0,011; S -0,005 и N2 -0,0015. Эти эксперименты показали, что в случае периодической загрузки губчатого железа при правильном Выборе геометрических и электрических параметров печи особых -технических трудностей в процессе его переплава не возникает, однако стоимость плавления, отнесенная к выходу годного металла, выше, чем при плавлении скрапа, увеличивается расход электроэнергии и раскислителей, выше износ футеровки, большие потери времени на скачивание шлака. Поэтому переплав губчатого железа в индукционной Кечи может быть экономически целесообразен, если стоимость его будет меньше стоимости скрапа или возможно будет найти источники компенсации этих потерь (большая однородность и чистота губчатого железа, удобство его загрузки и транспортировки и т.д.).
Особенно большие преимущества могут быть получены при обеспечении непрерывной загрузки и выпуска металла. В этом случае в принципе возможны резкое сокращение ручных операций, достижение высокой степени автоматизации процесса, работа при полном тигле на максимальной мощности при соответствии подводимой и потребляемой электрической мощности и обеспечении стационарного процесса плавления, температуры и химического состава металла.