Составной рабочий инструмент прокатных станов
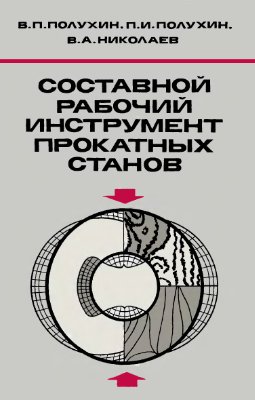
Полухин В.П., Полухин П.И., Николаев В.А.
Металлургия, 1977 г.
Эффективность применения составного инструмента в прокатных станах
1. Области применения составного инструмента
При определении рациональных областей применения составного инструмента в прокатных станах в каждом конкретном случае прежде всего необходимо ориентироваться на технико-экономическую эффективность его использования, технологичность изготовления и надежность при эксплуатации.
В ряде случаев понятно стремление разгрузить действующие мощности машиностроительных предприятий за счет применения составных валков, ось которых используется многократно. Таким образом используются, например, оси крупных опорных валков в ЧССР [3, 4]. Применение твердых сплавов для изготовления сплошных рабочих валков в большинстве случаев затруднено, так как эти материалы не способны воспринимать большие изгибающие нагрузки и крутящие моменты. Наконец, при изготовлении крупных опорных валков массой в 200 τ и более часто не представляется возможным выполнить их цельноковаными или цельнолитыми.
Весьма перспективным является применение составных опорных валков на широкополосовых тонколистовых и толстолистовых станах холодной и горячей прокатки. Как по отечественным данным, так и по зарубежным, стойкость составных опорных валков в 2—3 раза (больше, чем цельнокованых. В настоящее время в ряде стран наблюдается интенсивное развитие производства бандажированных валков. Опыт эксплуатации крупных составных опорных валков листовых станов за рубежом показывает, что многократное использование оси является выгодным мероприятием.
Литые валки являются конкурентоспособными цельнокованым, но они уступают им по прочности шеек. Поэтому перспективным является применение составных валков с бандажами из литых сплавов и кованой стальной осью.
Применение составных конструкций открывает широкие перспективы в создании уникальных, крупногабаритных валков, потребность в которых назрела в связи с возросшей потребностью в широком толстом листе. Строительство станов типа 3000—5000 требует создания надежных конструкций составных валков, масса которых доходит до 250 т. Следует отметить, что при изготовлении и эксплуатации крупногабаритных конструкций особую роль приобретает масштабный фактор. Как известно, при крупногабаритных отливках (слитках) и поковках пораженность их дефектами металлургического производства, а также возникшими в результате последующих технологических операций возрастает с увеличением развеса заготовок. Влияние масштабного фактора сказывается и в другом отношении. Оказывается, чем больший объем детали находится под воздействием одного и того же уровня напряжений, тем больше вероятность возникновения трещин в области детали с высоким уровнем напряжений. Поэтому вероятность возникновения разрушения 'Повышается с увеличением габаритов деталей, изготовленных из одних и тех же материалов. В связи с отмеченным выше целесообразность изготовления крупногабаритных валков в составном исполнении очевидна.
Бандаж и ось, как правило, могут изготавливаться из слитков более мелкого развеса, а следовательно, более качественных. В связи с применением составных конструкций возможно изготовление бандажей из таких сталей, которые будут способствовать повышению надежности и долговечности рабочего инструмента. Уже в настоящее время применение в опытном порядке литых бандажей из заэвтектоидных марок сталей и кованых осей повысило стойкость валков в три раза по сравнению с цельноковаными валками [3].
При организации возвращения изношенных по поверхности бочки валков с металлургических заводов на машиностроительные для их разборки и последующего бандажирования осей может быть получен значительный экономический эффект.
Широкое применение составные валки получили при производстве ленты и а плющильных станах. На этих станах используют рабочие валки диаметром от 50 до 200 мм. Бандажи изготавливают из твердых сплавов, что увеличивает жесткость валковой системы и обеспечивает повышение точности размеров и улучшение качества поверхности проката. Твердость поверхности бандажей из твердых сплавов составляет HRC 88—92; модуль упругости их более чем в 2,5 раза превышает модуль упругости обычных валковых сталей. Стойкость таких валков в 10—50 раз выше, чем стальных закаленных {5].
При высокотемпературной вакуумной прокатке тугоплавких металлов целесообразно применение составных валков из металлокерамических сплавов. Использование этих сплавов обеспечивает прокатку без налипания металла на валки и способствует улучшению чистоты поверхности выпускаемой продукции.
Бандажи составных валков изготавливают из твердых .сплавов ВК-6; ВК-8; ВК-Ю; ВКн15 [6—8]. Сплавы ВК-Ю и ВК-15 являются более вязкими, поэтому их применяют для изготовления сортопрокатных валков. Твердосплавные бандажи напрессовывают на оси из сплава «инвар», у которого коэффициент линейного расширения соответствует коэффициенту линейного расширения сплава ВК- Результаты исследования стойкости валков с твердосплавными бандажами, приведенные в работе ι[6], показывают, что износ поверхности калибров валков с бандажом из твердых сплавов в 10 раз меньше, чем валков с бандажом из стали ШХ10 или Х12М, твердость которых составляет HRC 62.
Основными причинами, сдерживающими применение твердосплавных бандажей для валков мелкого развеса, являются нарушение сопряженности бандажа и оси, а также разрушение бандажа в процессе эксплуатации. Так, при посадках бандажа на ось диаметром 100— 200 мм с гарантированном натягом 0,01—0,015 мм бандажи плющильных станов выходят из строя по растрескиванию.
Для «предотвращения растрескивания «бандажей требуется создание конструкций составных валков с разрезной осью, выполняющей роль демпфера, компенсирующего увеличение или уменьшение натяга © процессе эксплуатации валка.
Опыт эксплуатации составных рабочих валков с твердосплавными бандажами, посаженными на ось с гарантированным натягом, показал недостаточную надежность такого соединения. С целью обеспечения постоянства контактных давлений от натяга, а следовательно, и величины передаваемого крутящего момента необходимо:
1) -подобрать материал бандажа и оси с одним и тем же коэффициентом линейного расширения;
ι2) обеспечить постоянство давления от натяга за счет применения демпфирующей оси.
В первом случае при одинаковом коэффициенте линейного расширения материалов бандажа и оси для горячей прокатки необходимо уменьшение термосопротивления между ними с тем, чтобы не ослабить натяг при разогреве и не увеличить его при охлаждении бандажа. Поэтому для обеспечения постоянства контактных давлений необходимо использовать второй способ применения демпфирующей оси. При этом демпфирование -может осуществляться как механически, так и гидравлически за счет регулирования давления в полости оси {9, с. 214—222].
Для обеспечения постоянства давлений от натяга, т. е. сохранения его постоянной величины при разогреве (охлаждении) бандажа, диаметр оси должен увеличиваться (уменьшаться) во столько же раз, во сколько раз увеличивается (уменьшается) наружный диаметр бандажа. В идеальном случае это осуществляется при автоматическом регулировании давления внутри полости оси.
В качестве демпфирующей оси может быть использована так называемая «податливая» ось. Как и в первом случае, ось выполнена полой, -в горизонтальной плоскости ее прорезаны три сквозных паза на длине оси, превышающей длину бандажа в 1,2—1,7 раза [6]. Прорези, образующие три упругих элемента, после посадки бандажа с необходимым натягом и позволяют осуществлять демпфирование в широком диапазоне изменения размеров бандажа.
Применение осей таких конструкций рационально для валков плющильных, проволочных и сортовых станов. Дальнейшее их распространение ограничено размерами осей, так как при увеличении габаритов осей технологически трудно выполнять прорези. Кроме того, разрезные оси пригодны только при эксплуатации бандажей из твердых сплавов, поскольку переменная их жесткость в радиальном направлении зависит от угла поворота. Модуль упругости твердосплавных бандажей в 2—3 раза превышает модуль упругости оси и радиальное биение вследствие наличия прорезей будет незначительно.
Применение твердосплавных бандажей способствует повышению контактной жесткости .составных валков и получению проката с высокой точностью размеров.
Использование составных валков весьма перспективно на сортопрокатных станах, предназначенных для прокатки малотоннажных партий (300—400 профиле-размеров). С учетом многозаказной продукции при обилии профилеразмеров комплекты валков хранятся многие годы и за одну установку в клеть изнашиваются незначительно. Сумма потерь при таком использовании валков зависит от величины их запаса и времени нахождения валков в запасе. Расчеты показывают, что сумма дополнительных потерь в результате «замораживания», недоиспользования и последующей ликвидации недоиспользованных валков при производстве каждого профиля весьма значительна. Использование же составных валков исключает потери при долговременном складировании и при так называемом недоиспользовании металла валков, когда невозможно организовать нарезку новых калибров. Эта задача решается за счет применения унифицированных осей и наборных колец (бандажей), воспроизводящих как многоручьевые калибры, так и дающих возможность замены калибровки при использовании той же самой оси. В связи с этим при многократном использовании оси в балансе расхода металла в основном участвует лишь металл, идущий на изготовление наборного или сплошного бандажа, калиброванного для различных профилей. Поэтому использование бандажированных валков способствует уменьшению числа хранящихся на складе валков в ожидании прокатки того или иного профилеразмера согласно заказам. Это в значительной мере способствует снижению затрат на хранение и содержание складских помещений.
При этом необходимо отметить, что при эксплуатации бандажей при прокатке малотоннажных партий особое внимание следует уделять надежности оси, которая используется многократно, качество которой должно сохраняться более продолжительное время, чем бандажей.
В связи с тем что при изготовлении составных валков основная масса металла .[9, с. 192—200] (около 2/3 от массы монолитного валка) уходит на изготовление осей, при оценке рациональности применения составных валков особое внимание следует уделять разделению двух эксплуатационных характеристик — надежность оси и надежность бандажа [10].
Составные конструкции обладают скрытыми возможностями повышения надежности практически всех несущих составных его частей. Так, повышение надежности шеек (осей) можно осуществить за счет создания в них напряжения сжатия при применении стяжек. Аналогичным образом возможно увеличение долговечности износостойких, ,но хрупких валков (чугунных), когда 'напряжения сжатия создаются как в шейках, так и в валке.
При выборе соответствующей конструкции составного валка и материалов оси и бандажа ее работоспособность следует оценивать по менее прочной ее составной части (бандажа, оси, стяжки и др.). Это обстоятельство предопределяет возможность многократного использования одной из составных частей составных валков.