Электропечи для термовакуумных процессов
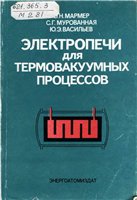
Мармер Э.Н., Мурованная С. Г., Васильев Ю.Э.
Энергоатомиздат, 1991 г.
ТЕРМОВАКУУМНЫЕ ПРОЦЕССЫ И ЭЛЕКТРОПЕЧИ ДЛЯ ТЕРМООБРАБОТКИ, СПЕКАНИЯ, ПАЙКИ И ПЛАВКИ ЧЕРНЫХ МЕТАЛЛОВ
3.1. Отжиг
Развитие вакуумной техники, с одной стороны, и повышение требовании к качеству термической обработки сталей и сплавов, с другой, привели к тому, что за последние годы начали широко использоваться термовакуумные процессы применительно к железу, сталям и сплавам.
Конструкционные, жаропрочные и коррозионностойкие стали и сплавы содержат различные легирующие металлы, в том числе: Сr - до 40%, Мо - до 6%, W- до 18%, V - до 2%, Nb- до 1%, Ti- до 5%, Zr- до 1%, в основном определяющие поведение сталей в вакууме. Свойства этих металлов и их соединений приведены в § 1 5 и 1 7
Взаимодействие газов со сплавами как при атмосферном давлении, так и в вакууме представляет сложный процесс, поскольку на поверхности сплава могут появляться сложные оксидные, нитридные и карбидные фазы.
В [88] указано, что подбором состава окружающей среды можно избежать окисления сталей, легированных Со, Ni, Mo, W, Мn, Сr, Si. Там же показывается что состав защитного газа является вполне определенным для каждой марки стали или для группы сталей со сравнительно узким концентрационным интервалом основных легирующих металлов. Поэтому регулирование состава защитного газа при изменении марки стали может представлять значительные трудности.
Улучшение свойств обрабатываемых изделий, снижение трудоемкости технологического процесса за счет устранения' таких операций, как травление, очистка, промывка, сушка, механическая обработка (полностью или частично), привели к широкому внедрению технологии обработки стали в вакууме. К этим технологическим процессам следует в основном отнести отжиг различного назначения (гомогенизирующий, ^кристаллизационный, для снятия напряжений, дегазационный), отпуск, особенно высокотемпературный. Светлая поверхность изделий может быть получена или сохранена при высокотемпературной обработке путем создания условий, препятствующих образованию оксидов, а также за счет испарения или восстановления оксидов.
Требования к безокислительному нагреву при термообработке в общем неоднозначны. Они зависят от назначения термообрабатываемых изделий, от места данного процесса в общем технологическом Цикле. В одних случаях требуется отсутствие отслаивающейся окалины, в других - отсутствие видимых тонких оксидных пленок (последующее восстановление которых привело бы к дополнительному газоотделению, что, например, для узлов электронных приборов недопустимо). Наличие пленок может препятствовать качественной сварке деталей. В отдельных случаях тонкие видимые оксидные пленки на поверхности изделий допустимы, но они должны равномерно покрывать поверхность, так как от этого зависят коррозионные свойства металлов. Поэтому при внедрении в промышленность термообработки в вакууме или в защитных средах с целью получения светлой поверхности весьма важным фактором является объективная оценка степени окисления поверхности.
Нержавеющие и жаропрочные сплавы. В качестве примера, выявляющего влияние вакуумной термообработки на свойства жаропрочных сталей, авторами было проведено исследование нагрева в вакууме при различных условиях охлаждения сталей: ХН65ВМТЮ, 20X13,15X11МФ [3]. Режимы термообработки и характер полученной поверхности приведены в табл. 3.1. Образцы представляли собой цилиндры диаметром 22, высотой 50 мм с шероховатостью боковой поверхности V 7. Вакуумная термообработка образцов проводилась на установке, состоящей из загрузочной камеры, камер нагрева и охлаждения. Камера нагрева была футерована высокоглиноземистым шамотным кирпичом. На стенках камеры диаметром 100 х 270 мм размещен зигзагообразный нагреватель из сплава Х20Н80 [3].
Было опробовано естественное охлаждение при давлении 1,3-0,13 Па и при давлениях 5 *104 и 9,3 . 104 Па аргона марки А, технического азота сорта I. Отпуск сталей 20X13 и 15X1ШФ производили при 0,13 Па, 700 °С и выдержке 2-3 ч, а стали ХН65ВМТЮ при 800 °С -12 ч.
После термообработки контролировались изменение класса чистоты, наличие оксидной пленки, микроструктура, наличие и глубина дефектного слоя. Определялись при комнатной температуре следующие механические свойства: временное сопротивление разрыву предел текучести, относительное удлинение, относительное сужение, ударная вязкость, твердость, а также исследовалось изменение химического состава послойным химическим анализом и анализом на рентгеновских микроанализаторах.
Для проведения послойного химического анализа с образцов последовательно снимали три слоя толщиной 0,1-0,15 мм, а также бралась стружка из центра образца.
Результаты работы, представленные на рис. 3.2, 33 и в табл. 3.1, Показали, что для исследованных материалов можно сделать следующие выводы:
нагрев в вакууме при давлениях 1-0,1 Па не а поверхности и сохраняет шероховатость V 7;
нагрев при т = 2 ч и охлаждение в вакууме при давлениях 1 и 0,1 Па по режимам 3, 4, 5, 6, 9,13, 17 (см. табл. 3.1) обеспечивают получение светлой поверхности;
после ускоренного охлаждения глубина поверхностного слоя, обедненного легирующими элементами (определенная по микротвердости, металлографическим анализом и микрорентгеноспектральным анализом) , не превышает 50-60 мкм;
отпуск и старение при давлении 0,1 Па не вызывают дополнительного изменения состояния поверхности и образования обедненного слоя;
изменение среднего по слою содержания С, Сr, Mo, W, Ti, А1, определенное послойным химическим анализом, не превышает разброса концентрации по ГОСТ 5632-72 для сталей 20X13,1X1ШФ ХН65ВМТЮ;
охлаждение в нейтральных газах (аргоне марки А по ГОСТ 10157-79, азоте I сорта по ГОСТ 9293-74) при давлениях 5 • 104 и 9,3 • 10* Па аналогично по изменению химического состава охлаждению в вакууме;
термически обработанные в вакууме образцы свидетельствуют, что вакуумная обработка не снижает прочности и повышает пластичность. Особенности поведения сталей при нагреве в вакууме проявляются при нагреве отливок из стали Г13Л, при этом слой, обедненный марганцем, составляет 0,3, а углеродом — 0,25 мм, что в 8—10 раз меньше, чем при обработке на воздухе [3].
Для нержавеющих сталей 1Х18Н9Т и Х17 при высокотемпературном отжиге при давлении 1,3 • 10~2 Па не наблюдалось обезуглероживания. При давлении 13 Па образцы стали Х17, не имеющие оксидной пленки, обезуглероживались при 1350 °С весьма незначительно (с 0,07% До 0,056% по массе). При наличии оксидной пленки за 6 ч содержание Углерода снижается до 0,005%. Показано, что на скорость обезуглероживания оказывает большее влияние толщина окисной пленки, чем содержание углерода в сплаве. Изменение толщины пленки с 4 • 10~3 до 2 • 10~2 мкм увеличивает скорость обезуглероживания в 10 раз по сравнению с изменением содержания углерода (в массовых долях) с 0,1 до 0,06%. Одним из основных условий, определяющих обезуглероживание, является наличие достаточного количества окислителя (СО2, О2, Н2О). Однако содержание С02 + Н2О в печах при нагреве уменьшается и при высокой температуре составляет всего 2—3% [3].
Нагрев стали Х18Н10Т при различных давлениях остаточной среды позволяет оценить ее влияние на состояние поверхности. Так, после отжига при 1000 °С, времени выдержки 15 ч и скорости охлаждения 100 °С. ч в печи с паромасляным диффузионным насосом получены результаты, представленные в табл. 3.2. Показано, что микрорельеф поверхности не изменился при всех режимах отжига, но светлая поверхность наблюдалась только после нагрева в сверхвысоком безмасляном вакууме (10~4—10"6 Па). Повышение давления до 4 • 10~2 Па при разогреве приводило к некоторому потемнению поверхности, что указывало на образование оксидных пленок в процессе нагрева. Эти пленки сохранялись при снижении остаточного давления во время выдержки до 10-2 Па при 1000 °С. Аналогичные результаты были получены и при 10-2-10-3 Па (паромасляные диффузионные насосы).
Масс-спектрометрический анализ остаточных газов в камере показал, что парциальные давления азота и окиси углерода и водорода существенно не изменились в процессе нагрева при давлении 10-5—10-6 Па.
При давлении 10~4 Па, создаваемом путем дросселирования затвором потока из форкамеры, состав остаточных газов заметно изменился. Увеличилось парциальное давление азота и окиси углерода и аргона.