Газоочистные аппараты и установки в металлургическом производстве
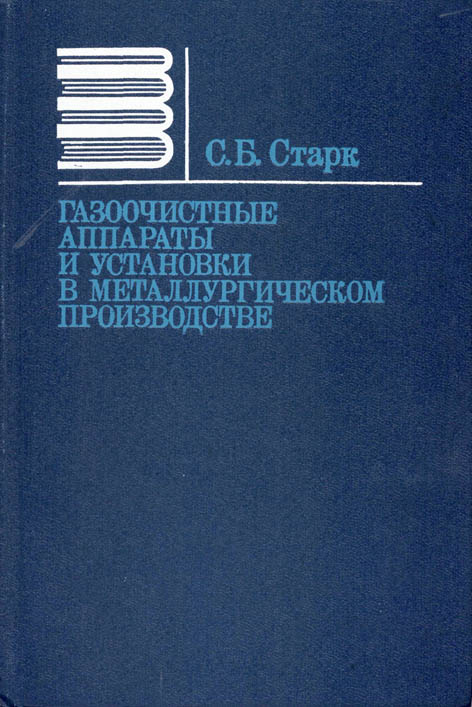
Старк С.Б.
Металлургия, 1990 г.
ОЧИСТКА ГАЗОВ ЭЛЕКТРОСТАЛЕПЛАВИЛЬНЫХ ПЕЧЕЙ
§ 1. Характеристика газопылевыделений
Выход газов из электросталеплавильной печи и состав газовой фазы зависят от состава шихты, скорости плавления, технологического и температурного режимов плавки, режима кислородной продувки и т. п. По ходу плавки состав газов в зависимости от скорости выгорания углерода изменяется в следующих пределах:
Компоненты Содержание, , % (объемн.)
СО СO2 Н2 O2 Ν2
15-25 5-11 0,5-35 3,5-10 61-72
Наличие в газах оксида углерода делает их взрывоопасными, что необходимо принимать во внимание при проектировании систем газоотсоса.
Большое влияние на режим газовыделения оказывает ряд факторов и в первую очередь подсос воздуха в печь, зависящий от внутрипечного давления, качества уплотнения имеющихся зазоров, наличия автоматического регулирования и т. п. Максимальный выход газов может превышать средний на 60—70 % и длиться до 30 мин (табл. 28.1).
Выходящие из печи газы в значительной степени засорены пылью. Мелкодисперсная пыль образуется в результате испарения металла в зоне действия электрических дуг и кислородной продувки и последующей конденсации в печном пространстве. Более крупные фракции дают шлакообразующие и молотые добавки.
Средняя концентрация пыли в газе 15—30 г/м3, что дает удельный выход пыли 6—9 кг/т стали.
Ниже приведены данные, характеризующие дисперсный состав пыли при выплавке среднеуглеродистых и хромистых сталей:
Размер частиц, мкм <0,7 0,7—7 7—80 >80
Содержание, % (по массе) 42 35 16 7
Обработка этих данных показывает, что dm=l,2 мкм при σч=13.
Основным компонентом пыли являются оксиды желез(а, суммарное количество которых составляет: в период расплавления 80 %, в период кипения (при продувке кислородом) 62 % и в период доводки 53 %. В период расплавления в пыли появляются оксиды марганца (11 %), в период доводки — оксиды кальция (6 %) и магния (9 %).
Удельное электрическое сопротивление пыли довольно значительно, при очистке газа в электрофильтрах следует принимать меры для его снижения.
В небольших количествах в газах находятся следующие токсичные микрокомпоненты, мг/м3 (г/т): оксиды азота 550 (270), оксиды серы 5 (1,6), цианиды 60 (28,4), фториды 1,2 (0,56).
Неорганизованные выбросы в цехах достигают 40 % технологических выбросов.
§ 2. Отсос и улавливание выделяющихся газов
В процессе эксплуатации дуговой электросталеплавильной печи осуществляются подъем и опускание электродов, подъем и, поворот свода, наклон ванны и другие операции. Поэтому создание стационарного устройства для отсоса газов представляет значительные конструктивные трудности. Если не принять специальных мер, газы, выделяющиеся в процессе плавки через загрузочные окна, зазоры между электродами и сводом и другие неплотности, поступают непосредственно в помещение цеха, откуда удаляются через фонари здания посредством аэрации. При этом пыль выпадает из медленно поднимающегося потока, оседает на своде печи, оборудовании, конструкциях здания, что снижает светопроницаемость окон и требует создания специальных устройств для уборки. Загазованность и запыленность помещения цеха часто настолько увеличиваются, что в верхней зоне затрудняется видимость для крановшиков, а на рабочей площадке концентрация пыли и газов во много раз превышает санитарные нормы. Пыль и газ выбрасываются через фонари и вытяжные шахты и существенно загрязняют атмосферу. Поэтому с ростом производительности печей и количества образующихся газов, особенно при применении кислородной продувки, такое решение вопроса становится совершенно неприемлемым.
Несколько лучшим решением является отсос газов с помощью зонтов и колпаков. В простейшем случае над печью выше электродов сооружают зонт, не связанный с конструкцией печи, охватывающий все места пыле- и газовыделений и не мешающий обслуживанию печи. Вследствие больших подсосов воздуха температура газов у стен зонта не превышает 100—150°С; зонт может быть сделан из обычной листовой стали толщиной 2—4 мм.
Вместо зонта иногда, делают колпаки, укрепленные на каркасе печи непосредственно у мест пыле- и газовыделения. Такое решение эффективнее, но усложняет конструкцию, так как колпаки перемещаются вместе с печью и требуют шарнирных соединений со стационарным газоходом.
Для эффективной работы отсоса необходимо, чтобы скорость во входном сечении зонта или колпака была не менее 2 м/с, что вызывает большие подсосы воздуха.
Общими недостатками отсоса газов с помощью зонтов и колпаков являются: невысокая эффективность (70—80 %); большой расход энергии на перемещение больших масс газа с присосанным воздухом; значительная металлоемкость; ухудшение условий обслуживания и доступа к печи.
Наиболее целесообразным способом удаления газов из печи является отсос их из рабочего объема через специальное отверстие чаще всего в своде печи вблизи рабочего окна (рис. 28.1, а) Скорость газов в отверстии при отсосе должна быть не менее 20 м/с во избежание отложения пыли. Температура газов в отверстии близка к температуре газов печи.
Другим конструктивным решением вопроса является отсос газов через арку рабочего окна (рис. 28.1, б). В верхней части арки, выполненной несколько удлиненной формы, делают прямоугольное отверстие размером 300X800 мм, над которым с небольшим зазором ( — 20 мм) устанавливают газозаборное устройство Г-образной формы.