Гидродинамическая подача смазки
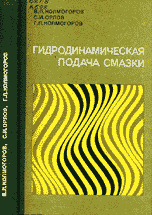
Колмогоров В. Л., Орлов С. И., Колмогоров Г. Л.
Металлургия, 1975 г.
ПРАКТИКА ВОЛОЧЕНИЯ В РЕЖИМЕ ГИДРОДИНАМИЧЕСКОГО ТРЕНИЯ
В настоящее время в практике обработки металловдавлением накоплен значительный опыт использования гидродинамического эффекта технологической смазки для интенсификации производства. Правда, этот опыт относится в основном к волочению проволоки, прутков и труб.
Знакомство с практическими результатами, по замыслу авторов, позволит расширить область применения гидродинамической подачи смазки в очаг деформации на те области волочения, где еще не перешли на жидкостное трение. Читателя, занимающегося другими процессами обработки металлов давлением, рассмотрение материалов этой главы может подтолкнуть к разработке аналогичной технологии для прокатки, штамповки, вытяжки и т. п.
1. ИНСТРУМЕНТ ДЛЯ ВОЛОЧЕНИЯ ПРОВОЛОКИ
Разработка новой технологии волочения изделий в режиме гидродинамического трения начата в СССР в конце 50-х годов работниками ВНИИметмаша и НИИ-метиза и активно продолжена затем в УралНИИЧМ. В содружестве с заводскими работниками в 1964 г. были разработаны и затем впервые в мировой практике широко внедрены в производство принципиально новый инструмент и прогрессивная технология волочения с подачей технологической смазки. Основу технологии составляют так называемые сборные волоки.
Существует несколько модификаций инструмента, предназначенных для изготовления продукции различных видов.
Волочению по новому способу подвергается проволока из углеродистой и легированной стали, из цветных металлов и сплавов, катанка с поверхностью, механически очищенной от окалины. Инструмент обеспечивает хорошее качество волочения проволоки с мягкими покрытиями, например биметаллической сталеалюминиевой. Кроме гидродинамической подачи смазки, инструмент дает возможность сохранить низкий уровень остаточных напряжений в готовых изделиях, а также проводить волочение с противонатяжением.
В некоторых случаях при новой технологии можно отказаться от нанесения технологических подсмазочных слоев, а также получить эксплуатационные покрытия увеличенной толщины и более равномерные по длине бухты.
Разработанный в СССР способ волочения может быть приспособлен к использованию любой смазки. Предпочтение отдается дешевым и легко удаляемым смазкам. Исследования показали, что при волочении изделий по новой технологии толщина пленки смазки на проволоке возрастает сравнительно немного, и это небольшое утолщение смазочной пленки имеет значительные преимущества.
Внедрение новой технологии волочения дало следующие результаты: увеличение производительности волочильных станов без их реконструкции достигает 30%; износостойкость инструмента — волок возрастает в три-четыре раза; расход электроэнергии на волочение уменьшается на 11—120%; единичные обжатия металла повышаются до 40—45%. Из-за меньшей обрывности проволоки при волочении и сокращении промежуточных термообработок удельный расход металла снижается на несколько килограммов на 1 т продукции. Упрощается, а в некоторых случаях совершенно не производится подготовка поверхности изделий перед волочением. Улучшается качество изделий.
При новом способе волочения вследствие меньшего разогрева изделий и инструмента и многократного повышения стойкости волок скорость волочения без ущерба для качества продукции увеличивается до предельно возможных значений (в условиях СССР иногда в 1,5— 2 раза). Это обеспечивает соответствующий рост (производительности волочильных станов.
Внедрение прогрессивной технологии золочения на предприятиях Советского Союза дало удельный экономический эффект до 25 руб. на 1 т проволоки из легированной стали.
Основу технологии составляет, как уже отмечалось, сборная волока. Одна из первых модификаций сборной волоки показана на рис. 6. Сборные волоки внешне отличаются от обычных только габаритами, имея несколько больший диаметр и высоту.
Преимущества сборных волок в сравнении с известными конструкциями инструмента для волочения с гидродинамической подачей смазки состоят в следующем:
1. Исключена горячая запрессовка твердосплавной рабочей волоки в обойму. Сборка волок осуществляется с натягом, обеспечиваемым холодной запрессовкой зажимной конической втулки с волоками в корпус сборной волоки. Сильное радиальное сжатие твердосплавных волок в стальном корпусе исключает их растрескивание в процессе работы и позволяет в ряде случаев уменьшить габариты твердосплавных заготовок. Это обстоятельство само по себе обеспечивает экономию твердого сплава.
2. Между напорной и рабочей волоками достигнута довольно высокая герметичность за счет специальных уплотнительных элементов и сильного осевого сжатия волок при их запрессовке в стальном корпусе.
3. Обеспечена хорошая соосность в результате применения шлифованных по наружному диаметру напорной и рабочей волок и радиального сжатия их в одной цилиндрической поверхности зажимной втулки. Соосное направление проволоки в рабочую волоку обеспечивает равномерный износ последней.
4. Нагнетающая волока, выполняющая роль насадки, представляет собой обычную отработанную твердосплавную волоку, в силу чего использование такого инструмента практически не приводиткрасширениюеголарка.
5. Стальные детали сборных волок изготовлены из высокопрочных материалов и термообработаны, поэтому они долговечны, что 'позволяет в сотни раз уменьшить потребность в стали, идущей на изготовление обойм, в сравнении с волоками старого типа.
6. Сборная волока не создает никаких осложнений при эксплуатации волочильного стана. Волочильщик получает уже готовый инструмент, установка которого в волокодержатель мыльницы (рис. 8) производится так же, как и обычных волок.
Практикой установлено, что эффективность внедрения сборных волок в значительной степени зависит от точности изготовления их деталей и правильности сборки. Если учесть, что перед рабочей волокой создается очень высокое давление смазки, превышающее порой при волочении труднодеформируемой проволоки 1000 МН/м2 (100 кгс/мм2), то станет очевидным, насколько важны прочность материала инструмента, правильность изготовления и сборки деталей.
Сборные волоки собираются и разбираются только в фильерной мастерской цеха. Комплектовка напорных и рабочих волок в сборных волоках производится согласно технологическим картам.
Применяется следующий порядок сборки нового инструмента: в зажимную втулку 3 (см. рис. 6) вставляется рабочая волока /, уплотнительная шайба 6 и напорная волока 2. Зажимная втулка помещается в коническое отверстие корпуса 4. Сверху кладется упорная шайба 7 и затем производится запрессовка комплекта зажимной втулки в корпус усилием, которое не меньше силы при волочении. При этом обеспечивается надежное радиальное сжатие твердосплавных вкладышей, что исключает их растрескивание в процессе работы. После запрессовки на прессе сборная волока окончательно фиксируется накидной гайкой 5 при помощи ключа с удлиненной рукояткой. Собранный таким образом инструмент хранится на стеллажах по размерам и выдается волочильщику только в обмен на изношенный.
Разделка канала рабочих волок производится в фильерной мастерской цеха в специальном устройстве, состоящем из корпуса с внутренним конусом и зажимной втулки (рис. 9).
В настоящее время назрела необходимость централизованного изготовления деталей сборных волок на специализированных предприятиях, так как многие метизные заводы не имеют для этого нужного обрудования и стоимость изготовления одного комплекта сборной волоки по заводам колеблется в значительных пределах. Стальные детали сборных волок выгодно изготовлять методом горячей штамповки с последующей их чистовой обработкой на специализированном оборудовании. Шлифованные по наружному диаметру твердосплавные вкладыши и корпуса сборных волок должны иметь единые стандартные размеры, которые приведены в табл. 1.
Шлифовать твердосплавные заготовки-волоки по наружному диаметру следует на заводах твердых сплавов.
Совершенствуя технологию волочения проволоки с гидродинамической подачей смазки, сотрудники Урал-НИИЧМ совместно с заводскими работниками создали новые модификации инструмента, работа с которыми аналогична работе с описанным выше инструментом. Новые модификации просты по конструкции и удобны для работы. Их внедрение в производство не связано с капитальными затратами и простоями оборудования, они обеспечивают лучшее нагнетание смазки в очаг деформации, более надежное уплотнение, в несколько раз более высокую стойкость рабочих волок, а также при необходимости снятие остаточных напряжений в изделиях непосредственно в процессе деформации металла.
2. ЭФФЕКТИВНОСТЬ ПРИМЕНЕНИЯ СБОРНЫХ ВОЛОК ПРИ ВОЛОЧЕНИИ ПРОВОЛОКИ
Результаты исследований и частичного внедрения гидродинамической подачи смазки при волочении проволоки, в основном из низкоуглеродистых сталей, довольно подробно изложены в книге «Волочение в режиме жидкостного трения» (см. предисловие). Здесь мы остановимся на эффективности процесса и результатах массового использования технологии и инструмента различных модификаций при волочении проволоки различных назначений с гидродинамической подачей смазки.
В СССР новая технология применяется преимущественно на станах сухого волочения. Волочение проволоки, как правило, производится на сухом порошке натриевого мыла, которое до известной степени является универсальной смазкой. Натриевое мыло имеет относительно высокую температуруплавления и прочность, достаточно «липко» при высокой температуре и легко растворяется в воде. Однако оно поглощает воду из окружающей атмосферы, что ухудшает его смазочные свойства.
В табл. 2 показаны физико-химические свойства ряда образцов заводских натриевых порошков ч стружек (по данным Уфимского авиационного института). Влажность мыльного порошка в состоянии поставки достигает 12%.