Производство железорудных окатышей
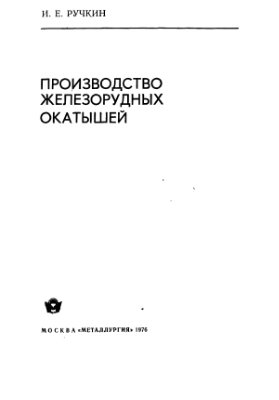
Ручкин Е.А.
Металлургия, 1976 г.
ОБЖИГ ОКАТЫШЕЙ В ШАХТНЫХ ПЕЧАХ
Шахтная печь имеет ряд преимуществ перед конвейерной машиной: она проста по конструкции; благодаря лучшей рекуперации тепла на обжиг его требуется меньше (525—924 МДж/т), а температура отходящих газов ниже; в ней окатыши остывают медленно, благодаря чему достигается высокая степень их окисления и прочность (содержание закиси железа составляет 0,4— 4%, прочность на раздавливание от 200 до 500 кг/окатыш, барабанная проба 7—12%); возможность обжигать крупные окатыши (25—40 мм); отсутдтвие дефицитных и дорогостоящих материалов и высокотемпературных дымососов.
Недостатками шахтной печи являются: ограниченная производительность вследствие затруднений в раздаче тепла по сечению слоя, возможность образования спеков («козлов») и трудность их удаления из печи; расстройства хода при образовании настылей на стенах; трудность обжига окатышей из гематитовых концентратов и офлюсованных окатышей из сравнительно бедных концентратов; повышенные требования к прочности сырых окатышей.
Известны три схемы конструкций современных шахтных печей (рис. 69). Для первой конструкции характерно то, что она имеет одинаковое сечение по всей высоте шахты и переточные воздушные каналы из печи в топочные камеры (для прохода подогретого воздуха, используемого на горение топлива). В другой конструкции ниже устьев каналов из топочных камер имеется расширение, которое постепенно сужается к низу шахты, но переточные каналы отсутствуют. В третьей конструкции расширение шахты печи сохраняется до комколомателей, имеются переточные каналы.
Первая и третья конструкции шахтных печей позволяют лучше распределить газы по сечению печи, но пыль, выносимая охлаждающим воздухом, затрудняет эксплуатацию топочных камер, особенно при обжиге офлюсованных окатышей, ошлаковывая их стены.
Загрузка окатышей в печь производится с помощью ленточного или пластинчатого укладчика (конвейера, снабженного пантографным устройством). Режим движения укладчика устанавливается в соответствии с требуемым профилем поверхности засыпи. При движении укладчика вперед и назад укладывается одинаковое количество окатышей.
Разгрузка обожженных окатышей из печи производится непрерывно с такой же скоростью, с какой в печь загружаются сырые окатыши, так что уровень засыпи на колошнике печи остается все время постоянным. Для разгрузки окатышей применяют устройства шлюзового, шнекового, вибрационного типа, устройства в виде вращающегося стола и качающегося лотка.
Разрушение в печи возможных спеков окатышей производится при помощи комколомателей (зубчатых многовалковых дробилок), которые могут быть качающегося и вращающегося типов. В промышленных условиях количество материала, требующего дробления, обычно не превышает 5%. Кроме прямой функции дробления спеков, комколоматели обеспечивают равномерный выпуск материалов из печи и равномерное распределение воздуха по сечению шахты. Скорость движения комколомателей устанавливают в соответствии с производительностью печи.
Оптимальные температуры в зонах печи поддерживаются при данной производительности путем стабилизации соответствующего соотношения высот зон обжига, нагрева и сушки. Это соотношение может несколько изменяться в зависимости от скорости фильтрации газов, температуры и качества окатышей (химического состава, крупности, плотности, прочности на сжатие, влажности). Ниже устьев топочных камер окатыши постепенно охлаждаются восходящим потоком холодного воздуха, вдуваемым в печь на уровне расположения комколомателей. Около 20% воздуха вдувается в каждую топочную камеру. Остальной воздух вдувается в шахту печи через устройства, имеющие форму жалюзи.
Давление воздуха в большой печи составляет в среднем 0,04 МПа и зависит от качества окатышей. Часовой расход воздуха ориентировочно равен часовой производительности печи. Количество охлаждающего воздуха превышает теоретически необходимое на 5—10%, а потери охлаждающего воздуха через разгрузочные отверстия достигают 3—5% (разгрузочное устройство в виде сужающихся вниз течек снижает потери воздуха).
Дымовые газы, нагретые до температуры 1250—1320°С, из топочных камер входят в печь, заполненную окатышами. На расстоянии 0,25—0,5 м от уровня засыпи температура, в печи достигает уже 1250—1300°С.
На уровне устьев топочных каналов температура в печи приблизительно на 30°С выше температуры газа-теплоносителя за счет окисления магнетита в гематит и снижается от периферии к центру печи. Иногда, если печь работает с максимальной нагрузкой, в шихту добавляют уголь в количестве 4,5 кг/т. Эта добавка обеспечивает более равномерное распределение температур по горизонтальному сечению печи. Температура обжига поддерживается постоянной регулированием количества поступающего газа-теплоносителя в соответствии с производительностью печи. Температура отходящего из печи газа составляет 150°С.
Температура окатышей, разгружающихся из печи, находится в зависимости от ее производительности и колеблется от 150 до 300°С. Расход тепла на обжиг 1 т окатышей колеблется от 798 до 924 МДж, а расход электроэнергии составляет 30 кВт-ч/т окатышей.