Специальные способы литья: Справочник
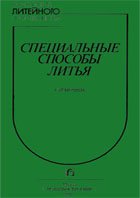
Ефимов В.А.
Машиностроение, 1991 г.
ЛИТЬЕ ПОД ДАВЛЕНИЕМ
1. Основные характеристики процесса
Литьем под давлением получают тонкостенные отливки, масса и теплосодержание которых даже при больших габаритных размерах в сотни раз меньше, чем масса и теплосодержание металлической формы. Высокая скорость теплоотдачи от отливки к форме обусловливает необходимость ее быстрого заполнения (менее 0,1 с). Такое заполнение обеспечивает машина, в которой залитый в камеру прессования металл под большим давлением и с высокой скоростью запрессовывается в форму. Высокие скорости впускного потока (до 100 м/с) способствуют качественному оформлению рельефа отливок сложной конфигурации.
Кроме скоростей прессования и впуска, существенное влияние на формирование отливки оказывают следующие факторы: температуры металла и формы, конструкция литниково-вентиляционной системы, режимы смазывания формы, давление и продолжительность действия подпрессовки после заполнения формы. Совокупность таких факторов, как скорость потока металла, давление в потоке, противодавление газов, определяет гидродинамический режим формирования отливки. Температуры заливаемого металла и формы, продолжительность заполнения, продолжительность действия подпрессовки, а также темп работы машины определяют тепловой режим процесса.
Для литья под давлением применяют машины с холодными (горизонтальными и вертикальными) и горячими камерами прессования [11], в которых движение пресс-поршня обеспечивается давлением рабочей жидкости, подаваемой в гидроцилиндр прессующего механизма от специальных аккумуляторов. Скорость прессования иПр и давление ρ рабочей жидкости в различные периоды движения пресс-поршня различны (рис. 1). За время tпресс-поршень перекрывает заливочное отверстие, двигаясь под небольшим давлением ргс небольшой скоростью vx. Период t2соответствует продвижению металла в камере прессования, вплоть до входа его в литниковые каналы (вспомогательный ход). Скорость достигает максимального значения υ2, а давление р2превышает Ρι на величину гидравлических сопротивлений в камере прессования. Период /8 соответствует заполнению литниковой системы и полости формы. Вследствие резкого сужения потока в питателе скорость падает до v3fа давление повышается до р3. В момент окончания заполнения формы наблюдается гидравлический удар. При меньших гидравлических сопротивлениях давление снижается, а скорость перемещения пресс-поршня в периоды вспомогательного хода и заполнения может быть также снижена (штриховые линии).
После затухания колебаний устанавливается конечное давление р4. Если к моменту его достижения металл сохраняет жидкоподвижное состояние, происходит подпрессовка, окончательно формирующая отливку. Готовая отливка после затвердевания автоматически выталкивается при раскрытии формы. Раскрытие и закрытие (запирание) формы осуществляются запирающим механизмом машины, рабочая жидкость в который подается от общего иль отдельного аккумулятора.
Область применения. Литье под давлением используют в основном для получения отливок из цинковых, алюминиевых, магниевых и медных сплавов.. Реже этим способом литья изготовляют отливки из стали, титана или сплавов на основе олова и свинца. Некоторые физические и механические свойства сплавов, а также их эксплуатационные характеристики приведены в табл. 1. Однако необходимо учитывать, что механические свойства отливок под давлением неравномерны по сечению из-за наличия мелкозернистого поверхностного слоя (0,5- 0,8 мм).
Требования к технологическим свойствам сплавов обусловлены высокой скоростью охлаждения потока металла. Сплавы должны иметь хорошую жидкотекучесть, небольшую усадку и не должны сильно взаимодействовать с металлом формы [6]. Если машина не обеспечивает подпрессовку, следует выбирать сплавы с узким интервалом кристаллизации.
Алюминиевые сплавы (особенно системы Аl—Si) наиболее широко (до 60% общего выпуска) используют при литье под давлением. Кремний увеличивает жидкотекучесть и прочность сплава. При содержании в сплаве 11,7% Аl образуется эвтектика. В этом случае жидкотекучесть сплава максимальна. Для отливок с повышенными требованиями к прочности и подвергаемых термической обработке применяют сплавы системы Al—Si— Сu, но с добавлением меди не более 4%, в противном случае снижается коррозионная стойкость. Чаще всего применяют сплавы с 7—8% Аl и 1—2% Сu. Небольшая добавка магния (0,2—0,3%)* повышает прочность при вибрационных нагрузках. Кроме того, для отливок с высокой коррозионной стойкостью используют сплавы системы Al—Mg, содержащие 9,5—10% Mg. Главный технологический недостаток алюминиевых сплавов — склонность растворять железо, ведущая к привариванию к стальной форме. Для нейтрализации приваривания в сплавы вводят до 1,5% Fe (в сплавы системы Al—Mg не более 0,2%).
Цинковые сплавы не взаимодействуют со стальной формой и деталями камеры прессования, что позволяет применять автоматические машины с горячей камерой прессования (более производительные, чем машины с холодной камерой прессования). Цинковые сплавы жидкотекучи, имеют низкую температуру плавления. Наиболее распространены сплавы системы Zn— Al—Сu с добавкой 3—5% Аl и 1—3% Сu. Цинковые сплавы склонны к межкристаллитной коррозии и поэтому не должны содержать таких элементов, как кадмий, медь, олово, свинец и железо. Общая сумма примесей этих элементов в стандартном сплаве не должна превышать 0,5%. Использование для цинковых сплавов машин с холодной камерой прессования дает возможность повысить содержание алюминия до 12% при содержании меди 2%. Такой сплав имеет довольно хорошие механические свойства: σΒ— 250 МПа; δ — 1%; 95 НВ.
Магниевые сплавы. Область применения этих сплавов расширяется благодаря внедрению машин с высокими скоростями прессования (до 8 м/с), позволяющими сократить продолжительность заполнения, что необходимо из-за малого объемного теплосодержания этих сплавов по сравнению с алюминиевыми и цинковыми. Одно из важных технологических свойств магниевых сплавов — отсутствие привариваемости. Это позволяет изготовлять крупногабаритные тонкостенные детали типа коробки скоростей, коробки передач автомобиля, корпусов компрессора, мотопил, приборов и др. Преимущество магниевых сплавов как конструкционных материалов заключается в их высокой удельной прочности. Обычно для литья под давлением применяют сплавы системы Mg-Al с содержанием 7—10% и добавками 0,15—0,5% Μn и 0,2—2% Zn. Алюминий и цинк повышают жидкотекучесть и прочность сплава, но снижают его коррозионную стойкость. Наилучшее сочетание механических и технологических свойств имеют сплавы с содержанием 0,3—0,5% Zn. Марганец повышает коррозионную стойкость. Основной недостаток магниевых сплавов — окисляются на воздухе (возгораются) — и поэтому при литье должны все время находиться под слоем защитного флюса. Для защиты от окисления магниевые сплавы легируют бериллием (до 0,002%).
Медные сплавы. Для литья под давлением используют в основном кремнистые латуни с содержанием, % (мае. доля): Zn 20—40; Si 3,5—4,4; Pb 0,2— 2; остальное Сu. Латуни имеют низкую температуру плавления, минимальный интервал температур кристаллизации и максимальную жидкотекучесть. Вредными примесями в латуни являются олово и сурьма, образующие хрупкие соединения Cu2Sbи Сu2Sn на границах зерен. Сумма примеси Sn+ Sb не должна превышать 0,3%. В латуни, предназначенные для деталей с высокой коррозионной стойкостью, добавляют до 0,3% Μη, нейтрализующего вредное влияние олова.
Сплавы на основе железа (в основном стали). Литье под давлением этих сплавов осуществляют на машинах, детали камеры прессования и формы которых изготовлены из сплавов на основе вольфрама или молибде на, выдерживающих температуры заливки более 1500 °С. Наиболее технологичны