Физико-механические испытания металлов, сплавов и неметаллических материалов
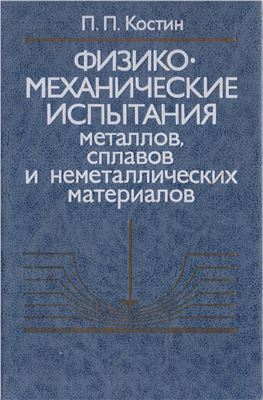
Костин П.П.
Машиностроение, 1990 г.
МЕТОДЫ КАПИЛЛЯРНОГО КОНТРОЛЯ
Классификация методов капиллярного контроля. Капиллярный контроль широко применяют для обнаружения дефектов в деталях из латуни, коррозионно-стойкой стали, алюминиевых, магниевых и титановых сплавов, пластмасс, стекла, пористого бетона и др.
Из многих методов капиллярного контроля наиболее распространены цветной, люминесцентный и люминесцентно-цветной. Они основаны на капиллярных явлениях. Капилляр, выходящий на поверхность объекта контроля только с одной стороны, называют поверхностной несплошностью, а сквозной капилляр, соединяющий противоположные стенки объекта контроля, — сквозной несилошностью. При капиллярном контроле индикаторные жидкости заполняют полости поверхностных и сквозных несплошностей. Образующиеся индикаторные следы регистрируются визуально или с помощью преобразователя. Индикаторный след (рисунок) появляется при нанесении на поверхность детали проявителя, предназначенного для извлечения индикаторной жидкости из полости несплошности. Кроме того, при этом создается фон для лучшей контрастности рисунка.
Индикаторный рисунок и выявляет расположение, форму, длину несплошности.
Капиллярные методы подразделяются по способу выявления индикаторного рисунка.
При цветном методе индикатором служит проникающая жидкость, которая образует индикаторный рисунок на фоне поверхности объекта контроля.
При люминесцентном методе используют проникающие жидкости, способные люминесцировать под воздействием ультрафиолетового излучения на фоне поверхности объекта контроля.
Люминесцентно-цветной метод включает элементы люминесцентного и цветного методов. Проникающая жидкость может люминесцировать в ультрафиолетовых лучах, а также имеет видимую при обычном освещении окраску. Осмотр деталей можно производить как при обычном освещении, так и при ультрафиолетовом излучении.
Подготовка деталей к контролю. Поверхность контролируемой детали и полости несплошностей перед контролем должны быть тщательно очищены. Различные покрытия (гальванические, лакокрасочные и т. д.) снижают эффективность контроля.
Жидкости (бензин, керосин, органические растворители, вода и т. д.), попавшие в полости несплошностей, препятствуют проникновению в них индикаторных жидкостей и тем самым снижают интенсивность окраски или люминесценцию рисунка.
Применяют паровой, механический, химический и электрохимический способы очистки, а также сушку, промывку водой, органическими растворителями и т. д.
При выборе способа подготовки деталей к контролю необходимо учитывать: материал изделия, характер загрязнения, вид покрытия, вид обработки, предшествовавший контролю.
Основные операции капиллярного контроля следующие:
подготовка деталей к контролю;
нанесение на детали проникающей жидкости;
удаление избытка проникающей жидкости с поверхности деталей;
нанесение проявителя;
осмотр деталей;
окончательная очистка деталей (удаление проявителя и следов других дефектоскопических материалов с их поверхности).
По характерным признакам индикаторного рисунка определяют характер дефекта: трещины имеют вид сплошных, иногда прерывистых линий различной конфигурации; межкристаллитная коррозия выявляется в виде пятен, размытых полос; поры — в виде отдельных точек.
Чувствительность методов капиллярного контроля зависит от качества проведения каждой операции контроля, от качества дефектоскопических материалов, освещения, температуры окружающей среды и т. д. Под чувствительностью понимают раскрытие несплошности типа единичной трещины определенной длины, выявленное с заданной вероятностью по заданным геометрическому или оптическому параметрам следа.
Чувствительность люминесцентного метода составляет по ширине несплошности 10 мкм и по глубине 30—40 мкм, цветного — по ширине несплошности 1—2 мкм и по глубине 10— 30 мкм.
Аппаратура для проведения капиллярного контроля. Дефектоскопы бывают переносные, передвижные и стационарные.
Переносное и передвижное оборудование предназначено для контроля деталей в полевых условиях, на ремонтных предприятиях, при необходимости контроля небольших участков без разборки контролируемого узла.
Стационарное оборудование используется при массовом контроле деталей на участках капиллярной дефектоскопии. Транспортировка деталей от одной операции к другой может быть механизирована (люминесцентный дефектоскоп ЛДП-3). Имеются автоматизированные установки для люминесцентной и цветной дефектоскопии, в которых автоматизированы режимы технологических операций контроля деталей, за исключением визуального контроля, проводимого оператором (автоматическая установка УКЛ-1).
В качестве источников ультрафиолетовых излучений применяются газоразрядные ртутные лампы высокого и сверхвысокого давления. Отечественной промышленностью выпускаются лампы типов ДРТ-2, ДРТ-4, ДРТ-5, ДРТ-7, СВД-120А, ДРШ-250, ДРШ-500, ДРШ-1000. Все эти лампы являются источниками ультрафиолетового, видимого и инфракрасного излучения. Для выделения ультрафиолетового излучения применяют светофильтры типов УФС-1, УФС-2, УФС-3, УФС-4, УФС-6, УФС-8.
Разработаны и выпускаются промышленностью лампы для люминесцентной дефектоскопии, не требующие применения светофильтров. Это лампы типов ДРУФ-125 и ДРУФЗ-125.
Так как при капиллярной дефектоскопии используются токсичные материалы и эксплуатируются электроустановки, необходимо строго соблюдать правила техники пожаро- и взрыво-безопасности, а также санитарно-гигиенические правила, обеспечивающие безопасность работающих.