Технология изготовления отливок
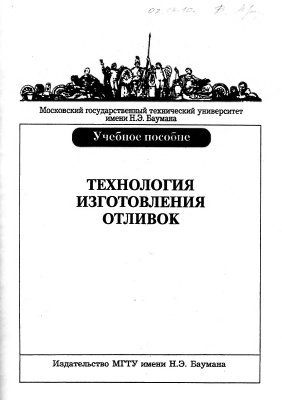
Вязов А.Ф.
МГТУ им. Н. Э. Баумана,, 2004 г.
2. РАЗРАБОТКА ТЕХНОЛОГИИ ИЗГОТОВЛЕНИЯ ОТЛИВКИ
2.1. Выбор способа изготовления отливки
Способ изготовления отливок выбирают по показателям технологических возможностей для различных способов литья (табл. П1.3). Выбирают тот способ литья, который наиболее полно удовлетворяет показателям технологических, возможностей. Если появляется возможность выбора двух или более способов литья, то способы сравнивают по коэффициенту использования металла (КИМ)
Очень часто при изготовлении отливок различными способами значения КИМ отличаются друг от друга незначительно. Вследствие этого окончательно способ выбирают по минимальной себестоимости получения детали (с учетом механической обработки)
Выбрав способ изготовления отливки, студент согласует свой выбор с преподавателем.
- Разработка чертежа элементов литейной формы
Исходным документом для разработки чертежа элементов литейной формы для выбранного способа изготовления отливки является чертеж детали с указанием технических требований на ее изготовление, при этом уточняется величина изготовляемой партии отливок.
Последовательность разработки чертежа отливки и чертежа элементов литейной формы представлена на рис. 2.
- Анализ чертежа детали
При анализе чертежа детали необходимо прочитать чертеж, т.е. представить в пространстве конфигурацию детали, габаритные размеры и форму отдельных ее частей (полостей, выступов, поднутрений, отверстий), выявить расположение обрабатываемых поверхностей, уточнить материал литой детали, а также технические и технологические требования, предъявляемые к ней.
- Выбор расположения модели в литейной форме и отливки при заливке формы металлом
Выбор проводится на основе анализа конструкции детали с учетом следующих требований:
модели (отливки) должны легко извлекаться из формы;
-при заливке формы ответственные обрабатываемые поверхности должны располагаться внизу или сбоку для получения чистой и плотной поверхности отливки;
-для повышения точности и уменьшения вероятности брака по перекосу желательно располагать отливку в одной полуформе.
На чертеже детали разъем модели и литейной формы обозначают штрихпунктирной линией.
Положения отливки в форме при заливке обозначают прописными буквами В (верх) и Н (низ), которые ставят у стрелок (рис.З).
- Расчет припуска на механическую обработку
Припуск — слой металла, который удаляют с поверхности отливки для обеспечения требуемой размерной точности и шероховатости поверхности детали.
Поверхности, подлежащие механической обработке, обозначают на чертеже детали знаком параметра шероховатости — (ГОСТ 2.309—73).
Величину припуска на механическую обработку назначают по ГОСТ 26645—85. По табл. П1.4, в зависимости от способа изготовления, наибольшего габаритного размера и материала отливки определяют класс точности размеров и ряд припуска.
Затем по табл. П1.5, в зависимости от номинального размера и класса точности, определяют допуски размеров отливок.
Для мелких отливок (до 250 мм) номинальный размер принимают, как правило, равным наибольшему габаритному размеру. Для крупных отливок в качестве номинального размера базовых поверхностей принимают наибольший габаритный размер отливки, а для остальных — размер, который контролируют при механической обработке.
Зная допуски размеров отливки и ряд припусков, по табл. П1.6 определяют припуски на механическую обработку.
В соответствии с ГОСТ 3.1125—88 на чертеже припуск на механическую обработку изображают тонкой сплошной линией, а его величину указывают цифрой перед знаком параметра шероховатости поверхности детали.
- Выбор величины формовочных уклонов
Уклоны выполняют на вертикальных наружных или внутренних поверхностях модели и другой литейной оснастки. Формовочные уклоны для отливок, изготовляемых в разовых формах, выполняют в направлении извлечения модели из формы или стержня из стержневого ящика. При изготовлении отливок в металлических формах с применением металлических стержней формовочные уклоны выполняют в направлении извлечения отливки из формы и стержней из отливки.
Формовочные уклоны выполняют:
- на обрабатываемых поверхностях — за счет увеличения размеров отливки сверх припуска на механическую обработку (рис. 4, а);
- на необрабатываемых поверхностях, которые не сопрягаются по контуру с другими деталями — за счет одновременного увеличения и уменьшения размеров отливки, от середины высоты уклона (рис. 4, в);
- на необрабатываемых поверхностях, сопрягаемых по контуру с другими деталями — за счет уменьшения (рис. 4, б) или увеличения (рис. 4, г) размеров отливки.
Величина формовочного уклона зависит от способа изготовления отливки, материала модели и высоты поверхности, на которую наносят уклон (ГОСТ 3212—88).
Формовочные уклоны отливок, изготовленных в разовых формах, выбирают по табл. П1.7.
Уклоны стенок отливок, изготовляемых литьем в металлических формах, назначают в соответствии с табл. П1.8.
Формовочные уклоны на чертеже отливки наносят сплошной тонкой линией, углы наклона указывают в градусах.
Следует помнить, что величины формовочных уклонов, приведенные в табл. П1.7 и П1.8, на чертеже детали не указывают и вычерчивают деталь без уклонов, за исключением чертежей крупногабаритных отливок, где целесообразно указывать уклоны или же предпочтительнее предусматривать конструктивные уклоны (1:5; 1:10; 1:20; 1:50), превышающие формовочные уклоны (в этом случае формовочные уклоны не выполняют).
2.2.7. Выбор припуска на усадку сплава
При затвердевании и охлаждении отливки в литейной форме ее габаритные размеры уменьшаются. Это необходимо учитывать при изготовлении модельного комплекта, кокилей и пресс-форм, увеличивая все их размеры на величину литейной усадки.
Величина литейной усадки зависит от литейных свойств сплава (литейная свободная усадка сплава), степени торможения усадки со стороны литейной формы (податливость формы) и отдельных частей отливки, сложности конструкции отливки, скорости охлаждения отливки в форме и т. д. Литейную усадку компенсируют, увеличивая размеры при изготовлении модельного комплекта и металлических форм (кокиль, пресс-форма). Эти размеры контролируют с помощью усадочного метра, каждая единица длины которого больше эталонной на величину усадки (0,75; 1; 1,25; 1,5; 1,75; 2; 2,25; 2,5 %).
Для упрощения технологии изготовления отливки следует принимать литейную усадку: для стали 2 %, для чугуна 1 %, для алюминиевых сплавов 0,9...1,3 %, для магниевых сплавов 1,5...1,7 %.
Разработанный чертеж элементов литейной формы используют при изготовлении модельного комплекта и сборке разовых форм, а также при изготовлении многократно используемых форм (кокиль, пресс-форма).
- Разработка эскиза литейной формы
Для выбранного способа изготовления отливки и разработанного чертежа элементов литейной формы вычерчивают эскиз литейной формы (Π, ОФ, ВМ, К, Д) с указанием особенностей литниковой системы для конкретного сплава.
3. ТЕХНОЛОГИЧНОСТЬ КОНСТРУКЦИИ ЛИТЫХ ДЕТАЛЕЙ
- Общие требования к технологичности конструкции литых деталей
Под технологичностью литой детали понимают совокупность свойств ее конструкции, позволяющих получать качественные отливки с минимальными затратами труда, средств, материалов и времени при их изготовлении в принятых условиях производства, а также обеспечение технологичности изготовляемых из них деталей механической обработкой (ГОСТ 18831—73).
Для создания технологичной конструкции литой детали конструктор должен учесть многие факторы, которые могут быть сведены к трем основным группам: факторы технологичности применяемого сплава, способа литья и способа механической обработки.
Технологичность применяемого сплава характеризуется физико-химическими, литейными (усадка, жидкотекучесть, ликвация) и специальными (герметичность, коррозионная стойкость, износостойкость и др.) свойствами.
Технологичность способа литья характеризуется точностью размеров, шероховатостью поверхности, припуском на механическую обработку, гарантированными показателями плотности, структуры и механических свойств отливок, ограничением массы, размеров и сложности конфигурации отливки.
Технологичность механической обработки зависит от геометрической формы отливки, расположения приливов, отверстий, баз для проведения механической обработки и т. д.
Важнейшей задачей при проектировании литой детали является максимальное уменьшение ее массы. Этого добиваются при реализации конструкторских и технологических факторов. Конструкторские факторы — улучшение качества проектирования детали (расчет на прочность, унификация деталей, применение сплавов с повышенными механическими свойствами). Технологические факторы — повышение точности изготовления отливок и снижение шероховатости их поверхности, уменьшение припусков на механическую обработку и толщины стенок
Для оценки технологичности созданной конструкции детали используют показатели технологичности, главными из которых являются:
коэффициент использования металла КИМ
он характеризует сравнительное количество металла, которое необходимо удалить при .механической обработке;
коэффициент необработанной поверхности (КНП), КНП характеризует точность изготовления отливки и качество ее поверхности.
Технологичные отливки должны иметь:
- простые контуры, облегчающие изготовление как литейной оснастки, так и самих отливок;
- толщину стенок в различных сечениях, при которой обеспечиваются необходимая прочность конструкции, а также возможность заполнения формы металлом без образования дефектов по недоливам и спаям;
- плавные переходы и сопряжения, ребра жесткости и другие конструктивные элементы, способствующие снижению внутренних напряжений и устранению дефектов в отливках (коробление, трещины);
- достаточное число окон и отверстий для удобства оформления стержнями внутренних полостей, выполнения обрубных и зачистных операций и транспортировки;
- конструктивные уклоны, обеспечивающие изготовление литейных форм без искажения контуров отливки формовочными уклонами и увеличения ее массы.
Желательно, чтобы отливки не имели выступающих частей, мешающих извлечению модели из разовых форм или отливок из многократно используемых форм, а также тонких ребер, глубоких впадин, закрытых полостей и поднутрений, затрудняющих изготовление литейной формы и выбивку отливки из формы.
3.2. Анализ технологичности конструкции литых деталей
Для повышения уровня технологичности литых деталей в процессе их изготовления необходимо провести конструкторско-технологическую отработку на основе поэлементного их анализа в последовательности, приведенной на рис. 10.
Основными документами для отработки на технологичность конструкции литой детали являются чертеж детали и чертеж сборочной единицы.
- Уточнение способа изготовления отливки
Уточнение проводится по технологическим возможностям способов изготовления литых заготовок (см. табл. П1.1 и П1.3).
При этом на чертеже детали контролируют класс точности размеров необрабатываемых поверхностей детали и параметр их шероховатости.
- Выбор расположения отливки в литейной форме
При этом руководствуются теми же правилами, что и при разработке чертежа элементов литейной формы (см. разд. 2.2).
- Анализ технологичности литой детали
Анализ проводят поэлементно (см. рис. 10, пп. 3.1—3.5), учитывая требования к технологичности литой детали (табл. 4). Для этого составляют перечень основных признаков технологичности по образцу, представленному в табл. 5. При выполнении требования признака технологичности ставят знак плюс, при невыполнении — знак минус. Для признаков «количество стержней» и «количество разъемов формы» указывают количество стержней, применяемых при сборке литейной формы, и количество разъемов формы. После заполнения табл. 5 и ее анализа изменяют конструкцию детали таким образом, чтобы исключить те признаки, которые не соответствуют технологичности конструкции.