Электрические методы обработки материалов
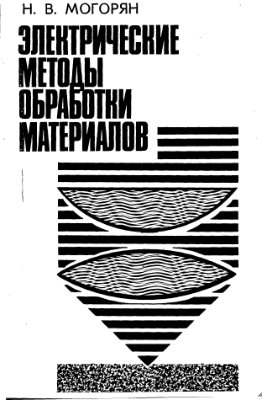
Могорян Н.В.
Кишинев, "Штиинца", 1982 г.
ТЕХНОЛОГИЧЕСКИЕ ПРОЦЕССЫ ЭЛЕКТРОИСКРОВОЙ ОБРАБОТКИ МАТЕРИАЛОВ
Многолетний опыт применения электроискровой обработки материалов показал практическую ценность этого способа. В развитии техники и технологии электроискровой обработки с момента ее появления различают четыре крупных этапа.
На первом этапе было экспериментально доказано, что технологические возможности электроискрового способа превосходят возможности широко применяемого традиционного способа обработки металлов резанием.
Вторым этапом было создание промышленных электроискровых установок и организация их серийного выпуска.
Третий этап характеризуется интенсивным развитием прецизионной электроискровой обработки металлов, когда задаваемая точность обработки деталей составляла менее 1 мкм.
Современный четвертый этап развития электроискровой обработки металлов связан с резким расширением границ применимости этого процесса, еще большим его проникновением во все звенья металлообрабатывающей промышленности.
Рассмотрим некоторые наиболее свойственные электроискровой обработке технологические приемы.
1. При изготовлении сквозных и глухих отверстий различной формы готовое отверстие полностью повторяет форму электрода-инструмента, причем с целью увеличения производительности целесообразно делать электрод-инструмент полым (с толщиной стенки 0,3— 0,6 мм). Для прошивки очень малых круглых отверстий возможно применение в качестве электрода-инструмента проволоки определенного диаметра из соответствующего металла. Этот прием применяется при изготовлении фильер, распылителей топливной аппаратуры, сопловых отверстий и пр.
2. Криволинейные отверстия или соединительные каналы применяются для охлаждения либо для подачи жидкостей или газов в сложных и малогабаритных деталях машин и приборов.
3. Электроискровое разрезание труднообрабатываемых материалов (инструментальные стали, твердые сплавы и др.), а также изготовление всевозможных пазов в ажурные и тонких изделиях или их разрезание могут производиться вращающимся диском или перемещающейся проволокой. Скорость перемещения проволоки при этом составляет 3—15 мм/с.
4. При изготовлении замедляющих систем для СВЧ-техники, к которым предъявляются очень высокие и жесткие требования, а также трафарет- или шаблон-масок для микроэлектроники требуются очень высокая точность (до 1 мкм) и чистота обрабатываемой поверхности.
5. Изготовление сложнопрофильных отверстий в фильерах для текстильной промышленности и волок из твердых сплавов для метизного (волочильного) производства проволоки и специальных профилей.
Выпускаемые отечественной промышленностью электроискровые установки позволяют производить текстильные фильеры за один технологический прием, помощью проволоки соответствующего диаметра прошивается отверстие, после чего этой же проволокой элекродом изготавливаются остальные элементы сложи профильной фильеры, что существенно упрощает технологию и повышает производительность процесса.
6. Электроискровое формообразование внешних и внутренних поверхностей непрофилированным электродом (электродом-проволокой).
Штамповка, ковка, литье под давлением — самые прогрессивные методы механической обработки металлов. Применяемые для их реализации штампы и формы составляют около 10% от общего количества металлообрабатывающего инструмента, однако затраты труда на изготовление этих штампов достигают 40—45% от общей трудоемкости изготовления инструмента.
Применение твердосплавных штампов, несмотря на более высокую их себестоимость, позволяет с тем же оборудованием и на тех же производственных площадях повысить выпуск продукции в десятки раз. Однако изготовить такие штампы или формы обычным режущим инструментом практически невозможно.
7. Электроискровое клеймение. При поточном производстве деталей, режущего и другого инструмента появляется необходимость их маркировки. Для маркировки, например, стальных изделий пригодны механические способы. В тех случаях, когда необходимо маркировать детали или инструмент из твердых сплавов, рационально применение электроискрового способа. Целесообразен он и при маркировке миниатюрных или ажурных деталей. Широко внедряется электроискровой метод для клеймения изделий из драгоценных и редких металлов, а также для изготовления маркировочного инструмента.
8. Электроискровая обработка токонепроводящих материалов. Ранее было отмечено, что одно из необходимых условий реализации процесса электроискровой обработки — электропроводность. Однако в ряде случаев возникает необходимость обработки такого сверхтвердого материала, как алмаз, который является хорошим диэлектриком. Применение электроискрового метода обработки в обычном виде не дает какого-либо эффекта. Поэтому для осуществления разряда поверхность алмаза покрывается металлической фольгой и подключается к аноду генератора. Электрический разряд пробивает фольгу и вместе с тем удаляет с поверхности алмаза значительные количества продуктов эрозии. Вместо металлической фольги возможно использование тонкого слоя электролита. Если по старой технологии на изготовление алмазной фильеры диаметром 200 мкм требовалось 106 ч, то применение электроискрового способа сокращает необходимое время до 5—6 ч.