Экономичные профили для сельскохозяйственного машиностроения
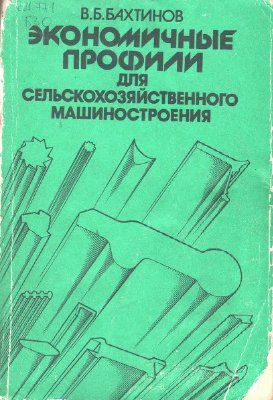
Бахтинов В.Б.
Металлургия, 1988 г.
ИСПОЛЬЗОВАНИЕ ВЫСОКОПРОЧНЫХ СТАЛЬНЫХ ПРОФИЛЕЙ В КОНСТРУКЦИЯХ ТРАКТОРОВ И СЕЛЬСКОХОЗЯЙСТВЕННЫХ МАШИН
Прогресс отечественного и зарубежного машиностроения связан с уровнем производства и особенно с качеством сортовой и листовой продукции. К качеству профилей, применяемых для изготовления конструкций тракторов методом особо сложной вытяжки, предъявляются высокие требования. За последние годы большие усилия исследователей сосредоточены на решении проблемы применения высокопрочной сортовой и листовой стали для упрочнения узлов тракторов и сельхозмашин. Одновременно необходимо снизить массу тракторов и сельхозмашин, так как при этом уменьшается рабочая мощность двигателя, и, значит, расход горючего на единицу пути. Большой запас прочности позволяет снизить геометрические параметры сортовых и листовых профилей и облегчить массу тракторов и сельхозмашин.
Исследования, проведенные фирмой "Chrysler Corp." по применению высокопрочной стали с целью эффективного уменьшения массы сельхозмашин, позволили сделать вывод, что увеличение στ от 240 до 400 МПа способствует снижению сечения детали на 40 %, если она испытывает напряжения растяжения или сжатия, и на 22 %, если она подвергается напряжению изгиба. При использовании стали с στ по 650 МПа можно уменьшить сечение детали на 62 %.
Наиболее распространенными материалами в тракторном и сельскохозяйственном машиностроении могут быть горячекатаные стальные листы с στ =400 МПа и холоднокатаные с στ =320-360 МПа. При этом сечения изделий снизятся на 20 — 25 и 10— 15 % соответственно.
Очевидно, что с позиции потребителя желательно иметь такой конструкционный материал, который наряду с высокой прочностью отличался бы хорошей технологичностью при обработке давлением и необходимым уровнем пластичности. Это объясняется тем, что листовая и сортовая сталь имеет пределы обрабатываемости, зависящие от уровня ее прочности на растяжение, так как по мере возрастания прочности относительное удлинение снижается.
В последнее время наметился значительный интерес потребителя к применению высокопрочной стали. Положительная оценка такой стали с точки зрения эффективности ее использования поддерживается проектно-конструкторскими институтами. Применение высокопрочной стали развивается в направлении использования легированной низкоуглеродистой стали, а также в направлении осуществления специальной термической обработки низкоуглеродистой стали. За последние годы производство высокопрочной стали в Японии увеличивается, и такая же тенденция наметилась в других промышленных странах. Новый метод продукции обладает способностью к формоизменению, отличается хорошей
свариваемостью, прочностью, планшетностью, малым допуском по разнотолщинности и экономичностью технологии.
В тракторном и сельскохозяйственном машиностроении получают распространение высокопрочные стали, предназначенные для изготовления поперечин, рам, кронштейнов, деталей тормоза и двигателя, а также других узлов и частей тракторов и сельхозмашин с целью увеличения прочности конструкции.
Ниже приведен анализ работ по производству высокопрочной низколегированной стали, обладающей различным уровнем прочности при высокой способности к формообразованию. В США разработана высокопрочная низколегированная сталь состава, %: С - 0,1; Μn 0,3-0,8; S<0,02; ΑΙ 0,02-0,06; Nb 0,01-0,12. В зависимости от содержания ниобия στ металла может колебаться от 350 до 560 МПа. Сталь прокатывают на полосу с температурой конца прокатки 890 —930°С.
После непрерывной термической обработки сталь имеет структуру феррита с включением карбидов и карбонитридов ниобия; перлит расположен только по границам зерен. Избыточные выделения карбидов ниобия имеют двоякий характер — более крупные размером около 20 и мелкодисперсные карбонитриды размером 3— 12 нм.
В стали патентуемого состава содержание углерода и марганца ниже, чем в обычных известных низколегированных высокопрочных сталях, что снижает количество перлита и повышает температуру γ — α-перехода при охлаждении. Последнее обстоятельство очень важно, так как температура γ —α-превращения определяет соотношение карбидов ниобия, выпадающих в грубой и мелкодисперсных формах, что, в свою очередь, сказывается на степени упрочнения твердого раствора и измельчения зерна феррита. Грубые выделения карбидов ниобия наблюдаются в процессе горячей прокатки, включая последние проходы. Эти грубые выделения замедляют рэкристаллизацию аустенита, особенно после окончания деформации, до тех пор, пока не начнется γ —α-превращение.
Таким образом, из низколегированной стали с добавками в качестве легирующего элемента ниобия при оптимальных режимах горячей прокатки в процессе непрерывной термической обработки можно получить высокопрочную сталь с хорошей способностью к вытяжке.
Фирма "Nippon Kokan" приводит данные по производству высокопрочных холоднокатаных листов с повышенной твердостью, обладающих высокими деформационными свойствами из стали, содержащей 0,04 — 0,12 % С и 0,1 — 1 % Μn. Технология производства предусматривает окончание горячей прокатки полосы при температуре выше 800 С. Горячекатаную полосу после травления прокатывают на стане холодной прокатки до требуемой толщины, после чего проводят непрерывную термическую обработку. Полосу нагревают до 700 —900°С, выдерживают при этой температуре в течение 10— 120 с и быстро охлаждают до комнатной температуры. После этого ее повторно нагревают до температуры перестаривающего отпуска 150 — 400°С с последующей выдержкой в течение 2—300 с. Затем полосу окончательно охлаждают и сматывают в рулон.
При проведении механических испытаний образцов получены механические свойства в следующих пределах: σΒ =490-1000 МПа; στ = =290-505 МПа; δ = 15,8- 36,2 %, что объясняется изменениями температуры отжига, времени выдержки металла и длительности процесса перестаривания, определяемой его температурным режимом, а также изменением содержания углерода и главным образом марганца в стали.
Аналогичные исследования по разработке технологии производства высокопрочной стали провел Б.Леви, который исходил из положения, что прочность штампованных деталей связана с тремя факторами: начальным значением предела текучести (после термической обработки), приращением прочности за счет холодной деформации, а также приростом сопротивления деформации при ускоренном старении в процессе нанесения и сушки краски. Исходя из этого было решено использовать модифицированную сталь ΑΙΑΙ 1010 с содержанием 0,01 % N2, созданную на основе стандартных низкоуглеродистых кипящих и полуспокойных сталей. Цель исследований состояла в получении высокопрочной стали, которая в готовом изделии (после штамповки и окраски деталей) имела бы σ7 до 500 МПа при сохранении необходимого запаса пластичности.
Подводя итоги приведенным материалам по получению высокопрочной стали, следует отметить достаточно разнообразный подход исследователей к решению поставленных задач и большой объем проводимых исследований. Это говорит о значимости и важности всей проблемы в целом. Предлагаемые технологические решения сводятся к применению низколегированной стали, содержащей разнообразный комплекс легирующих элементов, и существенно различных режимов термической обработки. Получены положительные результаты и показана возможность производства профилей, характеризуемых высоким уровнем прочности и необходимым запасом пластичности. Это позволяет использовать высокопрочную сталь для изготовления различных деталей тракторов и сельхозмашин, включая те из них, которые производят способами формовки, штамповки, протяжки и другими сложными процессами формоизменения.