Экономнолегированные стали для машиностроения
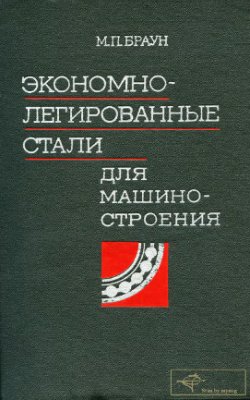
Браун М.П.
Наукова думка, 1977 г.
ЦЕМЕНТИРОВАННЫЕ СТАЛИ
Для шестерен коробок перемены передач машин, работающих в весьма тяжелых условиях, применяются цементированные хромоникелевые стали, содержащие повышенное количество никеля.
На основании систематических изысканий, детальному исследованию были подвергнуты такие стали: хромомарганцевомолибденовая типа 25ХГМ и хромомарганцевокремнемолибденовая типа 25ХГСМ.
Наряду с лабораторными исследованиями были проведены испытания в производственных условиях. Для этого изготовлены комплекты шестерен из сталей 25ХГМ и 25ХГСМ, которые подвергались испытанию на опытных машинах.
Для исследований были отлиты слитки сталей 25ХГМ и 25ХГСМ такого состава: 0,2—0,28% С; 1,1—1,42% Si; 1,1—1,3% Μn; 1,1—1,32% Cr; 0,15—0,3% Mo. Слитки были прокованы на штанги квадратного сечения размером 120 X 120 мм, а из штанг откованы заготовки для исследований. Ковка слитков и заготовок проходила в интервале температур 1200—850° С. Дефекты на заготовках не возникали. Заготовки для исследований подвергались нормализации при 920—930° С и отпуску при 620—650° С.
Некоторые незначительные колебания температуры заметно не изменяют статистических и динамических характеристик сталей.
Так, независимо от температуры закалки сталь 25ХГМ имела следующие значения механических характеристик: σΒ = 162 кГ/мм2; σт = 149 - 155 кГ/мм2; ψ = 45- 49,2%; ан= 7,1 - 7,8 кГ · м/см2;42 - 43 HRC. Закалка стали 25ХГСМ при температурах 880—900°С обеспечивает получение практически неизменных механических характеристик. У стали 25ХГСМав = 162 ~- 167 кГ/мм2; στ = 152 — 154 кГ/мм2 ψ = 47 ~ 48%; αΗ = 9,5 ~ 10 κΓ · м/см2.
Наилучшей температурой закалки, обеспечивающей сочетание высокой прочности и высоких пластических свойств, является температура 840—860° С для обеих сталей. Оптимальное сочетание свойств, т. е. высокой прочности и пластичности, у сталей 25ХГМ и 25ХГСМ получается при температуре отпуска 200—220° С.
Результаты испытаний образцов после закалки и отпуска с предварительным перегревом и без него показали, что механические характеристики всех сталей после одинарной и двойной закалки получаются практически идентичными.
Цементация проводилась на образцах 20 X 20 X 100 мм с надрезом на глубину 3 мм. Применялся бандюжский карбюризатор. Соотношение свежей и старой смесей составляло 3:1; 1 : 3; 1 : 4. Цементация образцов в карбюризаторе с соотношением свежей смеси и старой 3 : 1 проводилась при температуре 920° С и длительности 8, 12, 16, 20, 24 и 30 ч и в карбюризаторе с соотношением свежей и старой смесей 1 : 3 и 1 : 4 при температуре 900° С и длительности 12, 16, 20, 24 и 30 ч.
Глубина цементации сталей 25ХГМ и 25ХГСМ находится в прямой зависимости от ее длительности. С увеличением длительности цементации глубина слоя увеличивается. Сталь 25ХГМ при равных условиях имеет глубину цементации, большую, чем сталь 25ХГСМ.
Стали 25ХГМ и 25ХГСМ при цементации в карбюризаторе состава 25% нового и 75% старого дают глубину цементации, близкую к глубине цементации сталей 12Х2Н4А и 18ХНВА, достигаемой при карбюризаторе с 30—35% свежего.
Стали 25ХГМ и 25ХГСМ после цементации и термической обработки имеют твердость на поверхности образца 60—62 HRC, в центре 40—45 HRC. Микроструктура термически обработанных образцов стали 25ХГСМ показывает полное отсутствие карбидов в цементированном слое, независимо от состава карбюризатора.
При цементации стали 25ХГМ в карбюризаторе состава 25% нового и 75% старого после термической обработки в цементированном слое наблюдаются лишь следы глобулярных карбидов.
У стали 25ХГСМ структура цементированного слоя мартенситная; структура сердцевины — сорбитовая и троостосорбитовая, причем переход от цементированного слоя к основной массе металла (сердцевине) равномерный, постепенный.
У стали 25ХГМ после термической обработки в цементированном слое обнаруживается мелкоигольчатый мартенсит и остаточный аустенит. Переход цементированного слоя к сердцевине у стали 25ХГМ также равномерный и постепенный.
Таким образом, цементацию стали 25ХГМ на глубину 1,2—1,6 мм (для деталей коробки скоростей) необходимо проводить при температуре 880—900° С. Длительность цементации 16—24 ч. Цементацию стали 25ХГСМ на ту же глубину необходимо проводить в карбюризаторе состава: 35% нового и 65% старого при температуре 900— 920° С. Длительность цементации 16—24 ч.
При диаметре 30 мм образцы имеют полную прокаливаемость (45 HRC). При диаметре 50 и 70 мм также не наблюдается заметного снижения твердости в центре заготовки. Небольшое снижение твердости в центре происходит на заготовках диаметром 90 мм.
Стали 25ХГМ и 25ХГСМ при диаметре образцов 30, 50, 70 и 90 мм имеют высокие механические свойства. Наиболее высокие значения предела прочности, предела текучести и ударной вязкости при диаметре заготовок 30, 50, 70 и 90 мм имеет сталь 25ХГСМ.
Стали 25ХГМ и 25ХГСМ при испытании от —60 до +150° С не имеют зоны хрупкого разрушения.
Склонность сталей к трещинообразованию при закалке изучалась путем многократных повторных закалок образцов диаметром 25 мм и длиной 80 мм в масле и воде от температуры 840—860° С. После каждой закалки образцы тщательно зачищались и контролировались на трещины. После двенадцатикратной закалки в масле и воде трещины на образцах не возникали. Таким образом, можно сделать вывод, что стали 25ХГМ и 25ХГСМ не обладают склонностью к трещинообразованию. Это значительно расширяет область их применения.
Из сталей изготавливались шестерни коробки скоростей различных наименований. Ковка и штамповка опытных деталей проходила в интервале температур 1180—850° С. В процессе ковки и штампсвки никаких затруднений не возникало. После штамповки все детали были подвергнуты нормализации от температуры 920—950° С и отпуску при 620—650° С. После нормализации штамповки подвергались механической обработке, которая прошла вполне удовлетворительно, и корректирования режимов обработки сравнительно с обработкой деталей из хромоникелевых сталей не требовалось.
Окончательно механически обработанные шестерни проходили термическую обработку по таким режимам: цементация на глубину 1,3—1,6 мм при температурах для стали 25ХГМ 880—900° С и для стали 25ХГСМ — 900—920° С; нормализация при температуре 880—900° С; закалка от температуры 830—840° С в масле; отпуск при 180—200° С.
Цементация деталей была проведена в бандюжском карбюризаторе в электрических и пламенных печах. Отношение свежей смеси к старой для шестерен из стали 25ХГСМ было 1 : 3 и для шестерен из стали 25ХГМ —1:4.
Исследования деталей после термообработки показали, что глубина цементированного слоя для всех деталей составляет 1,3— 1,6 мм. Структура цементированного слоя стали 25ХГМ — мелкоигольчатый мартенсит и незначительное количество весьма мелких округленных карбидов, расположенных около поверхности на глубину до 0,1 мм. Структура сердцевины зуба троостосорбитовая. У деталей из стали 25ХГСМ структура цементированного слоя — мелкоигольчатый мартенсит, причем во всех случаях карбиды не наблюдались. Структура сердцевины зуба троостосорбитовая.
Контроль деталей показал, что твердость обеих сталей одинаковая и соответствует на поверхности зуба 60—61 HRC и в центре 40—45 HRC. Кроме того, на двух деталях, изготовленных из сталей 25ХГМ и 25ХГСМ, было проведено изучение изменения твердости от периферии к центру зуба и далее до венца детали.
Характер кривых изменения твердости для этих сталей совершенно одинаков, причем у стали 25ХГСМ твердость несколько выше, чем у стали 25ХГМ.
Твердость на поверхности зуба соответствует у стали 25ХГСМ 61 HRC и у стали 25ХГМ — 60 HRC; на глубине 3 мм у стали 25XГСМ — 48 HRC и у стали 25ХГМ — 46 HRC\ на глубине 10 мм у стали 25XГСМ — 44 HRC и у стали 25ХГМ — 43 HRC.
Детали из сталей 25ХГМ и 25ХГСМ в условиях тяжелых эксплуатационных испытаний машины выдержали заданный пробег. Сталь 25ХГСМ показала хорошее сочетание прочности, вязкости и цементируемое™, высокую стойкость в условиях тяжелых эксплуатационных испытаний машин и может рекомендоваться для широкого использования в промышленности.