Упрочнение деталей машин поверхностной закалкой при индукционном нагреве
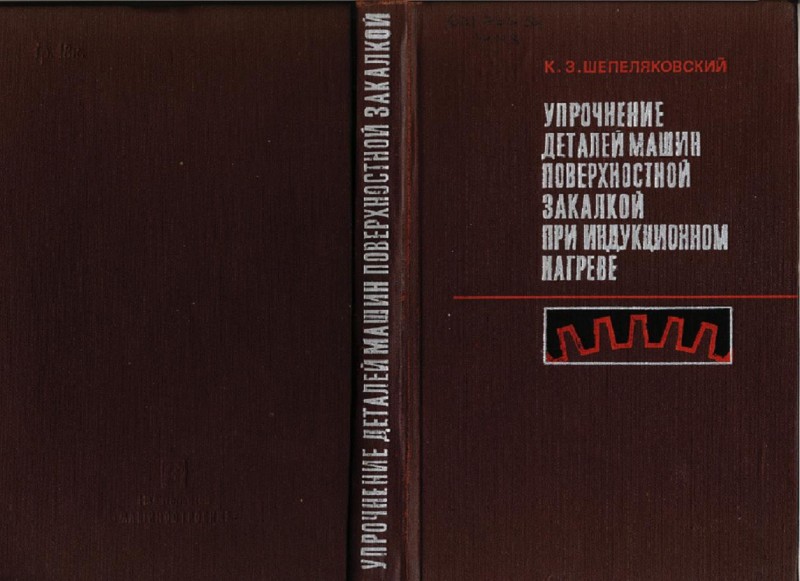
Шепеляковский К.З.
Машиностроение, 1972 г.
ОСОБЕННОСТИ СТРОЕНИЯ СТАЛИ, ЗАКАЛЕННОЙ ПРИ ИНДУКЦИОННОМ НАГРЕВЕ
1. РОСТ ЗЕРНА АУСТЕНИТА ПРИ ИНДУКЦИОННОМ НАГРЕВЕ
В закаленной и отпущенной при низких температурах стали с мартенситной структурой сохраняются границы зерна аустенита, возникшего при нагреве под закалку. Хотя эти границы не видны при обычном исследовании микроструктур, они могут быть выявлены после травления специальными реактивами. Размер действительного зерна аустенита оказывает значительное влияние на прочность и вязкость закаленной стали. Поэтому установление режимов индукционного нагрева, обеспечивающих получение мелкого зерна аустенита, необходимо для получения деталей с заданными свойствами.
Значительный интерес представляют данные о влиянии скорости и температуры индукционного нагрева на кинетику роста зерна аустенита. Для выявления размера зерна необходимо травить сталь в закаленном (мартенситном) состоянии. При этом может быть использовано как электролитическое травление с различными вариантами состава электролитов и режимов проведения процесса, так и химическое травление.
Оптимальные результаты на конструкционных сталях обычно получают химическим травлением закаленной стали в насыщенном водном растворе пикриновой кислоты с добавлением 1% солей синтетических спиртов (в виде моющих жидкостей «Синтол» , «Алкино» либо стирального порошка «Новость» [1]).
Опыт показывает, что для наиболее четкого выявления зерна аустенита методом химического травления состав реактива, а также методику травления необходимо подбирать применительно' к исследуемой марке стали, способу ее выплавки, режиму термической обработки и величине зерна. Получению хороших результатов способствует также выбор структурного состояния мартенсита (без отпуска или после отпуска при температурах 200—300°)
Метод химического травления может быть использован также для выявления действительного аустенитного зерна в легированных сталях, например, после цементации, закалки и низкого отпуска.
Начальное зерно аустенита при индукционном нагреве стали с дисперсной исходной структурой.
Начальным зерном аустенита называется его размер, полученный в момент завершения альфа-гамма превращения. Оптимальным режимом нагрева является такой, при котором после закалки стали с наиболее низкой температуры при данной скорости нагрева достигается структура безыгольчатого, равномерно травящегося мартенсита. Из этого следует, что оптимальному режиму индукционного нагрева, обеспечивающему получение - наилучшего сочетания свойств стали, имеющей структуру отпущенного мартенсита, соответствует размер начального зерна аустенита, возникающего в стали сразу после завершения образования достаточно гомогенного гамма-состояния во всем нагреваемом объеме.
Представляет несомненный теоретический и практический интерес вопрос о температурно-временных условиях индукционного нагрева, позволяющих получать наиболее мелкое — начальное зерно аустенита. Рассмотрим этот вопрос на наиболее простом случае, когда исходная структура является дисперсной, т. е. представляет собой смесь мелких, равномерно распределенных частиц феррита и цементита: Такая структура наблюдается в эвтектоидных и заэвтектоидных сталях после их отжига или нормализации на тонкий пластинчатый перлит и после улучшения, а также в доэвтектоидных сталях после их улучшения. Сюда же можно отнести сталь после предварительной закалки, так как при повторной скоростной аустенизации при прохождении критических температур мартенсит распадается с образованием дисперсной феррито-цементитной смеси [116].
Увеличение скорости нагрева с 0,02 до 100—1000° С/се/с при дисперсных исходных структурах измельчает начальное зерно стали с 8—9-го до 13—15-го балла. При скоростях нагрева порядка 10° С/сек на дисперсных исходных структурах получается некоторый промежуточный размер зерна аустенита—11—12-й балл (табл. 9).
Таким образом, при использовании мелкодисперсной исходной структуры имеется возможность изменять начальное зерно аустенита в широком интервале путем выбора той или иной скорости нагрева. При этом условиями, необходимыми для получения «сверхмелкого» начального зерна аустенита 14—15-го балла, являются мелкодисперсная исходная структура и относительно высокие скорости нагрева: 100—1000° С/сек.
Зависимость величины начального зерна аустенита от скорости нагрева при дифференцированной (феррито-перлитной) исходной структуре.
Образование начального зерна в нормализованной доэвтектоидной феррито-перлитной стали имеет существенные особенности. Выше точки Ах начинается превращение в структуреперлита, так как здесь находятся основные источники углерода — цементитные пластины. Лишь когда в процессе нагрева заканчивается превращение в перлите, начинается растворение структурно-свободного феррита и переход его в аустенит.
Таким образом, по сравнению с исходной закаленной структурой в этом случае окончание образования аустенита задерживается на температурно-временной интервал, необходимый для превращения структурно-свободного феррита в аустенит. Конец аустенитного превращения в стали 40 с нормализованной исходной структурой при скоростях 10, 100 и 1000° С/сек происходит при температурах 840, 870 и 950° С соответственно (см. табл. 9), что для высоких скоростей нагрева существенно выше, чем при исходной закаленной структуре (800° С).
Исследование микроструктуры стали 40, когда образование, аустенита из перлита закончилось, а феррит еще не растворился, показывает, что при 800° С и нагреве со скоростью 1000° С/сек получившийся из перлита аустенит имеет зерно 6 мкм2, в то время как при нагреве со скоростью 10° С/сек до той же температуры размер зерна равен 20 мкм. Таким образом, для тонкого перлита нормализованной доэвтектоидной стали действуют законемерности, обнаруженные для закаленной и улучшенной стали: увеличение скорости нагрева приводит к измельчению зерна.
Однако для растворения структурно-свободного феррита необходим дальнейший нагрев. При скорости нагрева 10° С/сек превышение температуры нагрева, необходимое для завершения растворения феррита, невелико. В этом случае начальное зерно мало отличается от зерна аустенита, образовавшегося из перлита при 800° С, или начального зерна в предварительно закаленной стали. При больших скоростях нагрева температура окончания аусте-нитного превращения сдвигается достаточно высоко, что приводит к существенному возрастанию зерна (в 5—6 раз по сравнению с зерном аустенита, полученного из перлита, или начальным зерном в предварительно закаленной стали). При этом оно достигает размеров начального зерна, возникающего при низких скоростях нагрева. Ниже приводятся экспериментальные данные, иллюстрирующие рассматриваемые явления. Исследования были выполнены для сталей 40, 45 и 55 ПП при скоростях нагрева в области фазовых превращений 6, 8, 200 и 1000° С/сек, перекрывающих диапазон скоростей, обычно применяемых в производственных условиях (не превышающих 300° С/сек). Исходная (нормализованная) структура состояла из феррита и перлита. Такая структура чаще всего используется в практике электротермической обработки. Для сопоставления определялся размер начального зерна аустенита в стали 40 при ускоренном (2° С/сек) и обычном (0,03° С/сек) нагревах в печи.