Технология кузнечно-штамповочного производства
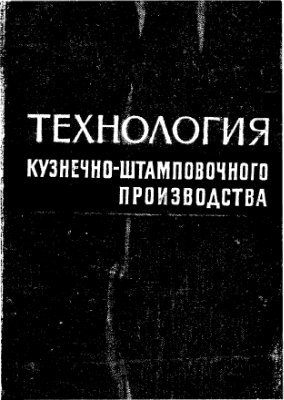
Охрименко Я.М.
Машиностроение, 1966 г.
ТЕРМИЧЕСКИЙ РЕЖИМ КОВКИ И ШТАМПОВКИ
Процессы ковки и штамповки, осуществляемые при высоких температурах (для разных марок стали в пределах 1300—750° С), можно рассматривать как совместные процессы обработки металлов давлением и термического воздействия па них. В общем случае при ковке литого металла (слитков) приходится решать три следующие задачи:
преобразование литой (дендритной) макроструктуры металла в волокнистую;
придание заготовке заданной формы и размеров поковки;
получение оптимальной зернистости металла при минимальных остаточных напряжениях. При ковке и штамповке прутковых заготовок и болванок (блюмов) решаются только две последние задачи.
Тепловое воздействие на металл приводит к почти полкой потере им упругих свойств, к уменьшению (в десятки раз) его сопротивления деформации и к повышению (на десятки процентов) пластичности. В процессе горячей обработки металла давлением происходит снятие появляющихся напряжений, в частности при возврате и рекристаллизации металла (непосредственно в процессе деформации и по ее окончании). Кроме того, тепловое воздействие па металл приводит к перекристаллизации и растворению карбидов, способствует и ускоряет диффузионные и релаксационные процессы.
К числу наиболее вредных явлений, вызываемых нагревом, относятся окалинообразование, порча поверхности металла, обезуглероживание и некоторые виды перегрева металла, приводящие к неисправимым дефектам. При неправильном ведении процесса происходит пережог стали и образование трещин вследствие растягивающих тепловых напряжений. Особенно опасен в этом отношении процесс охлаждения металла, при котором возможны и другие отрицательные явления, например флокенообразование (в результате повышенного содержания водорода в стали).
Оптимальный термический режим ковки, штамповки должен обеспечить необходимые условия для успешного проведения процесса, а также высокое качество поковок, при котором вредное влияние тепла по возможности ограничивается. Поэтому термический режим разрабатывается для каждой марки стали с учетом исходной структуры металла, его объема» соотношения размеров заготовки (слитка) и назначения поковки.
Термический режим ковки, штамповки состоит из трех этапов: нагрева металла перед ковкой, штамповкой; остывания металла в процессе ковки, штамповки (при одновременном переходе энергии деформации в тепловую); остывания металла по окончании ковки, штамповки.
В общих чертах термические режимы процессов ковки и штамповки аналогичны. Если имеется в виду ковка и штамповка одинаковых заготовок, то первый и третий этапы термического режима могут даже совпасть. Второй этап режима имеет некоторое отличие. Более быстрый темп штамповки позволяет обычно уложиться в отрезок времени, определяемый остыванием металла. При ковке часто оказывается этого времени недостаточно, и тогда приходится нагревать полуфабрикат поковки вторично (вторичный к последующие нагревы обычно называют подогревами). Особенно существенно отличие в термическом режиме катаных заготовок и слитков, в связи с чем эти режимы будут рассмотрены раздельно.
Поскольку масса слитков превышает в десятки и сотни раз массу отдельных заготовок, то длительность всех этапов термического режима ковки слитков получается относительно большей. Это приводит к повышенному окалинообразованию, значительному росту зерна и развитию других процессов, зависящих от длительности процесса. Процесс ковки слитков во времени намного превышает длительность остывания металла при ковке, что в отдельных случаях вызывает необходимость в пяти, шести и более (до двенадцати) подогревах металла.
ИНТЕРВАЛ КОВОЧНЫХ ТЕМПЕРАТУР
Одна из главных задач при разработке термического режима ковки, штамповки состоит в определении соответствующего температурного интервала, т. е. температуры начала и конца обработки металла.
Различают оптимальный (или допустимый) и технологически необходимый интервалы температур ковки, штамповки. Оптимальный интервал ковочных температур определяют в результате раздельного установления температур начала и конца ковки, штамповки. Точно установить эти температуры можно лишь на основании конкретных данных, касающихся металла (с металлургической, металловедческой и эксплуатационной). Обычно указывают ориентировочные начала и конца ковки и штамповки, которые затем подлежат уточнению исходя из конкретных обстоятельств.
Главным фактором, определяющим эти температуры, является химический состав сплава и определяемые им свойства. Ковочные температуры находятся между температурами плавления и конца рекристаллизации сплава. Более низкие температуры относятся к полугорячей, полухолодной и, наконец, холодной деформации. Обработка давлением при температурах, отвечающих промежутку между линиями солидуса и ликвидуса на диаграммах состояния, носит название штамповки или прокатки металла в момент кристаллизации. Однако обработка давлением, и в частности ковка, штамповка, не может быть осуществлена при температурах, обусловливающих в данных условиях деформации недостаточную пластичность металла.
Для уточнения интервала ковочных температур используются дополнительные сведения о сплаве в условиях ковки. Вблизи температуры плавления сплава находится температура потери его пластичности. В этой же температурной области происходит пережог стали, связанный с оплавлением и окислением границ зерен, поэтому ковать или штамповать металл при указанных температурах нельзя. Немного ниже находятся температуры перегрева сплава, который характеризуется значительным ростом зерен. Однако крупнозернистая структура большинства марок стали хорошо поддается ковке (при этом зерна измельчаются), так что максимальная температура ковки или штамповки может находиться в области температур перегрева, который начинается при температуре критического роста зерна. Иногда технологи снижают верхнюю границу температурного интервала ковки из-за необходимости уменьшить чрезмерное окалипообразование или обезуглероживание металла. Это снижение более значительно для крупных заготовок, поскольку при их нагреве требуется большое время выдержки в печи. При ковке литого металла (слитков) температура начала ковки может быть несколько повышена. Применение ускоренного режима нагрева также позволяет повысить верхний предел температурного интервала, но во всех случаях металл должен выдерживать предусмотренные технологическим процессом обжатия без трещинообразования. Если в начале ковки требуются небольшие обжатия, то их можно осуществить при температурах, более высоких, чем при ковке с большими обжатиями.
Нижнюю границу температур ковки, штамповки уточнить более сложно. Здесь приходится считаться не только с типом стали (заэвтектоидная или доэвтектоидаая), но к с объемом поковок, качеством требуемого металла, наличием или отсутствием термообработки поковок, способом их охлаждения (в том числе и с использованием ковочного тепла для термообработки и т. л.). Важным фактором при установлении ковочных температур являются требования, предъявляемые к механическим свойствам металла с учетом характера эксплуатации детали. Если для данной детали предусмотрена термическая обработка, например закалка с отпуском, то правильно выбранная температура конца ковки, штамповки (выше точки Ас2 среднеуглеродистой для доэвтектоидной стали) позволяет использовать ковочное тепло для последующей термической обработки. При этом следует стремиться к тому, чтобы условия деформации не вызывали дополнительной термической обработки в виде отжига или нормализации [83]. Если термическая обработка не предусмотрена, то нижний предел интервала ковочных температур ограничивается условиями получения мелкого зерна. Для небольших поковок (массой до —1000 кг) температура конца ковки, штамповки может быть высокой (на 200—300° С выше точки Лг3) или низкой (вблизи этой точки). Несмотря на то, что при высокой температуре конца ковки или штамповки зерно будет крупным, можно в результате быстрого охлаждения получить тонкое строение структуры сплава и соответствующие этому механические свойства. Высокая температура конца обработки способствует повышению технико-экономических показателей производства (повышению производительности, уменьшению расхода энергии на ковку, штамповку). Для поковок с большой массой и не подлежащих термической обработке получение высоких механических свойств за счет увеличения скорости охлаждения поковок маловероятно из-за невозможности в этих условиях ускорить остывание поковок. Поэтому чтобы решить эту задачу, следует подобрать такую комбинацию температуры и величины последних обжатий, которая обеспечивала бы оптимальную структуру. Здесь следует иметь в виду, что сталь, подвергнутая деформации в интервале критических обжатий (4—12%), после рекристаллизации будет иметь нежелательную крупнозернистую структуру.