Технология холодной штамповки
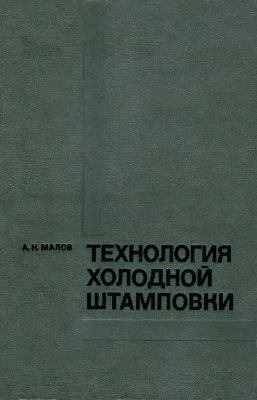
Малов А.Н.
Машиностроение, 1969 г.
КОМБИНИРОВАННАЯ ШТАМПОВКА НА УНИВЕРСАЛЬНЫХ ПРЕССАХ
Комбинированная штамповка в штампах последовательного действия осуществляется по одной из следующих схем.
1. Из полосы или ленты; вырезка по наружному контуру (отрезка) готовых деталей осуществляется на последнем переходе.
2. Из полосы или ленты; вырезка по наружному контуру предшествует формоизменяющим переходам, после чего вырезанная заготовка впрессовывается обратно в ленту или полосу и перемещается вместе с ней на последующие формоизменяющие переходы.
3. Из полосы или ленты; вырезка заготовки по наружному контуру производится перед формоизменяющими переходами, передача заготовки на формоизменяющие переходы производится специальными механизмами штампа.
4. Из предварительно изготовленной штучной заготовки; подача заготовки в штамп осуществляется вручную или специальным загрузочным устройством, а передача заготовки с одного перехода на другой — вручную или специальными механизмами (шиберными, револьверными, грейферными и т. д.).
Первую схему, т. е. комбинированную штамповку в полосе (ленте) с вырезкой (отрезкой) готовых деталей на последнем переходе, следует применять для деталей, требующих только разъединительных переходов: пробивки, надрезки, зачистки, снятия припуска по части контура и вырезки, а также для деталей, требующих разъединительных и нескольких формоизменяющих переходов: пробивки отверстий, гибки, разбортовки, отбортовки, вытяжки, вырезки и других при условии, что окончательная вырезка является последним переходом.
Штампы для рассматриваемой схемы штамповки допускают применение прессов с числом двойных ходов до 500 и более в минуту. В этих штампах легко автоматизировать подачу полосы (ленты). При шагах перемещения менее 50 мммеханизм подачи может быть встроен в штамп, а при больших перемещениях он является дополнительным узлом пресса. Преимуществом этого спссоба штамповки следует считать возможность объединения большого числа переходов, т. е. использование его для изготовления деталей сложной конфигурации. Достаточно указать, что имеются комбинированные штампы последовательного действия, объединяющие до 25 переходов.
Комбинированные штампы последовательного действия, построенные по первой схеме, являются наиболее распространенными.
Факторами, ограничивающими применение штампов, являются габаритные размеры изготовляемых деталей. Штампы используются для изготовления мелких деталей (линейный размер в направлении подачи менее 200 мм) и как исключение для деталей средних размеров. Однако независимо от габаритных размеров деталей толщина их должна быть более 0,2 ммвследствие большого брака по межосевому расстоянию отверстий.
Вторую схему, т. е. комбинированную штамповку в полосе или в ленте с вырезкой заготовки перед формоизменяющими переходами и запрессовкой вырезанной заготовки обратно в полосу (ленту), применяют для деталей, требующих одного формоизменяющего,1 перехода, например гибки, формовки, вытяжки и т. д., при условии что толщина штампуемого материала равна 0,3—2,0 мм. Если' толщина материала менее 0,3 мм, то заготовка, вырезанная и за-, прессованная обратно в полосу (ленту), плохо в ней удерживается и при перемещении полосы (ленты) выпадает из нее, что приводит к браку штампуемой детали, а иногда и поломке штампа. Если же толщина материала более 2,0 мм, требуется большое усилие для запрессовывания вырезанной заготовки обратно в полосу (ленту) и затрудняется выталкивание заготовки из последней в рабочую полость штампа. Штампы, построенные по этой схеме, используются для деталей сравнительно небольших габаритных размеров, штампуемых на прессах с числом двойных ходов до 150 в минуту.
Третью схему, т. ё. комбинированную штамповку в полосе (ленте) с вырезкой заготовки перед формоизменяющим переходом и передачей этой заготовки на последующие формоизменяющие переходы специальными шиберными или револьверными механизмами, следует применять в тех же случаях, что и вторую, но для материала толщиной 0,5—6 мм. Число формоизменяющих переходов зависит от конструкции механизма для транспортировки вырезанной заготовки. Если для транспортировки заготовки используется шиберный механизм, число переходов не более трех; если же вырезанная заготовка перемещается револьверным механизмом, то число формоизменяющих переходов может быть увеличено до шести, а иногда и более. Штампы, построенные по этой схеме, применяются при работе на прессах с числом двойных ходов не более 250 в минуту.
Четвертую схему, т. е. штамповку из штучных заготовок, следует применять для деталей, требующих в основном формоизменяющих переходов. Если передача с одного формоизменяющего перехода на другой осуществляется вручную, число переходов должно быть не более трех, а если автоматически, то число переходов, а вместе с этим и конфигурация изготовляемых деталей зависят от конструкции транспортирующего механизма. Если для транспортировки заготовок используется шиберный механизм, число формоизменяющих переходов должно быть меньше четырех. Этот способ используется главным образом для изготовления деталей, требующих гибки (скобки, втулки и т. д.).
Если используется револьверный механизм, число формоизменяющих переходов может достигать шести — десяти. Этот механизм используется главным образом для деталей, требующих вытяжки, отбортовки, разбортовки, обжима, закатки, листовой чеканки и реже гибки. И, наконец, если используется грейферный механизм, то число формоизменяющих переходов в зависимости от габаритных размеров штампуемой детали может достигать десяти. Этот тип механизма может быть использован для деталей, требующих любого вида формоизменяющих переходов.
Устанавливать штампы, работающие по четвертой схеме, при работе на автоматическом цикле можно на прессах с числом двойных ходов менее 120 в минуту.
Из рассмотренных схем построения комбинированных штампов последовательного действия необходимо обратить внимание на вторую и особенно на третью схему. Принятое в них конструктивное решение целесообразнее выделения формоизменяющих переходов в самостоятельные операции с выполнением их в штампах простого действия с питанием заготовками из магазинных или бункерных загрузочных устройств. Особенно целесообразны такие схемы для деталей малых габаритных размеров, требующих одного формоизменяющего перехода (операции).
Из большого разнообразия процессов штамповки в комбинированных штампах последовательного действия, построенных по первой схеме, ниже рассматриваются примеры штамповки деталей, изготовление которых требует следующих переходов: пробивки отверстий и отрезки; пробивки отверстий и вырезки; пробивки отверстий, зачистки снятием припуска по части контура и вырезки; пробивки отверстий, гибки и вырезки; вытяжки и вырезки, пробивки отверстий, листовой чеканки и вырезки; вытяжки, пробивки, отбортовки и вырезки.
Приведенный перечень сочетаний переходов не исчерпывает возможные случаи, их значительно больше, но рассматривать все их нет необходимости, так как они не содержат ничего принципиально нового для построения процесса штамповки на комбинированных штампах последовательного действия.
Штамповкадеталей, требующих отверстий и о т р е з к и. Схемы последовательности штамповки ряда деталей, требующих пробивки отверстий и отрезки, показаны на рис. 218. Пробивку отверстий и отрезку в одном штампе применяют для деталей простой конфигурации (допуски по наружному контуру соответствуют 5—7-му классам точности, при этом предъявляются пониженные требования к шероховатости поверхности среза), изготовляемых из калиброванной или калибруемой полосы (ленты) путем обрезки ее пуансонами-ножами по ширине в процессе штамповки. Простая конфигурация и относительно малая точность изготовления этой группы деталей позволяют широко использовать безотходную и малоотходную штамповку, а тем самым иметь высокие коэффициенты использования материала.
Схему последовательности штамповки, показанную на рис. 218, а, используют при изготовлении прямоугольных и квадратных пластинок с отверстиями (сечения пуансонов залиты или заштрихованы). Пластинки изготовляют за два перехода (здесь и в дальнейшем переходы на рисунках обозначаются римскими цифрами). За первый переход пробиваются отверстия, а за второй отрезаются готовые детали. Изменяя конфигурацию пуансона, можно уменьшать или увеличивать число одновременно изготовляемых деталей.