Газы и углерод в металлах
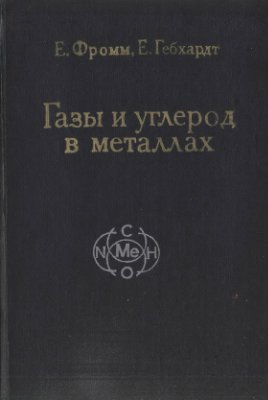
Фромм Е., Гебхардт Е.
Металлургия, 1980 г.
ДЕГАЗАЦИЯ СТАЛИ
Из экономических соображений плавку и рафинирование обычных металлов, сплавов и сталей проводят раздельно. Разделение процесса на два этапа позволило разработать более эффективные вакуумные установки для дегазации и рафинирования, благодаря чему значительно снизились общие капитальные затраты.
Первые предложения по вакуумированию были сделаны еще X. Бессемером в середине прошлого столетия. Впоследствии были изобретены новые способы [9]. Лишь в пятидесятых годах настоящего столетия вакуумирование нашло широкое промышленное применение с появлением производительных вакуумных насосов, работавших без повреждений в тяжелых условиях металлургического завода. Обычные механические насосы не могли откачивать сильно запыленные атмосферы, состоявшие в основном из продуктов испарения летучих компонентов, и лишь с развитием пароструйных насосов эта проблема была решена [9].
Все методы дегазации стали, которые можно разделить на 4 группы, направлены на снижение содержания водорода, азота и кислорода в жидкой стали. В процессе дегазации заметно снижалось содержание водорода; удаление азота и кислорода на разных установках было различным. Содержание кислорода можно значительно снизить, если раскислять металл углеродом с образованием оксида углерода. Добавки раскислителей и легирующие вводят после раскисления углеродом.
1. ДЕГАЗАЦИЯ В КОВШЕ
В самом простом случае разливочный ковш помещают в вакуумную камеру, к которой присоединены вакуумные насосы (рис. 104). В таких установках, впервые примененными А. М. Самариным с сотрудниками [10] в СССР, уже в начала откачки начинается энергичное выделение газа, приводящее к кипению металла. Через несколько минут кипение прекращается и давление понижается до нескольких миллиметров ртутного столба. Обработка 30-т ковша длится 10—20 мин. Для интенсификации рафинирования и увеличения массы обрабатываемого металла во время дегазации необходимо ускорять движение ванны. Это осуществляется различными способами, один из них — введение в металл аргона. Другой состоит в том, что ковш устанавливают в индуктор и для перемешивания хметалла подают ток низкой частоты — от 0,5 до 1 Гц. В этом случае корпус ковша должен быть изготовлен из немагнитной стали. Третий способ предусматривает установку в крышке камеры трех электродов для нагрева стали электрическими дугами (процессы Финкл-Моор и А5ЕА-5КР). При этом усиливается циркуляция металла и происходит дополнительный нагрев.
2. ДЕГАЗАЦИЯ СТРУИ
По способу фирмы «Бохум Ферайн» разливочный ковш ставят на вакуумную камеру, откачанную до давления 0,5— 10 мм рт. ст., открывают стопор ковша и струя металла направляется в ковш, стоящий в камере (рис. 105,а). Вся дегазация протекает практически во время свободного падения капель. Вследствие развитой поверхности капель выделение газов получает большое развитие, снижается содержание водорода, азота и кислорода, несмотря на короткое время обработки. При такой обработке стали значительно снижается температура расплавленного металла. По другому варианту (рис. 105,6) металл из печи непосредственно сливается в откачанный разливочный ковш. В этом случае падение температуры при скоростях разливки около 10 т/мин составляет около 50°С.
3. ДЕГАЗАЦИЯ В ИЗЛОЖНИЦЕ
На дегазацию струи металла или дегазацию при переливе из ковша в ковш очень похож способ дегазации в изложнице, при котором выделение газа происходит во время и после заливки металла в изложницу вплоть до затвердевания в ней. В этом случае в откачиваемую камеру либо помещают вместо второго разливочного ковша изложницу (рис. 106,а), либо накрывают ее специальной крышкой с вакуумной откачкой (рис. 106,6). Во время разливки стали изложницу герметизируют и подключают к вакуумному насосу.
4. ДЕГАЗАЦИЯ ПРИ ПОРЦИОННОМ ВАКУУМИРОВАНИИ
При такой дегазации лишь часть расплава находится некоторое время в вакууме и затем возвращается в ковш. Цикл периодически повторяется несколько раз. Способ ДН был разработан фирмой «Дортмунд Хёрдер Хюттенунион», его широко используют на многочисленных заводах для вакуумирования масс жидкого металла от 10 до 400 т. Рукав вакуумной камеры опускают в открытый разливочный ковш (рис. 107,а). В результате откачки металл поднимается в камеру, где из него выделяется газ. Далее вакуумная камера поднимается (рис. 107,6) так, что расплав вытекает из нее и рукав остается заполненным до высоты 1,4 м над уровнем металла в ковше. Это уравновешивает атмосферное давление. При последующем опускании камера снова наполняется свежим расплавом, при подъеме освобождается. Этот цикл периодически повторяется, причем подъемы давления газовой фазы в камере после вакуумирования отдельных порций обычно становятся ниже (рис. 107,в), что свидетельствует о все меньшем выделении газа. Для уменьшения тепловых потерь вакуумную камеру в большинстве случаев обогревают. Дегазация может по необходимости сопровождаться добавкой раскислителей и легирующих.
В КН-процессе, разработанном фирмами «Руршталь АГ» и «Гереус», вакуумирование происходит непрерывно. Вакуумная камера (рис. 108) имеет два рукава, причем в один рукав после погружения в расплав и откачки вакуумной камеры подается аргон. Газ поднимается в металле и увлекает за собой жидкий металл так, что со стороны этого рукава металл поднимается выше чем на 1,4 м по сравнению с зеркалом металла ковша. Из камеры металл вытекает по второму рукаву. При постоянной подаче газа расплав непрерывно циркулирует через вакуумную камеру и непрерывно выделяется газ.
ДЕГАЗАЦИЯ В ТВЕРДОМ СОСТОЯНИИ
Скорости реакций в жидком состоянии при высоких температурах на порядок выше, чем в твердом состоянии, и поэтому дегазацию практически всегда проводят в жидком состоянии. Правда, при обработке в твердом состоянии, например при нагреве или закалке, газы выделяются, причем речь идет о нежелательном или побочном результате используемого процесса [11]. Например, при спекании частиц процесс дегазации не может быть проведен в жидком состоянии. С помощью спекания в вакууме путем нужного управления процессом возможна очистка спекающихся частиц. Так, при спекании тантала и ниобия удаляется водород и азот, а также кислород в виде летучих субоксидов.
Дегазация в твердом состоянии становится необходимой, если после разливки в результате последующих обработок снова возрастает содержание газов. Содержание водорода увеличивается до нежелаемых концентраций после травления или гальванической обработки, особенно в закаливаемых сталях, которые после травления следует специально дегазировать путем вылеживания при 20—250°С. Титан после травления дегазируется в высоком вакууме при 550—800°С. Известна также дегазация деталей для радиоламп и высоковакуумных установок [12].