Электронная микроскопия в металловедении: Справочник
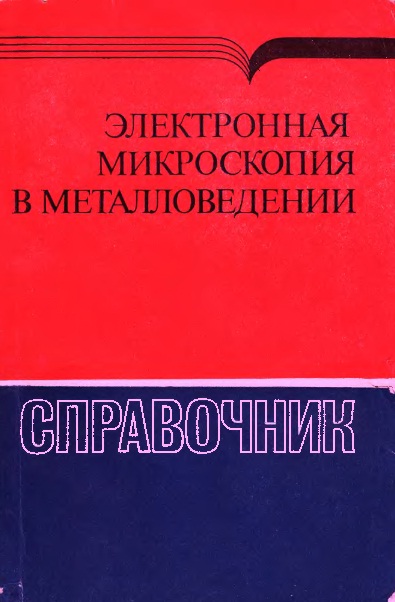
Смирнова А.В., Кокорин Г.А., Полонская С.М.
Металлургия, 1985 г.
МЕТОДЫ ПРИГОТОВЛЕНИЯ ОБЪЕКТОВ ДЛЯ ИССЛЕДОВАНИЯ СТАЛЕЙ И СПЛАВОВ НА ПРОСВЕЧИВАЮЩЕМ ЭЛЕКТРОННОМ МИКРОСКОПЕ (ПЭМ). МИКРОДИФРАКЦИОННЫИ АНАЛИЗ.
Просвечивающая электронная микроскопия (ПЭМ) обладает высокой разрешающей способностью (в 1000 раз выше, чем световая). Однако в отличие от световой микроскопии, где исследование микроструктуры металлических материалов проводится на микрошлифах массивных образцов на отражение, в ПЭМ используются специальные препараты— реплики или фольги, прозрачные для электронов. Приготовление их требует сложной, весьма тонкой и трудоемкой работы.
Реплики —тонкие пленки постороннего вещества, на которых получают отпечаток структурного рельефа (без фаз, либо с включенными частицами фаз) исследуемой металлической поверхности, подготовленной металлографически.
Принципиальная схема получения препарата в виде реплики состоит из следующих операций: металлографической подготовки образца, включающей шлифование, полирование, травление; приготовления самой реплики в виде тончайшей пленки, прозрачной для электронных лучей; отделения ее от шлифа.
Фольги представляют собою тонкие металлические пленки, которые получают из массивных образцов путем довольно сложных операций — механической и электрохимической обработки.
Каждая из операций как при приготовлении фольг, так и реплик, требует тщательного исполнения и оказывает существенное влияние на качество объекта, исследуемого под электронным микроскопом, и, в конечном итоге, определяет успех исследования.
1.1. МЕТОД РЕПЛИК
1.1.1. подготовка поверхности микрошлифов
К качеству микрощлифов, предназначенных к исследованию в просвечивающем электронном микроскопе, предъявляются специфические требования:
1) на поверхности микрошлифа не должно быть наклепанного слоя; наличие которого при последующем травлении не позволит четко выявить мелкие детали структуры металла и получить контрастное изображение;
2) при полировании и травлении микрошлифов недопустимы выкрашивание и вытравливание частиц избыточных фаз — карбидных, интерметаллидных и неметаллических включений. В противном случае нельзя получить экстракционную реплику с включенными в нее частицами и определить их природу дифракционным анализом;
3) поверхность шлифа должна быть чистой от посторонних частиц и каких-либо продуктов травления, которые могут привести к загрязнению реплики и внесению дополнительных данных, не относящихся к структуре исследуемого материала;
4) на поверхности шлифа после травления должен быть рельеф, точно соответствующий структурному состоянию исследуемого объекта;
5) поверхность шлифа после травления не должна содержать каких-либо окисных пленок, сглаживающих рельеф, что в конечном итоге снизит контрастность изображения.
Операции шлифования и полирования должны быть выполнены весьма тщательно. С целью уменьшения времени конечного полирования и, следовательно, уменьшения возможности выполировывания частиц избыточных фаз (особенно неметаллических включений), в последнее время используют мокрое полирование [11] или двойное полирование.
Следует отметить, что даже после тщательной подготовки шлифа путем механических процессов шлифования и полирования на его поверхности как правило остается тонкий наклепанный слой. Как уже указано выше, наличие этого слоя затрудняет получение четких и контрастных изображений структуры в электронном микроскопе. Для его удаления иногда применяют многократное чередование механического полирования с промежуточными травлениями. Однако этот метод не во всех случаях является эффективным. Может иметь место выкрашивание частиц избыточных фаз с поверхности шлифа.
Наилучшим способом удаления наклепанного слоя, а также рисок, которые всегда остаются даже после тщательной механической подготовки, является электролитическое полирование. В зависимости от конкретных условий толщина металла, растворяющегося при электрополировании, может изменяться в широких пределах, но практически она всегда должна превышать толщину наклепанного слоя.
Сложность применения электролитического полирования состоит в подборе электролитов и особенно режимов процесса для сталей и сплавов различного состава. При выборе состава реактива и режима полирования (плотности тока или напряжения, температуры) обычно пользуются известными закономерностями процесса электрополирования и некоторыми представлениями о механизме этого явления.
Относительно сущности процесса электрополирования известно несколько гипотез, достаточно подробно изложенных в работах [13— 14]. Наиболее полное объяснение явлений, наблюдаемых при электрополировании, на наш взгляд, дает теория пассивации, которая рассматривает зависимость плотности тока от напряжения между катодом и анодом в электролитической ячейке. Типичная поляризационная кривая показана на рис. I. Эта зависимость имеет практическое значение и ею следует руководствоваться при выборе состава реактивов и режимов электрополирования.
Участок «аб» кривой соответствует активному травлению поверхности анода-шлифа. Поверхность шлифа при этом приобретает обычно матовый вид, характерный для травления металлической поверхности
Участок «бе» соответствует режимам неустойчивого травления. При данных режимах на образцах часто появляется характерная чернота, которая обусловлена образованием дисперсного рельефа травления.
Участок «вг» соответствует пассивации (анодной поляризации), прочно сцепленной с основой, затем идет растворение пассивной пленки прочно сцепленной с основой, затем идет растворение пассивной пленки и образование вязкой пленки в непосредственной близости от полированной поверхности. Бывает и так, что не весь участок «вг» соответствует качественной полировке. В отдельных местах участка наблюдается появление пассивной пленки, прочно сцепленной с основой. В этих случаях обычно проводят корректировку состава электролита или условий электрополирования. Важно подобрать для данного материала такой состав электролита и температуру полирования, которые позволили бы получить удлиненный участок «вг» и тем самым устранить появление нежелательных процессов, связанных с некоторыми колебаниями режима электропитания гальванической ячейки.
При режимах, соответствующих участку «гд», происходит электрополирование и выделение на поверхности металла кислорода. В случаях, если пузырьки выделяющегося кислорода прочно удерживаются на поверхности металла, полировка сопровождается образованием питтинга. Для устранения вредного влияния пузырьков кислорода часто применяют полировку в струе электролита или подбирают состав электролита, в котором образующаяся вязкая пленка препятствует возникновению прочной связи между пузырьками кислорода и металлом.
Так как современная теория еще не позволяет сделать расчеты конкретных условий процесса, в практической работе режимы электрополирования подбирают эмпирически, руководствуясь описанными выше закономерностями. Для этих целей, а также для уточнения режимов травления весьма полезно использование потенциостатов, которые в настоящее время применяют в электрохимическом фазовом анализе для отработки метода изолирования и разделения фаз [15, 16].
К настоящему времени имеется специальная литература по электролитическому полированию металлографических шлифов, где приводится большое количество составов электролитов и режимов электролиза [13, 14 и др.]. Однако применение указанных в работах рекомендаций не во всех случаях обеспечивает высокое качество шлифов. Обычно для каждого состава или групп сталей и сплавов требуется уточнять состав и подбирать оптимальный режим процесса, обеспечивающий удаление рисок, наклёпанного слоя и получение плоской или слегка волнистой блестящей поверхности. Волнистость поверхности шлифа при исследовании на электронном микроскопе, в отличие от световой микроскопии, не является дефектом, так как исследуется не сам шлиф, а реплика со шлифа.
При выборе состава электролита предпочтительно использовать электролит, который позволяет проводить качественное полирование при температурах близких к комнатным.
Многолетний опыт работы авторов позволяет рекомендовать для электрополирования различных сталей и сплавов всего четыре электролита. Состав реактивов, режимы полирования и области их применения представлены в табл. 1.
Фосфорно-хромовый, азотно-уксусный [15] и хлорно-уксусный реактивы (№ 1—3) наиболее эффективны для полирования углеродистых, низколегированных и других сталей.
Для сложнолегированных сталей и сплавов, содержащих в значительных количествах такие элементы как ниобий, молибден, вольфрам, рекомендуется электролит (№ 4) с серной кислотой. Растворителем в этом электролите предпочтительнее использовать метиловый спирт, вместо этилового.
При составлении реактивов следует соблюдать некоторые предосторожности. Кислоты в растворитель надо добавлять постепенно, малыми порциями при обязательном перемешивании раствора. Следует осторожно пользоваться концентрированной серной кислотой, так как попадание ее на кожу может вызвать ожог. Метиловый спирт, как известно, токсичен и при работе с ним необходимо соблюдение специальной инструкции. Хлорно-уксусный электролит, являющийся раствором хлорной кислоты в ледяной уксусной, требует предварительной подготовки. Хлорную кислоту до плотности 1,62 г/см3 доводят путем выпаривания. Реактивы с хлорной кислотой взрывоопасны, поэтому следует соблюдать особую предосторожность. При составлении реактивов хлорную кислоту следует добавлять к уксусной небольшими порциями, перемешивая раствор. Так как при этом протекает экзотермическая реакция, необходимо следить, чтобы температура раствора не превышала 30°С. Во избежание воспламенения реактива нельзя держать его вблизи открытого огня.
Работу со всеми электролитами необходимо проводить в вытяжном шкафу.
Все четыре рекомендуемые электролита относятся к активным. Как видно из табл. , процесс в них ведется при сравнительно высоких значениях силы тока или напряжения на зажимах \ванны. Полирование проводится путем многократного (3—7 раз), кратковременного (в течение нескольких секунд) погружения образца. Поэтому отпадает необходимость в специальном перемешивании раствора.
Все электролиты применяют в свежеприготовленном виде. Образец при полировании является анодом. В качестве катода используют пластину из нержавеющей стали, размер которой должен быть больше размера полируемого образца. Образец вводится в электролит при включенном электрическом токе так, чтобы полируемая поверхность была параллельна катоду.
После получения блестящей поверхности шлиф быстро переносят под струю проточной воды, тщательно отмывают от следов электролита и обдувают струей сжатого холодного воздуха до полного удаления влаги. При отсутствии сжатого воздуха для этих целей может быть использован бытовой пылесос.
Следует иметь в виду, что в процессе электрополирования реактив нагревается. При этом полирующая способность электролитов, не требующих подогрева, заметно снижается. Повышение температуры идет тем быстрее, чем выше применяемое напряжение, чем больше размер полируемой поверхности образца. Чтобы предотвратить нагрев надо либо увеличить объем ванны с электролитом, либо предусмотреть специальную систему охлаждения. Для охлаждения электролита можно использовать стеклянный сосуд с двойными стенками, охлаждаемыми проточной водой. Это простейшее устройство в настоящее время широко используют в практике подготовки объектов с помощью электрополирования. Оно позволяет поддерживать температуру электролита на уровне 15—20°С. Если требуется температура более низкая можно использовать жидкий азот. Количество добавляемого жидкого азота зависит от температуры ванны. При использовании ванной объемом 400—500 мл рекомендуют образцы для электрополирования площадью не более 1 см2.
Контроль качества полирования, особенно при подборе составов к режимов процесса, следует проводить на световом микроскопе.
Не менее ответственной, чем полирование операцией является травление шлифа. Травление шлифов может быть химическим или электролитическим. Метод химического травления более простой, не требующий специальных устройств.
Выявление микроструктуры при химическом травлении происходит либо за счет избирательного растворения отдельных участков структуры, различающихся по химическому составу, либо за счет образования тонкой плотноприлегающей к поверхности шлифа окисной пленки. Окисная пленка на шлифе при исследовании с помощью электронного микроскопа недопустима, так как она, во-первых, сглаживает структурный рельеф, во-вторых, при отделении реплики от шлифа пленка может подтравливаться и частично оставаться в ней. Это внесет дополнительные (ложные) данные, не относящиеся к истинной структуре металла.
Электролитическое травление шлифов предпочтительно при исследованиях с помощью электронного микроскопа. Процесс выявления микроструктуры электролитическим способом сводится к избирательному растворению структурных составляющих, различающихся значениями потенциалов. В результате такого травления на шлифе всегда создается рельеф, соответствующий структурному состоянию исследуемого металла. Этот процесс по сравнению с химическим травлением более трудоемкий и сложный. Данные о характере взаимодействия электролитов с различными фазами весьма ограничены. Для качественного травления, обеспечивающего выделение в рельефе той или иной фазы, требуется, как правило, экспериментальная работа по подбору составов электролитов и режимов травления. Это особенно важно при использовании экстракционных реплик. Состав электролита в этом случае должен быть таким, чтобы при электролизе растворялась лишь матрица, а исследуемые фазы с ним не взаимодействовали. Режимы электролиза должны обеспечивать получение оптимальной глубины рельефа, позволяющего четко выявить исследуемую структуру и получить достаточную контрастность изображения. Следует иметь в виду, Что слабое травление выявляет более тонкие детали структуры, но оно не всегда обеспечивает достаточную контрастность. Глубокое травление обеспечивает хорошую контрастность, но оно неприменимо для мелкодисперсных структур. Кроме того, глубокий рельеф способствует сильному сцеплению реплики с поверхностью шлифа, отделение ее бывает затруднительным.
Иногда электролитическое травление проводят в том же электролите, что и электрополирование, но при пониженном (примерно в 10 раз) напряжении или плотности тока. Однако такой метод не всегда обеспечивает получение качественных и воспроизводимых результатов. Существует мнение, что наилучшими электролитами для травления шлифов, предназначенных к исследованию в электронном микроскопе, являются те, которые используют при фазовом химическом анализе для количественного разделения ,фаз. Например, для карбидных фаз в сталях—реактив Н. И. Поповой (75 г КО 5 г лимонной кислоты; 100 мл воды), для интерметаллидных фаз типа Ni3 (TiΑΙ) в сплавах на никелевой основе — реактив Μ. М. Шапиро (10 мл H2SО4; 85,5 мл Н2О; 3 г FeS04 и 3,5 г NaCl) и др.
Однако, как показывает практика, для получения положительных результатов нельзя ограничиться указанными реактивами. В каждом конкретном случае требуется уточнение состава электролита и режимов травления.