Влияние водорода на свойства стали
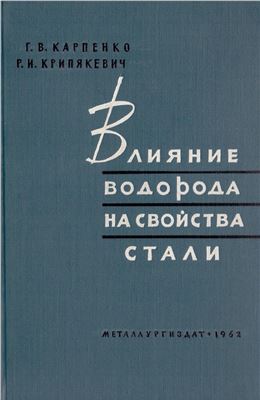
Карпенко Г.В., Крипякевич Р.И.
Металлургиздат, 1962 г.
ИСТОЧНИКИ НАВОДОРОЖИВАНИЯ
1. НАВОДОРОЖИВАНИЕ ПРИ МЕТАЛЛУРГИЧЕСКИХ ПРОЦЕССАХ
Процесс выплавки стали всегда сопровождается наводороживанием металла. Водород попадает в металл из шихтовых материалов, печной атмосферы и различных добавок, вводимых в ванну. Чугун и стальной лом содержат значительное количество водорода, однако его содержание в готовой жидкой стали определяется главным образом технологическими особенностями плавки и почти не зависит от содержания водорода в металлической шихте.
Кислый мартеновский процесс обеспечивает более низкое содержание водорода в готовой жидкой стали, чем основной. По данным литературы концентрация водорода в кислой мартеновской стали обычно находится в пределах 3—5 см3/100 г, а в основной 5—9. см3/100 г. Это различие объясняется свойствами кислого мартеновского шлака, обладающего жидкотекучестью и газопроницаемостью, причем количество растворенного водорода в таком шлаке ниже, чем в шлаках основного мартеновского процесса, что значительно уменьшает переход водорода из шлака в металл. Кипение в кислых мартеновских печах происходит менее интенсивно, чем в основных, кислый шлак лучше смачивает металл, чем основной; благодаря этому во время кипения металл обнажается меньше, что также затрудняет поглощение водорода из атмосферы печи [83].
В основных электропечах условия для дегазации металла лучше. Однако полная смена шлака и загрузка шлакообразующих материалов на поверхность обнаженного металла во время плавки качественной стали приводит к усвоению влаги жидким металлом, в результате чего содержание водорода в стали повышается и обычно достигает такого же уровня, как у основной мартеновской стали (5—9 см3/100 г).
Во время выпуска плавки из печи содержание водорода в стали обычно понижается, так как смещается равновесие между концентрациями водорода в расплавленном металле и в окружающей среде.
Эффективный метод снижения концентрации водорода в стали — вакуумная обработка жидкой стали в ковше или при переливе из одного ковша в другой, либо в изложницу. В вакууме выделение растворенных в стали водорода и азота происходит весьма интенсивно благодаря понижению их растворимости. При вакуумировании струи металла и создании достаточного разрежения можно снизить концентрацию водорода в жидкой стали до 2 см3/100 г.
Количество водорода в стали резко снижается при ее затвердевании. Часть водорода при этом выделяется в виде пузырьков, создавая пористость. Чаще всего это наблюдается в слитках хромистой стали. В отливках пористость может иметь место независимо от состава стали.
Влияние водорода, содержащегося в жидкой стали, на физические свойства твердой стали невелико.
В слитках и в прокатанных заготовках перепад концентрации водорода между внутренними и поверхностными зонами заготовки зависит от среднего содержания водорода по всему сечению: большему среднему содержанию отвечает больший градиент концентрации в радиальном направлении.
По мере переката блюмсов на меньшие профили содержание водорода значительно понижается и в большинстве случаев не превышает 3 см3/100 г, однако после первых перекатов градиент его концентрации увеличивается (сравнительно небольшие потери водорода при значительном уменьшении диаметра), а потом опять снижается в связи с десорбцией водорода.
Неравномерное распределение водорода по сечению прокатных заготовок нельзя объяснять ни удалением части водорода из поверхностных зон заготовки, ни его перераспределением после кристаллизации слитка [83], ни диффузионными процессами,, протекающими в объеме твердого металла, так как разница температур по сечению слитка очень незначительна и даже длительной термической обработкой равномерное распределение его не достигается.
Сегрегация водорода, очевидно, происходит во время кристаллизации стального слитка из-за различной растворимости его в жидкой и твердой стали. При этом жидкий металл обогащается водородом и поэтому объемы металла, застывающие последними (осевая и головная части слитка), содержат его больше. Вместе с тем в процессе кристаллизации одновременно с диффузией водорода в осевую и головную части слитка некоторое количество водорода удаляется в атмосферу и среднее содержание водорода в блюмсах становится ниже его содержания, в жидкой стали во время разливки.
Таким образом содержание водорода в жидкой стали не может однозначно характеризовать среднее содержание водорода в прокатке или поковках, и тем более его содержание в центральных зонах этих изделий. Однако обычно, чем ниже концентрация водорода в жидкой стали, тем ниже его содержание в полученных из этой стали изделиях (поковках, прокате и т. д.).
Для возможно более полного удаления водорода из проката: и поковок применяют специальную термическую обработку — низкий отжиг стали. Скорость выделения водорода из твердого металла определяется величиной коэффициента диффузии и растворимостью водорода в металле. Обе эти величины понижаются с температурой, однако, поскольку в аустените растворимость водорода больше, а коэффициент диффузии меньше, чем в продуктах распада аустенита, оптимальной для отжига
Разработка надежного способа отбора проб металла для определения содержания водорода по сечению стальных изделий [83, 71] позволила изучить влияние термической обработки на удаление водорода и перераспределение его в блюмсах различного сечения. Выявлено, что во время отжига блюмсов при 660—700° С содержание водорода в металле понижается. Количество выделившегося водорода зависит от размера сечения блюмсов и продолжительности отжига. Начало процесса отжига характеризуется так называемым «инкубационным периодом» (20—30 час), во время которого удаляется только незначительное количество водорода (10—20% от начального содержания), причем характер его распределения по сечению заготовки остается прежним. Только более длительный отжиг (до 60 час.) резко увеличивает количество удаленного водорода: таким образом может быть удалено до 40% от начального содержания водорода. При дальнейшем увеличении длительности отжига скорость выделения водорода постепенно уменьшается, так как снижается градиент концентрации водорода по сечению блюмса и в связи с этим уменьшается скорость диффузии. В результате отжига среднее содержание водорода в стали понижается до 2 см3/100 г при довольно равномерном его распределении по сечению заготовки (колебание концентрации не превышает обычно 1 см3/100 г).
2. НАВОДОРОЖИВАНИЕ СТАЛИ В СРЕДАХ, СОДЕРЖАЩИХ ВОДОРОД, ПРИ ВЫСОКИХ ТЕМПЕРАТУРАХ И ДАВЛЕНИЯХ
Высокотемпературное наводороживание стали наблюдается не только в процессе ее выплавки и передела, но и при термической обработке, и даже в процессе эксплуатации стальных деталей, если металл долго находится при повышенных температурах в среде, содержащей водород, особенно если среда имеет повышенное давление. Проникая в сталь в указанных условиях, водород приводит к снижению ее пластичности и длительной прочности и зачастую к хрупкому разрушению. Значение этой проблемы становится ясным, если вспомнить о необходимости применения стальной аппаратуры при синтезе аммиака, производстве искусственного жидкого топлива и др.
Процесс наводороживания стали при высоких температурах и давлениях можно подразделить на три этапа: 1) поглощенной сегрегация водорода; 2) обезуглероживание; 3) растрескивание ή разбухание стали.
Механизм поглощения водорода сталью по сравнению с поглощением водорода чистым железом усложняется наличием углерода стали, взаимодействующего с водородом при достаточно высокой температуре.
Диссоциированный водород среды, адсорбируясь поверхностью стали, ионизируется и в виде протонов проникает в нагретую углеродистую сталь, диффундируя в глубь ее в основном через кристаллическую решетку феррита (аналогично абсорбции водорода чистым железом), и сегрегируется в коллекторах, расположенных преимущественно у границ зерен. Однако диффузия водорода через кристаллы цементита при повышенных температурах неизбежно ведет к реакции гидрирования цементита
Fe3C + 4Н+ + 4е — 3Fe + СН4. (1)
Таким образом первый этап наводороживания (адсорбция) сразу же переходит во второй (обезуглероживание).
Молекулярный водород, сегрегировавшийся в микропустотах, тоже может принимать участие в реакции гидрирования, но с несколько большей затратой энергии:
Fe3C + 2Н2 - 3Fe + СН4. (2)
3. НАВОДОРОЖИВАНИЕ ПРИ ТЕРМИЧЕСКОЙ ОБРАБОТКЕ
При некоторых условиях наводороживание при термической: обработке может привести к снижению прочности, не восстанавливаемому даже путем отпуска. Такому наводороживаиию способствуют восстановительная атмосфера, присутствие влаги; (действующей как катализатор), наличие атомарного водорода, возникающего при закалке в воду, а также быстрое охлаждение, препятствующее десорбции водорода, проникшего уже в сталь.
4. НАВОДОРОЖИВАНИЕ ПРИ СВАРКЕ
Еще при освоении электродуговой сварки было замечено, что околошовная зона становится хрупкой и в ней появляются трещины; однако только сравнительно недавно (с 1940 г.) процесс сварки начали исследовать более глубоко. Теперь одной из причин появления околошовных трещин считают наводороживание.
При дуговой сварке стали возникают условия для наводороживания металла наплавленного шва и основного металла, так как в атмосфере сварочной дуги находится водород, легко диффундирующий в сталь при высокой температуре процесса.
Источником наводороживания при сварке, как показали эксперименты [275], является гигроскопическая и кристаллизационная влага, содержащаяся в электродных покрытиях и флюсах, а также влага ржавчины на кромках свариваемых поверхностей.
Для электросварки характерны высокие скорости охлаждения наплавленного металла шва и околошовного материала в связи с наличием больших масс смежного, не нагретого в процессе сварки, металла.
5. НАВОДОРОЖИВАНИЕ ПРИ ЭЛЕКТРОЛИТИЧЕСКИХ ПРОЦЕССАХ
Электролитическое наводороживание стали может происходить при действии электролитов на погруженный в них металл как при катодной его поляризации от внешнего источника тока, так и без нее. Технологическими процессами, в основе которых лежит действие растворов щелочей или кислот на металл, являются обезжиривание, декапирование, травление и гальванопокрытие. Кроме того, электролитическое наводороживание происходит в производственных условиях при эксплуатации деталей в некоторых коррозионных средах, и особенно при катодной защите.
Обезжиривание обычно проводится ιβ щелочных ваннах часто при катодной поляризации стали от внешнего источника тока. в качестве электролита обычно применяют едкий натр, соду, поташ. Обезжиривание проводится при комнатных температурах или горячими растворами щелочей (70—80° С).
Декапирование — это кратковременное травление стали в слабых растворах серной и соляной кислот. Этот процесс применяют обычно перед гальванопокрытиями.
Травление применяют для изменения вида поверхности металла или для удаления окислов, а также перед пайкой и лужением. Травление проводится в основном в водных растворах серной или соляной кислот, иногда три поляризации стали от внешнего источника тока.
Эти виды технологической обработки металла вызывают выделение ионов водорода на катодных участках металла. В случае катодной поляризации вся поверхность стали является катодной и подвергается наводороживапию; при отсутствии поляризации от внешнего источника тока, но при наличии водородной деполяризации наводороживание происходит через участки металла, имеющие более положительный электродный потенциал, т. е. через катодные участки поверхности, тогда как анодные участки металла подвергаются растворению.