Дефекты стали: Справочник
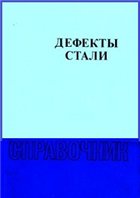
Новокрещенова С.М., Виноград М.И.
Металлургия, 1984 г.
ВВЕДЕНИЕ
Многообразие дефектов сталей и сплавов не всегда резко различающихся по внешнему виду, создает значительные трудности при их идентификации в практической работе заводов. Эти трудности нередко возрастают в связи с тем, что металл после возникновения дефекта подвергается горячей обработке давлением или термической обработке. Особенно сложно определять происхождение дефектов поверхности, на которые при нагревах воздействует воздух или атмосфера печи, что приводит к изменению химического состава поверхностного слоя, окислению, обезуглероживанию, образованию в зоне дефекта оксидов, нитридов и других фаз. Достоверно определить вид и источник образования поверхностного дефекта удается лишь «непосредственно после его возникновения.
В связи с этим важно установить характерные признаки различных дефектов при использовании соответствующих методов контроля и исследования «металла.
В современной практике используются следующие основные методы обнаружения и изучения поверхностных и внутренних дефектов:
1) внешний осмотр металла;
2) ультразвуковой контроль для выявления внутренних дефектов;
3) электромагнитные методы контроля для выявления поверхностных дефектов;
4) местная зачистка поверхности;
5) осадка образцов, вырезанных из прутков для более четкого выявления поверхностных дефектов;
6) ступенчатая обточка прутков для выявления волосовин;
7) исследование макроструктуры на поперечных и продольных темплетах после травления в кислотах или специальных реактивах, выявляющих неоднородность, а также путем снятия серных отпечатков;
8) исследование продольных и поперечных изломов (визуальное и методами световой и электронной микроскопии);
9) исследование нетравленых микрошлифов (для оценки загрязненности неметаллическими включениями, выявления микропор и микротрещин);
10) исследование микроструктуры после травления для выявления структурных составляющих, обезуглероживания, величины зерна и т. д.;
11) электронно-микроскопические методы исследования дисперсных фаз, границ зерен и особенностей тонкой структуры металла в зоне дефекта;
12) микрорентгеноспектральный анализ с целью определения состава неметаллических и инородных металлических включений, участков химической неоднородности;
13) рентгеноструктурный анализ;
1.4) петрографическое исследование неметаллических включений.
Для достоверного установления причин образования дефекта часто необходимо использовать комплекс методов. Так, при исследовании дефектов сталеплавильного происхождения после изучения макро- и микроструктуры необходимо просматривать под микроскопом нетравленый микрошлиф. Получаемая при этом информация позволит ограничить возможные причины дефекта. В случае обнаружения неметаллических включений последующее исследование их .состава и структуры методами микрорентгеноопектрального анализа, электронной микроскопии и петрографического анализа выявит источник загрязнения.
Комплексное определение происхождения дефектов, встречающихся в металловедческой практике, дает возможность использовать установленные эталоны и признаки дефекта.
Многообразие дефектов сталей и сплавов не всегда резко различающихся по внешнему виду, создает значительные трудности при их идентификации в практической работе заводов. Эти трудности нередко возрастают в связи с тем, что металл после возникновения дефекта подвергается горячей обработке давлением или термической обработке. Особенно сложно определять происхождение дефектов поверхности, на которые при нагревах воздействует воздух или атмосфера печи, что приводит к изменению химического состава поверхностного слоя, окислению, обезуглероживанию, образованию в зоне дефекта оксидов, нитридов и других фаз. Достоверно определить вид и источник образования поверхностного дефекта удается лишь 'непосредственно после его возникновения.
В связи с этим важно установить характерные признаки различных дефектов при использовании соответствующих методов контроля и исследования металла.
В современной практике используются следующие основные методы обнаружения и изучения поверхностных и внутренних дефектов:
1)внешний осмотр металла;
2)ультразвуковой контроль для выявления внутренних дефектов;
3)электромагнитные методы контроля для выявления поверхностных дефектов;
4)местная зачистка поверхности;
5)осадка образцов, вырезанных из прутков для более четкого выявления поверхностных дефектов;
6)ступенчатая обточка прутков для выявления волосовин;
7)исследование макроструктуры на поперечных и продольных темплетах после травления в кислотах или специальных реактивах, выявляющих неоднородность, а также путем снятия серных отпечатков;
8)исследование продольных и поперечных изломов (визуальное и методами световой и электронной микроскопии);
9)исследование нетравленых микрошлифов (для оценки загрязненности неметаллическими включениями, выявления микропор и микротрещин);
10)исследование микроструктуры после травления для выявления структурных составляющих, обезуглероживания, величины зерна и т. д.;
11)электронно-микроскопические методы исследования дисперсных фаз, границ зерен и особенностей тонкой структуры металла в зоне дефекта;
12)микрорентгеноспектральный анализ с целью определения состава неметаллических и инородных «металлических включений, участков химической неоднородности;
13)рентгеноструктурный анализ;
14) петрографическое исследование неметаллических (включений. Для достоверного установления причин образования дефекта часто необходимо использовать комплекс методов.
Так, при исследовании дефектов сталеплавильного происхождения после изучения макро- и микроструктуры необходимо просматривать под микроскопом нетравленый микрошлиф. Получаемая при этом информация позволит ограничить возможные причины дефекта. В случае обнаружения неметаллических включений последующее исследование их состава и структуры методами микрорентгеноспектрального анализа, электронной микроскопии и петрографического анализа выявит источник загрязнения.
Комплексное определение происхождения дефектов, встречающихся в металловедческой практике, дает возможность использовать установленные эталоны и признаки дефекта.