Высокопрочные сложнолегированные стали
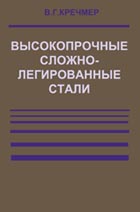
Кречмер В.Г.
Наука, 1975 г.
Глава I. ВЫБОР ХИМИЧЕСКОГО СОСТАВА
ВЫСОКОПРОЧНЫХ СЛОЖНОЛЕГИРОВАННЫХ СТАЛЕЙ И МЕТОДОВ УПРОЧНЕНИЯ
Влияние углерода и некоторых легирующих элементов на структуру и свойства сложнолегированных конструкционных и инструментальных сталей
Известно, что углерод повышает твердость закаленной стали. Закаливаемость возрастает с увеличением содержания углерода примерно до 0,6%, а при более высоком его содержании твердость закаленной углеродистой стали практически не изменяется [164]. Для углеродистой стали с 0,6% С можно получить после закалки максимальную твердость, равную 65—67 HRC.
В легированных сталях, содержащих сильные карбидообразующие элементы (Ti, Nb, V, Zrи др.), углерод образует труднорастворимые карбиды, при этом аустенит обедняется углеродом, и после закалки твердость оказывается пониженной. С увеличением степени легирования при неизменном содержании углерода твердость закаленной низколегированной стали падает. Это вызвано тем, что легирующие элементы понижают температуру начала мартенситного превращения и увеличивают количество остаточного аустенита в структуре.
После закалки в воде образцов стали 40 диаметром 25 мм можно получить твердость до 55 HRC, для стали 40Х — 53 HRC, 40ХН — 52 HRC, 40ХНМА — 51—52 HRC. Такое же явление наблюдается при усложнении состава и дополнительном легировании никелем, который увеличивает количество остаточного аустенита в закаленной стали.
В сложнолегированных сталях марок 43ХГСТФ и 42ХГСНТФ твердость образцов диаметром 25 ммпосле закалки составляла соответственно 53 ЯД С и 49,5 НДС [108].
Увеличение количества углерода ведет к интенсивному возрастанию предела прочности в отожженной стали за счет увеличения количества перлита в структуре. При этом снижается уровень ударной вязкости, а температура перехода в хрупкое состояние не изменяется. Это положение справедливо для сталей с исходной ферритно-перлитной структурой [38]. В сталях со структурами, полученными после отпуска мартенсита, температура перехода в хрупкое состояние повышается при увеличении содержания углерода. Это связано с тем, что структура таких сталей более чувствительна к надрезу.
Данные о температуре перехода в хрупкое состояние некоторых сталей типа «хромансиль» после закалки и отпуска приведены в табл. 1.
Таблица 1
Изменение температуры перехода в хрупкое состояние сталей группы ХГСТФ в зависимости от режима термической обработки
Марка стали | Температура перехода в хрупкое состояние, °С | Термообработка (закалка, отпуск), °С |
37ХГСТФ | -70 | 200 |
37ХГСТФ | -70 | 400 |
37ХГСТФ (ГАЗ) | -40 | 450 |
44ХГСТФ | -35 | 200 |
44ХГСТФ | -10 | 400 |
42ХГСТФ с церием |
|
|
(0,002 % Р) | -70 | 400 |
Ударная вязкость, соответствующая температуре перехода в хрупкое состояние принята равной 3,0 кгс-м/см2 [62]. По данным В. Н. Зикеева и др. [83], при таком значении ударной вязкости в изломе наблюдается 12% вязкой составляющей для стали 35ХГСА (радиус надреза 0,9 мм).
В последнее время большое внимание уделяется исследованиям и оценке склонности сталей к хрупкому разрушению. Содержание углерода в конструкционных сталях, устойчивых против хрупкого разрушения при отрицательных температурах, должно составлять менее 0,1%, так как при большем его содержании возрастает склонность к хрупкому разрушению. Это связано с ростом количества хрупкой карбидной фазы, наличие которой облегчает процесс зарождения трещины. С увеличением карбидной фазы хрупкое разрушение в отличие от вязкого (транскристаллитного) происходит по границам зерен [71]. При содержании углерода более 0,5% резко снижается пластичность и ударная вязкость стали, возрастает количество остаточного аустенита, снижается мартенситная точка Мн.
Углерод в штамповых сталях для горячего деформирования содержится в пределах 0,5—0,6% (стали типа 5ХНМ, 5ΧΉΒ, 5ХНСВ, 5ХГМ). Эти стали получили наиболее широкое применение. В некоторых более сложнолегированных сталях во избежание получения стали заэвтектоидного состава, что происходит вследствие резкого смещения точки Sвлево, содержание углерода уменьшают до 0,35—0,45%. (Стали 4Х5В4ФСМ (0,6—1,0% Si), 4Х5В2ФС (0,8—1,2% Si) и др. (ГОСТ 5950—73). Последние, естественно, являются более стойкими против разупрочнения за счет сложного легирования и высокого суммарного содержания легирующих элементов, что повышает температуру фазовых превращений и соответственно их теплостойкость.
Изучение ряда штамповых сталей типа ХВМФ (0,4— 0,5% С) с различным содержанием хрома (2—6%) и вольфрама (2—5%) при постоянном содержании молибдена (0,95—1,2%) и ванадия (0,45—0,60%) позволило установить следующее [138].
С увеличением содержания углерода твердый раствор обедняется легирующими элементами. Стали обладают эффектом вторичного твердения. Следует отметить, что большинство исследованных сталей, вероятно, обладает повышенной хрупкостью за счет высокого содержания углерода и хрома. Авторы [138] не приводят данных об ударной вязкости сталей в условиях их применения. Однако известно [81], что ударная вязкость характеризует важнейшее свойство штамповых сталей — разгаростойкость (табл. 2).
Разгаростойкость стали 5ХНМ сохраняется до температуры 500°, а в стали 5ХГСТФ примерно до 450°. Учитывая, что высокая ударная вязкость и твердость сохраняются после отпуска при 200—250°, рекомендуется использовать прессовые штампы из стали 5ХГСТФ, отпущенные при этой температуре. В процессе работы штампы нагревали до
400—450°; к этому моменту было отштамповано деталей на 20—25% больше, чем штампами, отпущенными при 400°.
Авторы [81, 82] предлагают использовать стали с кремнием для штампов горячего деформирования марок 4ХЗВМС (0,43% С; 3,3% Сr; 0,8 W; 1,4% Мо; 0,1% V и 1,1% Si) и 4Х5МФС (0,36% С; 5% Сr; 1,3% Мо; 0,9% V и 1,2% Si). Они не уступают по стойкости более высоколегированной марке 4Х5В2ФС, которая была предложена взамен 5ХНМ и 5ХНВ. Из этого следует, что сталь 4Х5В2ФС может быть заменена менее дефицитной маркой 4Х5МФС.
Штамповые стали типа 5ХНВ, 5ХНТ, 5ХГС, 5Х2ГФ, 5ХЗГС по прочностным свойствам различаются мало [162], поэтому применение каждой марки связывается с размерами штампов и условиями их работы.
Рассмотрим кратко влияние некоторых легирующих элементов на структуру и свойства конструкционных и инструментальных сталей.
Хром в конструкционной стали является основным легирующим элементом, содержится в большинстве сталей в количестве от 0,8 до 3% с содержанием углерода от 0,25 до 0,45% и марганца — 0,65—1,2% [50]. С увеличением содержания хрома измельчается зерно, возрастает прочность и прокаливаемость. Однако, по данным А. П. Гуляева [47], при содержании хрома более 1% повышается температура перехода стали, содержащей 0,4% С, в хрупкое состояние. В низколегированных сталях хром частично растворяется в цементите, образуя легированный цементит (Fe, Сr)зС, остальная часть хрома находится в твердом растворе.
Введение 1% хрома в сталь 40 повышает ее прокаливаемость в 3 раза (с 10 до 30 мм) [164]. М. П. Браун [23] показал, что определенное сочетание хрома и марганца позволяет получить высокую прочность при достаточной пластичности и вязкости и устранении отпускной хрупкости. При повышенном содержании хрома несколько компенсируется ухудшение свойств, вызванное увеличенным содержанием марганца. Данное положение является, вероятно, ошибочным. Следует отметить, что при одновременном повышении содержания хрома и марганца более чем на 1— 1,2% уменьшается сопротивляемость стали хрупкому разрушению, повышается чувствительность к отпускной хрупкости и флокенообразованию. По ГОСТу 4543—71, хромомарганцевые стали применяются как цементуемые (С=0,15—0,21%) и улучшаемые (С=0;37—0,45%) при содержании хрома и марганца не более 1,3% каждого.
Улучшение свойств хромистой стали достигается легированием 0,002—0,005% В или 0,15—0,25% Zr, а хромомарганцевой — 0,03—0,09% Ti, 0,2—0,3%) Mo. Для повышения сопротивляемости коррозии добавляется до 0,2% Си. Применение хрома в инструментальных сталях основано на его способности к образованию карбидов [50]. Хром, повышая прокаливаемость, увеличивает прочность на сжатие и усталостную прочность.
Штамповые стали перлитного класса, предназначенные для горячего деформирования, содержат 0,5—0,8% Сr (5ХНМ,5ХНВ), 1,3—1,6% Cr(5ХНСВ), 0,6—0,9% Сr(5ХГМ). Более высоколегированные марки типа ХВФМ, ХВФСМ и др. содержат от 2 до 5% Сr и 0,35—0,45% С. Они обладают большей стойкостью, но дороже сталей типа ХНВ и труднее обрабатываются резанием.
Марганец в конструкционной стали содержится в количестве 0,8—1,8% при содержании углерода от 0,15 до 0,5%· В цементуемых сталях при содержании 0,12—0,17% углерода может присутствовать 0,8—1,1 % Μη (20ХГНТР). В марганцевых сталях присутствует 0,7—1,0% Μη (20Г) и 1,4— 1,8% Μη (35Г2; 50Г2). В улучшаемых сталях (0,3—0,4% С) количество марганца в среднем составляет 1%, но может доходить до 1,25% (сталь 35ХГФ). Содержание марганца в сложнолегированной конструкционной стали стремятся ограничить количеством 1,0—-1,3% (30ХГСН2А), в маргацевой стали его может быть 1,8% (35Г2).
Известно, что марганец в среднеуглеродистых сталях способствует росту зерна аустенита при нагреве, усиливает отпускную хрупкость стали, увеличивает анизотропию свойств. В сложнолегированных сталях поведение марганца имеет некоторые особенности.
Так, в сложнолегированной закаленной стали 45ХГСНТ под влиянием отпуска релаксация напряжений происходит менее интенсивно, чем в стали 45ХСНТ. Распад остаточного аустенита заканчивается при 320° в стали с повышенным содержанием марганца (45ХГСНТ), а в стали 45ХСНТ — при 280°. Пик внутреннего трения при 200°, служащий мерой концентрации дислокаций при мартенситном превращении, у стали 45ХГСНТ выше, чем в 45ХСНТ, что согласуется с более высоким уровнем прочности в первой стали [107].
Установлено [151], что в α-железе при увеличении содержания марганца от 0,6 до 3,4% повышается прочность и увеличивается пластичность, снижается порог хладноломкости железа за счет уменьшения размера зерна и изменения свойств u-твердого раствора. Повышение пластичности связано с ослаблением блокировки дислокаций, за счет чего увеличивается работа распространения трещины. С увеличением содержания марганца от 0,6 до 2,14%) порог хладноломкости железо-марганцевых сплавов высокой чистоты снижается от —40° до —80°.