Диагностирование механического оборудования металлургических предприятий
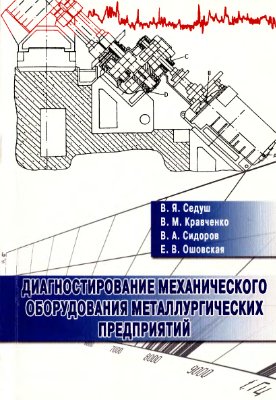
Седуш В.Я. и др.
Донецк, 2004 г.
ОСОБЕНОСГИ ПРОЯВЛЕНИЯ И ВЫЯВЛЕНИЯ ПОЛОМОК МЕТАЛЛУРГИЧЕСКИХ МАШИН
Достижение максимальной эффективности использования металлургического оборудования возможно лишь при наличии информации о техническом состоянии механизмов. Полученные данные имеют большой практический интерес и используются при определении объемов ремонтных работ, допустимой степени нагруженности и сроков эксплуатации машин. Характерным признаком наличия дефектов в механической системе является появление вибраций. Регистрация механических колебаний определила основную суть диашостироваш1я оборудования. Однако при взаимодействии узлов механизма не всегда возможно определить источник колебаний, используя традиционный подход. Необходим глубокий анализ данных измерений с использованием диагностических моделей.
Основная задача технической диагностики — получение информации о состоянии объекта. Для этого выполняются выбор, измерение и анализ диагностических параметров. Диагностическими параметрами, наиболее полно отражающими состояние механического оборудования, являются параметры вибрации. Механическое оборудование металлургических предприятий имеет характерные отличия, соответственно, процесс его диагностики требует учета этих особенностей.
Металлургические машины имеют напряженный циклический ритм работы, динамический и близкий к ударному режим нагружения. Характерным для данного класса оборудования являются: единичное и мелкосерийное изготовление; большая масса и габариты; большая мощность привода; тяжелые условия работы (запыленность, воздействие высоких, быстроменяющихся температур); высокие динамические нагрузки при цикличном характере нагружения и относительно низких частотах вращения: различные уровни вибрации при работе на холостом ходу и под нагрузкой. Обычно машины металлургического производства включают: привод, состоящий из электродвигателя и редуктора, а также исполнительный механизм.
Индивидуальность изготовления определяет высокие требования к надежной работе оборудования. Это достигается либо обеспечением прочности за счет завышенных коэффициентов запаса прочности, либо резервированием. Первый путь имеет естественные ограничения, связанные с увеличением массы, габаритов и мощности привода. При этом часто не происходит пропорционального роста срока службы. Резервирование применяется: для исполнительных органов — созданием дополнительных комплектов рабочей оснастки; для электродвигателей — наличием запасного оборудования. В результате лишь редуктор привода, не имеющий резервирования, оказывается наиболее уязвимым местом системы.
Известно, что надежность системы определяется произведением показателей надежности каждого из составляющих элементов. Отсюда вытекают повышенные требования к безотказной работе редуктора. В силу единичности изготовления на стадии проектирования отсутствуют статистические данные о надежности аналогичных механизмов. Стадия изготовления в лучшем случае обеспечивает заданные показатели и лишь на стадии эксплуатации имеется возможность оценить правильность принятых конструкторских решений.
Следовательно, металлургические машины в технологическом цикле не имеют прямого резервирования, поэтому при обеспечении их надежной, безотказной работы важнейшим фактором являются техническое обслуживание, своевременное и качественное проведение ремонтов.
Решение данной проблемы невозможно без проведения технической диагностики, в частности, контроля параметров вибрации. Однако в силу своих особенностей к металлургическим машинам не применимы нормативы общепринятых стандартов. Уникальность оборудования требует индивидуального полхода к решению вопросов оценки технического состояния конкретного механизма
Машины, непосредственно участвующие в технологическом процессе, обычно имеют два характерных режима работы: под нагрузкой и холостой ход. Дефекты привода проявляются на холостом ходу и увеличивают вибрацию механизма под нагрузкой. Дефекты исполнительного механизма проявляются лишь при работе под нагрузкой и не влияют на вибрацию машины на холостом ходу. Отсюда вытекает необходимость измерения параметров вибрации в двух указанных режимах и учет их соотношения при анализе результатов.
Основным результатом диагностирования оборудования является определение технического состояния и прогнозирование его изменения. Полученная информация используется ремонтными службами в своей деятельности, что и обеспечивает экономическую эффективность работы служб технической диагностики. Следовательно, качество переданных данных должно отображать всю сущность происходящих в механизме изменений. В настоящее время это требование не выполняется. Значительные успехи в развитии радиоэлектроники, вычислительной техники привели к появлению анализаторов параметров вибрации, предоставляющих обширную информацию о спектральном составе вибрации. Однако использование амплитудно-частотных характеристик идет по пути использования упрощенных диагностических моделей, основное содержание которых заключается в распознавании дефектов по отслеживанию амплитуд вибрации на вычисленных информативных частотах возможного проявления дефекта, а прогнозирование сводится к определению тенденций развития дефекта, в предположении неизменной скорости его изменения [8].
Данные положения не всегда позволяют объяснить внезапные изменения технического состояния машин стационарного режима работы и абсолютно недостаточны для описания процессов, происходящих в механизмах с динамическим режимом нагружения. В реальном механизме вибрация — следствие комплекса причин: состояния элементов и узлов механизма; критерии их износа; технологических параметров процесса; качества технического обслуживания. Каждый из этих факторов может стать основной причиной вибрации. Задача диагноста сводится к определению причины и способа устранения либо уменьшения уровня вибрации. Сложной проблемой является распознавание основного источника при одновременном проявлении нескольких причин.
Например, спектр вибрации редукторов металтурпгческих машин складывается из оборотных частот вращения валов, их гармоник; частот зубчатых передач и их гармоник; информативных частот возможных дефектов подшипников качения. При ослаблении посадки подшипниковна валу и в корпусе, ослаблении затяжки резьбовых соединений появляются также суб- и супергармоники. На эти частоты накладываются резонансные частоты элементов редуктора. Технологический процесс прокатки в свою очередь вызывает появление динамических колебаний. Используя метод суперпозиции, получаем сложную картину спектральных характеристик механизма, разобраться в которой при совпадении и наложении информативных частот весьма затруднительно.
Если бы информативные частоты проявления дефектов не были бы разнесены во времени и пространстве, задача определения вида повреждения не имела бы решения. Практически же определяется не весь перечень дефектов, а концентрируются внимание на одном, двух, имеющих наибольшие параметры вибрации.
Измерение спектральных характеристик вибрации требует использования сложной аппаратуры, стабильных условий измерения и кватиф1шировашгого персонала. Зачастую гораздо более практичным является предварительное исследование механизма с использованием комплекта портативных диагностических приборов контроля взаимодополняющих параметров вибрации либо анализа акустического шума. Эти методы, несмотря на незначительную глубину поиска дефекта, позволяют получить первое предупреждение о происходящих изменениях в механизме, безусловно, при правильном выборе диагностических параметров.