Производство стали
Борнацкий И.И., Михневич В.Ф., Яргин С.А
Металлургия, 1991 г.
Способы раскисления стали
В настоящее время применяют следующие способы раскисления: осаждающее, диффузионное, раскисление стали углеродом при помощи вакуума и синтетическим шлаком.
При осаждающем раскислении раскислители вводят в сталь (в печь или ковш), при этом часть растворенного кислорода переходит в стойкие оксиды. Так как плотность продуктов раскисления меньше, чем жидкой стали, то часть продуктов раскисления успевает всплывать на поверхность и перейти в шлак, а часть продуктов раскисления остается в стали, при этом общее содержание кислорода в металле уменьшается. Продукты раскисления в виде неметаллических включений понижают качество изготовляемой стали, вызывая в отдельных случаях такие дефекты, как расслоения, трещины и др.
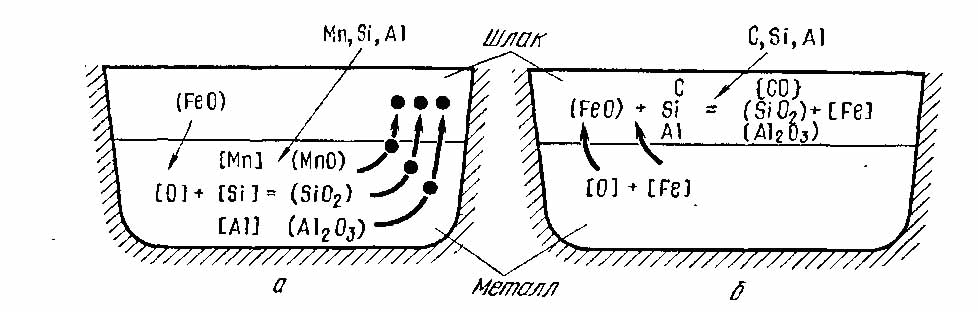
Рис. 19.1. Схема осаждающего (а) и диффузионного (б) раскисления стали
Сущность диффузионного раскисления, в основном применяемого при выплавке стали в дуговых электропечах, состоит в том, что к концу плавки шлак обрабатывается измельченными восстановителями — коксиком, ферросилицием, алюминием, понижающими содержание оксида железа в шлаке. В соответствии с законом распределения оксид железа (кислород) переходит из металла в шлак, при этом содержание кислорода в металле понижается. При диффузионном раскислении, в сравнении с осаждающим раскислением, сталь содержит меньше кислорода и неметаллических включений, так как реакции раскисления в самом металле не происходят. На рис. 19.1 показана схема осаждающего (а) и диффузионного (б) раскисления стали.
Для раскисления стали синтетическим шлаком в отдельных сталеплавильных агрегатах приготавливается синтетический шлак из извести, глинозема, плавикового шпата. За несколько минут до выпуска плавки расплавленный шлак с температурой 1700 °С в количестве 3—4 % от массы плавки заливают в сталеразливочный ковш. Струя металла во время выпуска плавки с большой высоты падает на шлак, происходит дробление металла и шлака, поверхность контакта между шлаковой и металлической фазами резко возрастает и в соответствии с законом распределения оксид железа переходит в шлак. Этот переход сопровождается снижением содержания кислорода и неметаллических включений в металле.
При раскислении стали в условиях вакуума значительно повышается раскислительная способность углерода в связи с тем, что продукт раскисления углеродом СО удаляется из сферы взаимодействия.
Более низкая концентрация остаточного кислорода в стали, раскисленной комплексными раскислителями, обусловлена тем, что образующиеся оксиды (МnО, SiO2 и др.) вступают во взаимодействие между собой и сдвигают равновесие реакции раскисления в сторону более низкого содержания остаточного кислорода в стали. При раскислении стали комплексными раскислителями продукты раскисления в большинстве случаев образуются в жидком виде.
Величина зерна оказывает значительное влияние на механические и технологические свойства стали. Так, крупнозернистая сталь характеризуется повышенной прокаливаемостью, она лучше обрабатывается резанием. Однако с увеличением действительного размера зерна ухудшаются механические свойства, в наибольшей степени ударная вязкость. Различают природную и действительную величину зерна. Природная величина зерна в значительной степени определяется процессами, протекающими при легировании и раскислении стали. Неметаллические включения, образующиеся при раскислении стали (AI2O3, TiO2 и др.), являются центрами кристаллизации, а при нагреве стали выполняют роль «барьеров» и таким образом препятствуют росту зерна. На действительную величину зерна влияют температура начала и конца прокатки, условия термической обработки, а также величина природного зерна в стали.
Алюминий широко применяется для получения мелкозернистой структуры стали. В зависимости от содержания углерода в стали присадки алюминия могут составлять 0,06—0,12 %. Из других элементов, способствующих получению мелкозернистой структуры, следует отметить ванадий. При его введении в сталь получается более однородное зерно, чем при раскислении стали алюминием. Имеются также данные о тормозящем действии нитрида алюминия A1Nна рост зерна в стали.