Советы заводскому технологу
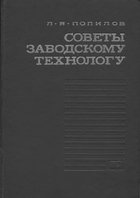
Попилов Л.Я.
Лениздат, 1975 г.
СОСТАВЫ, ИСПОЛЬЗУЕМЫЕ В МОДЕЛЬНОМ ДЕЛЕ
Изготовление деталей и изделий отливкой из расплавов — один из наиболее распространенных в промышленности технологических процессов — основа литейного производства. Существенным элементом литейной технологии является создание модели будущего изделия, по которой изготовляют форму, подлежащую заливке расплавленным металлом.
Изготовление литейных моделей — модельное дело — обширный раздел технологии литейного производства, имеющий свои приемы выполнения операций, свои особенности и использующий большое разнообразие материалов в различных сочетаниях.
в этой главе приводятся некоторые сведения о составах и свойствах разнообразных, преимущественно новых, композиций, применяемых в модельном деле для изготовления различных видов модельной оснастки (моделей, стержневых ящиков и др.).
Приводимые рецепты представляют лишь небольшую часть составов, имеющих практическое применение. Различные варианты возможных композиций вместо одной-двух рекомендуемых даются для того, чтобы технолог, мастер или исследователь, работающие в области модельного дела и знакомые с его основами, имели достаточный материал для выбора и отправные данные для самостоятельной разработки оптимальных составов применительно к конкретным условиям.
Собранные здесь сведения могут в определенных условиях служить также полезным справочным материалом при оперативном решении разнообразных технологических задач или при постановке опытно-исследовательских работ, избавляя специалистов от необходимости разыскания нужных сведений, разбросанных в большом числе источников.
Изготовление деталей (изделий) отливкой всегда требует наличия формы, представляющей собой точную обратную (негативную) копию будущего изделия. в свою очередь для получения формы необходимо иметь прямую копию будущей детали, называемую моделью. в редких случаях роль модели может выполнять готовая деталь (изделие), если она уже имеется.
в зависимости от материала, из которого готовят модель, и способа ее использования различают модели постоянные (многократные), используемые до естественного износа, и модели разовые (однократные), удаляемые из формы перед заливкой металла (выплавляемые, растворяемые) либо уничтожаемые в процессе заливки формы расплавленным металлом (газифицируемые).
Постоянные (многократные) модели изготовляют из древесины, металлов, пластических масс. Технология их изготовления («модельное дело») хорошо изучена и подробно освещена в литературе. Здесь приводится лишь краткий перечень некоторых (новых) модельных составов на основе синтетических смол, которые находят все более широкое применение в литейном деле при изготовлении постоянных моделей.
1. составы для изготовления постоянной модельной оснастки из пластмасс
Модельная оснастка (модели, стержневые ящики) из пластических масс является наиболее прогрессивным видом оснастки, так как трудоемкость ее изготовления во много раз (5—20) ниже, чем деревянной либо металлической, а стойкость и срок службы не уступают стойкости металлических моделей.
Составы на основе фураново-эпоксидиых смол. Хорошо зарекомендовали себя на практике в качестве материалов модельной оснастки композиции на основе фураново-эпоксидных смол типа 41-ФАЭД. Эти смолы дешевле и более теплостойки, чем эпоксидные смолы, обладая в то же время достоинствами последних.
Приготовление композиций, рецепты которых приводятся ниже, осуществляется в следующем порядке.
Смолу ЭД-6 подогревают до 70—80° С для расплавления и смешивают с мономером ФА. в смесь смол вливают дибутил-фталат, предварительно нагретый в течение 20—30 мин при 80—85° С для удаления летучих. Повышают температуру смеси до 120° С, перемешивают ее в вакуум-смеси-
теле при давлении 500—600 мм рт. ст. и в два приема вводят в нее наполнитель, продолжая перемешивание. За 5—10 мин до заливки форм в смесь добавляют отвер-дитель (бензолсульфокислоту или поли-этиленполиамин) и перемешивают еще 3— 5 мин. Приготовленную композицию необходимо немедленно использовать, так как оиа быстро затвердевает.
Наполнители, вводимые в композицию, предварительно просеивают через сито 025, сушат и прокаливают (маршалит — при 900—950е С 1—1,5 ч; графит —при 400— 450° С 30—40 мин; стальную стружку а проволоку 1—1,5 ч при 500° С, из алюминиевых сплавов — 1—1,5 ч при 200°С). Бензолсульфокислоту перед введением в смесь расплавляют в сушильном шкафу при 40— 45° С или растворяют в спирте либо ацетоне в соотношении 1 :5.
в наиболее распространенных технологических вариантах изготовления моделей принята следующая последовательность процессов:
1. Изготовление первоначального образца (мастер-модели или мастер-стержня), имеющего конфигурацию будущего пластмассового изделия. Материалом мастер-модели или мастер-стержня могут служить гипс, дерево или металл.
2. Покрытие поверхности мастер-модели (стержня) разделительным составом, облегчающим ее отделение от формы после затвердевания последней.
3. Изготовление формы по мастер-модели (стержню) для изготовления модели заливкой ее гипсовым раствором (гипс+вода), песчано-силикатными смесями, пластмассовыми композициями и т. п.
4. Отделение затвердевшей формы от мастер-модели (стержня).
5. Заполнение полости формы пластмассовой композицией (составы см. ниже) или послойное нанесение этой композиции на стенки формы с установкой упрочняющих сердечников или без них.
6. Извлечение затвердевшей модели из формы.
Техника изготовления пластмассовых изделий достаточно подробно освещена в литературе. Основное различие в технологии «их изготовления заключается в составе связующих смол и режиме отверждения. Наиболее распространены в качестве связующих полиэфирные, эпоксидные, фурановые смолы, их смеси и некоторые другие смолы конструкционного назначения.