Электрохимико-термическая обработка металлов и сплавов
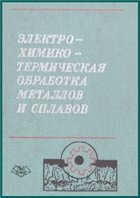
Кидин И.Н., Андрюшечкин В.И., Волков В.А., Холин А.С.
Металлургия, 1978 г.
АЛИТИРОВАНИЕ СТАЛИ
Алитирование стали и некоторых сплавов широко применяется в промышленности для повышения их жаростойкости в окислительных и других средах [1, 11, 157]. Особенно рациональным является применение алитирования для защиты стальных изделий, работающих в горячих сернистых средах. Алитированная сталь, по данным работ [157—158], при эксплуатации в средах, содержащих сероводород, в интервале температур 500—600 ° С с успехом конкурирует с нержавеющей хромоникелевой сталью типа 18-8.
Дальнейшее распространение этого прогрессивного способа ХТО сдерживается в основном двумя факторами. Первый из них — технологические трудности процесса насыщения (особенно из порошковых сред): необходимы высокие температуры (до 1100° С) и длительные выдержки (до 30 ч), возможно значительное коробление изделий, требуется дополнительная термическая обработка. Во-вторых, несмотря на относительно большое число исследований, наиболее широко распространенный процесс алити-рования в порошковых средах изучен далеко недостаточно. В первую очередь это относится к фазовому составу, структуре и механизму формирования алитированных слоев на стали, сведения о которых весьма малочисленны и противоречивы. Следствием этого являются отсутствие обоснованных рекомендаций о варьировании фазового состава, а следовательно, и свойств алитированного слоя, что особенно важно для возможности повышения пластических характеристик алитированного слоя.
Применение скоростного электронагрева для алитирования позволяет не только резко интенсифицировать процесс насыщения и избежать ряд технологических трудностей, но также изменить фазовый состав и структуру диффузионного слоя, устранить хрупкую зону, значительно увеличить деформационную способность слоя и тем самым расширить область применения алитированных изделий [165—168, 179].
1. Способы и режимы алитирования
К настоящему времени разработаны следующие способы термодиффузионного алитирования с применением скоростного электронагрева:
1) в порошкообразных смесях;
2) в пастах;
3) в газовой среде;
4) в жидкой среде (растворы солей);
5) металлизация стали алюминием и последующий отжиг с нагревом ТВЧ.
Последний способ применяют в промышленности при алитировании рабочих фасок клапанов двигателей внутреннего сгорания. Остальные способы алитирования проверены в лабораторных условиях, причем наиболее полно исследован способ насыщения из активных паст.
Авторы работ [18, с. 82; 148] проводили газовое алитирование армко-железа, среднеуглеродистой (0,64% С) стали и стали 35ХМА. Источником активного агента являлись хлориды алюминия, предварительно созданные взаимодействием тщательно очищенного хлора и алюминиевого порошка при 600—650° С. Алитирование стали 35ХМА при 800—1000° С в течение 25 с привело к образованию слоя глубиной около 20 мкм. На армко-железе при 1200— 1300° С в течение 8 с образовался слой глубиной 300 мкм. Микротвердость слоя на армко-железе составляла около 320 кгс/мм2, а основы 130 кгс/мм2. Металлографическое исследование после травления в смеси HFи НС1 показало наличие на поверхности α-твердого раствора; других фаз не обнаружено. Большим недостатком этих опытов является невысокая точность измерения температуры, проводившаяся оптическим, пирометром ОППИР-09 и не позволившая исследовать кинетику процесса образования слоев.
Диффузионный отжиг с нагревом ТВЧ предварительно металлизированных алюминием стальных деталей при 780—810° С позволяет за 10—15 с получать диффузионные слои толщиной 20—25 мкм [159—161 ]. На сталях Х9С2 и Х10С2М, предварительно покрытых алюминием с помощью металлизации, при последующем отжиге при 700° С с нагревом ТВЧ в течение 10—20 с образуются слои толщиной 15—20 мкм. Повышение температуры отжига до 900° С увеличивает слой до 136 мкм. Толщина слоя при этом способе алитирования зависит как от количества предварительно нанесенного алюминия, так и от контакта покрытия с основой [162— 163].
Наблюдения за «рассасыванием» алитированного слоя, образовавшегося на армко-железе в результате предварительного кратковременного алитирования в порошковой среде, показывают, что интенсивность этого рассасывания в значительной степени зависит от структуры аустенита, определяемой скоростью нагрева. Исследование нагрева предварительно алитированных образцов со скоростями 50 и 1200° С/с в интервале 900—1200° С с выдержкой на изотерме 5 мин показало заметное ускорение диффузионной подвижности алюминия в железе при больших скоростях нагрева.
Имеются сведения о положительных результатах при насыщении стали алюминием из жидких сред (растворы солей) с нагревом ТВЧ [164].
Наиболее полно исследован процесс алитирования с нагревом ТВЧ из активных паст и порошковых сред [165—168; 22, с. 123; 19, с. 142].
КИНЕТИКА ПРОЦЕССА АЛИТИРОВАНИЯ
ПРИ РАЗЛИЧНЫХ СПОСОБАХ И СКОРОСТЯХ НАГРЕВА
Первые опыты по алитированию железа и стали с применением скоростного электронагрева и активных паст показали, что при правильном подборе состава насыщающих паст и режимов обработки удается достигнуть весьма высоких скоростей процесса. Насыщение технического железа алюминием из пасты, состоящей из порошка алюминия дисперсностью 350 мкм и гидролизованного этилсиликата, при 1000—1050° С в течение 1—2 мин при электронагреве со скоростью 50° С/с позволяет получить диффузионные слои толщиной 0,17—0,22 мм [19, с. 142 ]. Изучение алитирования стали 10, 45 и чугуна из паст, состоящих из криолита, алюминиевой пудры и хлористого аммония, показало, что при нагреве до 850—1050° С применение индукционного нагрева 20° С/с позволяет в 3—4 раза интенсифицировать процесс насыщения по сравнению с нагревом в печи1. При этом, однако, отмечается нестабильность получаемых результатов, невозможность применения больших скоростей нагрева (200—300° С/с из-за осаждения толстого слоя алюминия на поверхность изделия и ухудшения качества поверхности образцов).
Нами совместно с ВНИИ нефтяного машиностроения проведены систематические исследования влияния состава насыщающих сред, способа нагрева и режимов ЭХТО на результаты алитирования. Насыщению подвергали техническое железо, сталь 10 и теплоустойчивую сталь Х5М, нашедшую широкое применение в нефтеперерабатывающей промышленности.
Алитирование проводили в пастах со скоростями нагрева 10, 50 и 1000° С/с. Для сравнения осуществляли алитирование с нагревом в печи (внешний источник тепла) в порошковой смеси со скоростью нагрева 0,1° С/с и в активной пасте со скоростью 10° С/с. Насыщение проводили в интервале 950—1200° С с выдержками на изотерме от 1 до 10 мин (при электронагреве) и от 15 мин до 2 ч (при нагреве в печи).