Алюминиевые сплавы. Состав, свойства, технология, применение
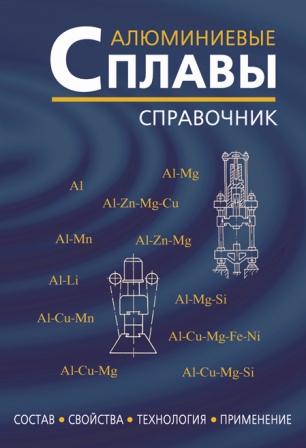
Белецкий В.М., Кривов Г.А.
КОМИНТЕХ, 2005 г.
1.3.4. СРЕДНЕПРОЧНЫЕ КОВОЧНЫЕ СПЛАВЫ СИСТЕМЫ АЛЮМИНИЙ-МЕДЬ-МАГНИЙ-КРЕМНИЙ (Al-Cu-Mg-Si)
К сплавам системы Al—Сu—Mg— Si относятся сплавы АК6 и АК8, которые служат для получения заготовок методом горячей пластической деформации — ковкой и штамповкой.
Сплав АК6 высокотехнологический ковочный сплав средней прочности разработан С. М. Вороновым в 40-х годах XX ст. и длительное время является одним из основных ковочных сплавов с хорошими характеристиками вязкости и пластичности.
Сплав АК8 (международное обозначение 2014) отличается от сплава АК6 большим в 2 раза содержанием меди, что обеспечивает повышение прочности и понижение относительного удлинения. За рубежом сплав применяется широко не только в виде кованных, но и катанных и прессованных полуфабрикатов.
Химический состав сплавов АК6 и АК8 приведен в табл. 96.
Существуют варианты сплава АК6 с содержанием, железа 0,4%, титана 002—0,1 % и хрома 0,01—0,2% - сплав АК6ч. В результате это позволило в сплаве АК6ч повысить механические свойства, вязкость разрушения, пластичность в горячем состоянии.
Сплавы АК6 и АК8 упрочняются закалкой и как правило старением. Возможно и искусственное старение.
Для обеспечения оптимальных механических свойств сплава АК6 перерыв между закалкой и искусственным старением должен быть не более 6 часов. Для сплава АК8 перерыв между закалкой и искусственным старением не сказывается на уровне механических свойств после последующего искусственного старения.
Сплав АК8 склонен к пережогу, поэтому детали толщиной больше 10 мм необходимо нагревать под закалку при температуре около нижнего предела температуры закалки.
Для обеспечения стабильных механических свойств полуфабрикатов и деталей охлаждение после закалки необходимо проводить в воде с температурой не выше 40°С.
Для снижения закалочных напряжений и коробления при закалке массивных, сложных по конфигурации деталей и полуфабрикатов из сплавов АК6, АК64 с толщиной стенки до 30 мм допускается охлаждение в воде при 80—90°С, а с толщиной до 150 мм при 70—80°С. Закалка в горячей воде вызывает снижение прочностных характеристик до 5%, но не ухудшает другие свойства по сравнению со свойствами, обеспечиваемыми закалкой в холодной воде. При этом наблюдается некоторое повышение сопротивления коррозионному растрескиванию.
Отжиг производится при температуре 380—420°С — 10—60 мин, охлаждение со скоростью 30°С/ч до 260°С, далее на воздухе.
Старение при 20°С (естественное) сплавов АК6 и АК8 обеспечивает высокую пластичность и сопротивление КР, при пониженных прочностных свойствах по сравнению с искусственным старением. Режим Т1 применяют 1ля получения высокой прочности и удовлетворительной пластичности. Для сплава АК6 (АК6ч) допускается применение сокращенного режима Т1: 170—175°С, 3 ч. Гарантируемые механические свойства полуфабрикатов из сплавов АК6 и АК6ч приведены в табл. 98.
Гарантируемые механические свойства полуфабрикатов из сплава АК8 приведены в табл. 99.
Механические свойства полуфабрикатов из сплавов АК6 и АК8 соответственно при высоких и низких температурах приведены в табл. 100, 101, 102, 103.
Вязкость разрушения и скорость роста трещины у полуфабрикатов из сплава АК6 приведены в табл. 104 и 105 соответственно.
Физические свойства сплавов АК6 и АК8 приведены в табл. 106.
Плотность сплавов: АК (АК6ч) и АК8 соответственно равно 2,75 г/см3 и 2,80 г/см3.
КОРРОЗИОННЫЕ СВОЙСТВА.
Сплавы АК6 (АК6ч) и АК8 обладают пониженной коррозионной стойкостью. Сопротивление коррозионному растрескиванию сплава АК6 в состоянии Т1 в условиях заданной деформации при переменном погружении в 3%-ный раствор NaClсоставляет в высотном направлении 120 МПа, в поперечном — 150 МПа, в продольном — 200 МПа. При перестаривании сопротивление коррозионному растрескиванию повышается.
Технологические и эксплуатационные нагревы не приводят к ухудшению коррозионной стойкости сплавов АК6 и АК8. Защита от коррозии в зависимости от назначения деталей осуществляется анодно-окисными, химическими и лакокрасочными покрытиями.
ТЕХНОЛОГИЧЕСКИЕ СВОЙСТВА.
Сплавы АК6 и АК8 имеют высокие технологические свойства при непрерывном литье, горячей обработке давлением (свободной ковке, штамповке, прессованием). Сплавы хорошо
армируются в горячем и холодном состояниях, интервал горячей деформации составляет 420—470°С.
Сплав АК6 может успешно деформироваться и в более высоком температурном интервале. Деформация сплава при 505—525°С с непосредственной закалкой в воде и последующее старение (высокотемпературная термомеханическая обработка) приводят к некоторому повышении прочности и ударной вязкости сплава. В микроструктуре наблюдает фрагментация внутри зерен, а также уменьшается глубина ободка с рекристаллизованной структурой. Такая обработка является перспективны технологическим процессом.
На структуру и механические свойства штамповок влияет вид заготовки: слиток или промежуточная прессованная заготовка. Штамповки, изготовленные из прессованной заготовки, имеют крупнозернистую направленную рекристаллизованную структуру, а штамповки, изготовленные из слитка, имеют мелкокристаллическую нерекристаллизованную структуру, соответственно изменяются и механические свойства. Многолетняя статистика механических свойств штамповок из сплава АК6 оказывает, что штамповки из сплава АК6, изготовленные из прессованного прутка, имеют более высокие механические свойства (500—520 МПа), чем те же штамповки, изготовленные из слитка. Такая закономерность характерна для протяженных узких штамповок, заготовка которых штампуется плашмя, что обеспечивает сохранение механических свойств прессованного прутка. В табл. 107 приведены механические свойства штамповок из сплава АК6Т1, изготовленных из прессованных прутков.
Для литой заготовки существенное влияние на структуру и свойства тюковок имеет схема ковки слитка.
I схема - осадка слитка на галету;
II схема - осадка на галету и вытяжка на высоту заготовки;
III схема - две осадки и две вытяжки на высоту заготовки;
IV схема - три осадки и три вытяжки на высоту заготовки.
Ковка по 1 и II схемам недостаточно деформирует металл и не обеспечивает требуемых механических свойств.
Ковка по III и IV схемам обеспечивает требуемые по техническим условиям механические свойства, при этом уменьшается разброс механических свойств.
В зависимости от назначения, условий работы и требований конструкции штамповки и поковки делятся по объему и видам испытания на пять групп. В табл. 108 приведено деление штамповок и поковок на группы в зависимости от объема и видов испытания.
Группы контроля штамповок и поковок обязательно указываются в чертежах и (или) оговариваются в технических условиях.
Одна штамповка или поковка от партии, изготавливаемая впервые или по новой технологии, подвергается всесторонним исследованиям, включающим испытание механических свойств, макроструктуры, микроструктуры и др. Схема всесторонних исследований и контрольных испытаний оговаривается в согласованных чертежах и технических условиях.
Применение. Сплавы АК6 и Ак6ч используют для ответственных силовых деталей авиационной техники длительного ресурса, в частности в крыльях пассажирских самолетов.
Сплав АК6 благодаря высокой пластичности в горячем состоянии применяют для изготовления штамповок, крыльчаток компрессора, крыльчаток вентилятора для компрессоров реактивных двигателей, корпусных деталей агрегатов.
Сплав АК8 не нашел широкого применения в отечественном авиастроении, хотя его аналог — сплав 2012 — широко применяется за рубежом не только в виде штампованных, но и катанных и прессованных полуфабрикатов.
Сплав системы Аl—Сu-Mg—Si широко используют в строительстве, транспорте, электротехнике и других отраслях промышленности. В табл. 109 приведены сводные данные по сплаву АК6.