Чугун: Справочник
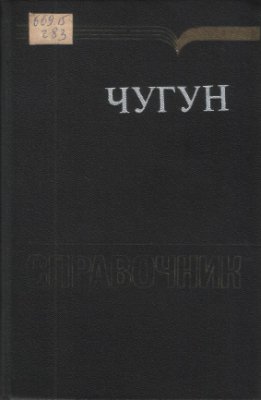
Шерман А.Д. (ред.)
Металлургия, 1991 г.
ПРИМЕНЕНИЕ АЛЮМИНЕВЫХ ЧУГУНОВ
Алюминиевые чугуны применяются, главным образом, как жаростойкие материалы в различных агрессивных газовых средах при повышенных температурах.
Чугун марки ЧЮХШ жаростоек в воздушной среде до 700 °С, стоек против истирания. Применяется как материал пресс-форм для изготовления стеклянных изделий, для деталей печного оборудования; колосников агломерационных машин и топок котлов, для деталей коксохимического оборудования; для роликов чистовых клетей листопрокатных станов, деталей газовых двигателей и компрессоров, горелок, кокилей.
Чугун марки ЧЮ6Сб жаростоек в воздушной среде до 800°С, коррозионностойкий в среде содержащей соединения серы, стоек к резким сменам температуры. Стоек в условиях трения и износа. Применяется для изготовления деталей топочной гарнитуры, колосников, кокилей, сероуглеродных реторт, деталей турбокомпрессоров, деталей аппаратов химического оборудования, деталей агломерационных машин, деталей стекольных машин, арматуры химического машиностроения, деталей цементных печей.
Чугун марки ЧЮ7Х2. Жаростойкий в воздушной среде до 1100 °С. Стойкий в среде, содержащей пары воды, сернистый носа. Применяется для деталей химического и нефтеперерабатывающего оборудования, деталей печной арматуры, колосников агломерационных машин и топок котлов, деталей цементных печей.
Чугун марки ЧЮ22Ш. Жаростойкий в воздушной среде до 800 °С и среде печных газов. Стоек в условиях истирания и из-газ и оксиды ванадия. Обладает высокой прочностью при нормальной и повышенной температурах. Алюминиевый чугун с шаровидным графитом применяют в химической, металлургической и энергетической промышленности для изготовления деталей печей пылевидного обжига колчедана, механических колчеданных печей, колосников агломерационных машин, топочной арматуры, деталей термических печей для вытяжных зонтов криолитовых ванн, футеровочных плит камер сгорания газотурбинных установок, плавильных тиглей и т. д.
Применение алюминиевого чугуна с шаровидным графитом в химической промышленности при производстве серной кислоты показало его эффективность в сравнении с высокохромистыми сталями. Детали колчеданных печей, отлитые из алюминиевого чугуна с шаровидным графитом, имеют стойкость в 1,5—2 раза выше, чем из сплава Х28. Продолжительность эксплуатации деталей в колчеданных печах на самых горячих сводах составляет более 100 сут.
Чугун марки ЧЮ30. Жаростойкий в среде, содержащей серу и сернистый газ, в среде топочных газов. Стойкий против износа при нормальных и высоких температурах. В воздушной среде жаростойкий до 1100 °С. Применяется для отливки деталей термических печей, печей обжига колчедана, тиглей для плавки алюминия. Низкокремниевые алюминиевые чугуиы применяются главным образом как конструкционный материал.
8.4. ХРОМИСТЫЕ ЧУГУНЫ
8.4.1. ВЛИЯНИЕ ХРОМА НА ЖАРОСТОЙКОСТЬ ЧУГУНА
Легирование чугуна малыми добавками хрома (не более 4 %) повышает устойчивость эвтектоидного цементита при нагреве и уменьшает рост чугуна. Повышение окалиностойкости низко-хромистих чугунов связано прежде всего с измельчением графита и уменьшением его количества в структуре. Однако в структуре таких чугунов может быть цементит.
Наличие цементита в структуре серого чугуна, легированного хромом, приводит к увеличению твердости, ухудшению обрабатываемости.
Чугуны с содержанием свыше 4—7% Сr— белые чугуны; большая часть хрома входит в состав цементита, а при нагреве чугуна металлическая основа окисляется с образованием оксидов типа Fe2O3, не препятствующих дальнейшему окислению чугуна.
Существенное повышение жаростойкости хромистых чугунов достигается при содержании в них хрома свыше 15%. При высоком содержании хрома при нагреве чугуна на поверхности образуется оксидная пленка типа шпинели (FeO-Сr2Оз), имеющая высокую плотность и прочное сцепление с металлической основой [3]. В результате резко повышается окалиностойкость чугуна (табл. 8.18, рис. 8.25). По мере повышения содержания хрома возрастает температура, при которой чугун сохраняет высокую жаростойкость:
Сr, % .....15—17 20—25 20—30 30—36
T °С ..... 900 1000 1100 1300
Чем выше содержание углерода в высокохромистом чугуне, тем больше образуется карбидов в его структуре. Поскольку большая часть хрома входит в состав карбидов, матрица обедняется хромом и снижается стойкость чугуна против окисления.
8.5. КРЕМНИСТЫЙ ЧУГУН
8.5.1. ВЛИЯНИЕ КРЕМНИЯ НА СТРУКТУРУ И СВОЙСТВА ЧУГУНА
При содержании 5,6 % Si чугун практически имеет однофазную ферритную матрицу и поэтому отличается высокой ростоустойчивостью. Окалиностойкость кремнистого чугуна связана с образованием в поверхностном слое наряду с оксидами железа и оксидов кремния S1O2. Эта пленка имеет плотную структуру при незначительной толщине.
Легирование кремнистого чугуна никелем (до 2 %) или хромом (0,5—4 %) повышает его жаростойкость (рис. 8.28).
Влияние кремния на окалиностойкость чугуна с шаровидным графитом показано на рис. 8.29 [6].
Легирование молибденом в количестве 1—3 % увеличивает прочность при повышенных температурах, а также сопротивление ползучести кремнистого чугуна с шаровидным графитом.
9.3.1. ВЛИЯНИЕ ХИМИЧЕСКОГО СОСТАВА НА КОРРОЗИОННУЮ СТОЙКОСТЬ
Хром относится к самопассивирующимся металлам, так что при механическом повреждении пассивной пленки оксидов хрома она легко самопроизвольно восстанавливается [2]. Пассивность хромистых чугунов приводит к сильному торможению анодного процесса коррозии и сопровождается сдвигом электродного потенциала в положительную сторону.
Как уже отмечалось, хром с железом образует ряд твердых растворов и интерметаллическое соединение FeCr. С углеродом хром образует ряд карбидов, обладающих электрохимическим потенциалом, близким к потенциалу хромистого феррита (—0,446), и поэтому они практически не снижают химическую стойкость сплава. С точки зрения химической стойкости полезным является только хром, находящийся в твердом растворе. Количество хрома в твердом растворе определяет плотность пассивирующей пленки на поверхности сплава и стойкость его в тех или иных агрессивных средах. При сильно окисляющих реагентах пассивность наступает при меньшем содержании хрома, а при слабо окисляющих реагентах пассивность наступает при большем содержании хрома.
При содержании 11,8% Сr наступает первая граница стойкости (рис. 9.1). Такие сплавы являются стойкими в разбавленной азотной кислоте комнатной температуры. Повышение содержания хрома в сплаве вызывает увеличение стойкости в азотной кислоте [4]. Высокая коррозионная стойкость хромистых чугунов обеспечивается в том случае, если содержание хрома в основе сплава не ниже 12—13 % [1]. Коррозионная стойкость хромистых чугунов зависит от соотношения хрома и углерода [5], которое определяет распределение хрома между матрицей и карбидами (рис. 9.2). Массовая доля хрома в карбидах колеблется от 30 до 50 % [6]. Соотношение массовых долей хрома и углерода должно быть в пределах от 17: 1 до 10 : 1. Установлено [7], что коррозионная стойкость сплава с 27,5 % Сг в 20 %-ной HN03 при 100 °С практически не изменяется при повышении содержания углерода до 1,5%» но заметно снижается при дальнейшем его повышении (рис. 9.3). Так как большая часть углерода связывается в карбиды, содержание свободного хрома в высокохромистых чугунах в большинстве случаев не выходит за пределы первой границы устойчивости. Этим объясняется более низкая коррозионная стойкость высокохромистых чугунов по сравнению с высокохромистыми сталями.
Кремний уменьшает растворимость углерода в кремистом феррите, образует с хромом химическое соединение CrSi, что неблагоприятно отражается на химической стойкости сплава.
Повышенная концентрация кремния в хромистых чугунах увеличивает их твердость, и только в высокоуглеродистых чугунах нарастание твердости несколько замедляется (рис. 9.4).
Содержание марганца в хромистых чугунах ограничивается 0,5—0,8 % при минимальном содержании серы [4]. Для улучшения антикоррозионных свойств и борьбы с крупнозернистым строением рекомендуют содержание марганца повышать до 2—3%. При этом увеличивается коррозионная стойкость в некоторых средах (20%-ная HN03 при кипении, 1 %-ная H2S04, 85 %-ная Н3РО4) [5]. По данным, приведенным в работе [8], увеличение концентрации марганца до 10—12 % в сплавах с высоким содержанием хрома на коррозионную стойкость заметно не влияет.
Добавка молибдена до 3,5 % увеличивает коррозионную стойкость (за счет увеличения эффективного содержания хрома в твердом растворе), в ряде разбавленных растворов кислот, таких как H2SO4, HQ, Н3РО4, HSO3, уксусной, муравьиной и др. [6, 4]. Молибден обладает также высокой пассивирующей способностью в некоторых восстановительных средах. Пассивированная пленка состоит из 53 % Fe2O3, 32 % Сг20з, 12 % Мо03 [6]. Легирование молибденом особенно повышает коррозионную стойкость чугунов в агрессивных средах, содержащих ионы хлора [2]. Сильно повышает коррозионную стойкость в серной кислоте средних концентраций совместный ввод 2 % Мо и 2 % Си [4].
Титан размельчает структуру чугуна и оказывает положительное влияние на антикоррозионные свойства. Весьма действенна добавка 0,5 % Ti к чугуну с 27 % Сr и 10 % С. В этом случае устраняется транскристаллизация и происходит измельчение структуры, механические свойства повышаются. Химическая стойкость при добавке 0,5 % Ti увеличивается в 20 %-ной H2S04, 20 %-ной НС1 и 85 %-ной Н3РO4 при температуре кипения. При добавке титана свыше 0,5 % измельчение структуры уменьшается [4]. При содержании 0,6—1,0 % Ti с добавкой от 5 до 6 % Си сплав стоек в 70 %-ной H2SO4. Содержание титана в этом сплаве 0,8—1,5 % делает его стойким в 80 %-ной H2SO4 при 60 °С. Механические свойства чугуна при легировании титаном возрастают.
Рекомендуется введение в высокохромистый чугун 0,1—0,3 % азота для повышения механических свойств, однако пластичность и вязкость чугуна остаются низкими из-за присутствия карбидной фазы в сплаве [3, 4].
Медь, будучи добавлена в высокохромистый чугун в количествах от 0,5 до 2,0 %, повышает химическую стойкость, но не устраняет транскристаллизацию [4].