Влияние процесса выплавки на физические и технологические свойства Mo-пермаллоя
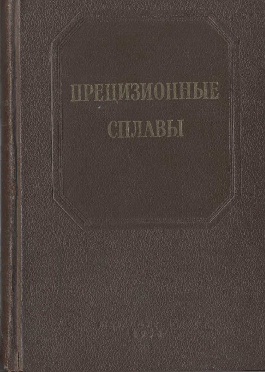
Ю. А. Грацианов А. А. Герасименко
Металлургиздат, 1956 г.
ВВЕДЕНИЕ
Среди прецизионных сплавов имеется большая группа магнитномягких сплавов, получивших широкое распространение в электро- и радиотехнической промышленности. Эти сплавы должны иметь возможно высокую начальную и максимальную магнитные проницаемости и соответственно малую коэрцитивную силу. Такими свойствами обладают железоникелевые сплавы — так называемые пермаллои.
В настоящее время разработано большое количество марок пермаллоя, содержащих различные легирующие элементы. Из них наибольшее распространение в слаботочной электропромышленности получил молибденовый пермаллой.
За последние годы опубликован ряд работ о физических свойствах, природе и отдельных характеристиках магнитно-мягких сплавов [1—9]. Однако производственные процессы изготовления таких сплавов в этих работах освещены очень слабо. Те краткие сведения о выплавке сплавов типа пермаллой, которые опубликованы в технической литературе, не позволяют составить определенного представления о рациональной технологии их выплавки. Опубликованных работ, посвященных изучению влияния условий выплавки магнитно-мягких сплавов на их технологические и физические свойства, нет совсем.
Из общей металлургической практики известно, что технология выплавки является одним из самых важных звеньев в общей технологической схеме изготовления сталей и сплавов и предопределяет получение тех или иных свойств. Последующий передел литого металла (ковка, прокатка и т. п.) вплоть до окончательной термической обработки лишь способствует в той или иной мере выявлению его потенциальных возможностей.
В Институте прецизионных сплавов ЦНИИЧМ на протяжении ряда лет проводились работы в направлении изыскания оптимальной технологии выплавки прецизионных сплавов и изучения влияния режима плавки на их технологические и физические свойства.
НАПРАВЛЕНИЯ ИССЛЕДОВАНИЙ
Из работ по изучению физической природы магнитомягких сплавов (работы В. К. Аркадьева, Я. И. Френкеля, Е. И. Кондорского, Н. С. Акулова, С. В. Вонсовского, Я. С. Шура, А. С. Займовского, Б. С. Меськина, Б. Г. Лившица и др.) следует, что для достижения высокой магнитной проницаемости должны быть соблюдены следующие основные требования:
- заданный химический состав сплава должен быть выдержан с максимально возможной точностью;
- сплав должен быть гомогенным, т. е. представлять собой однородный твердый раствор;
- сплав должен содержать минимально возможное количество неметаллических включений.
Перечисленные требования могут быть удовлетворены в той или иной мере при выплавке сплава. Эти требования и были положены в основу разработки технологии плавки.
В данной работе исследовалось влияние на технологические и магнитные свойства сплава:
- качества шихтовых материалов;
- метода выплавки;
- различных количеств технологически необходимых добавок кремния и марганца, металлургически неизбежных примесей серы, фосфора и свинца и малых присадок элементов раскислителей;
- изменения технологических и магнитных свойств в процессе выплавки и связь этих изменений с содержанием в сплаве газовых и твердых неметаллических включений.
Для выплавки опытного металла употребляли однородные (одной партии или одной плавки) шихтовые материалы. Последующий предел каждой серии плавок проводили по одной технологии. Образцы каждой серии плавок перед магнитными измерениями подвергали термической обработке одновременно.
ПЛАВИЛЬНЫЙ АГРЕГАТ И ШИХТОВЫЕ МАТЕРИАЛЫ
В качестве плавильного агрегата для выплавки прецизионных сплавов обычно употребляется тигельная индукционная печь. Применение тигельной индукционной печи обеспечивает получение:
а) максимально чистого по углероду и другим примесям металла вследствие отсутствия источников загрязнения, имеющихся в других плавильных агрегатах (газы в мартеновской печи, электроды в дуговой электропечи);
б) однородности сплава благодаря электродинамическому перемешиванию металлической ванны, что трудно обеспечить при выплавке в других агрегатах;
в) необходимой температуры металла и точности ее регулировки во всей массе без местных перегревов;
г) наименьшего угара металла по сравнению со всеми печами других типов [10], что очень ценно при применении дорогостоящих легирующих присадок.
Опыт работы ряда исследователей [1, 11], проверенный и в ЦНИИЧМ, показал, что кислая футеровка печи для выплавки высоконикелевых и высококобальтовых сплавов не пригодна. Стойкость кислой футеровки при выплавке таких сплавов низкая, а пластичность металла при горячей обработке давлением неудовлетворительная. Поэтому для выплавки прецизионных сплавов применяется только основная футеровка из смеси металлургического и каустического магнезита.
Особенностью футеровки печи является применение вставного тигля, заранее изготовленного в прессформе и прошедшего сушку на воздухе.
Стойкость таких магнезитовых тиглей в печах емкостью 40 кг достигает 100 плавок, а в печах емкостью 150 кг — 40 плавок.
Принимая во внимание высокие требования, предъявляемые к Мо-пермаллою по содержанию примесей (углерод, сера, фосфор и др.), и учитывая, что чистота исходных материалов во многом предопределяет качество сплава, подбор соответствующих шихтовых материалов для его выплавки произвели особенно тщательно.
В качестве железной составляющей применялось технически чистое железо в виде сутунок толщиной 17—20 мм, выпускаемое заводом «Серп и молот» и содержащее С< 0,025%; Si <0,03%; Мn < 0,10%; S<0,025%; Р < 0,015%; Сu< 0,25%.
Существуют и более чистые сорта железа— электролитическое, карбонильное железо, получаемое прямым восстановлением из чистых руд.
Технология производства карбонильного и электролитического железа еще широко не внедрена в промышленность, сложна и дорога, и поэтому эти материалы в условиях данной работы не применялись.
Производство железа путем прямого восстановления из чистых руд сравнительно несложно. Работы, ведущиеся в этом направлении, позволяют надеяться на возможность получения в недалеком будущем этого материала в достаточном количестве сравнительно недорого.
Особое внимание при подборе шихтовых материалов было уделено никелю. Наиболее чистым по содержанию примесей до 1947 г. считался электролитический никель марок Н0 и Н1. Однако, как показала практика, отдельные партии никеля марок Н0 и Н1, несмотря на одинаковое содержание примесей, указанных в ОСТе, очень сильно отличаются по своему качеству. Это было нами обнаружено при наблюдении за качеством металла отдельных плавок, выплавленных на разных партиях никеля одной и той же марки.
Следует обратить особое внимание на примеси, не указанные в ОСТе, но чрезвычайно вредно влияющие на качество никеля и изготовленных из него сплавов, а именно — на свинец и водород. Эти примеси могут находиться в электролитическом никеле, имея более положительный потенциал выделения, чем никель.
Свинец не растворяется в никеле и при застывании выделяется по границам зерен. Поэтому даже тысячные доли процента свинца могут сообщать никелю и его сплавам красноломкость [12]. Влияние свинца на технологические и физические свойства было исследовано и в данной работе. Результаты исследований изложены ниже.
Применение никеля, содержащего значительное количество водорода, также нежелательно, так как приводит к повышенной газонасыщенности сплава и как следствие к рослости и пористости отливки. Исследования показали, что качественное определение пригодности той или иной партии никеля можно сделать на основании осмотра поверхности и среза листа катодного никеля. В случае бугристой поверхности и губчатого среза (рис. 1) катодных листов никеля наблюдается значительно большее содержание газов и особенно водорода (табл. Г), чем у катодных листов с гладкой поверхностью и плотным срезом (рис. 2).
При ведении плавки на «губчатом» никеле имеет место вскипание металла при расплавлении, сильные брызги при даче никеля в расплавленный металл. Отливка же, несмотря на кажущуюся хорошую раскисленность металла перед выпуском, получается с большим количеством газовых пузырей, которые впоследствии являются причиной образования плен на холоднокатаных листах
Применение других материалов: ферромолибдена марки МО-1, металлического молибдена, металлического марганца (Мр-3), кристаллического кремния (Кр-1), не вызывало существенных затруднений с точки зрения получения чистого по содержанию примесей металла. Электротермический марганец по сравнению с алюминотермическим имеет повышенное содержание азота, чем и объясняется рослость и пористость слитков.
Из изложенного выше следует, что электротермический марганец нельзя применять при выплавке прецизионных сплавов в индукционных печах.
ЗАВИСИМОСТЬ ТЕХНОЛОГИЧЕСКИХ И ФИЗИЧЕСКИХ СВОЙСТВ Мо-ПЕРМАЛЛОЯ ОТ ОБРАБОТКИ МЕТАЛЛА ШЛАКОМ
I Исследованию подвергали плавки весом по 40 кг. выплавленные;
1) без шлака:
2) под кислыми шлаками;
3) прд основным шлаком с диффузионным раскислением.
Для. плавок под кислыми шлаками были выбраны шлаки, употреблявшиеся в работах А. С. Точингкоро и Перрена (с содержанием кремнезема от 50 До 70%,-) [13].
[' Для плавок под основным шлаком, с диффузионным раскислением на основании специально проведенных опытов была выбрана шлаковая смесь состава: извести 65-%, магнезита 20%, плавикового шпата 15%, и определена температура плавления шлака из этой смеси (1340 + 20°).
В качестве раскислителей для диффузионного раскисления применяли: порошок алюминия, порошок силикокальция, боркальк, карбид кальция, смесь порошков древесного угля и силикокальция.
На каждый вариант было выплавлено по 5—10 плавок.
Оценка результатов производилась по данным химического анализа, макроструктуре, магнитным свойствам (после отжига листа толщиной 0,35 мм) и по выходу годного.
ОПЫТЫ ПО РАЗЛИВКЕ СПЛАВА
При разливке сплава Мо-пермаллой в круглые или квадратные слитки небольшого веса (30—40 кг) и последующей их ковки в период освоения производства сплава было обнаружено, что этот сплав обладает неудовлетворительной ковкостью. Вследствие образования при ковке большого количества глубоких трещин выход годного после ковки был весьма низким (30—40%), а при последующих переделах поковок (горячей и холодной прокатки) выход годного становился еще ниже (10—15%). Подобные результаты были получены ранее и другими исследователями при проведении комплексной работы ВЭЙ, заводом «Электросталь» и заводом «Серп и молот» в 1936 г. [3].
Сплавы типа пермаллой находят применение главным образом в виде тонких холоднокатаных полос, лент и листов, что, естественно, требует большого количества операций при переделе литого металла.
Ввиду изложенного выше важнейшим вопросом при освоении производства Мо-пермаллоя было получение надлежащей заготовки для горячей прокатки на лист. На всех заводах черной металлургии для этой цели служат кованые или катаные заготовки, так называемые сутунки, полученные из слитка путем его ковки или горячей прокатки.
ВЛИЯНИЕ ТЕХНОЛОГИЧЕСКИХ ДОБАВОК И НЕИЗБЕЖНЫХ ПРИМЕСЕЙ НА СВОЙСТВА ПЕРМАЛЛОЯ
Основными примесями, попадающими в сплав из шихтовых материалов, являются углерод, сера, фосфор и свинец. Кроме этих примесей, в сплавах типа пермаллой обычно содержатся кремний и марганец, применяемые при выплавке для раскисления металла.
Исследование влияния указанных элементов производилось на отдельных сериях пятикилограммовых плавок с различными добавками изучаемых элементов. Содержание других элементов, кроме специально вводимого, в каждой серии плавок было постоянным.
У этих плавок изучалась макроструктура литого металла, магнитные свойства и технологические свойства путем непосредственных наблюдений при ковке и горячей прокатке. Магнитные свойства измеряли на отожженных тороидальных образцах, отштампованных из листа толщиной 0,35 мм.
Результаты исследования показали, что присадка марганца оказывает большое влияние на макроструктуру (рис. 14) и пластичность сплава. Введение в сплав марганца в количествах до 0,3°/о необходимо для улучшения технологических свойств сплава. Содержание же марганца до 1,0 ,% обеспечивает повышение максимальной проницаемости (рис. 15). Следовательно, для пермаллоя пределы содержания марганца, равные 0,8—1,2%, приняты вполне правильно.
При увеличении в сплаве содержания кремния вплоть до 1,2% резких изменений технологических свойств не обнаружено. При содержании кремния до 0,7% максимальная .проницаемость также не изменяется, а начальная проницаемость несколько возрастает (на 10—20%). Удельное электросопротивление пермаллоя с увеличением содержания кремния увеличивается (рис. 15 и 16). Оптимальные пределы содержания в сплаве кремния равны 0,4— 0,7%.
Сера и свинец являются вредными примесями. Сера оказывает чрезвычайно вредное влияние как на технологические, так и на магнитные свойства. Уже при содержании серы свыше 0,015 % магнитные свойства сплава резко ухудшаются (рис. 15).
Влияние небольших количеств свинца на магнитные свойства
незначительно (рис. 17), однако свинец резко ухудшает пластичность сплава в горячем состоянии при содержании более 0,005%.
Содержание в пермаллое фосфора до 0,08% каких-либо изменений технологических и магнитных свойств (рис. 15) не вызывает.
ВЛИЯНИЕ МАЛЫХ ПРИСАДОК ЭЛЕМЕНТОВ РАСКИСЛИТЕЛЕЙ И МОДИФИКАТОРОВ НА ТЕХНОЛОГИЧЕСКИЕ И МАГНИТНЫЕ СВОЙСТВА Мо-ПЕРМАЛЛОЯ
- бериллий, титан и цирконий ухудшают магнитные свойства сплава (понижают максимальную проницаемость и увеличивают коэрцитивную силу);
- ниобий и ванадий в исследуемых количествах существенно не изменяют магнитные свойства сплава, если не считать, что при введении их в количестве 0,2% несколько возрастает начальная проницаемость;
- при применении в качестве присадок магния, кальция и лития были получены высокие магнитные свойства.
На основании изложенных выше результатов исследования были установлены элементы раскислители и их количества, присадка которых обеспечивает повышение технологических и магнитных свойств Мо-пермаллоя. Такими присадками являются кальций в количестве 0,025% (вводимый в виде силикокальция) и магний в количестве 0,05% (вводимый в виде 10—15%-ной никель-магниевой лигатуры). Эти результаты проверены на производственных плавках.
Применение диффузионного, осадочного (кремнием и марганцем) и окончательного раскисления металла магнием и кальцием обеспечивает получение сплава с высокими магнитными свойствами и высокий выход годного при производстве ленты как из литой сутунки, так и из слитка весом до 150—500 кг.
Анализ всех этих результатов позволил сделать следующие выводы.
- Содержание в металле азота в течение обычной плавки мало, от следов до 0,0005%, и в этих пределах существенно не влияет на технологические и магнитные свойства. При увеличении содержания азота до 0,003—0,005% было замечено понижение максимальной проницаемости и увеличение коэрцитивной силы.
- Содержание водорода в металле по ходу обычной плавки постепенно увеличивается, достигая в конечных пробах 0,0006—0,0008 %.
ВЫВОДЫ
- Технологические (пластичность в горячем состоянии) и магнитные свойства сплава зависят от режима плавки. Выплавка сплава в открытой индукционной печи без шлака или под кислыми шлаками не обеспечивает получение металла хорошего качества. Выплавка сплава с применением основного шлака и диффузионного раскисления металла через шлак позволяет получить сплав с хорошими технологическими и высокими магнитными свойствами за счет значительного уменьшения в сплаве неметаллических включений и газов.
- Необходимыми условиями для получения сплава с хорошими технологическими и высокими магнитными свойствами при выплавке в открытой высокочастотной печи является применение диффузионного раскисления и последовательного осадочного раскисления металла марганцем (0,8—1,2%), кремнием (0,2— 0,7%), магнием (0,05—0,1%) и кальцием (0,025—0,050%).
- Сера и свинец являются вредными примесями. Присутствие в сплаве серы в количестве свыше 0,015% вызывает резкое понижение магнитных свойств при сохранении вполне удовлетворительной пластичности в горячем состоянии. Присутствие свинца свыше 0,005% (балл 3 по спектральному анализу) резко ухудшает пластичность сплава в горячем состоянии, но не оказывает заметного влияния на его магнитные свойства.
- Применение в качестве технологических добавок (раскислителей и модификаторов) бериллия, титана, циркония и алюминия приводит к ухудшению технологических и магнитных свойств Мо-пермаллоя.
- Наличие в сплаве при обычном способе ведения плавки в открытой печи с диффузионным раскислением водорода в количестве до 0,0008% и азота в количестве до 0,0005% почти не оказывает влияния на его технологические и магнитные свойства.
- Между содержанием в сплаве кислорода и его технологическими и магнитными свойствами существует определенная зависимость: чем выше содержание в сплаве кислорода, тем хуже его пластичность в горячем состоянии, выше коэрцитивная сила и ниже начальная и максимальная проницаемость.