Специальные виды штамповки
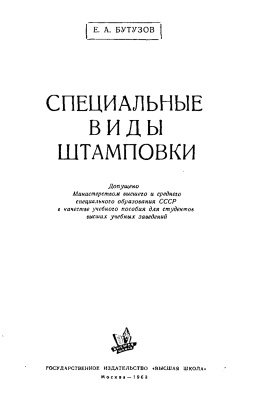
Бутузов Е.А.
Высшая школа, 1963 г.
ШТАМПОВКА РЕЗИНОЙ
§ I. ОБЩИЕ СВЕДЕНИЯ
Сущность штамповки резиной сводится к тому, что один аз жестких формоизменяющих элементов штампа (матрица или пуансон) заменяется резиновой подушкой, которая при рабочем ходе обжимает по жесткому формоизменяющему элементу—обычно пуансону (формоблоку) — заготовку из листового металла, уложенную на этот элемент.
Резиновую подушку заключают в высокопрочную емкость — контейнер, который закрепляют на ползуне пресса. Жесткий формоизменяющий элемент устанавливают на подштамповую плиту, закрепляемую на нижней плите пресса.
При рабочем ходе пресса подштамповая плита с установленным на ней жестким формоизменяющим элементом входит в контейнер и деформирует резиновую подушку, которая, обжимая заготовку, выполняет роль универсальной матрицы или пуансона.
И обычных стальных штампах работы по подгонке поверхности матрицы по поверхности пуансона весьма трудоемки, особенно при штампах для штамповки тонколистовых крупногабаритных деталей. При штамповке резиной эти работы отпадают, а изготовление одного жесткого формоизменяющего элемента не представляет трудностей, поскольку обычно его изготовляют из легкообрабатываемых материалов (сплавов алюминия, балинита, пластмассы и др.).
Известно пять схем штамповки резиной.
Схема I — штамповка без прижима с резиновой родушкой, работающей в качестве матрицы.
Схема II — то же, но при установке на подиггамповую плиту нескольких пуансонов — групповая штамповки.
Схема III — штамповка без прижима с резиновой подушкой, работающей в качестве пуансона.
Схема IV — штамповка с прижимом и резиновой подушкой, работающей в качестве пуансона.
Схема V — штамповка с прижимом и резиновой подушкой, работающей в качестве матрицы.
Регулировки усилия прижима можно достигнуть изменением внутреннего диаметра прижимного кольца. Чем больше этот диаметр, тем меньше площадь кольца, воздействующая на фланец заготовки, и усилие прижима.
При штамповке резиной обычно применяют крупные гидравлические прессы. Штамповка деталей даже относительно небольших габаритов требует больших усилий пресса.
Необходимость крупного прессового оборудования является основным недостатком метода штамповки резиной. Это объясняется тем, что стоимость таких прессов очень велика. Прессы занимают большие производственные площади и сложны в наладке. В настоящее время усилие применяемых прессов доходит до 75 000 т и выше. Эти прессы уникальны и не могут быть рекомендованы для широкого применения в мелкосерийном производстве.
§ 4. ОПЕРАЦИИ, ВЫПОЛНЯЕМЫЕ МЕТОДОМ ШТАМПОВКИ РЕЗИНОИ
Методом штамповки резиной можно произвести следующие операции: вырезку по контуру; просечку отверстий; гибку бортов прямых, выпуклых и вогнутых; формовку; вытяжку.
Особенностью метода штамповки резиной является возможность совмещения ряда операций и их выполнения при помощи одного жесткого формоизменяющего элемента.
Рассмотрим процессы выполнения отдельных операций.
1. Вырезка по контуру
Для выполнения этой операции заготовка должна иметь достаточный припуск порядка 30—40 мм. Величина припуска зависит от механических характеристик материала и его толщины. Ввиду больших отходов, сопровождающих эту операцию, ее применяют очень редко и то при условии, что вырезка совмещена с другими операциями. На рис. 10 приведена схема процесса вырезки, который имеет ряд фаз и сводится к следующему.
Припуск а при воздействии резиновой подушки отжимается к подщтамповой плите. Дальнейшее повышение давления приводит к образованию ступеньки, которая увеличивается с одновременным подтягиванием к основанию жесткого элемента штампа. Между припуском и подштамповой плитой образуются силы трения, которые при определенной величине давления будут препятствовать перемещению припуска к основанию жесткого элемента штампа. Припуск заклинивается, и у режущей кромки образуется зона сложной деформации — срез с растяжением. Дальнейшее увеличение давления приводит к обрыву припуска по контуру режущего штампа.
Из схемы видно, что вырезка происходит под действием вертикальной составляющей вектора давления, действующего нормально к поверхности припуска.
ШТАМПОВКА НА ПАДАЮЩИХ МОЛОТАХ
§ 1. СУЩНОСТЬ МЕТОДА
Штамповка на падающих молотах известна с давних пор. Значительный объем доводочных ручных работ, большой шум и сотрясения при работе являются основными недостатками этого вида штамповки. Однако в опытных и мелкосерийных производствах благодаря малотрудоемкой и дешевой оснастке, требующейся при штамповке на падающих молотах, в ряде случаев целесообразно применять этот вид оборудования. Конструкция падающих молотов была усовершенствована за последнее время, кроме того, была отработана методика штамповки, что сократило необходимые доводочные ручные работы при изготовлении деталей.
Сущность формоизменения при штамповке на падающих молотах сводится к тому, что по- заготовке, уложенной на жесткую металлическую матрицу, жестким пуансоном совершают ряд нарастающих по силе ударов.
Под влиянием этих ударов заготовка принимает форму, соответствующую форме матрицы.
Последний удар является калибрующим и наибольшим по силе.
Система нарастающих ударов позволяет ограничить формоизменение заготовки, однако в ряде случаев эта мера оказывается недостаточной, и ограничение формоизменения достигается путем укладки в глубокие места матрицы кусков резины или же установкой на матрицу стопки фанерных ограничивающих рамок (рис. 64). Привёденный порядок формоизменения допускает использование одних и тех же матрицы и пуансона при многопереходной штамповке деталей, имеющих элементы глубокой вытяжки. В ряде случаев при штамповке деталей, требующих нескольких переходов, применяют промежуточный отжиг для повышения пластичности материала и ручные операции для разглаживания гофров, образующихся на фланцах заготовки. Указанная методика штамповки исключает необходимость иметь штампы для каждого перехода, чем значительно сокращается количество оснастки.
Характер процесса формоизменения позволяет штамповать детали, имеющие сложную форму и элементы глубокой вытяжки, штампами простой конструкции. На рис. 65 показаны характерные детали, штампуемые этим методом. Формообразование таких деталей в инструментальных штампах потребовало бы сложных штампов для каждого перехода.